Home » DYNO MILL – A DYNAMIC WAY TO GRIND EASIER
DYNO MILL – A DYNAMIC WAY TO GRIND EASIER
Dyno Mill
Dyno mill is nothing but an agitator bead mill. It is widely used in the production of paints, coatings, agrochemistry, and pharmaceutical products. They are available in different designs and sizes. The designs can vary from small laboratory models up to large mills for production plants.
Details of Dyno mill
- The frame of the Dyno mill
- Grinding system of Dyno mill
- Double mechanical seal of Dyno mill
- The transmission system of the Dyno mill
- Grinding cylinder of Dyno mill
Application: Paint, Adhesive, Battery, Pharmaceutical industry, Cosmetic
Two types of grinding are there based upon the materials used: dry grinding and wet grinding. The dyno mills are classified in a variety of ways. The stirring shaft can be classified into three types based on its structure and shape: disc type, rod type, and rod disc type (both bump types). Vertical and horizontal grinding cylinders can be classified based on their layout. The cylinder can be classified into the laboratory, small, medium, big, and super large categories based on its volume. It can be split into static and dynamic separation mills according to the medium separation method.
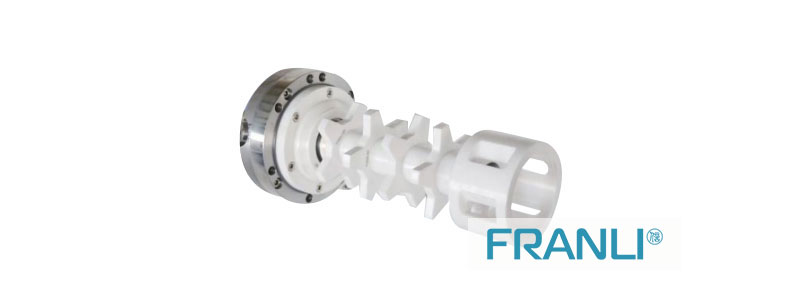
Working Principle of a Dyno Mill
This dyno mill consists of a horizontal grinding container that is used for dispersion and the finest wet grinding. This process is carried out in a completely enclosed system. Dyno mill working principle is suitable for mixing and grinding materials in two types: dry grinding and wet grinding. Agitator discs which are designed especially are mounted symmetrically on a shaft. They transfer the energy required for dispersion and wet grinding to the spherical grinding beads. Their shape and arrangement ensure optimal energy input also used to distribute the grinding beads evenly in the grinding container. The products are feed into the mill by an external pump. All the machine parts which are in contact with the product are subject to wear. They are easily replaceable.
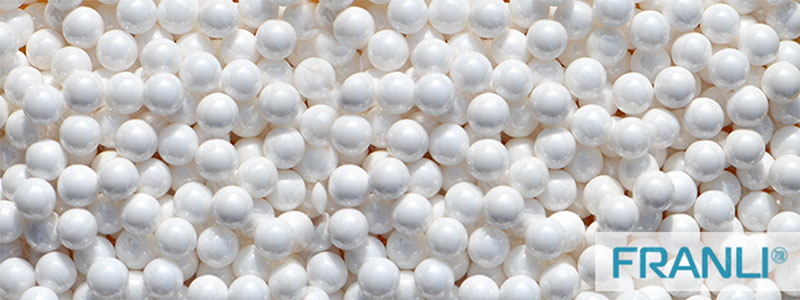
The grinding containers are constructed in a very slim manner. This ensures a narrow residence time distribution. The spiral flow of the cooling water in the outer jacket creates a high cooling efficiency. This high cooling efficiency allows the processing of highly viscous products which are temperature–sensitive. Coming to the grinding beads, they are made out of glass, ceramic, or steel depending upon the application and mill size. The size can vary from 0.15mm to 3.0 mm. The grinding result is directly influenced by the size and type of grinding dyno mill suppliers.
The materials used also depend on the size of the mill and its application. Wear parts are made out of chrome-plated stainless steel, alloyed stainless steel, tungsten carbide, or synthetic materials. There is a dynamic gap separator or a special slot screen that helps in retaining the grinding beads in the mill. This separation system again depends upon the size and the products used.
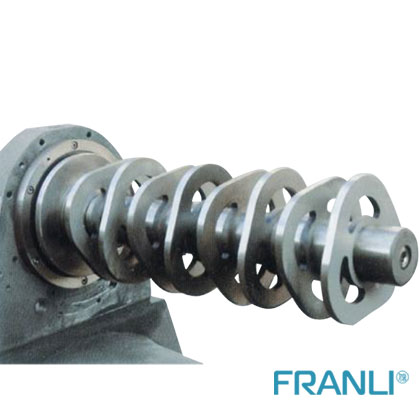
Simplified handling techniques involved
This machine is designed in such a way that the cleaning process becomes very much easier. The guide rails that are integrated into the mill facilitate the dismantling of the milling. The cooling cylinders are made out of a combination of stainless steel and aluminum. This provides lightweight handling. Fast product changes are enabled due to small volumes of the grinding chamber. Only a small amount of cleaning agents are required as the cleaning process is very simple. There will be no need for opening the grinding chamber to change the separation system. There will be an increased lifetime of the screen.
Advantages and benefits of using a Dyno Mill
Some of the noted advantages of this machine are listed out here:
The housing is made out of stainless steel so that the cleaning process becomes easier. It has a higher ability to process highly viscous products. Appropriate mill sizes are available based upon the application. Its improved ability enables the handling of foaming products effectively. High throughputs and simple handling of the machine. The screen has a longer lifetime. It can grind even in the nanometer range. There is a higher possibility for fast product changes at considerable costs. Pass mode and the circulation mode have optimal suitability. A batch size of one liter is possible.
The new dyno mill generation was consistently designed to increase throughput. Increased throughput offers greater flexibility in the selection of process parameters. High throughputs in the circulation process usually have a positive effect on production capacity. A higher number of circulations, in addition to increasing production capacity, can lead to a narrower particle size distribution.
The combination of optimized bead circulation and a much larger cross-sectional area for flow through the screen improves the ability to process highly viscous products significantly. In this case, the directed axial flow of the beads across the screen surface removes coarse particles from the screen surface, allowing for better flow through the screen. Because this self-cleaning effect prevents blockages, the free flow through the screen is not reduced. An increase in pressure, which can occur with highly viscous products, is thus avoided.
Price of Dyno Mill in Turkey
The dyno mill price range can vary based upon the manufacturers, locations, and other factors. Listed below are the price details of the agitator bead mills which are only approximate. The price of Lab Bead Mill is around Rs. 1.20 Lakh. The price of a Bead Mill is around Rs. 2.50 Lakh. The price of Vertical Bead Mill is around Rs. 3.50 Lakh.
Fields of Application
This type of dyno mill is most commonly used in the production of paint and varnishes, printing inks, coatings, pigment and dyestuffs production, audio and videotape coating, automobile coatings, food industries, filling, agrochemicals, filters for paper and plastic industries, thermal and fax paper coating, life sciences, biotechnology, and also in microbiology and biochemistry.
Among most of the dyno mill manufacturer, FRANLI manufacturer, specializes in designing efficient dyno mills that use the principle of collision, squeeze, and friction between the grinding media to crush the materials. Those are most commonly applied in the field of Printing ink, offset ink, gravure ink, carbon black, and UV ink production. This manufacturer gives different classifications of dyno mill such as disk type, rod type, and rod disk type.
Welcome to send inquiry to us and let’s make a win win business together !
Guidelines For Bead Mill
Bead Mill(sand mill) helps many factories to improve production. Grinding for low viscosity, well-flowing material. Self-cycling cooling system. Don’t need the cooling pump. Franli produces Disc Bead Mill, Pin Bead mill, Turbine Nano Bead mill, etc. Optional material of inner chamber and disc: hardness Alloy, Zirconia, PU.
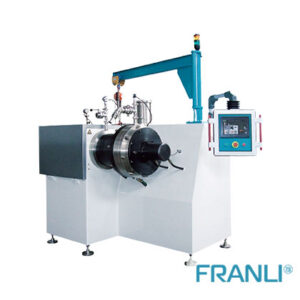
DYNO MILL – A DYNAMIC WAY TO GRIND EASIER
Dyno mill is nothing but an agitator bead mill. It is widely used in the production of paints, coatings, agrochemistry, and pharmaceutical products.
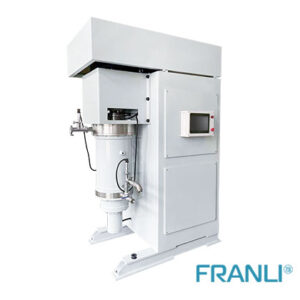
Role of Pearl Mill in the Nano Industry
Pearl Mill can handle both high and low viscosity materials. One is for Nano grinding materials, while the other is for high viscosity materials like offset ink. The operation of the Pearl Mill is straightforward, and all maintenance; may be handled quickly and efficiently. Adding grinding media from the feeding hole is simple.
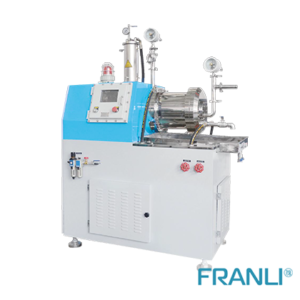
Guide to Bead Mills
The Bead mill is one of the main grindings and dispersing equipment in paint production. Bead mills for coatings are mainly divided into four categories: vertical, horizontal, basket, and special-shaped bead mills.
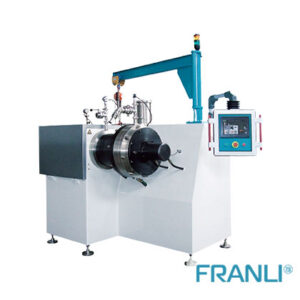
Dyno Mill|Coating & Inks
Dyno mill is a type of bead mill machine which is used in the coating industry specifically, in the manufacturing of inks products.
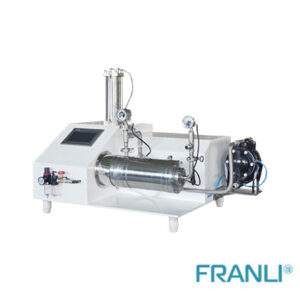
The structure and type of laboratory bead mill
The laboratory bead mill in the chemical experimental equipment, also known as the lab sand mill, is a kind of grinding equipment compared with the bead mill for industrial production.
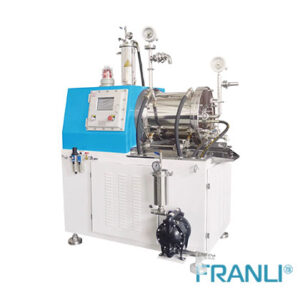
High Viscosity Material Grinding – Bar Pin Bead Mill
The bar pin bead mill is a machine suitable for ultra-fine dispersion and nano-scale grinding of water-based and solvent-based materials. The bar pin bead mill is one of the most widely used production types of equipment. With its very stable performance and sophisticated technology, it has been recognized by a wide range of users. The key thing to know is the characteristics of the bar pin bead mill, which is also the key to people’s favor of it.