TRS-Three Roll Mill For Lipstick
Three roll grinders are used in various chemical industries to produce medium to high viscosity products. These machines pass through all kinds of pigments, UV and offset inks, decorative coatings, and lubricants, achieving the highest fineness in cosmetics and lipsticks and the electronics industry.
Three rollers for easy operation and cleaning offers three unique roller mills for hydraulic and laboratory use. Each has its advantages and capabilities and can meet completely different needs.
Here are triple roll mills that are unlike anything you’ve seen before.
- Wide range of applications
- High strength and high wear resistance
- uniform pressure
- easy to use
- Fast hydraulic cooling
Application

Coating

Cosmetic

Battery

Graphite

Agrochemistry

Adhesives
Frequently Asked Questions
A triple roll mill consists of 3 horizontally arranged rolls rotating in the opposite direction and at different speeds. The used material to be milled should be placed between the feed roller and the hard roller and is transferred from the middle roller to the aprons roller by sticking.
It is dispersed by the shears force between the adjacent rollers. The smaller the gap between the rolls, the higher the shear force, lower the yield. Hole settings on the order of 0.001″ is common.
The crushed material is scraped off the deck rollers with a starter blade. This cycle can be repeated to improve the dispersions or until the particle size balances are achieved.
Although the triple roll mill is a traditional technique, inherently low-powered and requiring skilled operators, it is probably the best strategy for preparing high-performance particle dispersions for paint, ink, cosmetic, ointment, dental composite, and various viscous materials.
triple roll mill are typically assembled. While removing the mills from the container in which it is shipped, special care must be taken not to damage the working surface of the Milling rolls. A perfect roller surface is essential for the proper operation of the mill.
The mill must be bolted down before it can be put into operation. A solid base is necessary, especially when building large models. Once the mill has been leveled as well as bolted down, the connection and adjustment of the {electrical} control elements must be done by qualified electricians.
The take-off knives on the locking apron are a sharp innovation and should always be handled with care. Due to its precise positioning, the blade contacts the roller just above the centerline and is paralleled.
Check the optimal hole setting as per your product to maximize through it without compromising dispersion quality.
Don’t allow the mill to dry out. When the production run is almost complete, open the rollers and remove the aprons.
Don’t wear loose clothing or equipment that could be caught on the roller.
The shaft journal is held in place by balls or rollers bearing. We recommend lubricating the bearings once a month.
Hot sale three roll mill
TRS-Three Roll Mill For Lipstick
Franli TRS three roll mill has below technical parameter and features.
1.Roll diameter: 150mm, Working length: 300
2.Roll speed radio:1: 2.3 :5.3
3.Different material chosen for roll, high wear-resistant alloy steel roll and ceramic roll
- The hardness of alloy steel roller is 68-75
- The Moh’s hardness of ceramic roller is 9
4.With water cooling system, the roll inside can pass the cooling water, which can keep the roll temperature as a balance condition to avoid material damaged.
For some special material, for example: epoxy resin, heating type three roll mill can be customized.
5.Adjustable table for tank, which the height of the table can be adjusted according to the tank height.
6.Adjustable speed is optional to fit different viscosity of different materials.
The work of the three roll mill
The functional design of the three roll mill makes it one of the first tasks in the method of separating tiny particles. The application of three-roll mills is also evident in mixing, refining, homogenizing or dispersing viscous materials fed to them. How does the three-roll mill realize these functions? The answer to this question can be found in the design of the three roll mill.
Working principle of three roll mill
You can find three horizontally placed rolls in a three-high mill, all rotating in opposite directions at different speeds. The material you want to mill must be placed between the center and the feed roller. The material is then transferred from the center roll to the baffle roll by the adhesive properties. Now, the shear force between the rolls helps to create the dispersion.
It is important to note that shorter distances between the rolls will generate more shearing forces and at the same time reduce throughput. However, you may encounter common gap settings in measurements of almost 0.001 inches. You can scrape the crushed material off the apron roller with the help of a take-off knife. All processes must be repeated again for improving dispersion or until the stage of reaching particle size equilibrium.
If interested, please contact Franli.
Related production lines
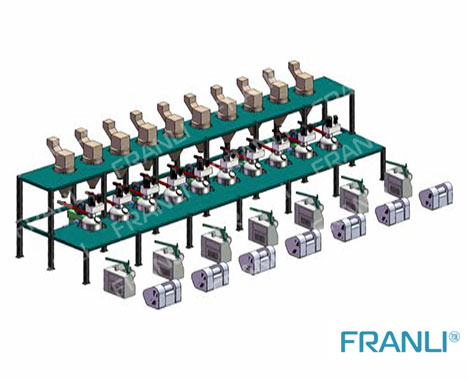
Offset Ink machine line
FRANLI is specialized in offset ink full line production for 20+ years. Helped customer save the cost, save the man power, also save the space.
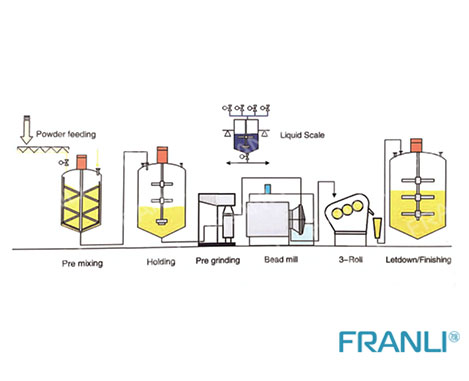
Offset Ink, UV Ink machine line
The FRANLI engineering company, offer the full set of UV INK Production Line, we can make the full drawing according with your factory size, formulas, weather and safety system.
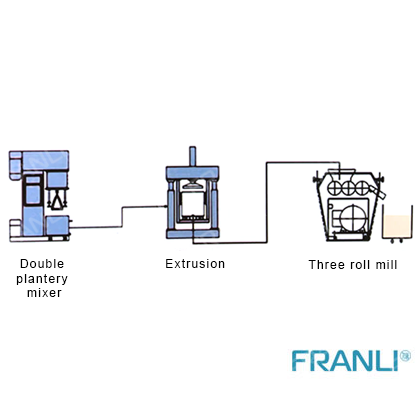
PCB INK Machine line
FRANLI supplies all equipments for the production of PCB inks, from the powder feeding station to the filling part.
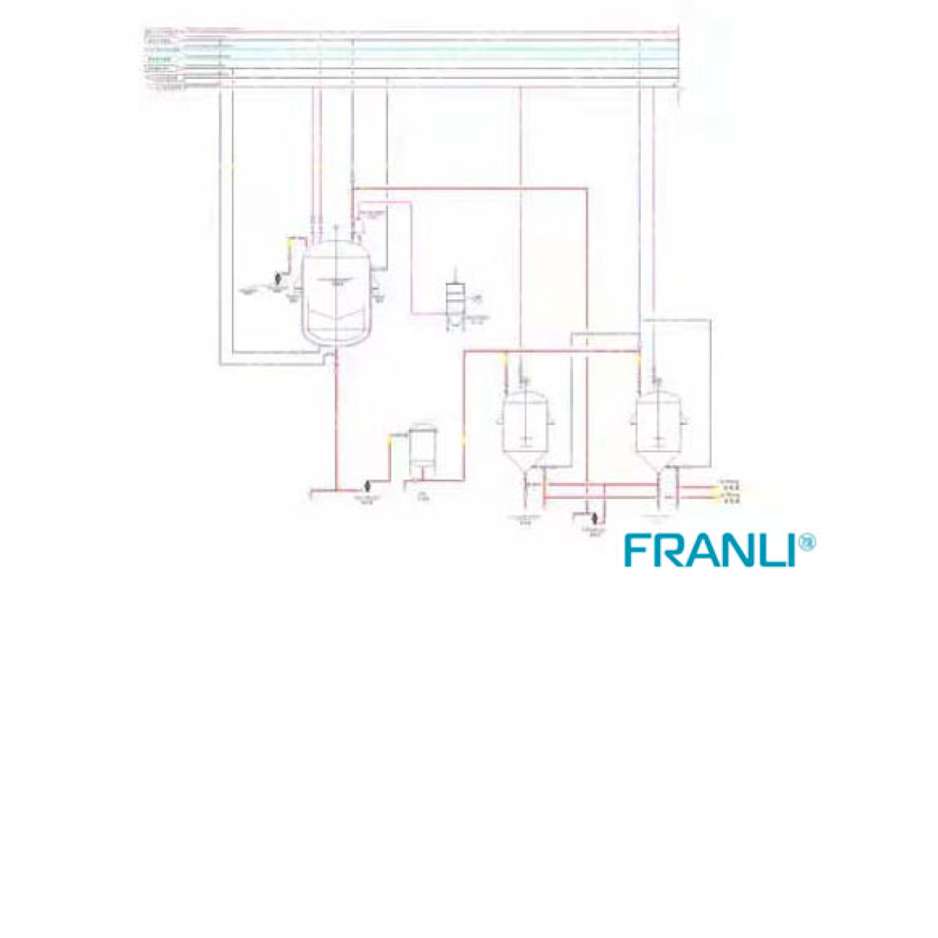
EW-pesticide line
The EW production line mainly mixes raw materials, solvents, and emulsifiers through a reactor (oil-based).
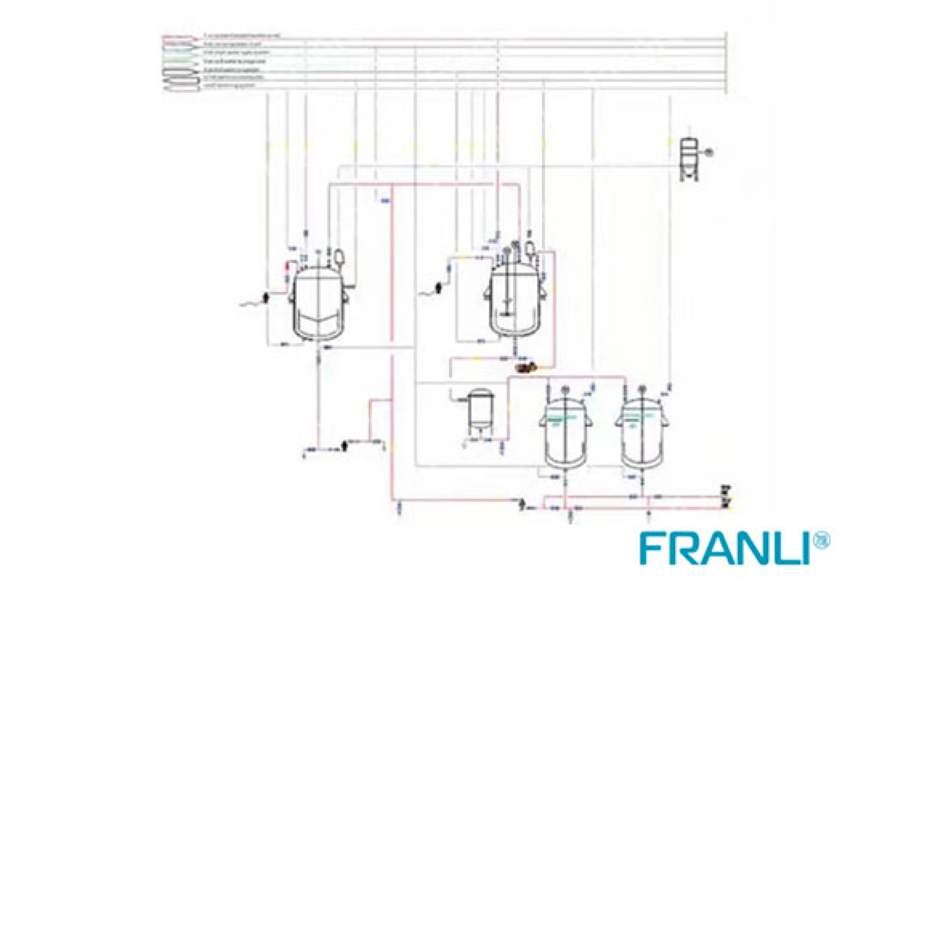
SL_EC pesticide line
The EC production line is mainly composed of an agitator mixer, bag filter, filling machine, etc.
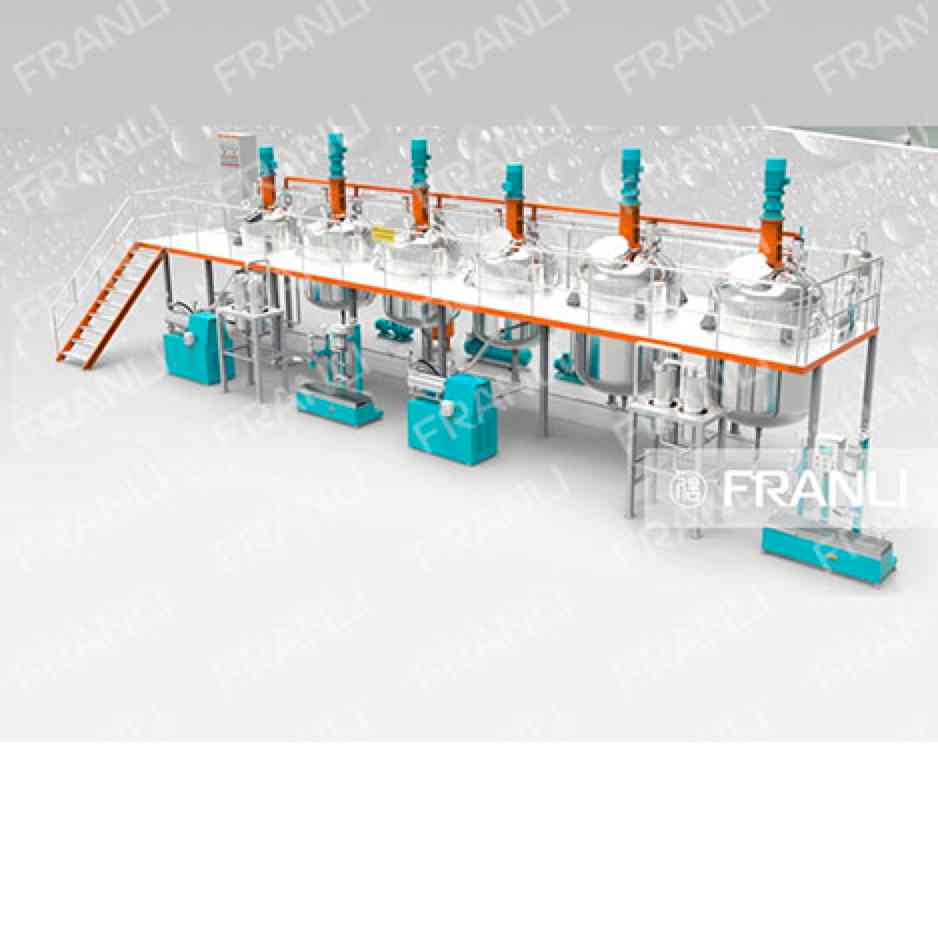
Automotive Paint machine line
The automotive paint machine line is mainly for the production and grinding of automotive paint, Automotive paint has many layers, such as Primer/electrophoretic layer, Medium coat, Colored coat, and Clearcoat.
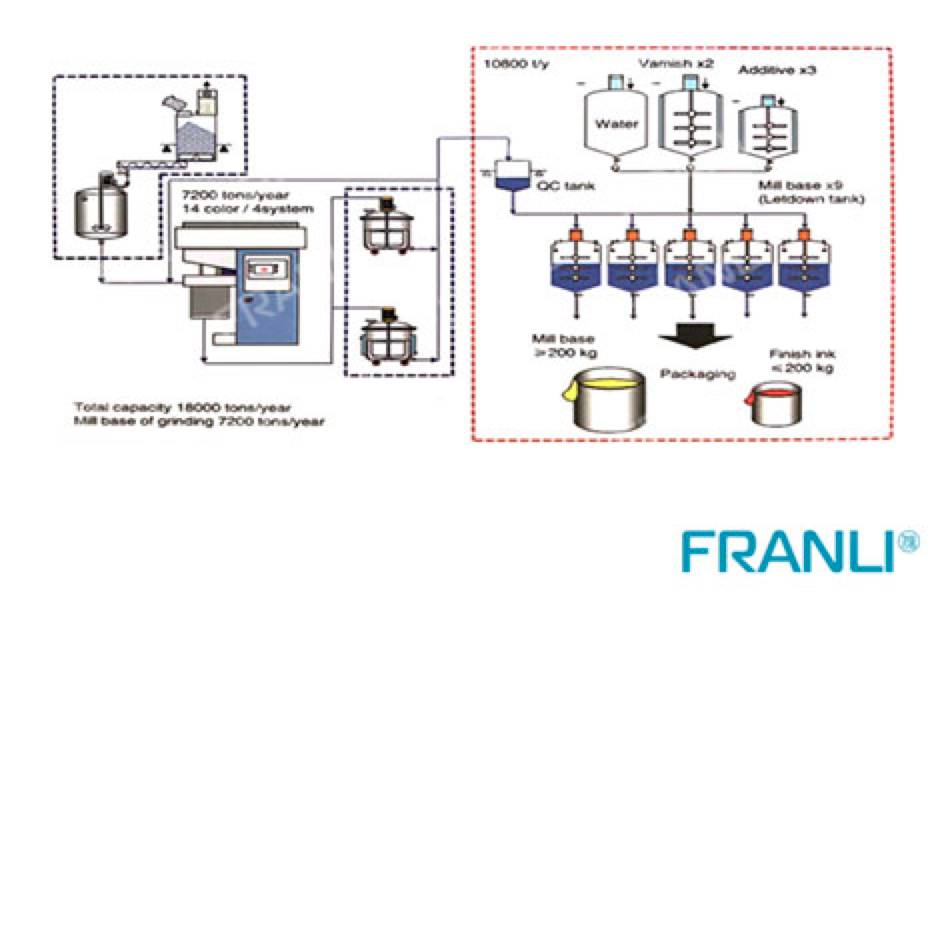
Digital Ink machine line
Franli has professional experience for digital ink machine line, we offered hundreds customers to expand production, or build up new project.