Home » Bead mills | Manufacturing technology in various industries
Bead mills | Manufacturing technology in various industries
Bead Mill
Bead mills, also known as sand mills or grinding mills, are versatile machines widely used across various industries for the wet grinding and dispersion of solid particles in liquid media.
Application: Paint, Adhesive, Battery, Pharmaceutical industry, Cosmetic
These bead mills play a crucial role in the production processes of numerous products, ranging from paints and coatings to pharmaceuticals and cosmetics.
Operating principles of bead mills
Bead mills operate on the principle of attrition, where small grinding beads collide with the material to be processed, resulting in particle size reduction and dispersion. The key components of a bead mill include:
1. Grinding chamber: A cylindrical chamber that houses the grinding beads and the material to be processed.
2. Rotor: A central component that agitates the grinding beads, creating a shearing effect and promoting efficient particle size reduction.
3. Grinding beads: Small, spherical particles made from materials like glass, ceramic, or steel, which collide with the material, breaking it down into smaller particles.
4. Motor: An electric motor that drives the rotor’s movement, with adjustable power and speed to control the milling process.
The choice of grinding beads and their material depends on the specific application and the desired end product. Common bead materials include zirconia, glass, and stainless steel.
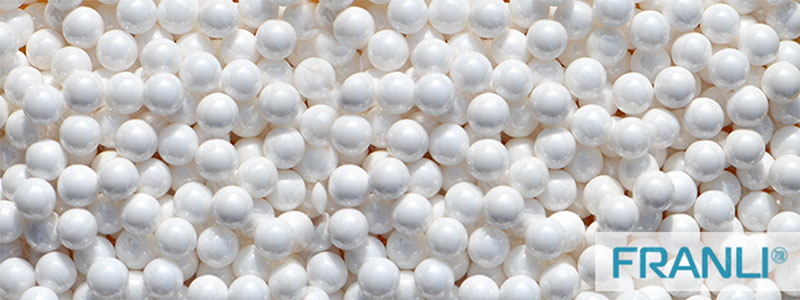
Bead mills in the paint and coatings industry
The paint and coatings industry extensively utilizes bead mills for the production of high-quality pigments and coatings. The manufacturing process typically involves the following steps:
1. Pigment dispersion: Raw pigments are combined with resins, solvents, and other additives in the bead mill’s grinding chamber. The high-speed agitation and shearing forces provided by the grinding beads break down the pigment agglomerates, ensuring uniform dispersion and optimal color development.
2. Particle size reduction: The bead mill’s grinding action reduces the particle size of the pigments and other solid components, resulting in a finer and more stable dispersion. This process improves the coating’s gloss, opacity, and overall performance.
3. Milling and mixing: Continuous milling and mixing in the bead mill ensure that all components are thoroughly incorporated, creating a homogeneous mixture ready for further processing or packaging.
Horizontal bead mills are commonly used in the paint and coatings industry due to their efficient grinding and dispersion capabilities.
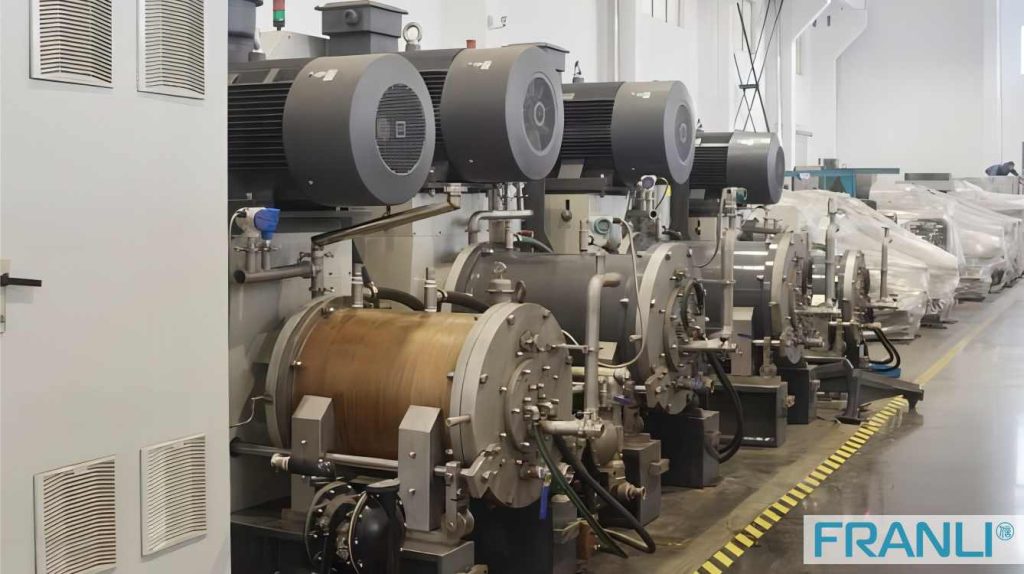
Bead mills in the pharmaceutical industry
In the pharmaceutical industry, bead mills play a crucial role in the production of finely dispersed suspensions and pharmaceutical formulations. The manufacturing process typically involves the following steps:
1. Active ingredient dispersion: The active pharmaceutical ingredient (API) is combined with excipients and a liquid medium in the bead mill’s grinding chamber. The grinding beads facilitate the dispersion and particle size reduction of the API, ensuring uniform distribution and improved bioavailability.
2. Nanosuspension production: Bead mills are capable of producing nanosuspensions, where the particle size of the API is reduced to the nanometer range. This process enhances the solubility and dissolution rate of poorly soluble drugs, improving their therapeutic efficacy.
3. Homogenization and stabilization: Continuous milling and mixing in the bead mill ensure that the formulation is homogenized and stabilized, preventing agglomeration and sedimentation of the dispersed particles.
Vertical bead mills are often preferred in the pharmaceutical industry due to their ability to process viscous materials efficiently and their suitability for producing small batch sizes.
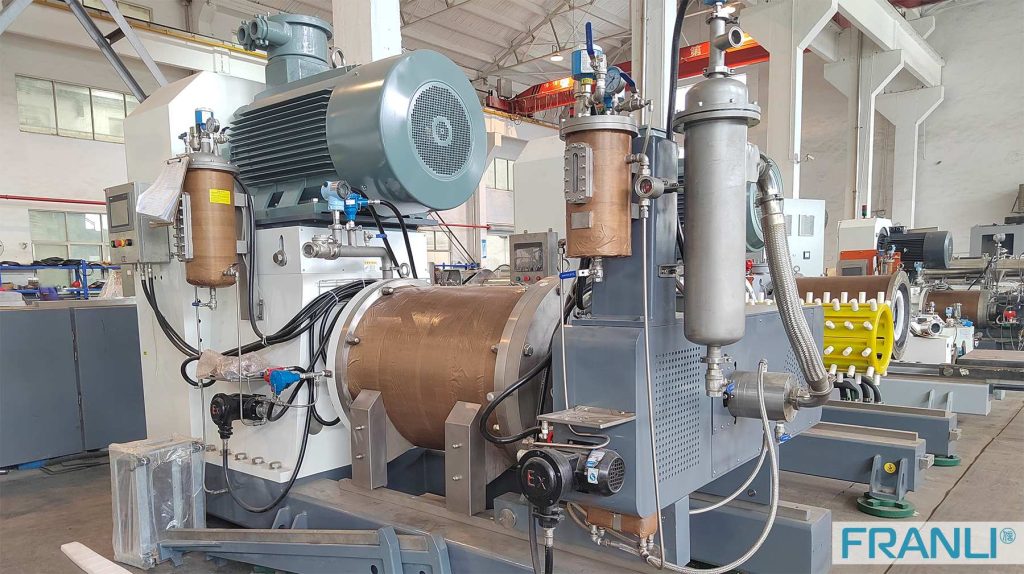
Bead mills in the cosmetics industry
The cosmetics industry relies on bead mills for the production of various formulations, including creams, lotions, and personal care products. The manufacturing process typically involves the following steps:
1. Pigment dispersion: Similar to the paint and coatings industry, bead mills are used to disperse pigments and other solid components in cosmetic formulations, ensuring uniform color distribution and optimal aesthetic properties.
2. Emulsion production: Bead mills facilitate the production of stable emulsions, such as creams and lotions, by dispersing the oil and water phases with the aid of emulsifiers and the grinding action of the beads.
3. Particle size reduction: The bead mill’s grinding action reduces the particle size of active ingredients and other solid components, improving their bioavailability and enhancing the overall performance of the cosmetic product.
4. Homogenization and stabilization: Continuous milling and mixing in the bead mill ensure that the formulation is homogenized and stabilized, preventing phase separation and ensuring consistent product quality.
Vertical bead mills are commonly used in the cosmetics industry due to their ability to process viscous materials and their suitability for small-scale production runs.
Bead mills in the food and beverage industry
Bead mills find applications in the food and beverage industry for the production of various products, including sauces, dressings, and beverages. The manufacturing process typically involves the following steps:
1. Ingredient dispersion: Raw ingredients, such as spices, herbs, and thickening agents, are combined with liquids in the bead mill’s grinding chamber. The grinding beads facilitate the dispersion and particle size reduction of these solid components, ensuring a smooth and homogeneous texture.
2. Emulsion production: Bead mills are used to produce stable emulsions, such as salad dressings and mayonnaise, by dispersing the oil and water phases with the aid of emulsifiers and the grinding action of the beads.
3. Particle size reduction: The bead mill’s grinding action reduces the particle size of solid ingredients, improving their dispersion and enhancing the overall flavor and mouthfeel of the product.
4. Homogenization and stabilization: Continuous milling and mixing in the bead mill ensure that the formulation is homogenized and stabilized, preventing separation and ensuring consistent product quality.
Basket mills, a type of bead mill, are commonly used in the food industry due to their efficient circulation and mixing capabilities, making them suitable for processing viscous materials.
Bead mills in the ceramics and minerals industry
Bead mills are employed in the ceramics and minerals industry for the production of various products, including ceramic glazes, frits, and mineral dispersions. The manufacturing process typically involves the following steps:
1. Raw material grinding: Raw materials, such as clays, minerals, and frits, are introduced into the bead mill’s grinding chamber. The grinding beads facilitate the particle size reduction of these materials, ensuring a uniform and fine dispersion.
2. Glaze and slip production: Bead mills are used to produce ceramic glazes and slips by dispersing and grinding the raw materials in a liquid medium. The grinding action ensures a homogeneous mixture and the desired particle size distribution.
3. Mineral dispersion: Bead mills are employed in the dispersion of minerals and other solid components in various applications, such as paints, coatings, and construction materials.
4. Homogenization and stabilization: Continuous milling and mixing in the bead mill ensure that the formulation is homogenized and stabilized, preventing agglomeration and sedimentation of the dispersed particles.
Horizontal bead mills are commonly used in the ceramics and minerals industry due to their efficient grinding and dispersion capabilities, as well as their ability to handle abrasive materials.
Pharmaceutical Wet Milling
The chemical industry utilizes bead mills for the production of various products, including pigments, dispersions, and specialty chemicals. The manufacturing process typically involves the following steps:
1. Pigment dispersion: Raw pigments and other solid components are combined with solvents and additives in the bead mill’s grinding chamber. The grinding beads facilitate the dispersion and particle size reduction of these materials, ensuring a uniform and stable dispersion.
2. Particle size reduction: The bead mill’s grinding action reduces the particle size of solid components, improving their reactivity and enhancing the overall performance of the chemical product.
3. Homogenization and stabilization: Continuous milling and mixing in the bead mill ensure that the formulation is homogenized and stabilized, preventing agglomeration and sedimentation of the dispersed particles.
4. Specialty chemical production: Bead mills are used in the production of various specialty chemicals, such as catalysts, inks, and coatings, by facilitating the dispersion and particle size reduction of solid components.
Horizontal and vertical bead mills are both used in the chemical industry, depending on the specific application and the viscosity of the materials being processed.
Advantages of bead mills in industrial production processes
Bead mills offer several advantages that make them indispensable in various industrial production processes:
1. Efficient particle size reduction: Bead mills are capable of reducing the particle size of solid components to the submicron or nanometer range, improving product performance and enhancing properties such as solubility, reactivity, and bioavailability.
2. Uniform dispersion: The grinding action of the beads and the high shear forces generated within the bead mill ensure uniform dispersion of solid particles in liquid media, preventing agglomeration and sedimentation.
3. Versatility: Bead mills can process a wide range of materials, including abrasive and viscous materials, making them suitable for various industrial applications.
4. Scalability: Bead mills are available in different sizes and configurations, allowing for scalability from small-scale laboratory operations to large-scale industrial production.
5. Continuous operation: Bead mills can operate continuously, facilitating efficient and high-throughput production processes.
6. Energy efficiency: Compared to other grinding methods, bead mills offer energy-efficient particle size reduction and dispersion, contributing to cost savings and environmental sustainability.
Bead mills are versatile and essential tools in various industrial production processes, contributing to the manufacturing of high-quality products across diverse sectors. From paints and coatings to pharmaceuticals and cosmetics, bead mills facilitate efficient particle size reduction, uniform dispersion, and homogenization of solid components in liquid media.
Welcome to send inquiry to us and let’s make a win win business together !
Guidelines For Bead Mill
Bead Mill(sand mill) helps many factories to improve production. Grinding for low viscosity, well-flowing material. Self-cycling cooling system. Don’t need the cooling pump. Franli produces Disc Bead Mill, Pin Bead mill, Turbine Nano Bead mill, etc. Optional material of inner chamber and disc: hardness Alloy, Zirconia, PU.
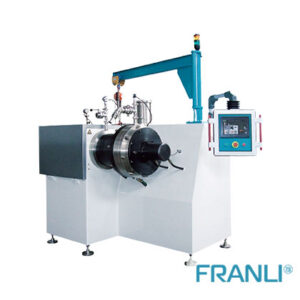
DYNO MILL – A DYNAMIC WAY TO GRIND EASIER
Dyno mill is nothing but an agitator bead mill. It is widely used in the production of paints, coatings, agrochemistry, and pharmaceutical products.
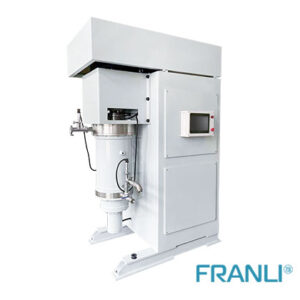
Role of Pearl Mill in the Nano Industry
Pearl Mill can handle both high and low viscosity materials. One is for Nano grinding materials, while the other is for high viscosity materials like offset ink. The operation of the Pearl Mill is straightforward, and all maintenance; may be handled quickly and efficiently. Adding grinding media from the feeding hole is simple.
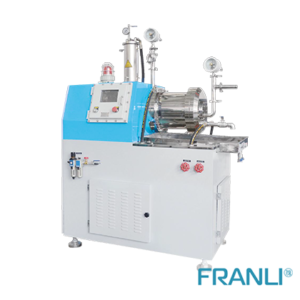
Guide to Bead Mills
The Bead mill is one of the main grindings and dispersing equipment in paint production. Bead mills for coatings are mainly divided into four categories: vertical, horizontal, basket, and special-shaped bead mills.
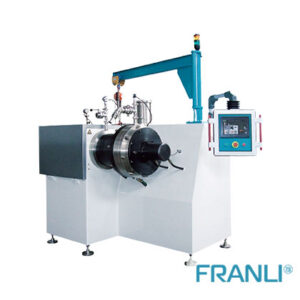
Dyno Mill|Coating & Inks
Dyno mill is a type of bead mill machine which is used in the coating industry specifically, in the manufacturing of inks products.
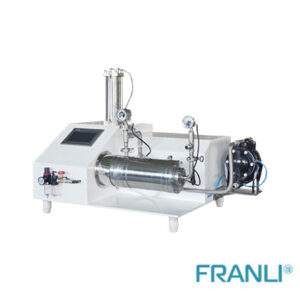
The structure and type of laboratory bead mill
The laboratory bead mill in the chemical experimental equipment, also known as the lab sand mill, is a kind of grinding equipment compared with the bead mill for industrial production.
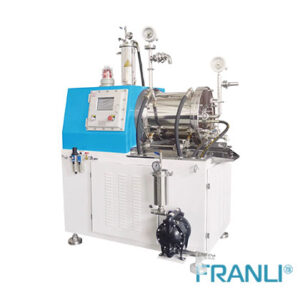
High Viscosity Material Grinding – Bar Pin Bead Mill
The bar pin bead mill is a machine suitable for ultra-fine dispersion and nano-scale grinding of water-based and solvent-based materials. The bar pin bead mill is one of the most widely used production types of equipment. With its very stable performance and sophisticated technology, it has been recognized by a wide range of users. The key thing to know is the characteristics of the bar pin bead mill, which is also the key to people’s favor of it.