Home » Everything You Need to Know About a 3 Roll Mill
Everything You Need to Know About a 3 Roll Mill
In the three roll mills, fine dispersing happen after pre-dispersion. The three roll mills require two or three passes to attain the needed coloristic properties or particle size. Its feeding is often done by the pumps or press-out systems. Cleanability is a major benefit of the three roll mills. On just one machine, it is possible to produce numerous small batches of various colors.
Advantageous features such as cleanability, defined stress, extremely small hold-ups, and no possible cross-contamination are still not repeated by other technologies. However, hydraulic systems, mechanical systems of roll pressing are not even comparable with the automated machines present these days.
How a 3 Roll Mill Operates and Its Advantages?
The three roll mills are composed of basically three horizontally placed rolls that rotate in completely opposite directions at various speeds. The material which will be milled is then positioned between the center rolls and the feed. After that, the material is transferred from center rolls into the apron rolls, and this happens by adhesion.
Between the adjacent rolls, there are shear forces that produce dispersion. By reducing the distance present between the rolls, greater shear is produced. However, the distance reduction between rolls reduces the throughput. The gap settings with a range of nearly 0.001” are quite common.
Materials that are milled are taken out from an apron roll through the take-off knife. This cycle can also be repeated in order to enhance the dispersion or to reach the equilibrium of particle size. A three roll mill technology with low throughput generally needs skilled operators, but it is the best method to prepare a dispersion of fine particles in inks, cosmetics, paints, dental composites, ointments, and several viscous materials.
There are also many advantages of the 3 roll mills, and some of them are given below.
- It produces fine particles which show better product quality. The three roll mills guarantee that the product will pass in both the shear zones.
- The controlled energy input can increase precise processing.
- Powder clumps and agglomerates break up and completely homogenize.
- It generates less heat than most mills.
- A 3 roll millhas very less loss of moisture.
- It has a good work environment as the machine noise level is low.
- The three roll mills are energy-saving or energy-efficient.
Certain Finest Practices for Efficient and Safe 3 Roll Milling
- Take Proper Care:
The three roll mills usually come fully assembled when normally supplied. While removing it from the container of shipping, do take proper care and handle gently in order to prevent any damage that may happen in the rolls’ working surfaces. The damage-free roll surfaces are very important for the mills to function properly.
- A Good Installation is Necessary:
Before getting the mill to operate, it is important to make sure that it is bolted well in its place. Also, it requires a solid base, especially for the models of production size. When the 3 roll mill is properly leveled as well as bolted, installation of all electrical components then should be done. Moreover, ensure that it is done by a qualified electrician.
- Take-off knife should be well handled:
The take-off knife of the apron has a sharp edge and needs to be handled carefully. When the knife is correctly positioned, it contacts the apron roll slightly above the line of center and remains parallel to it.
- Never run the three roll mill dry:
It is essential to remember that one should not run a 3 roll mill dry. When all the product has run through, immediately open the roll and also disengage apron rolls.
- Do testing to know the correct gap setting:
Test it for determining the best gap setting. It is important to have an ideal setting for a specific product to maximize the throughput while the dispersion quality is not compromised.
- Avoid Loose Clothing Articles:
It is advised not to wear any loose clothing articles or accessories so that they will not get caught between the rolls.
- Lubricate all the bearings:
Roll journals need to get equipped with roller bearing or ball. It is always better to lubricate all those bearings frequently or once a month.
Copyright Notice :
This article only represents the author’s point of view.
This article is published under the authorization of the author.
Source: Franli
This article address:Three roll mill – A detailed Note and usage guidance
Related Products
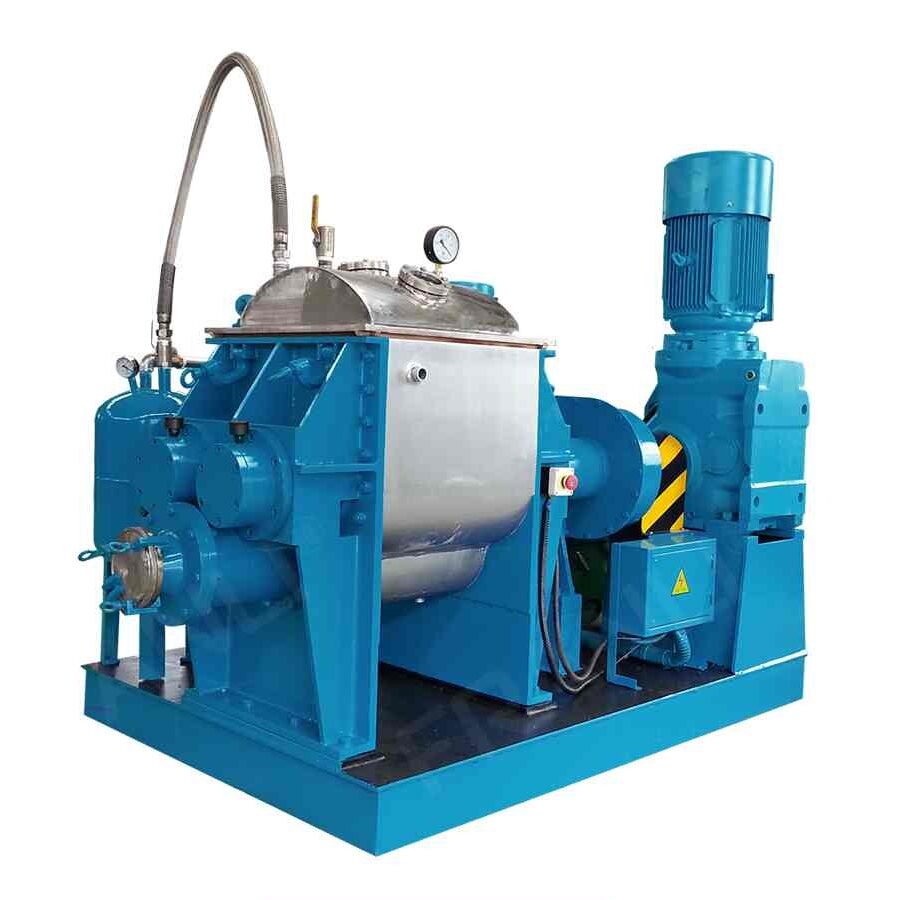
Z Blade Mixer
The Z blade mixer is made for extensive mixing, kneading, and stabilizing strong and high viscous materials, such as bubble gum bases, bread, caramel mass, body wash platform, and glue.
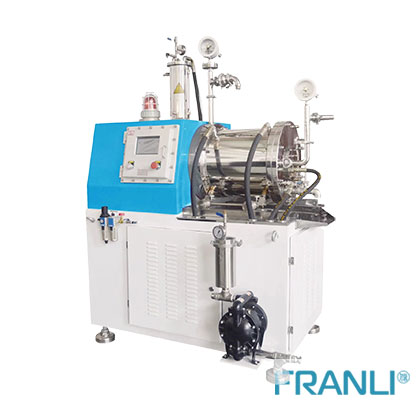
SMP Agitator bead mill
This SMP Agitator bead mill is used in the paint, ink, and coating industries to ready the equal-sized particles of a particular material.
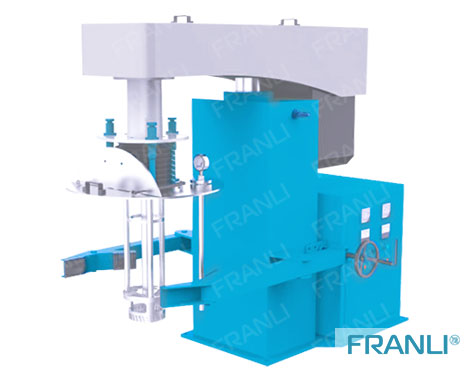
High Shear Mixer
High Shear Mixer is to disperse one or more phases into another continuous phase through efficient, fast, uniform and other processes, and under normal circumstances each phase is insoluble.
News
High Shear Mixers in Biopharmaceutical Applications
high shear mixers are highly versatile and can be used for a wide range of applications in biopharmaceutical manufacturing.
Operating Guide for Laboratory Reactors
Laboratory reactors play a crucial role in chemical research and development. Understanding the proper operating procedures is essential to ensure accurate results and maintain a safe working environment.
Glass Reactors and Selection of Stirring Blades
Glass reactors, also referred to as glass reaction vessels, are vessels made from high-quality borosilicate glass material.
High Shear Mixers in the Resin Industry
High shear mixers are essential equipment in the resin industry for achieving uniform dispersion of solids into liquid matrices, emulsifying oil-based components, and blending various additives to create resin formulations with desired characteristics.
High Speed Dispersers for Painting: Enhancing Efficiency and Quality in the Coating Industry
High-speed dispersers are powerful machines used in the paint and coating industry to disperse solid particles into liquid components effectively.
Ribbon Blender Mixer: The Right Choice for a High-Quality Blender
Ribbon blender mixers, also known as ribbon mixers or ribbon blenders, are horizontal mixing devices characterized by their unique ribbon-shaped agitators.
Related production lines
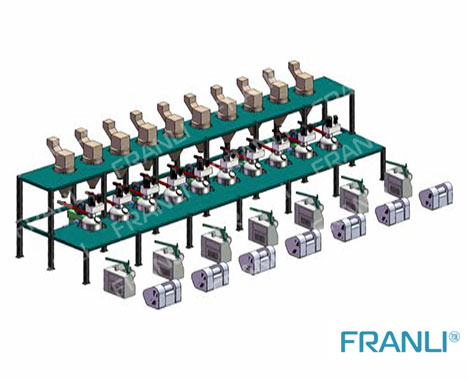
Offset Ink machine line
FRANLI is specialized in offset ink full line production for 20+ years. Helped customer save the cost, save the man power, also save the space.
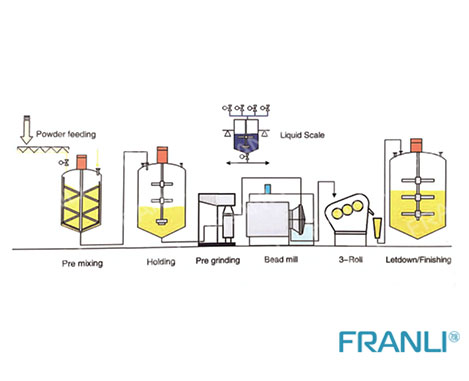
Offset Ink, UV Ink machine line
The FRANLI engineering company, offer the full set of UV INK Production Line, we can make the full drawing according with your factory size, formulas, weather and safety system.
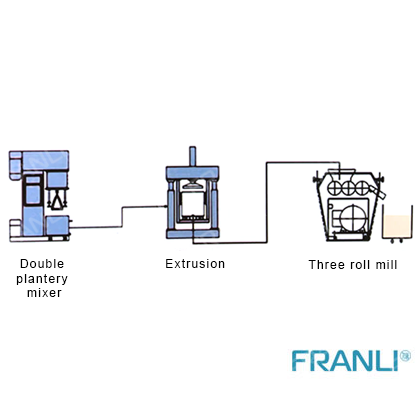
PCB INK Machine line
FRANLI supplies all equipments for the production of PCB inks, from the powder feeding station to the filling part.
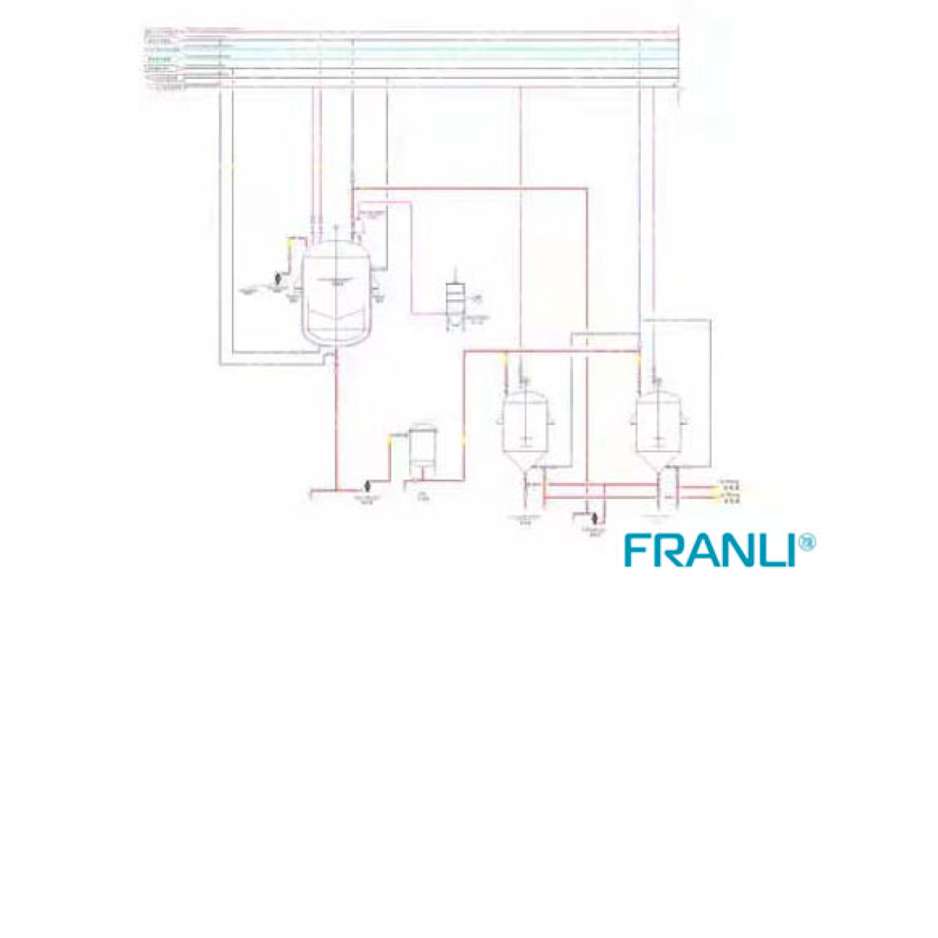
EW-pesticide line
The EW production line mainly mixes raw materials, solvents, and emulsifiers through a reactor (oil-based).
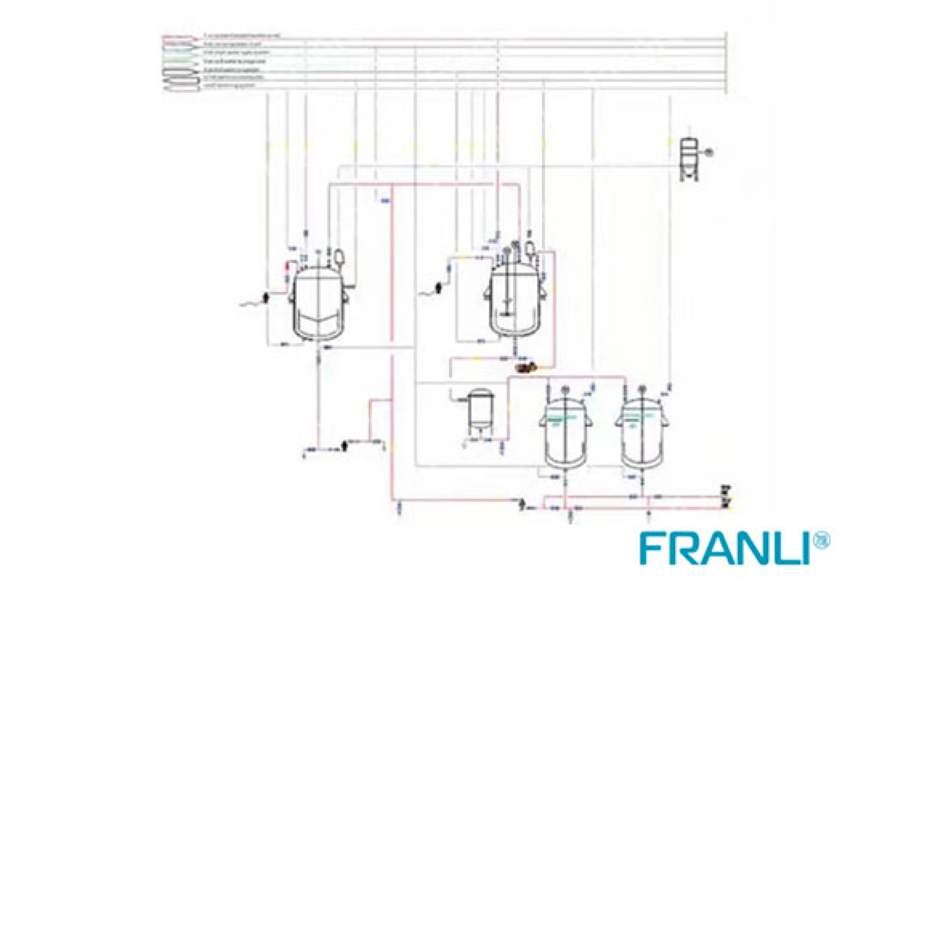
SL_EC pesticide line
The EC production line is mainly composed of an agitator mixer, bag filter, filling machine, etc.
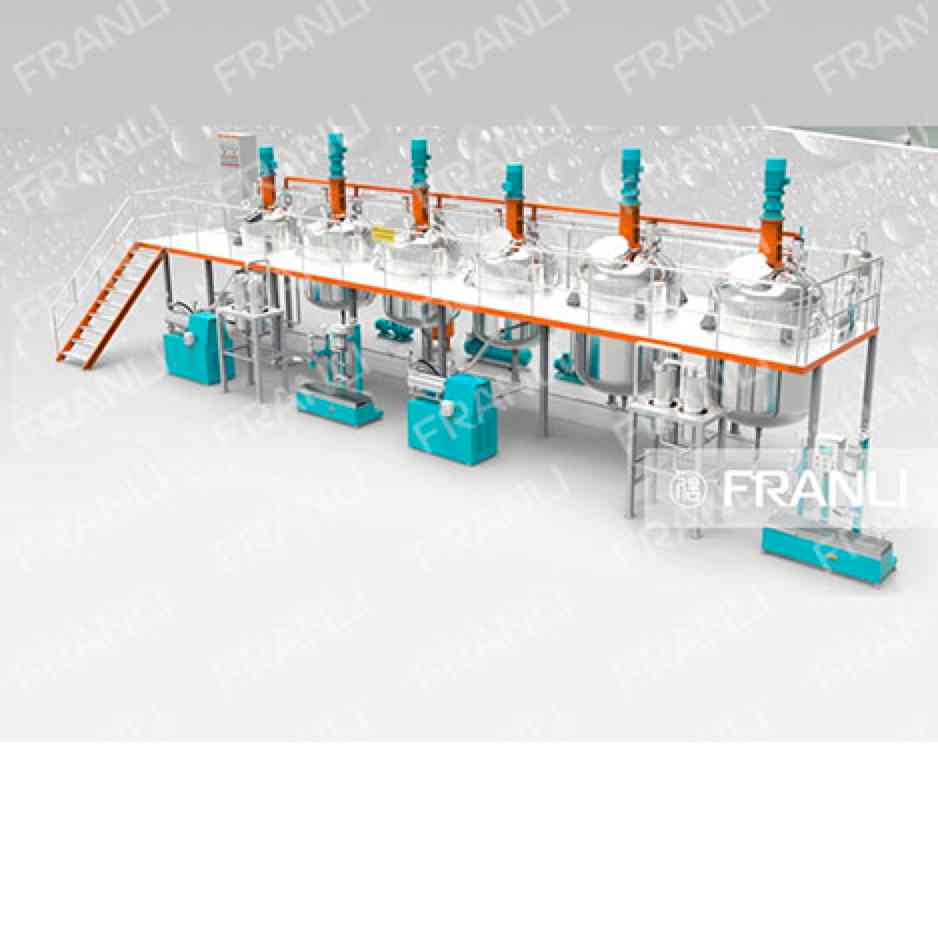
Automotive Paint machine line
The automotive paint machine line is mainly for the production and grinding of automotive paint, Automotive paint has many layers, such as Primer/electrophoretic layer, Medium coat, Colored coat, and Clearcoat.
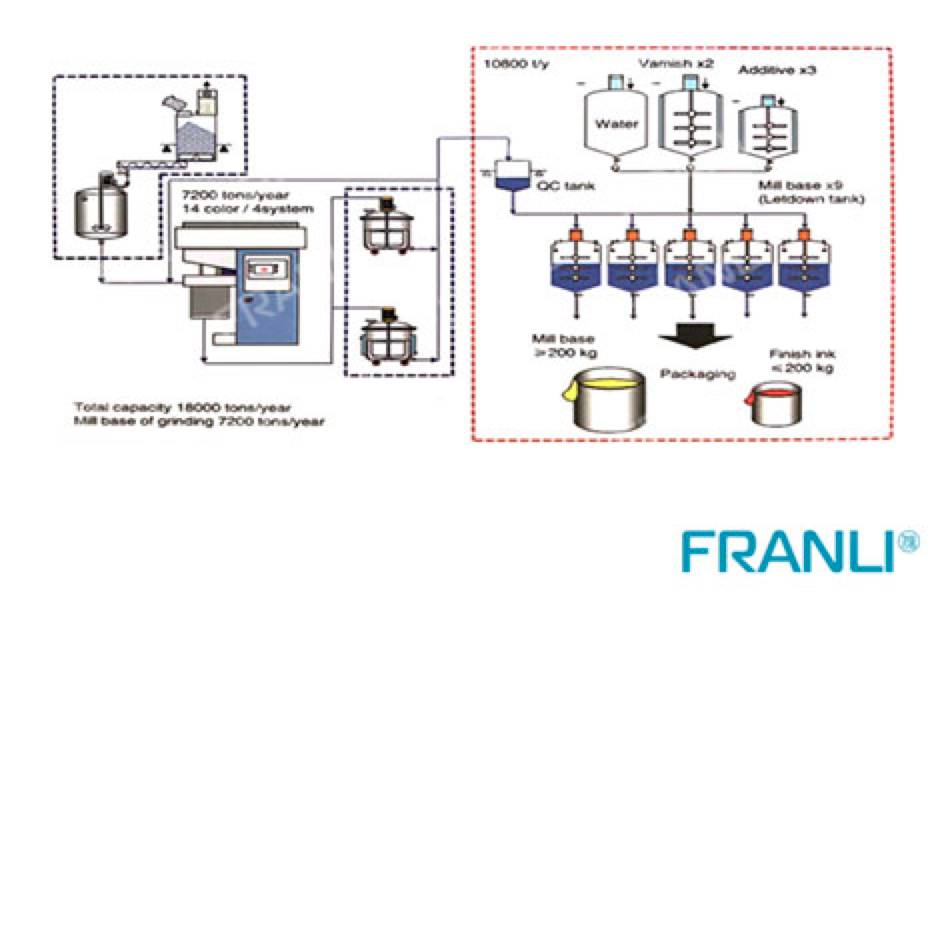
Digital Ink machine line
Franli has professional experience for digital ink machine line, we offered hundreds customers to expand production, or build up new project.