Home » Role of Pearl Mill in the Nano Industry
Role of Pearl Mill in the Nano Industry
Pearl Mill
Details of Pearl Mill
- The frame of Pearl Mill
- Grinding system of Pearl Mill
- Double mechanical seal of Pearl Mill
- The transmission system of the Pearl Mill
- Grinding cylinder of Pearl Mill
Application: Paint, Adhesive, Battery, Pharmaceutical industry, Cosmetic
The media should not be discharged or grounded. However, the protective screen from the closed mill; can be removed. The replacement of the product only necessitates the use of a small amount of cleaning fluid. Pearl Mill is used in making offset oil ink and materials with a high viscosity In addition to making offset oil ink, it is also useful for printing ink, screen printing ink, condensed ink, gravure ink, letterpress ink, carbon black, and other high viscosity materials.
Characteristic of pearl mill
● Internal grinding media recirculation and high efficiency, two chambers, agitated media mills with a vertical configuration provide the highest product flow rates without crushing media compression.
● Has multiple grinding zone systems with two integrated grinding vessels in sequence, which grinds and disperse particles by shear force.
● Separation of grinding medium by centrifugal force.
● Has a closed and sealed system.
● The mill has wetted parts which cooled the materials.
● The wetted mill parts are made of special hardened stainless steel and tungsten carbide.
● The use of an inbuilt raising device to lower the grinding chamber will appear to be very easy.
● Along with the pivot, the grinding chamber can descend and spin.
● It can be used independently or in conjunction with a three-roller mill as part of a fully automated production line.
● Pearl mill has a low viscosity hence, used in automobile paint, topcoat, clear coat, printing ink, and digital ink, among other applications.
● For control, a PLC is used for comparable sketching and a touch screen (Optional).
● The pressure in the grinding chamber is automatically adjusted to select the best milling output. The mechanical sealing and bearing are coupled in an open mode to tackle the problem of a clash between the main shaft and the coupler in a high-viscosity state, allowing for more dependable and safe equipment operation.
● The interior double-spiral cooling channel can distribute the heat during high-viscosity operation.
● The German brand “BURGMANN” is used for mechanical sealing, and the Japanese brand “NSK” is for bearings. The dynamic separator is built of powder metallurgy. This prevents the substance from leaking.
● The magnetic filter is rated at 8000 Gauss.
● When combined with a three roller mill, the material can be milled to the ideal fineness in just one pass, resulting in a significant boost in inefficiency.
Operation of pearl mill
The purpose of these operating instructions is to acquaint the user with the equipment and its intended usage. The Pearl mill comes with crucial instructions on how to use the equipment safely and effectively. Following these guidelines helps minimize risk, lower maintenance costs and downtime, and extend the mill’s dependability and longevity.
There should be national rules and regulations to avoid accidents and preserve the environment in addition to the instruction manual.
To ensure safe and correct operation, users must adhere to widely established technical norms as well as the equipment’s operating instructions and any applicable national or local laws and regulations on accident prevention and environmental protection. These Pearl mill operating instructions are exclusively for the order confirmation number listed on the cover page. This number can also be seen on the nameplate of the pearl mill.
Pearl mill safety instructions
Observe the generally legitimate, legal, and otherwise binding requirements for accident avoidance in addition to those mentioned in the operating instructions! These kinds of liabilities might apply to things like handling dangerous products or wearing protective gear.
Only operate the equipment when there are no technical difficulties and only as advised, in line with the operating instructions! Above all, address any issues that may jeopardize safe operation as soon as possible.
Only after contacting the manufacturer can any back fitting or equipment adjustments be made. The spare components must meet the manufacturer’s technical requirements. Using authentic spare parts ensures this will always be the case. You are no longer responsible for any later injury if you use non-original spare parts that you have got from other sources.
Cover or tape any openings that must be protected from moisture for safety or operational reasons before washing the mill with water or other cleaning chemicals.
Only certified professionals should transport and assemble mills! Please ensure that the equipment is raised as low as possible during transit for safety reasons! Staying beneath overhead loads is not permitted!
Pearl Mill advantages
Particles move through the grinding chamber utilizing high-speed shear force and the impact action of zirconium beads to produce micro-level grinding in this mill’s working principle. When used, the mill provides several advantages. These include;
● The speed of the mill is very high, attaining maximum production within a short time.
● It has a dynamic separator that separates the particles at the exit. This mechanism enables the attainment of finer particles.
● It has a smaller crushing medium, between 0.03 -0.1mm
● It also has a mechanical seal on both sides.
● Has the best grinding effect due to the presence of conic grinding and mixing tanks. The materials are pushed from the bottom to the top and discharged from the top, resulting in complete particle crushing and the creation of finer particles.
● Cleaning the mill is very easy since it self-cleanse hence no manual work is needed.
● Since the mill grinds particles in an enclosed crushing chamber, air pollution, which may affect staff, is minimal.
● The mill is easy to operate. Grinding media replacement requires the least amount of time and cleanliness
● The vertically integrated design integrates the pearl mill host, feeding pump, and electrical control box as a whole making the mill take less space.
Franli companies tend to manufacture different varieties of Pearl Mill mills used in the production of TOKA ink, PEONY, Kingswood inks and many more. The company provides a two years warranty for its customers globally. A team of professional experts offers training and installation. Therefore, this is the best company to shop this type of mill for your material.
Welcome to send inquiry to us and let’s make a win win business together !
Guidelines For Bead Mill
Bead Mill(sand mill) helps many factories to improve production. Grinding for low viscosity, well-flowing material. Self-cycling cooling system. Don’t need the cooling pump. Franli produces Disc Bead Mill, Pin Bead mill, Turbine Nano Bead mill, etc. Optional material of inner chamber and disc: hardness Alloy, Zirconia, PU.
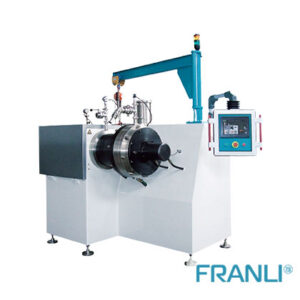
DYNO MILL – A DYNAMIC WAY TO GRIND EASIER
Dyno mill is nothing but an agitator bead mill. It is widely used in the production of paints, coatings, agrochemistry, and pharmaceutical products.
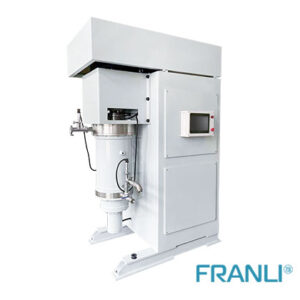
Role of Pearl Mill in the Nano Industry
Pearl Mill can handle both high and low viscosity materials. One is for Nano grinding materials, while the other is for high viscosity materials like offset ink. The operation of the Pearl Mill is straightforward, and all maintenance; may be handled quickly and efficiently. Adding grinding media from the feeding hole is simple.
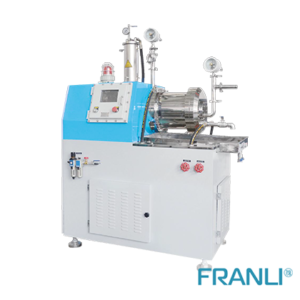
Guide to Bead Mills
The Bead mill is one of the main grindings and dispersing equipment in paint production. Bead mills for coatings are mainly divided into four categories: vertical, horizontal, basket, and special-shaped bead mills.
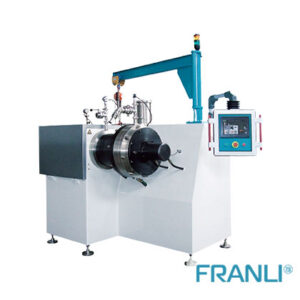
Dyno Mill|Coating & Inks
Dyno mill is a type of bead mill machine which is used in the coating industry specifically, in the manufacturing of inks products.
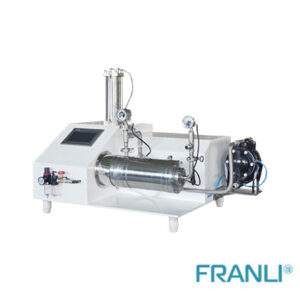
The structure and type of laboratory bead mill
The laboratory bead mill in the chemical experimental equipment, also known as the lab sand mill, is a kind of grinding equipment compared with the bead mill for industrial production.
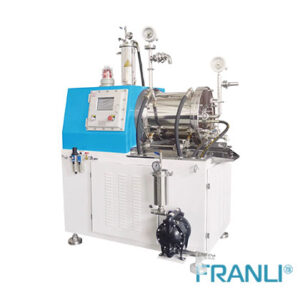
High Viscosity Material Grinding – Bar Pin Bead Mill
The bar pin bead mill is a machine suitable for ultra-fine dispersion and nano-scale grinding of water-based and solvent-based materials. The bar pin bead mill is one of the most widely used production types of equipment. With its very stable performance and sophisticated technology, it has been recognized by a wide range of users. The key thing to know is the characteristics of the bar pin bead mill, which is also the key to people’s favor of it.