Home » What is a bead mill?
What is a bead mill?
A Bead Mill also known as a sand mill, is mainly used for the wet grinding of chemical liquid products. Compared with grinding equipment such as ball mill, roller mill, and colloid mill, bead mill has the advantages of high production efficiency, strong continuity, low cost, and high product fineness. The process conditions vary greatly, and the fineness requirements can be adjusted and classified by adding or subtracting grinding media in an appropriate amount.
1. The medium distribution in the grinding chamber of the horizontal large-flow bead mill is relatively uniform, the grinding technology has high efficiency, it is very easy to start with load, and the operation is simple and convenient. It can be designed to be large or super large. However, the energy density (installed power per unit volume) is low and the grinding fineness is limited.
2. The medium distribution of the vertical bead mill is uneven, the efficiency of grinding technology is low, and it is difficult to start the capital with the load. The advantage is that there is no mechanical seal and the structure is simple.
3. The energy density of the conical bead mill, short cylinder grinding, a large area of filter media separation, the short residence time of materials, high cooling effect, high grinding efficiency, and narrow product size distribution. Generally, it can be used for the circulating grinding process with the large flow of difficult-to-grind materials.
4. High viscosity rod pin bead mill has high energy density and high strength of grinding material. Mainly used for the production of high viscosity materials, such as offset printing ink and UV ink.
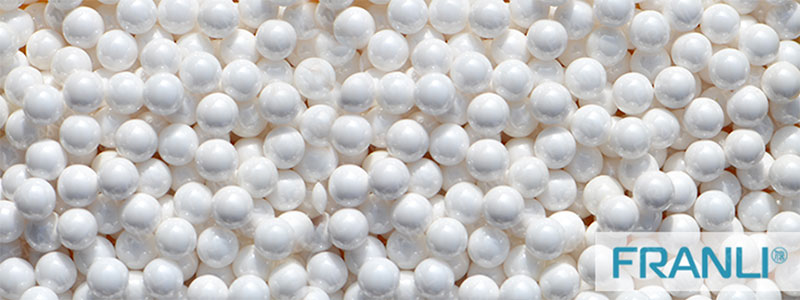
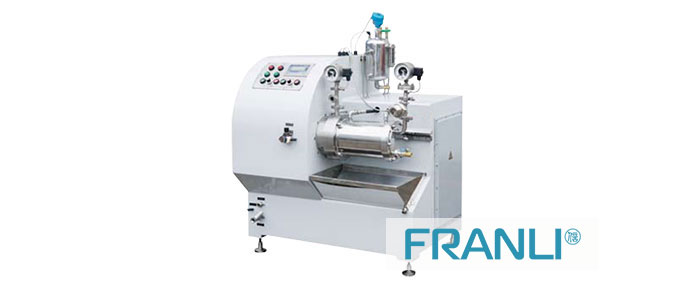
Bead mill grinding and dispersing principle
Copyright Notice :
This article only represents the author’s point of view.
This article is published under the authorization of the author.
Source: Franli
This article address : What is a bead mill?
Related Products
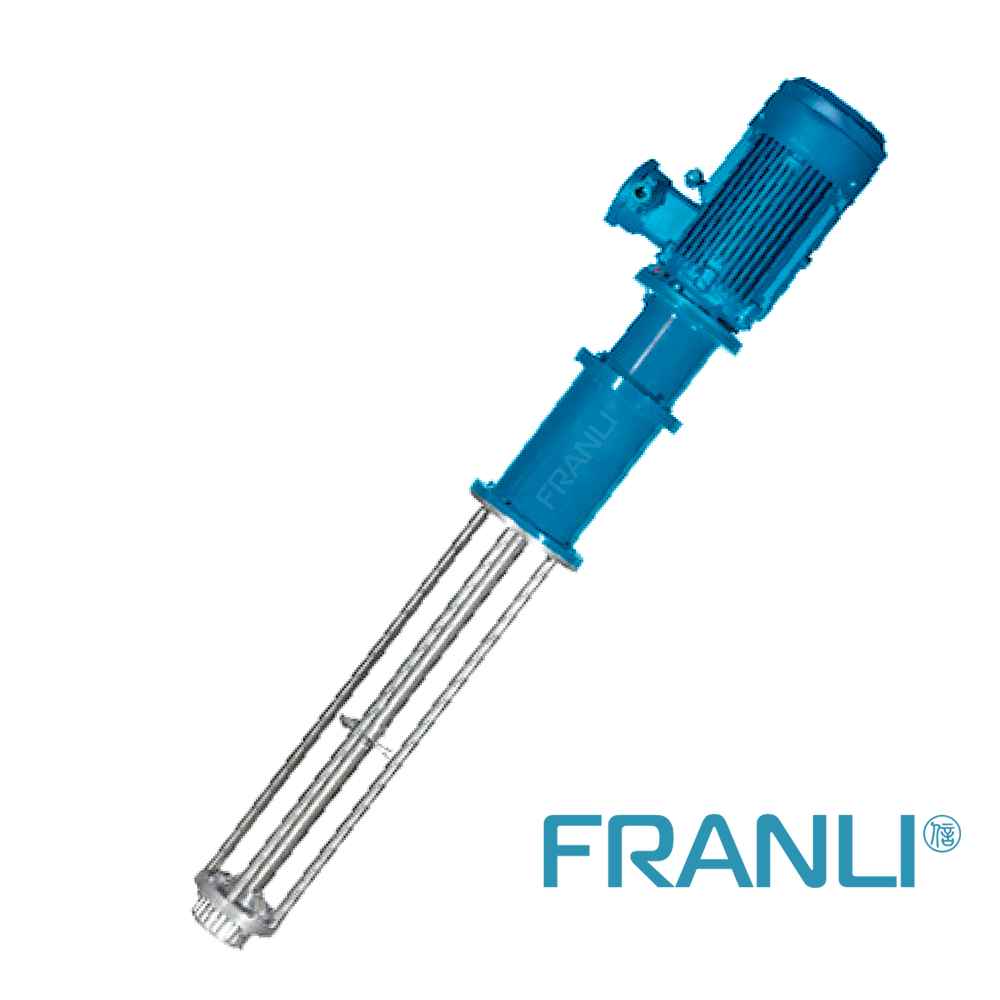
High Shear Emulsifier
The high shear Emulsifier is widely used in the experimental fields of liquid mixing, emulsification, liquid/solid powder dispersion, and slurrying in biology, physics, chemistry, cosmetics, health care products, food, paint, coatings, and chemicals.
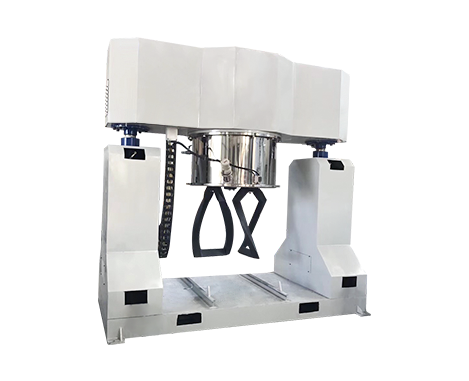
Double planet mixer
Double planet mixer is a new type of mixing equipment with high performance, high speed, easy cleaning, and maintenance. The two agitators of the equipment revolve around the axis while rotating.
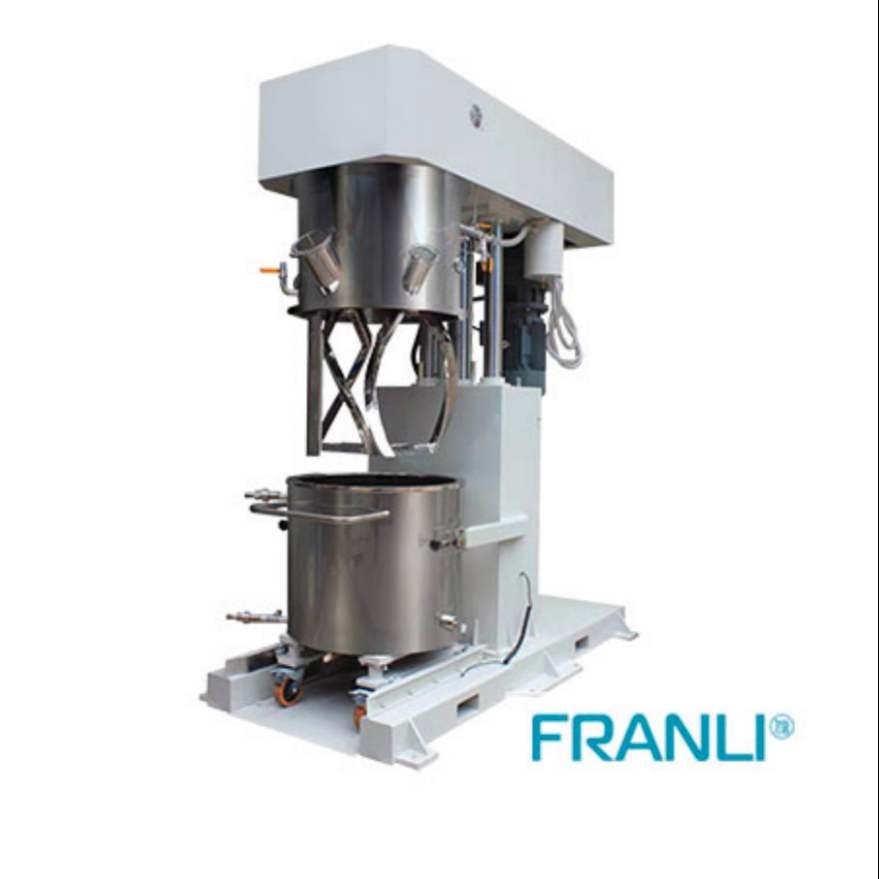
Vacuum Double Planetary Mixer
A Vacuum double planetary mixer is an essential part of any industry to mixing particular material. A double planetary mixer contains two blades that help mix by revolving on their axis in the vessel.
News
Laboratory Reactor: Guide to Stirring System
The laboratory reactor is composed of a pot body, a pot cover, an agitator, a jacket, a support and transmission device, a shaft seal device, etc.
Grinding Media for Bead Mill | Zirconia Beads & Zirconium Silicate Beads
Bead mills mainly use grinding balls as media, and use impact, extrusion, and friction to achieve the final grinding effect, which mainly depends on the size and hardness of the grinding beads, the filling rate of the grinding beads, and the collision frequency adjustment between the grinding beads and the particles.
Overview of Laboratory Reactor
Laboratory reactors, also known as lab reactors, are essential tools in scientific research, product development, and process optimization. These reactors provide a controlled environment for conducting chemical reactions, mixing, dispersing, and homogenizing processes.
Bead mills | Manufacturing technology in various industries
Bead mills, also known as sand mills or grinding mills, are versatile machines widely used across various industries for the wet grinding and dispersion of solid particles in liquid media.
Ribbon Blender Mixer Equipment
A ribbon blender mixer, also known as a ribbon mixer or horizontal ribbon blender, is a powerful industrial machine designed for thorough and efficient blending of various materials.
What is A Stainless Steel Reactor?
Stainless steel reactors are essential equipment in various industries, including chemical, pharmaceutical, biotechnology, and food processing.