Home » Quality Bead mill Manufacturer From China
Quality Bead mill Manufacturer From China
The bead mill is one of the most advanced and efficient grinding equipment with wide material adaptability. The entire grinding cavity has a narrow space, and the gap between the levers is small. It has the characteristics of intensive grinding energy. It is equipped with a high-performance cooling system and automatic control system. , it can easily realize the long-term processing and continuous discharge of materials. After the continuous upgrading and transformation of franli engineers, the production efficiency of the bead mill can reach twice that of the ordinary bead mill. A bead mill, also known as a sand mill, is mainly used for wet grinding of chemical liquid products, electronic paste, ink, and paint. According to the performance, bead mills can be divided into horizontal bead mills, basket bead mills, vertical bead mills, etc.
The bead mill is mainly composed of the body, the grinding drum, the sanding disc (lever), the grinding medium, the motor, and the feeding pump. The franli bead mill manufacturer sets the function of controlling the speed of the feeding, mainly for the control of the feeding pump, not only that, the grinding media of the bead mill can be of different types. For example, the commonly used grinding media are generally divided into zirconia beads, glass beads, zirconium silicate beads, etc. The grinding effect of different grinding media is also different.
Bead mill design principle:
The bead mill adopts an eccentric disc grinding structure and is arranged in sequence. The system overcomes the disadvantage of uneven distribution of grinding media in traditional grinding machines, enabling the grinding media to obtain large energy transfer and high grinding efficiency. Sealing, good sealing effect, and reliable operation, the separation system adopts a large flow ldc dynamic grid slot separator, the discharge port will not be blocked under large flow conditions, the flow area is up to 0.05-2.0mm, and 0.1 mm can be used. Grinding media above mm.
The franli horizontal bead mill adopts the closed design of the eccentric disc grinding chamber. The grinding discs are installed on the stirring shaft in sequence, which overcomes the disadvantages of uneven distribution of grinding media and poor particle size distribution after grinding in traditional horizontal bead mills. Under the action of the material pump, it enters the grinding chamber. The design of the inlet is at one end of the drive connection flange. The flow direction of the material is opposite to the bottom end of the mechanical bearing, which greatly reduces the pressure on the mechanical seal and prolongs its service life. During the high-speed operation of the eccentric disk, the mixture of the material and the grinding medium move relatively, so that the solid particles of the material are effectively dispersed, sheared, and ground, and after passing through the dynamic large-flow rotor gap separation filter, the product with perfect fineness is obtained. Due to different products, the grinding process has certain differences. The factory can adopt independent batch circular grinding and series grinding processes.
Features of franli bead mills
1. The medium distribution in the grinding chamber of the horizontal bead mill is uniform, the grinding efficiency is high, the start-up with load is easy, the operation is convenient, and it can be designed to be large. However, the energy density (installed power per unit volume) is low, so the grinding fineness is limited;
2. The medium distribution of the vertical bead mill is uneven, the grinding efficiency is low, and it is difficult to start with the load. The advantage is that there is no mechanical seal and the structure is simple;
3. The horizontal bar grinding bead mill has high energy density, short grinding cylinder, large filtering area of media separator, short material residence time, good heat dissipation effect, high grinding efficiency, and narrow product particle size distribution. Generally used for large flow circulating grinding process of difficult-to-grind materials;
4. The vertical bar bead mill not only has pins arranged on the stirring shaft but is also often arranged on the inner wall of the cylinder. High energy density and high grinding strength. Mainly used for high viscosity materials, such as offset printing ink, and uv ink production.
Franli is a bead mill manufacturer and supplier with 20+ manufacturing experience. Its bead mills have several invention patents and obtained several certificates, helping factories in dozens of countries to solve the grinding problems and efficiency, if you are looking for a suitable bead mill manufacturer, you can get in touch with franli directly.
Copyright Notice :
This article only represents the author’s point of view.
This article is published under the authorization of the author.
Source: Franli
This article address : Quality Bead mill Manufacturer From China
Related Products
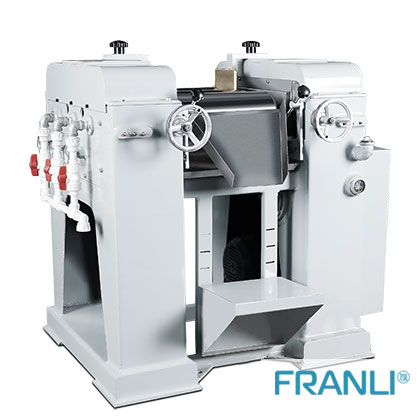
TRS-Three Roll Mill For Lipstick
TRS Three roll mill is widely used in milling paste material including paint, inks, China ink, pigment, coatings, food, cosmetics, and so on.
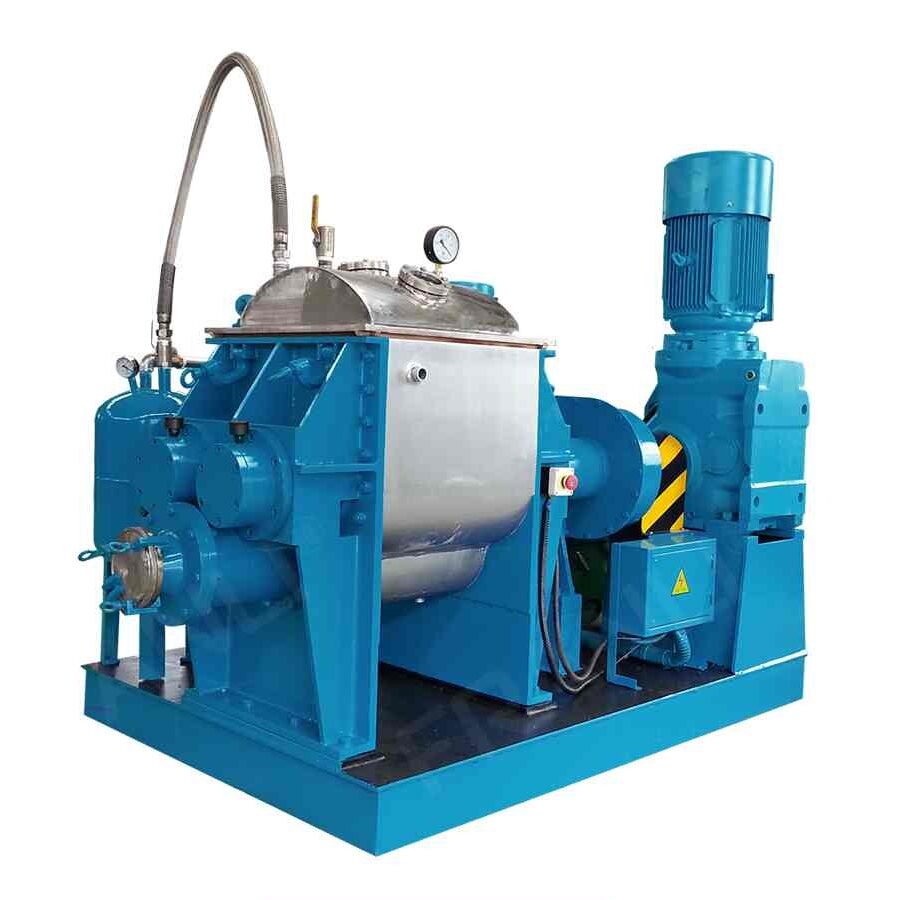
Z Blade Mixer
The Z blade mixer is made for extensive mixing, kneading, and stabilizing strong and high viscous materials, such as bubble gum bases, bread, caramel mass, body wash platform, and glue.
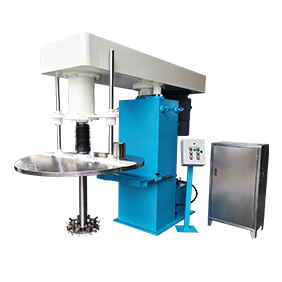
High Speed Disperser
Architectural waterproof coating production equipment The preparation process of the high-speed disperser machine mainly includes the dispersion of pigments and fillers, grinding, coating preparation, toning, etc.
News
Laboratory Reactor: Guide to Stirring System
The laboratory reactor is composed of a pot body, a pot cover, an agitator, a jacket, a support and transmission device, a shaft seal device, etc.
Grinding Media for Bead Mill | Zirconia Beads & Zirconium Silicate Beads
Bead mills mainly use grinding balls as media, and use impact, extrusion, and friction to achieve the final grinding effect, which mainly depends on the size and hardness of the grinding beads, the filling rate of the grinding beads, and the collision frequency adjustment between the grinding beads and the particles.
Overview of Laboratory Reactor
Laboratory reactors, also known as lab reactors, are essential tools in scientific research, product development, and process optimization. These reactors provide a controlled environment for conducting chemical reactions, mixing, dispersing, and homogenizing processes.
Bead mills | Manufacturing technology in various industries
Bead mills, also known as sand mills or grinding mills, are versatile machines widely used across various industries for the wet grinding and dispersion of solid particles in liquid media.
Ribbon Blender Mixer Equipment
A ribbon blender mixer, also known as a ribbon mixer or horizontal ribbon blender, is a powerful industrial machine designed for thorough and efficient blending of various materials.
What is A Stainless Steel Reactor?
Stainless steel reactors are essential equipment in various industries, including chemical, pharmaceutical, biotechnology, and food processing.