Home » Three roll mill for silicone rubber
Three roll mill for silicone rubber
Three roll mills are the most effective equipment for grinding and dispersing high-viscosity materials and are widely used in slurry manufacturing in paint, ink, pigment, plastic, and other industries. The principle is to work by pressing the surfaces of the three rollers against each other and friction at different speeds. The material of the grinder is the centrifugal casting of chilled alloy cast iron, and the surface hardness exceeds HS70°. The diameter of the roller is ground with high precision and fineness so that the grinding fineness of the material can reach about 15 microns so that uniform and fine high-quality products can be produced.
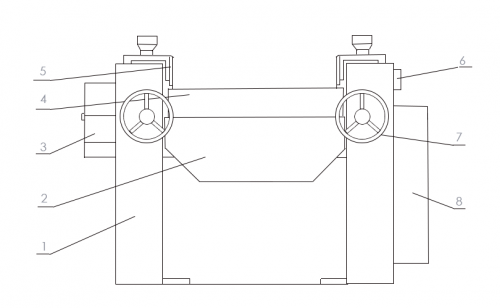
(1) Body, (2) Discharge plate, (3) Cooling system, (4) Roller, (5) Baffle plate, (6) Electrical switch or electrical control system, (7) Handwheel, (8) Transmission system
The working principle and procedure of the three roll mill:
Three roll mill is the most effective grinding and dispersing equipment for high viscosity materials. The three roll mill is composed of the front, middle, and rear three rollers, and two baffles. The violent friction reaction of the raw material is caused by the opposite asynchronous rotation of the two rollers. Strong shear forces break down the structural stress between molecules in the raw material particles. After the second grinding of the first two rollers, the raw materials can be quickly pulverized and dispersed, so that various highly uniform mixed raw materials can be obtained.
To grind liquid silicone rubber with low viscosity and good mechanical strength of vulcanizate, it is impossible to achieve the ideal target requirements simply by using low molar mass base polymers and increasing the proportion of fillers. According to the specific requirements of the process performance and performance of liquid silicone rubber, the expected results can be achieved by the comprehensive use of the basic polymer combination, the appropriate filler matching and vulcanization system, and the fine mixing process and preparation technology.
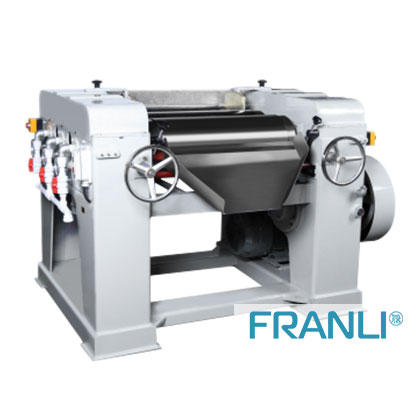
⑴ Kneading and mixing of silicone rubber compound
The production of liquid silicone rubber mostly goes through the kneading and mixing process of silicone polymer plus filler. The kneading and kneading operation is not only the simple mixing of the materials, but also the extrusion and shearing of the materials during the kneading process, which promotes the infiltration of the filler and the polymer, and the filler is evenly dispersed in the polymer, which may play a reinforcing role. During the kneading process, the high-consistency material has a strong shearing effect and high mixing efficiency. For the mixture of the low-filler ratio system (relatively dilute viscosity), the extrusion resistance cannot be formed when it is stirred by the stirring paddle of the kneader, that is, the material with excessively low viscosity Failure to withstand effective rubbing and shearing will affect the reinforcement effect. Therefore, even if a silicone rubber compound with a low filling ratio is produced, it is best to knead a high-viscosity thick material first, and then add a polymer to dilute it to a predetermined low filling ratio.
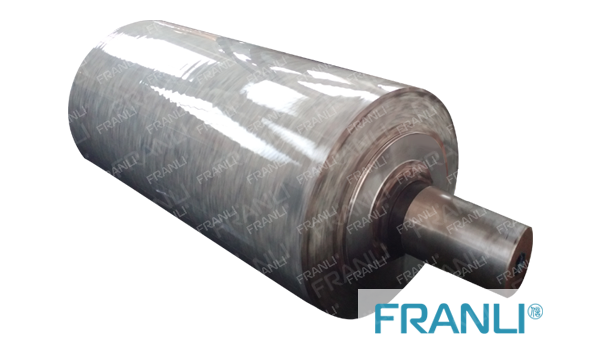
⑵ Processing of silicone rubber compound
The silicone rubber compound is prepared directly using the paste obtained by kneading at room temperature. The fluidity of the silicone rubber may be poor. Appropriate heat treatment is performed on the paste. The low molecular weight in the compound is equivalent to the modification agent, which can improve the wetting of the polymer and filler surface while reducing the viscosity of the rubber compound and improving the mechanical properties of the vulcanizate.
It is not advisable to use a high-speed mixer for a long time and high-speed shearing to produce liquid silicone rubber. Because the silicone polymer is sheared at a high speed for a long time, part of the silicone polymer chain may be sheared, and the obtained silicone rubber has a thin viscosity, but the mechanical properties of the vulcanizate will be significantly reduced. In the same way, when the liquid silicone rubber is thinned through the three roll mill, it is necessary to control the appropriate roller distance, which not only ensures the shearing and kneading effect but also avoids the shearing of the silicone polymer chain.
Through the scientific structural design of FRANLI engineers, the fineness and uniformity of the ground materials can reach the ideal level. Three-roll grinding machine is one of the main products of our factory. Our technical engineers have concentrated on researching and improving this machine many times, which has greatly improved its competitiveness in the grinding machine market. If you are still looking for a suitable three-roll machine manufacturer and supplier, you can contact us directly.
Copyright Notice :
This article only represents the author’s point of view.
This article is published under the authorization of the author.
Source: Franli
This article address : Three roll mill for silicone rubber
Related Products
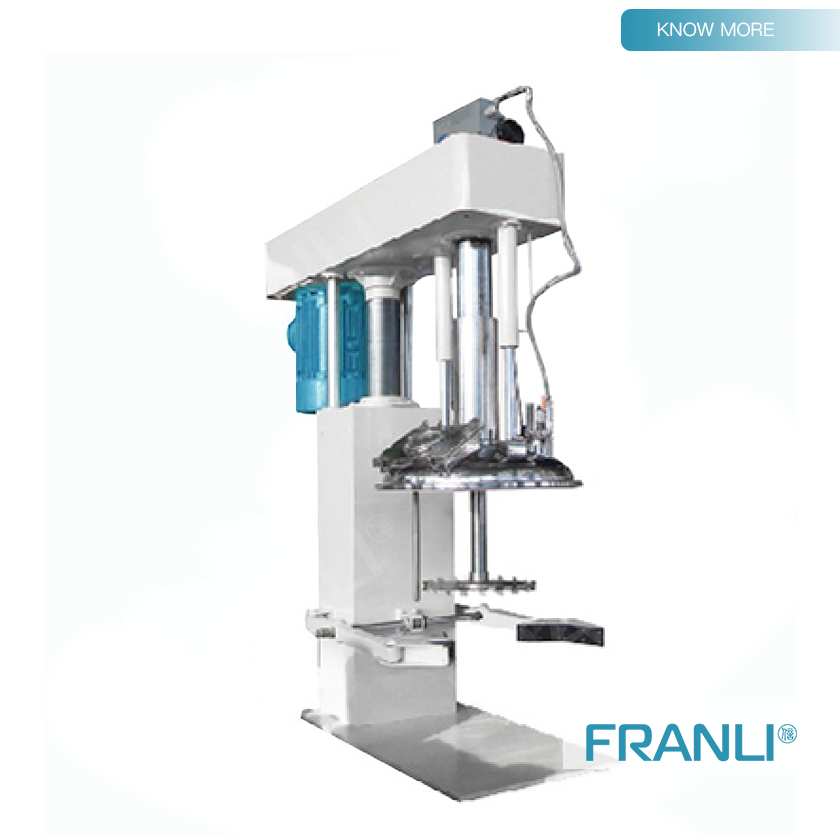
High speed dissolver
High speed dissolver for sale: FRANLI high speed dissolver is one high-efficiency equipment that can mix, dissolve and disperse various liquid mixtures.
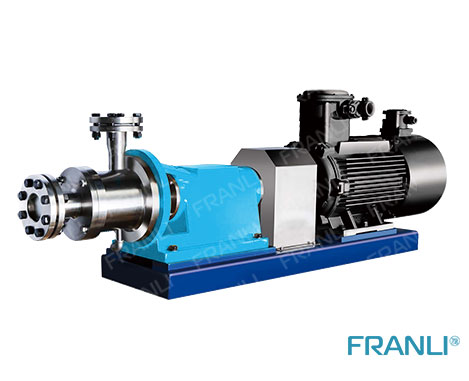
Inline Emulsifier
The inline emulsifier is composed of three sets of stators (two layers, four layers, and six layers) in the working cavity, which has higher processing accuracy, large processing capacity, and wide processing viscosity range.
News
Laboratory Reactor: Guide to Stirring System
The laboratory reactor is composed of a pot body, a pot cover, an agitator, a jacket, a support and transmission device, a shaft seal device, etc.
Grinding Media for Bead Mill | Zirconia Beads & Zirconium Silicate Beads
Bead mills mainly use grinding balls as media, and use impact, extrusion, and friction to achieve the final grinding effect, which mainly depends on the size and hardness of the grinding beads, the filling rate of the grinding beads, and the collision frequency adjustment between the grinding beads and the particles.
Overview of Laboratory Reactor
Laboratory reactors, also known as lab reactors, are essential tools in scientific research, product development, and process optimization. These reactors provide a controlled environment for conducting chemical reactions, mixing, dispersing, and homogenizing processes.
Bead mills | Manufacturing technology in various industries
Bead mills, also known as sand mills or grinding mills, are versatile machines widely used across various industries for the wet grinding and dispersion of solid particles in liquid media.
Ribbon Blender Mixer Equipment
A ribbon blender mixer, also known as a ribbon mixer or horizontal ribbon blender, is a powerful industrial machine designed for thorough and efficient blending of various materials.
What is A Stainless Steel Reactor?
Stainless steel reactors are essential equipment in various industries, including chemical, pharmaceutical, biotechnology, and food processing.