Home » Bead Mill: The effective tool for grinding & dispersing
Bead Mill: The effective tool for grinding & dispersing
The grinding media or the beads are agitated within the cylindrical vessel for grinding or dispersing minute particles in the slurry is done with the help of an apparatus or bead mill. Shear force, along with the impact on the particles, is induced with the help of the rotor of the mill that is generating the bead motion here. Over a massive range of applications, including the grinding of the larger particles along with dispersing the nanoparticles are done with the help of the bead mill.
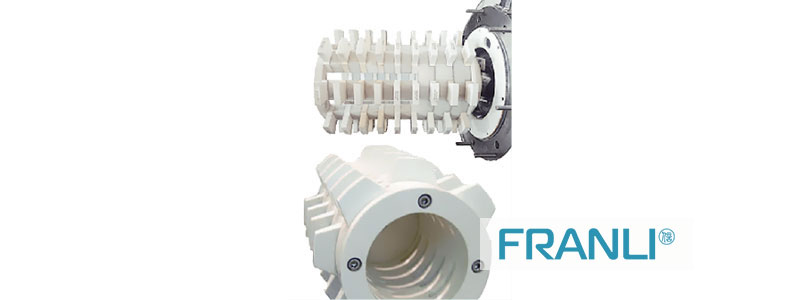
main parts of bead mill
The importance of the size of the beads selected
The smaller beads generally have processing rates that are quite fast here in terms of dispersing, where the larger impacts are not required here. The size of the bead, including the speed of the rotor and the mass of the beads here, are charged in the bead mill machine through the adequate energy impacted in the mill here. It is generally controlled with the help of the speed of the rotor along with the size of the bead affecting the rate of processing is considered as the frequency of the impact made between the particle as well as the bead.
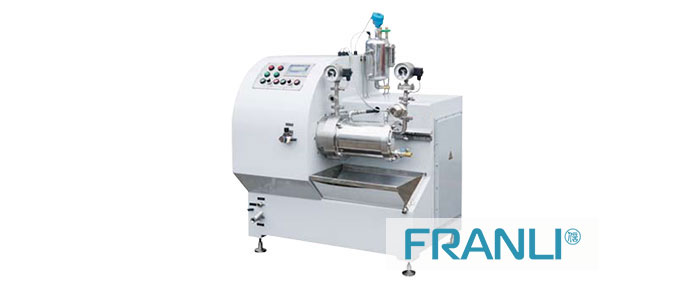
Lab Bead Mill
Bead selection in the process of dispersing
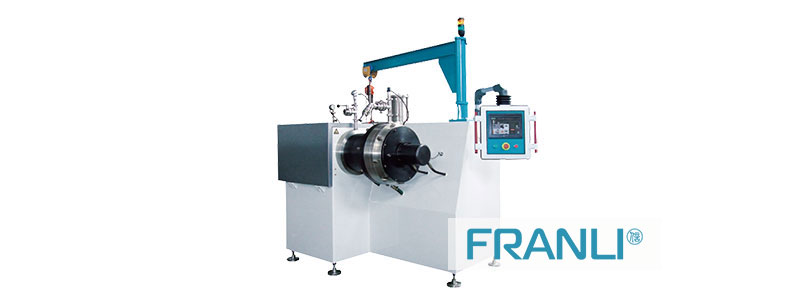
dyno mill
Selecting the kind of bead mill
One of the highly vital factors involved in terms of selecting the kind of bead mill is the kind of separation processes of the beads here. They are basically grouped into the screen, slit as well as centrifugation methods since each of them have their own preferred size of the bead here in terms of the bead separation of the bead mill working principle.
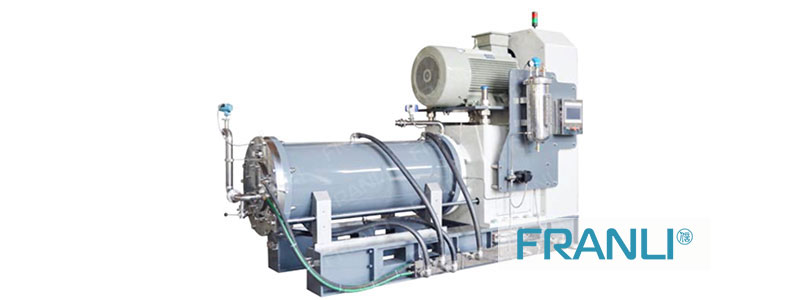
horizontal sand mill
Slit separator
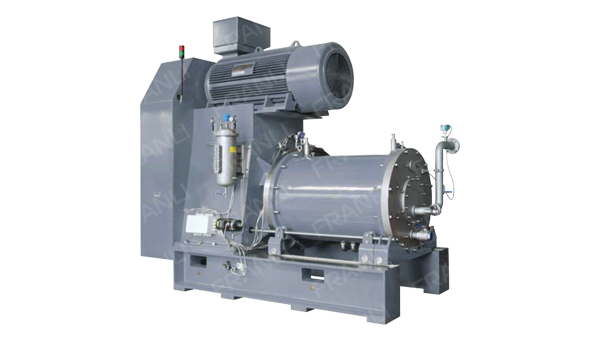
nano mill
Screen separator
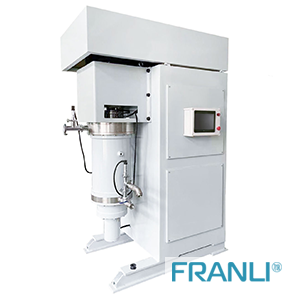
pearl mill
Centrifugal separator
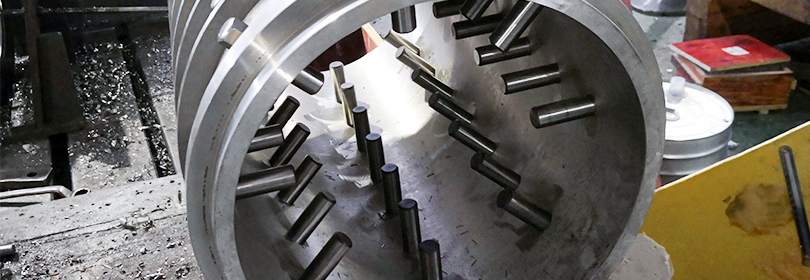
main parts of bead mill
Comparison of the types of separators
The kind of separator offered by the bead mill manufacturers like Franli is the one where they have their own weak and strong points and are chosen in accordance to the characteristics as well as the selected size of the bead.
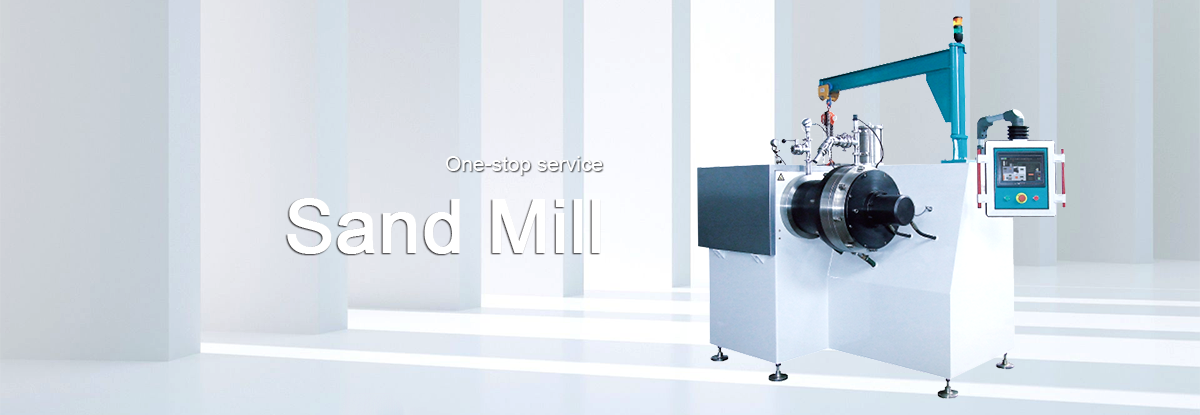
Copyright Notice :
This article only represents the author’s point of view.
This article is published under the authorization of the author.
Source: Franli
This article address: What is a bead mill?
Related Products
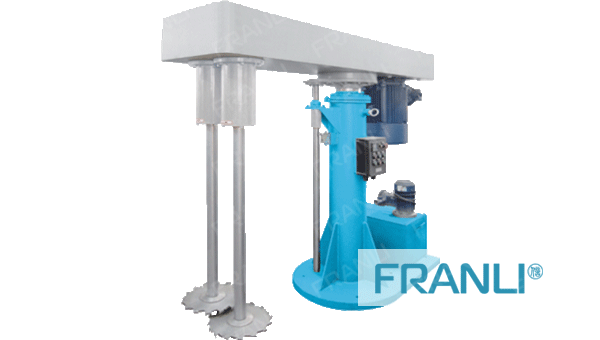
FRANLI Twin Shaft Disperser
Franli Twin Shaft Disperser is composed of a low-speed anchor stirring and two high-speed dispersing disc paddles to realize the function of dual-axis high-speed dispersion.
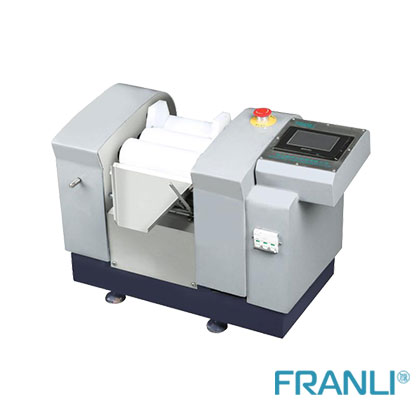
Triple roller mill
Three-roller mills are also called triple roller mills. In daily work, they can be divided into Lab triple roller mills and production triple roller mills. They are mainly used in ink, paint, paint and other industries.
News
Laboratory Reactor: Guide to Stirring System
The laboratory reactor is composed of a pot body, a pot cover, an agitator, a jacket, a support and transmission device, a shaft seal device, etc.
Grinding Media for Bead Mill | Zirconia Beads & Zirconium Silicate Beads
Bead mills mainly use grinding balls as media, and use impact, extrusion, and friction to achieve the final grinding effect, which mainly depends on the size and hardness of the grinding beads, the filling rate of the grinding beads, and the collision frequency adjustment between the grinding beads and the particles.
Overview of Laboratory Reactor
Laboratory reactors, also known as lab reactors, are essential tools in scientific research, product development, and process optimization. These reactors provide a controlled environment for conducting chemical reactions, mixing, dispersing, and homogenizing processes.
Bead mills | Manufacturing technology in various industries
Bead mills, also known as sand mills or grinding mills, are versatile machines widely used across various industries for the wet grinding and dispersion of solid particles in liquid media.
Ribbon Blender Mixer Equipment
A ribbon blender mixer, also known as a ribbon mixer or horizontal ribbon blender, is a powerful industrial machine designed for thorough and efficient blending of various materials.
What is A Stainless Steel Reactor?
Stainless steel reactors are essential equipment in various industries, including chemical, pharmaceutical, biotechnology, and food processing.