Home » Printing Ink
Printing Ink
Case one: high viscosity printing ink.
Case two: low viscosity printing ink
2. Twin-shaft disperser, which is more highly effective than single HSD. A twin shaft disperser (TSD) is a low and fast speed shaft scrapper and disperser machine.
3. Horizontal Sand Mill for printing ink, Franli has the disc, pin type, different inner type can reach difference size of material, also you may think about the zirconia beads size.
4. The agitator mixer is the final process for adjusting the additional materials.
5. Filling machine for the package, which is weight type filling machine or piston filling machine.
Welcome to connect with us for a suitable turnkey project for printing ink.
Related Products
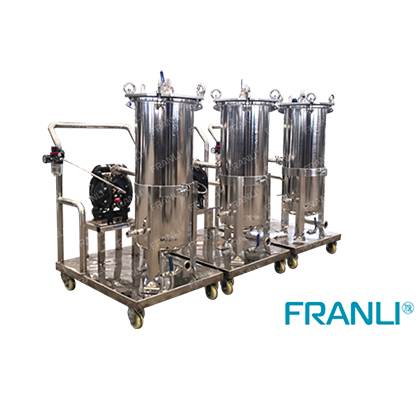
Bag Filter
The bag filter is a device that filters through pressure. When the liquid passes through the inlet of the machine and is filtered by the filter bag, it will effectively filter impurities and obtain high-quality materials.
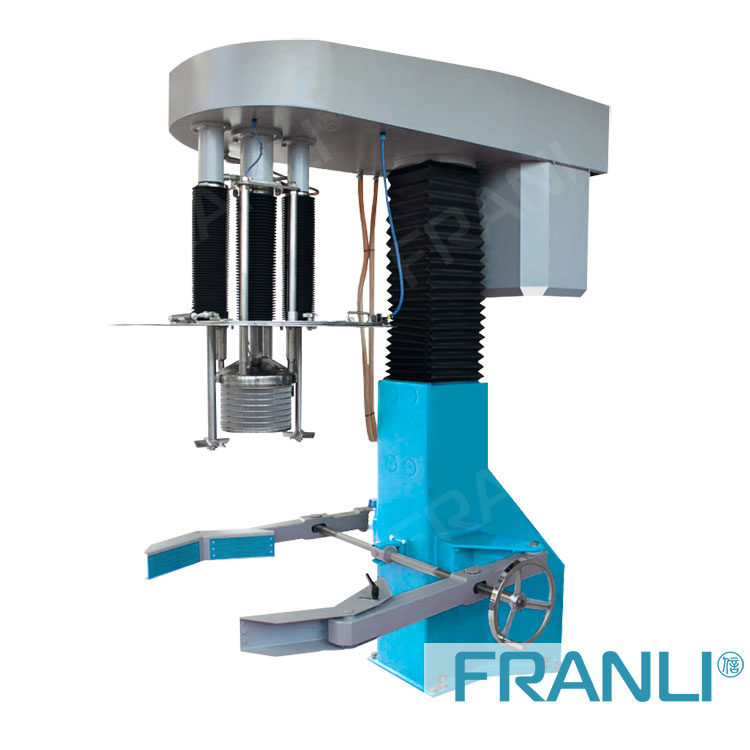
Basket Mill With Mixer
Basket mill with mixer is an indispensable equipment in coatings, ink, cosmetics, and other industries. Its main function is to provide multi-functional dispersion.
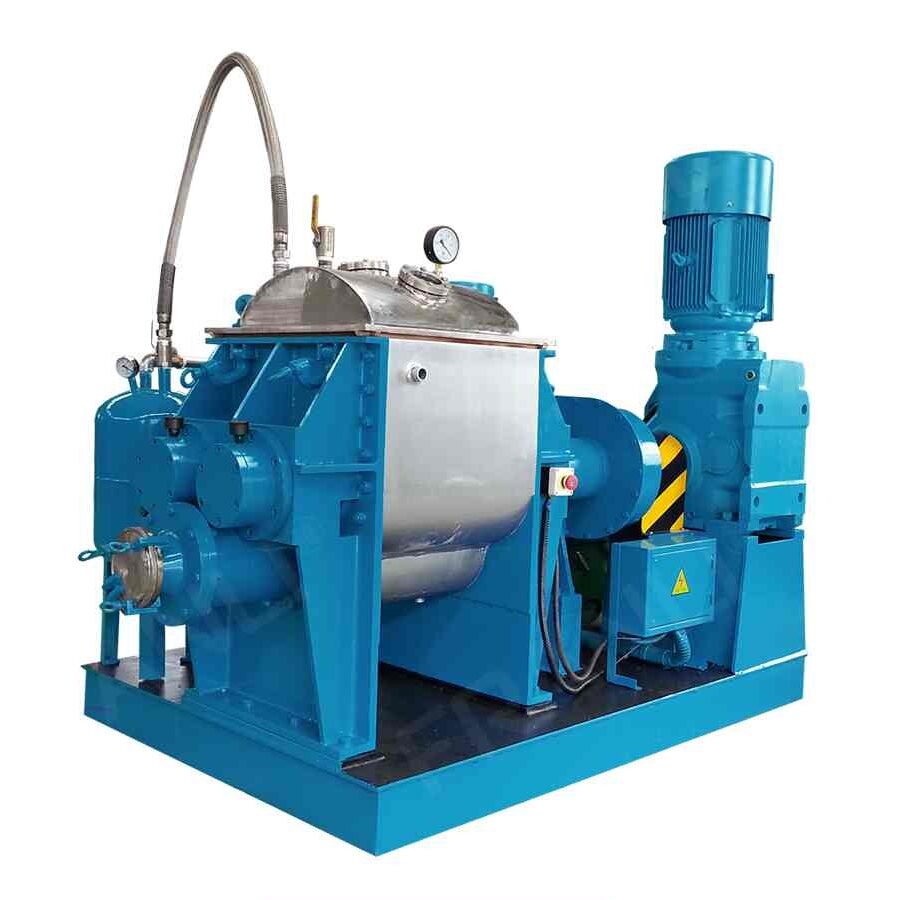
Z Blade Mixer|Shearing and mixing
The FRANLI z blade mixer is a mixer used for evenly mixing semi-solid materials. The mixer contained a U trough bowl with two Z shape blades that rotate in opposite directions for accurate blending of particles.
After Sales Support
News
Laboratory Reactor: Guide to Stirring System
The laboratory reactor is composed of a pot body, a pot cover, an agitator, a jacket, a support and transmission device, a shaft seal device, etc.
Grinding Media for Bead Mill | Zirconia Beads & Zirconium Silicate Beads
Bead mills mainly use grinding balls as media, and use impact, extrusion, and friction to achieve the final grinding effect, which mainly depends on the size and hardness of the grinding beads, the filling rate of the grinding beads, and the collision frequency adjustment between the grinding beads and the particles.
Overview of Laboratory Reactor
Laboratory reactors, also known as lab reactors, are essential tools in scientific research, product development, and process optimization. These reactors provide a controlled environment for conducting chemical reactions, mixing, dispersing, and homogenizing processes.
Bead mills | Manufacturing technology in various industries
Bead mills, also known as sand mills or grinding mills, are versatile machines widely used across various industries for the wet grinding and dispersion of solid particles in liquid media.
Ribbon Blender Mixer Equipment
A ribbon blender mixer, also known as a ribbon mixer or horizontal ribbon blender, is a powerful industrial machine designed for thorough and efficient blending of various materials.
What is A Stainless Steel Reactor?
Stainless steel reactors are essential equipment in various industries, including chemical, pharmaceutical, biotechnology, and food processing.