High Shear Mixers in the Resin Industry
High Shear Mixer
High shear mixers are essential equipment in the resin industry for achieving uniform dispersion of solids into liquid matrices, emulsifying oil-based components, and blending various additives to create resin formulations with desired characteristics. These mixers typically consist of a rotor-stator configuration where a high-speed rotor generates shear forces by interacting with a stationary stator. This unique design allows high shear mixers to achieve rapid and efficient mixing of even the most challenging materials.
Details of High Shear Mixer
- Suitable for the material before the process
- Small energy consumption
- Large capacity
- Certain self-suction and low lift transport function
Application: Paint, Adhesive, Battery, Pharmaceutical industry, Cosmetic
In the resin industry, the application of high shear mixers has revolutionized the manufacturing process by enabling efficient dispersion, emulsification, and blending of raw materials to produce high-quality resins with consistent properties. High shear mixers are specialized machines designed to generate intense mechanical forces that break down particles, disperse components, and create homogeneous mixtures within resin formulations.
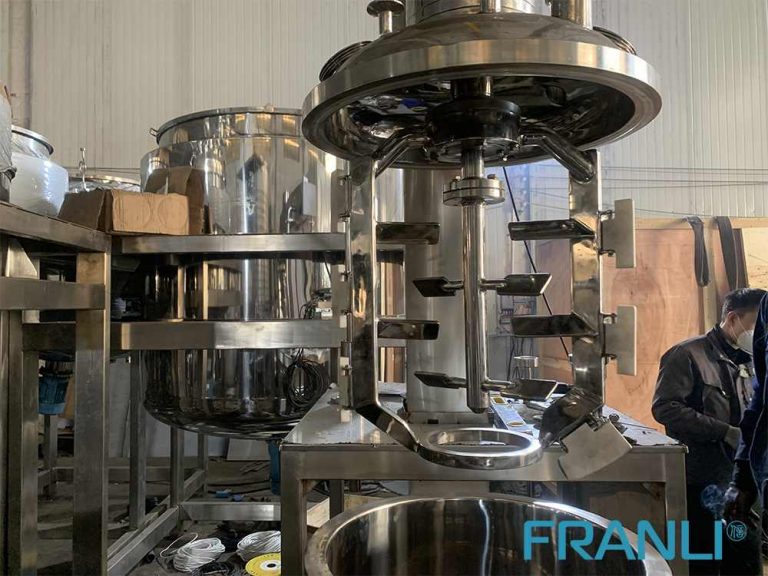
One of the primary advantages of high shear mixers is their ability to disperse and incorporate various additives into the resin. This capability allows manufacturers to enhance the performance characteristics of the final product. Additives such as fillers, pigments, and stabilizers can be efficiently dispersed throughout the resin matrix, ensuring uniformity and consistency.
Another significant benefit of high shear mixers is their ability to break down agglomerates and improve the dispersion of particles. Resin-based materials often contain particles that tend to agglomerate, leading to inconsistent properties and performance issues. High shear mixers effectively break down these agglomerates, resulting in a more uniform dispersion of particles and improved material properties.
The unique design of high shear mixers also facilitates increased reaction rates and reduced processing times. By subjecting the resin mixture to intense shear forces, the mixing process is accelerated. This not only enables faster production cycles but also leads to improved energy efficiency, as less time and energy are required to achieve the desired level of blending.
Moreover, high shear mixers offer superior control over the mixing process. Manufacturers can adjust the operating parameters, such as mixing speed and shear intensity, to achieve specific product requirements. This flexibility allows for precise customization of resin formulations, catering to a wide range of applications and industries.
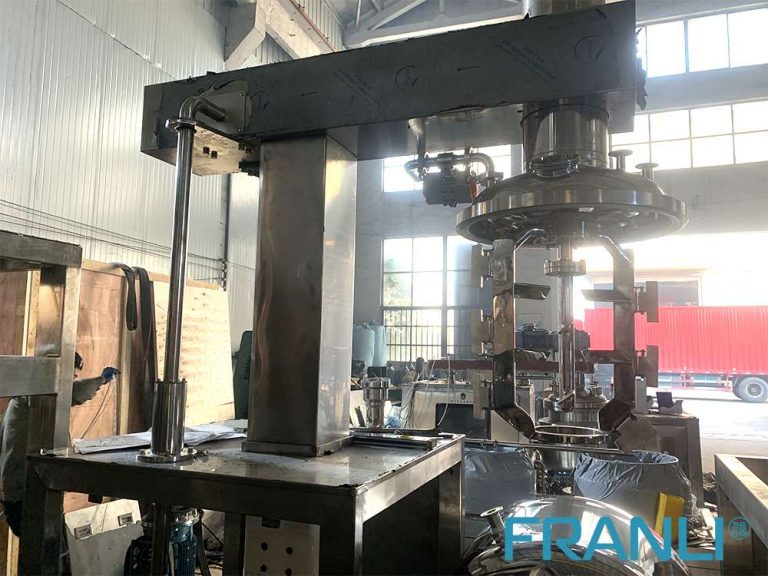
Applications of High Shear Mixers in the Resin Industry
1. Polymer Dispersion:
High shear mixers are used in the resin industry for dispersing polymers into liquid matrices to create stable dispersions that form the basis of various resin formulations used in coatings, adhesives, composites, and other applications.
2. Emulsification of Oil-Based Components:
These mixers facilitate the emulsification of oil-based components such as plasticizers, tackifiers, and modifiers into water-based or solvent-based resins to improve flow properties, adhesion characteristics, and overall performance.
3. Additive Incorporation:
High shear mixers play a crucial role in incorporating additives such as fillers, pigments, stabilizers, and thickeners into resin formulations to enhance properties like color stability, UV resistance, viscosity control, and mechanical strength.
4. Reactive Mixing:
In reactive resin systems such as epoxies or polyurethanes, high shear mixers are utilized to promote chemical reactions between reactive components by ensuring thorough mixing and dispersion for consistent curing and final product properties.
Benefits of Using High Shear Mixers in Resin Production:
1. Improved Mixing Efficiency:
High shear mixers offer rapid mixing times and enhanced dispersion capabilities compared to traditional mixing methods, resulting in improved process efficiency and reduced production times for resin manufacturers.
2. Enhanced Product Quality:
The intense shear forces generated by high shear mixers ensure thorough blending of materials within resin formulations, leading to homogeneous mixtures with consistent properties such as viscosity, color uniformity, and performance attributes.
3. Versatility and Flexibility:
High shear mixers can accommodate a wide range of raw materials with varying viscosities and properties commonly found in resin formulations, providing manufacturers with versatility in formulation development and process optimization.
4. Scalability for Production Demands:
With scalable designs that allow seamless transition from lab-scale testing to full-scale manufacturing operations without compromising on mixing performance or product quality attributes.
5. Cost-Effective Production:
By achieving efficient dispersion and emulsification within resin formulations using high-shear mixers manufacturers can reduce material waste lower energy consumption during mixing processes increase production throughput ultimately leading to cost savings and improved profitability for resin production facilities.
High shear mixers have become indispensable tools in the resin industry for achieving efficient dispersion emulsification blending of raw materials to produce high-quality resins with consistent properties across various applications from coatings and adhesives composites these sophisticated machines play a crucial role in enhancing efficiency productivity quality control within resin production processes by facilitating effective mixing dispersion of components ultimately contributing to the success competitiveness of manufacturers worldwide by understanding the key features benefits applications considerations when choosing a high shear mixer companies can make informed decisions that align with their specific needs requirements ensuring optimal mixing performance superior product quality in today’s dynamic demanding market landscape.
Welcome to send inquiry to us and let’s make a win win business together !
Guidelines For High Shear Mixer
The mixing device of the high shear mixer is a rotor with four blades, which rotates at a high speed in a stationary stator to complete the entire stirring and mixing process.
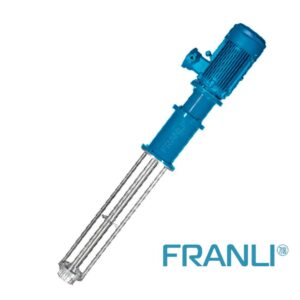
High Shear Mixers: A Guide to Applications in the Cosmetics Industry
A high shear mixer is one of the most versatile pieces of equipment used in the cosmetic industry. It is designed to mix, emulsify, disperse, and homogenize a wide range of cosmetic products.
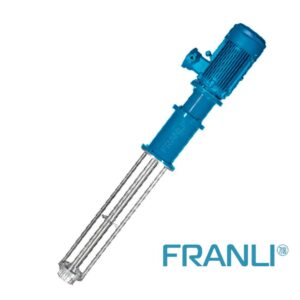
What is a High Shear Emulsifier?
High shear emulsifiers are innovative and efficient machines that are used in various industries for the purpose of emulsification, homogenization, and particle size reduction.
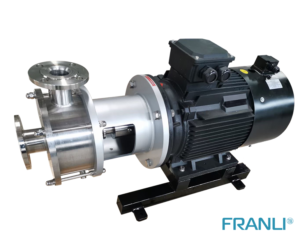
What is an Inline Homogenizer?
An inline homogenizer is a machine that is used to mix and blend different substances together to create a uniform mixture. It is an essential tool in the manufacturing industry, particularly in the production of food, pharmaceuticals, and cosmetics.
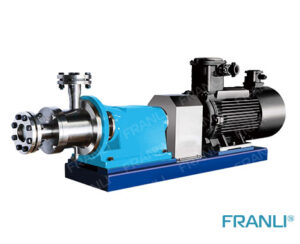
What is an Inline Emulsifier?
An inline emulsifier is a type of high shear mixer that is designed to create a stable emulsion by breaking down the droplets of one liquid into smaller droplets and dispersing them throughout the other liquid.
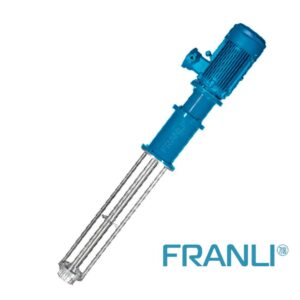
High Shear Mixer: An Essential Tool for Efficient Mixing
A high shear mixer is a device that is used to mix, emulsify, disperse, and homogenize materials. It is a versatile tool that can be used in a variety of industries such as food, pharmaceuticals, cosmetics, and chemical manufacturing.
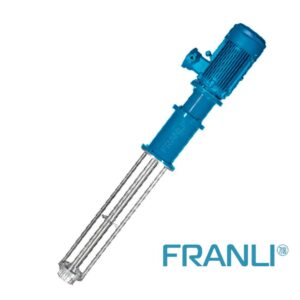
High Shear Mixers: Experimental & Production
High-shear mixers are primarily used in industry to produce standard mixtures of ingredients that do not mix naturally. When the total fluid of the material is composed of two or more liquids, after the work of the high-shear mixer, an emulsion is finally formed.