Home » Different grinding process of nano mill
Different grinding process of nano mill
There is always a greater impact on all the things ranging from the cost of the ingredient to the quality of the final products made out of the nano mill, and even there are folks that hardly know about them all.
nano mill
So, how well can you be determining the proper method for grinding for the processes as well as the products? Though it is not a proper place to start, it is not a matter of matching the materials within the mills here.
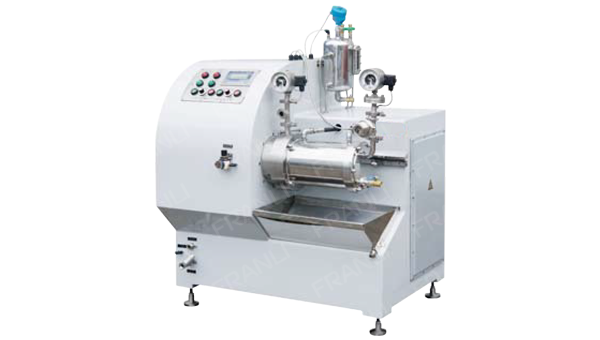
Vertical nano mill
The main crushing & coarse methods of crushing
There are two jaws of the mills here where one is fixed, and the other is movable. The jaw that is movable compresses the material against the one that is fixed with the use of the tear, shear, and the impact of the force that causes the material to fracture the materials. There is a range of materials that are used for industrial purposes
It leads out to the size of the particles that range a lot depending on the brittleness and the hardness of the material here in terms of its heavy-duty nature, along with the simple actions of the jaw crushing. For the sticky, rubbery, and wet materials, these jaw crushers are not well-suited. An additional amount of grinding is called to use with the other milling methods if there is a need for finer gauges.
Impact of crushing
These crushers are, at times are used as the second crushing steps that are included after the crushing of the jaws.
The use of roller mills
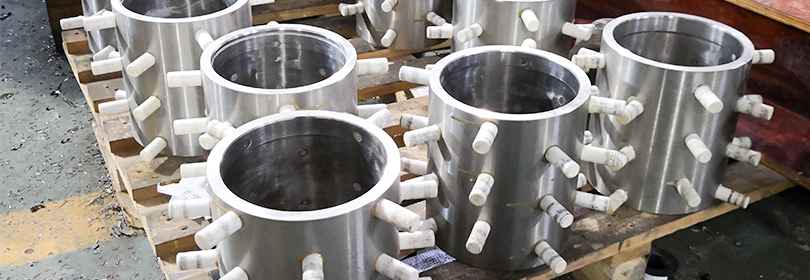
nano mill core parts
The use of hammer mills
The hammer mills can thereby reduce the size of the particle on a broader range of materials that includes the tougher and greater materials for fibrousnesses as they are not well-suited for the sticky, quite robust, or abrasive materials, unlike the roller mills here. It is quite important to be aware of the lowered melting points and the application of technologies, including the cryo-milling as well as the inert gases as indicated.
The use of universal mills
In order to achieve the desired size of the particles along to the cryo-milling can make this type of milling an option for even a greater range of the raw materials in terms of the universal mills grinding elements and the rotor speeds that are selected.
The use of jet milling processes
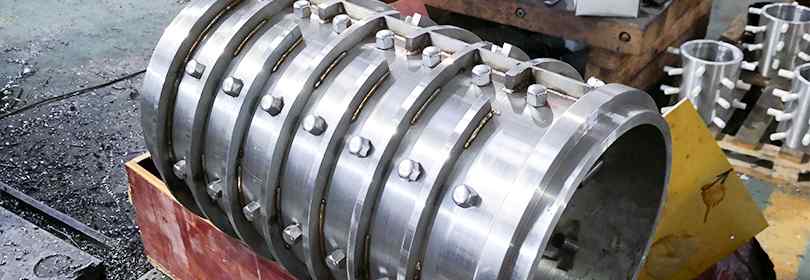
nano mill roll
• Reduction to the material required here within the agriculture chemicals as well as the pharmaceuticals with the lower dosages.
• Precise color outcomes or sheen in pigments
• Exacting control over abrasives in polishes
Copyright Notice :
This article only represents the author’s point of view.
This article is published under the authorization of the author.
Source: Franli
This article address : What is a bead mill?
Related Products
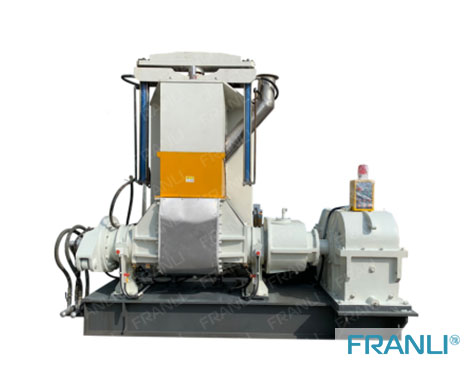
Dispersion Kneader
The dispersion kneader is suitable for the mastication of rubber and plastics, and the mixing of various rubber materials and plastics.
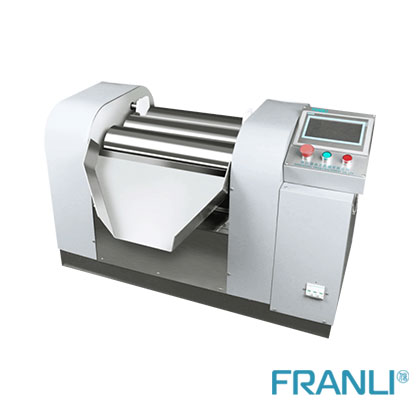
Digital Control Three Roll Mill
The roller of the digital control three roll mill is made of zirconia ceramic material and equipped with a frequency conversion speed regulating device to meet the grinding needs of different materials.
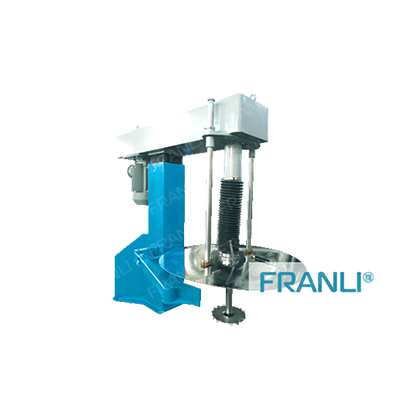
Hydraulic Lifting High Speed Disperser
The hydraulic lift high speed disperser has the characteristics of simple operation and high flexibility. The hydraulic lifting high speed disperser is suitable for the production of paints, inks, coatings, dyes, papermaking, etc.
News
Laboratory Reactor: Guide to Stirring System
The laboratory reactor is composed of a pot body, a pot cover, an agitator, a jacket, a support and transmission device, a shaft seal device, etc.
Grinding Media for Bead Mill | Zirconia Beads & Zirconium Silicate Beads
Bead mills mainly use grinding balls as media, and use impact, extrusion, and friction to achieve the final grinding effect, which mainly depends on the size and hardness of the grinding beads, the filling rate of the grinding beads, and the collision frequency adjustment between the grinding beads and the particles.
Overview of Laboratory Reactor
Laboratory reactors, also known as lab reactors, are essential tools in scientific research, product development, and process optimization. These reactors provide a controlled environment for conducting chemical reactions, mixing, dispersing, and homogenizing processes.
Bead mills | Manufacturing technology in various industries
Bead mills, also known as sand mills or grinding mills, are versatile machines widely used across various industries for the wet grinding and dispersion of solid particles in liquid media.
Ribbon Blender Mixer Equipment
A ribbon blender mixer, also known as a ribbon mixer or horizontal ribbon blender, is a powerful industrial machine designed for thorough and efficient blending of various materials.
What is A Stainless Steel Reactor?
Stainless steel reactors are essential equipment in various industries, including chemical, pharmaceutical, biotechnology, and food processing.