High Shear Emulsifier
High Shear Mixer is to disperse one or more phases into another continuous phase through efficient, fast, uniform and other processes, and under normal circumstances each phase is insoluble. Because of the high rotor high-speed rotation of the tangent velocity and kinetic energy of high frequency mechanical effect brings strong, make the material in the narrow gap, rotor fierce mechanical and hydraulic shear, centrifugal extrusion, tearing and turbulent liquid layer friction, lighting strike etc inductive effect, so that the miscibility of the solid phase, liquid phase and gas phase in the corresponding mature technology and with a moderate amount of additive effect, Disperse and emulsify evenly and finely in an instant, and get stable and high-quality products after high frequency cycles.
Advantages of High Shear Emulsifier:
- low grinding fineness
- Wide range of applications
- high working efficiency
Application

Coating

Cosmetic

Battery

Graphite

Agrochemistry

Adhesives
Hot sale High Shear Mixer
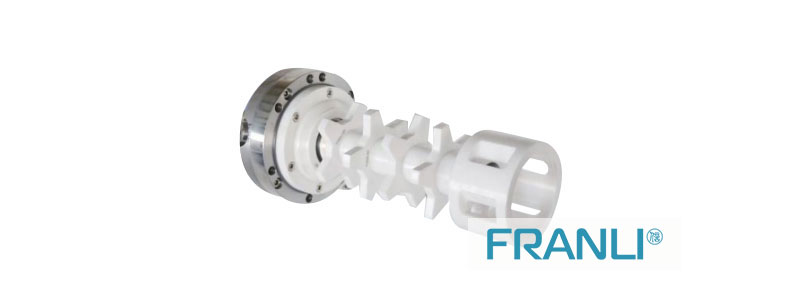
• Easy installation of the bead mill machine: The best features of this bead mill machine are: You can easily install it wherever you want. This task is so simple, and effortless. And due to this feature, it is extremely popular among other equipment. You can find the bead mill working principle so effective, and you can perform all the mixing tasks effectively without adding so much effort. As this machine is very bulky and cheap, it needs only a few minutes to install. In this way, you can reduce the labor charges and other exhausting jobs. So, you can stay worry-free about how to install this machine? As the company has made this task easier for you.
• Efficient work performance of this bead mill machine: As we know, the bead mill working principle has been created in such a way that you can achieve higher and efficient work performance on this bead mill machine. If you are looking for quality and stable work, these bead mill machines are the best option to get a consistent mixture of any particular material. You can use this bead mill for paint, ink, and coating industries. And, it is a comfortable and easy method to perform all the mixing and dispersing activities without wasting so much time. So, here bead mill working process is so necessary to obtain the desired results for the company.
• Contains grinding media of 2-3 mm size: It is the necessary feature of the bead mill working process as it includes the grinding media. In this area, grinding and other dispersing activities take place that they turn into a fine mixture. You can use a bead mill for paint, ink, and coating industries, where mixing works have been done regularly. It contains grinding media of 2-3 mm size that is enough to transform all the material to a smooth and fine paste. For this purpose, bead mill manufacturers have added advanced technology to this machine to provide consistent and quality work performances for the company. In this way, you can get a higher productivity ratio. And you can reach the peak of the higher conversion rate. Thus, these bead mill machines are ideal for fabrication companies to get their desired goals with full efficacy.
• Easy operation of the bead mill machine: It is a great feature of this SMP Agitator bead mill machine as bead mill manufacturers create this bead mill machine with advanced technology. And, with this quality, the operation of this sand grinding mill is extremely comfortable. You do not need to call any professional to do the same, and you can do it yourself without adding so much effort. So, it is another best feature to consider about this bead mill machine.
• Easy to clean the bead mill machine: This sand grinding mill is remarkably best for the fabrication companies to enhance the overall growth and production. As we know, while we use any bead mill machine, we need to clean it so that we can get hygienic work performance. For this purpose, companies manufacture this bead mill machine in a way that you can clean it comfortably without making yourself exhausted. You can go through the bead mill pdf and other relative documents that provide you the guidelines of clean this bead mill machine.
• Easy to maintain the bead mill machine: Maintaining is also a matter of concern as it requires your time and money. For this purpose, you can check the bead mill pdf and manual provided by the company at the time of purchase. You can either contact the company or read the manual carefully to know all the information about the bead mill machine. And, you can find this process is extremely simple to perform. So, you can get this bead mill machine without spending so many amounts on it. And, in this way you can concentrate on the work performance of the company.
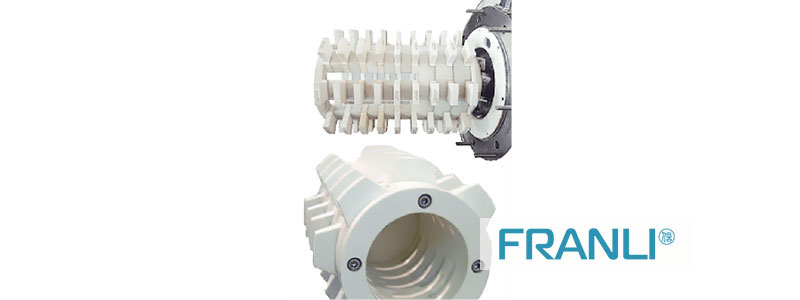
Also, you can use SMP Agitator bead mill in paint industry, ink, and other coating work companies to make all the mixing and grinding activities easier and more manageable. To get this bead mill machine, you search for those companies that deal in these machines and other equipment. For this purpose, you can get a quote or related other information about the bead mill machine.
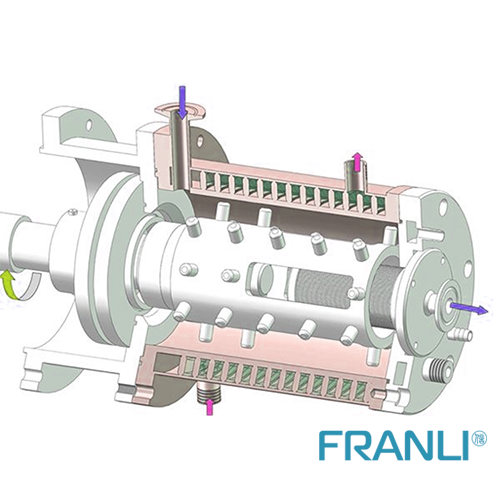
Hydraulic TRH type
Hydraulic Three Roll Mill, which is a full hydraulic auto-controlling system equipment. 1- Cooling system: an individual cooling system for each roller. 2- hydraulic control: hydraulic control pressure blades, roller gaps, etc. 3- Optional installation:PLC system with SIEMENS touching screen, FRANLI engineer set formulas of grinding according to different viscosity materials.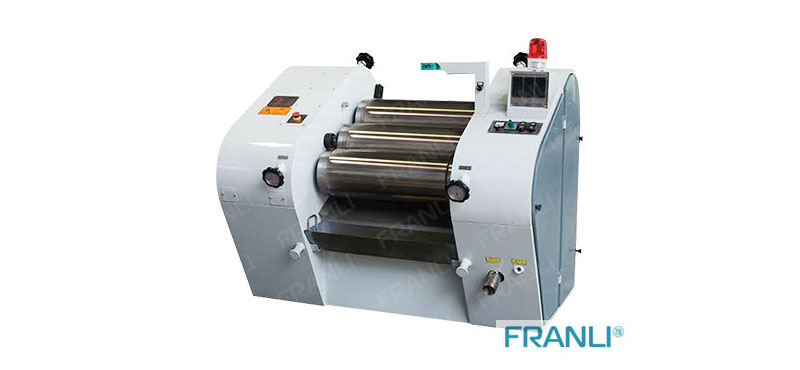
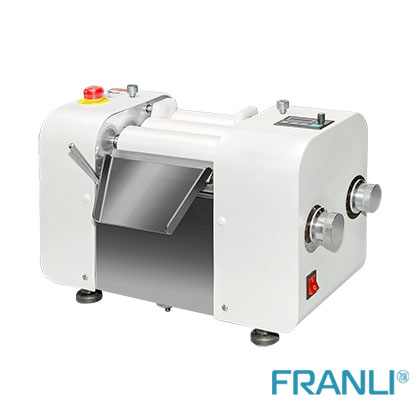
Vertical type for Grinding Powder
Also, we have a vertical three-roll mill for grinding powder and chocolate. We have 3 rollers, 4 rollers, and even 5 rollers, which are all vertical types. We export to the soap industry and chocolate companies.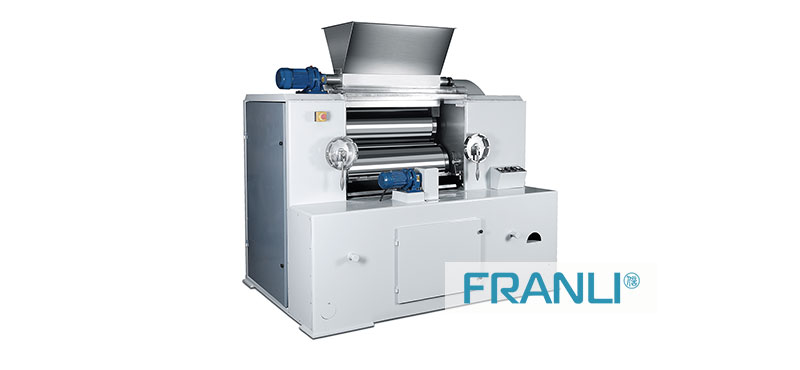
Heating type
Franli also offers a heating hydraulic three roll mill for rubber, EVA, PVS, and color masterbatch. As this type of machine grinds high viscosity material, we specially design the gear quality. This type is been Heated by oil or steam. Franli three roll mill machine are full automatic PLC controlling, hydraulic system, stable operation, reliable quality. We choose the international brand parts. Standrad parts, ABB VFD, Siemens Motor, SKF or NSK bearings, SEW or Nord reducer. A roller is 45-55mm thickness of metal, cast steel. You can widely choose ceramic, alloy, granite rollers for your material. If you have several formulas of material, we can set up formulas in the PLC system, your workers only need to choose numbers on touching the screen, don’t need to waste time to adjust the rollers’ gap or the pressure of the blade.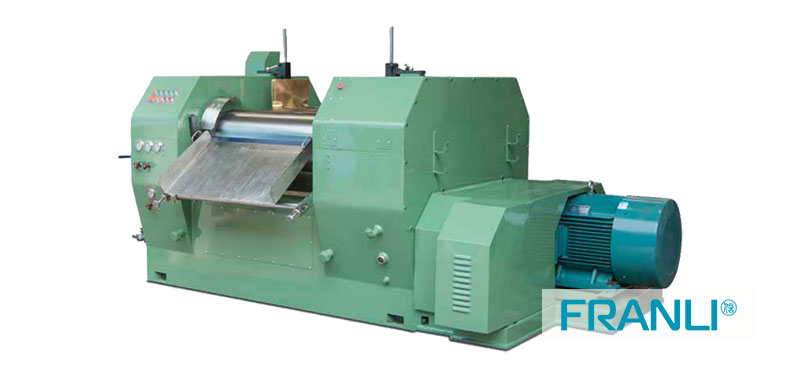
Related production lines
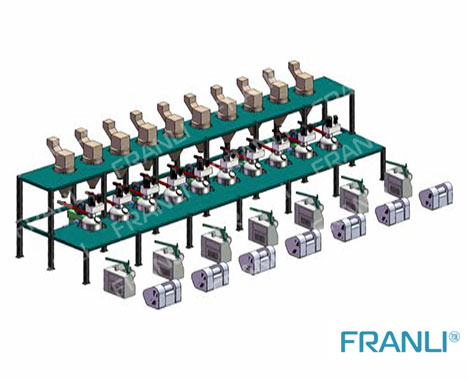
Offset Ink machine line
FRANLI is specialized in offset ink full line production for 20+ years. Helped customer save the cost, save the man power, also save the space.
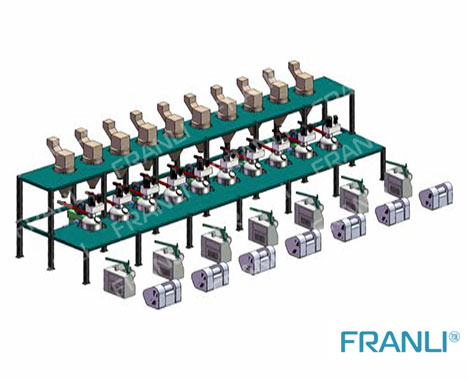
Offset Ink machine line
FRANLI is specialized in offset ink full line production for 20+ years. Helped customer save the cost, save the man power, also save the space.
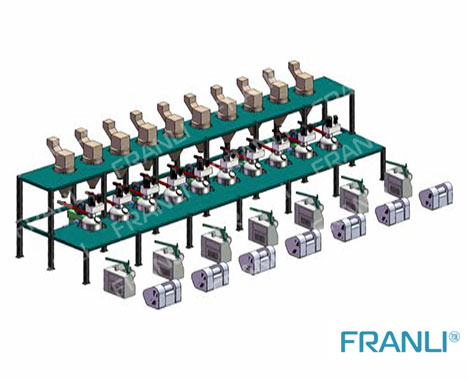
Offset Ink machine line
FRANLI is specialized in offset ink full line production for 20+ years. Helped customer save the cost, save the man power, also save the space.
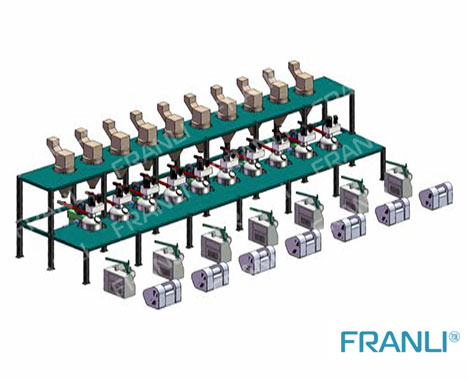
Offset Ink machine line
FRANLI is specialized in offset ink full line production for 20+ years. Helped customer save the cost, save the man power, also save the space.
Guidelines For High Shear Mixer
The high shear mixer is a kind of emulsification homogenizer, which can be said to be an upgraded version of the emulsifier. In the material processing industry, a series of operations such as mixing, emulsification, dispersion, dissolution, and reaction are generally inseparable from mixing equipment such as high shear mixers. For operators of high shear mixers, it is very important to be familiar with relevant parameters such as equipment performance, characteristics, installation, and application.
The dispersion process of the high shear Emulsifier is based on the cutting principle of the rotor and the stator. The experimental equipment is driven by a high-speed motor to drive the shearing and emulsifying working head, which promotes the rotor to make a high-speed circular motion. The high-speed rotating rotor and the precision stator form high-frequency, strong circumferential tangential velocity, angular velocity, and other comprehensive kinetic energy, which encourages the experimental materials to be sucked into the rotor area from the bottom of the experimental container, and the stator hole under the action of huge centrifugal force throw out.
The stator and rotor form strong, reciprocating hydraulic shear, friction, centrifugal extrusion, and fluid collision in a reasonably narrow gap. The experimental materials cyclically reciprocate in the container, and withstand tens of thousands of times per minute of shearing, tearing, impact and mixing, to achieve the effect of shearing and emulsification, and the efficiency of high shear Emulsifier is about a thousand times higher than that of ordinary mixing.
Related production lines
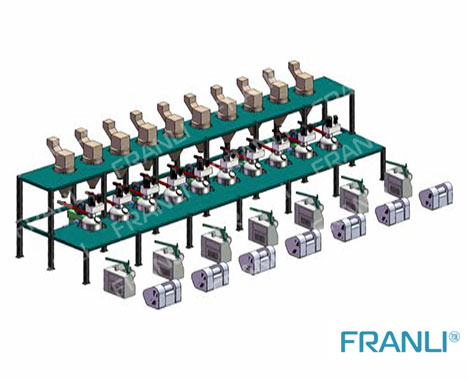
Offset Ink machine line
FRANLI is specialized in offset ink full line production for 20+ years. Helped customer save the cost, save the man power, also save the space.
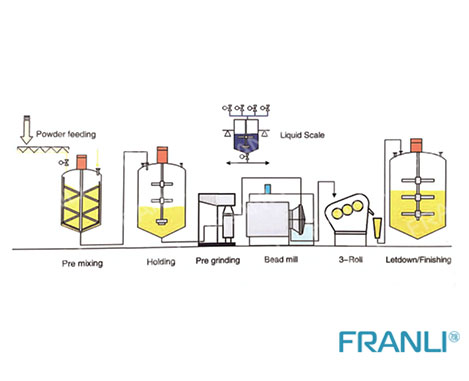
Offset Ink, UV Ink machine line
The FRANLI engineering company, offer the full set of UV INK Production Line, we can make the full drawing according with your factory size, formulas, weather and safety system.
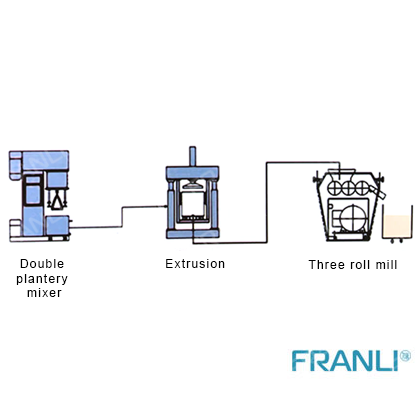
PCB INK Machine line
FRANLI supplies all equipments for the production of PCB inks, from the powder feeding station to the filling part.
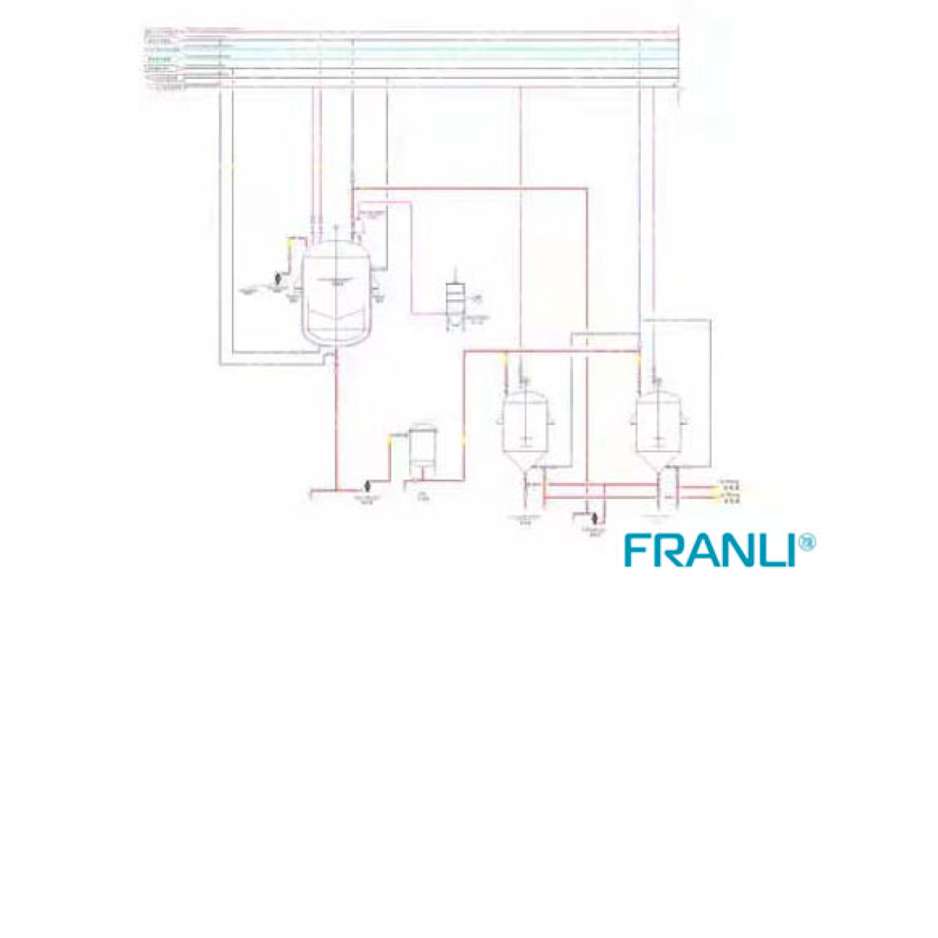
EW-pesticide line
The EW production line mainly mixes raw materials, solvents, and emulsifiers through a reactor (oil-based).
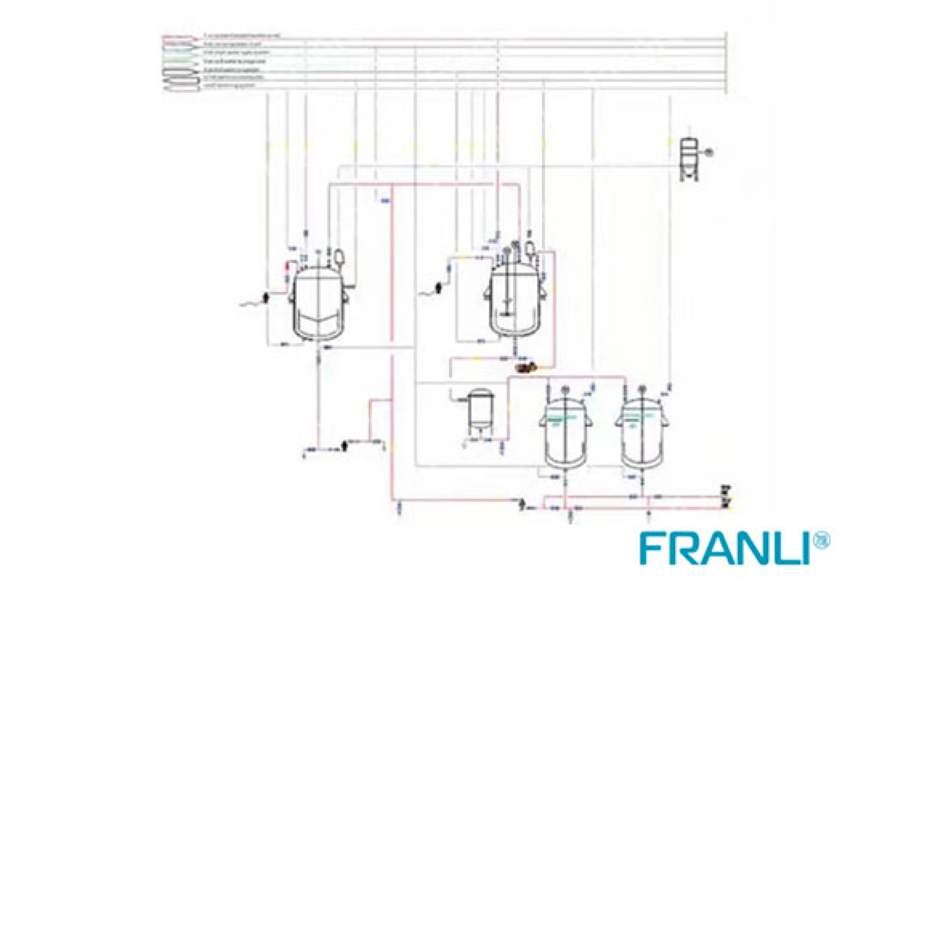
SL_EC pesticide line
The EC production line is mainly composed of an agitator mixer, bag filter, filling machine, etc.
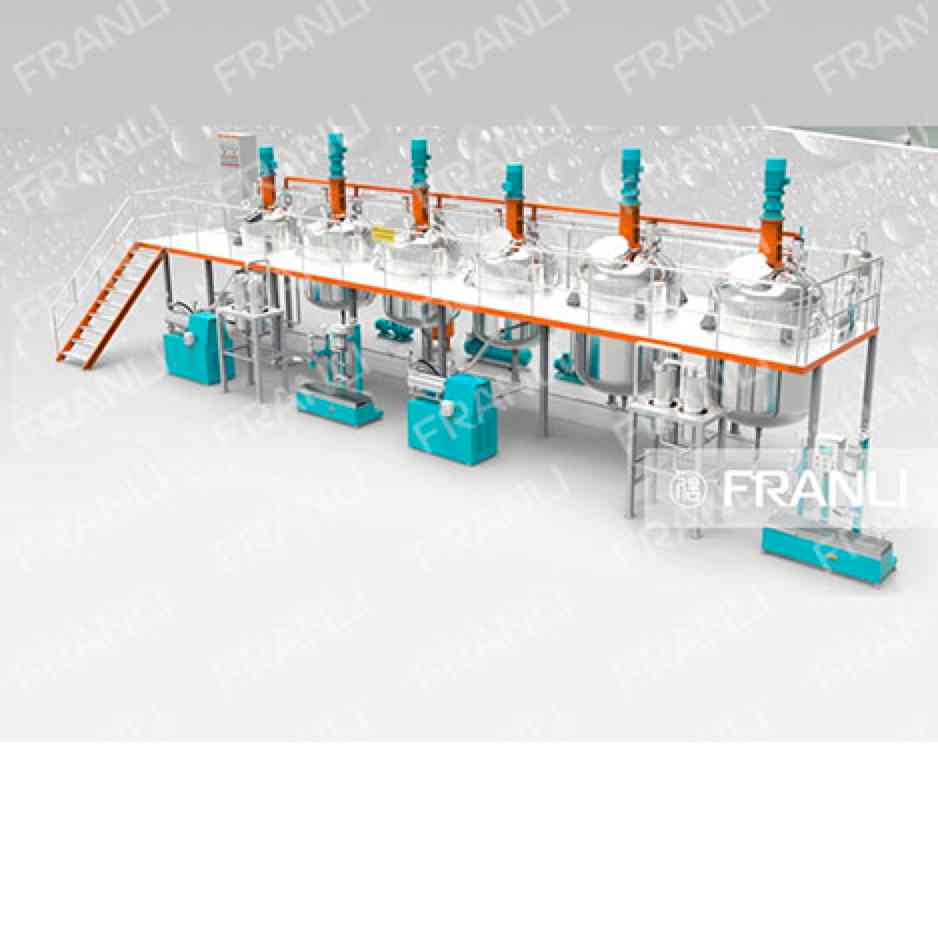
Automotive Paint machine line
The automotive paint machine line is mainly for the production and grinding of automotive paint, Automotive paint has many layers, such as Primer/electrophoretic layer, Medium coat, Colored coat, and Clearcoat.
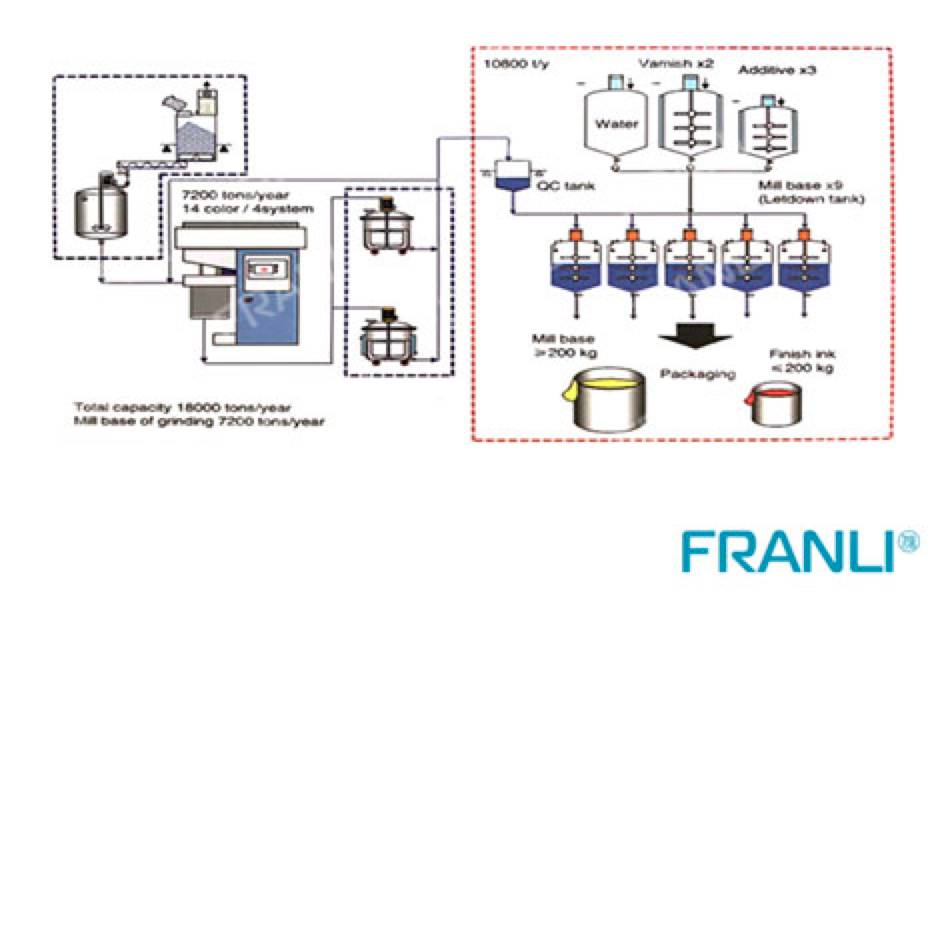
Digital Ink machine line
Franli has professional experience for digital ink machine line, we offered hundreds customers to expand production, or build up new project.