Home » Instructions for use of the three roll mill
Instructions for use of the three roll mill
The three roll mill is one of the best products among the mills, and it is especially suitable for dispersing equipment for grinding high-viscosity materials. Three roll mills are widely used in the manufacture of slurry in paint, ink, pigment, plastic, and other industries.
The working principle of the three roll mill:
The three-roll grinder achieves the grinding effect by squeezing the surface of three horizontal rollers and friction at different speeds. The material of the roller body of this grinder is the centrifugal casting of chilled cast iron, and the surface hardness is above HS70. The grinding roller has high diameter precision and high fineness, which can make the grinding fineness of the material reach about 15 microns, and produce uniform and fine high-quality products. Grinders are super-efficient equipment for grinding and dispersing high viscosity materials. It is widely used in the grinding of chemical raw materials such as paints, inks, inks, paints, dyes, plastics, rubber, lead cores, leather, medicine, food, cosmetics, insulating materials, and so on. It has various functions such as grinding, dispersing, emulsifying, homogenizing, and toner. It enables uniform mixing of raw materials and recycling of waste materials.
Preparation of the three roll mill:
- Check whether the position and locking of each component are normal, inject lubricating oil as shown in the figure, and turn on the power;
- Adjust the front and rear handwheels and observe whether the continuous movement of the rollers is normal.
- Clean the dirt on the roller surface: wipe with soft paper or clean cotton yarn, loosen the baffle, and pinch the handle;
- Adjust the gap between the front and rear rollers and the middle roller to 0.5 mm, then start the power supply and idle for 1-2 minutes.
The working procedure of the three roll mill:
After starting the operation, adjust the gap between the middle and rear rollers to 0.3mm, press down the baffle plate, add pulp appropriately, visually inspect the depth of shading, fine-tune the rear rollers to make the shading evenly distributed on the rollers, and tighten the fixing nut.
Adjust the handwheel of the front roller with both hands at the same time, so that the front roller slowly touches the current roller surface of the middle roller. After evenly coloring, tighten the fixing nut, and then adjust the angle of the blanking plate so that it presses on the roller surface correctly to make the slurry Discharge evenly. Check the discharge uniformity and finished product size, and continue to fine-tune the front and rear rollers until the finished product size meets the predetermined requirements. The cutter head should be returned to the front and rear in time.
After the three roll mill stops working:
Clean up the paint in time, wipe the test roller and related parts, loosen the knife and baffle, apply a small amount of oil, and then protect it with wax paper.
Precautions for the operation of the three roll mill
- After starting, adjust the gap between the middle and rear rollers to 0.3mm, press the baffle, add slurry appropriately, visually inspect the coloring depth, and fine-tune the rear rollers, so that the coloring spreads evenly on the rollers, and lock the fixing nut.
- Adjust the handwheel of the front roller with both hands at the same time, so that the front roller and the surface of the current roller are slowly contacted, uniformly color, lock and fix the nut, and then adjust the angle of the material plate so that it is properly pressed on the roller surface, and the slurry can be uniform discharge. Check the discharge uniformity and finished product size, and continue to fine-tune the front and rear rollers until the finished product size meets the predetermined requirements. Note that the front and rear scrapers should be returned in time.
Copyright Notice :
This article only represents the author’s point of view.
This article is published under the authorization of the author.
Source: Franli
This article address : Instructions for use of the three roll mill
Related Products
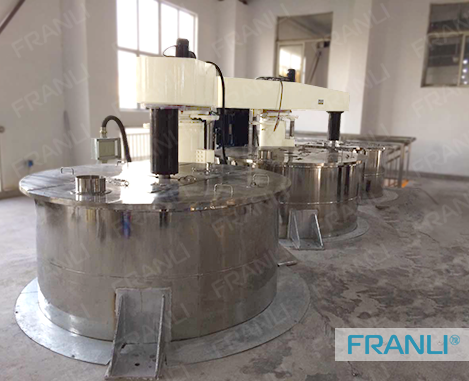
Platform Type High Speed Disperser
Platform type high-speed disperser is mainly used for high production material. Normally the high-speed disperser is installed between two tanks, easily mixing material in two tanks. also another type.
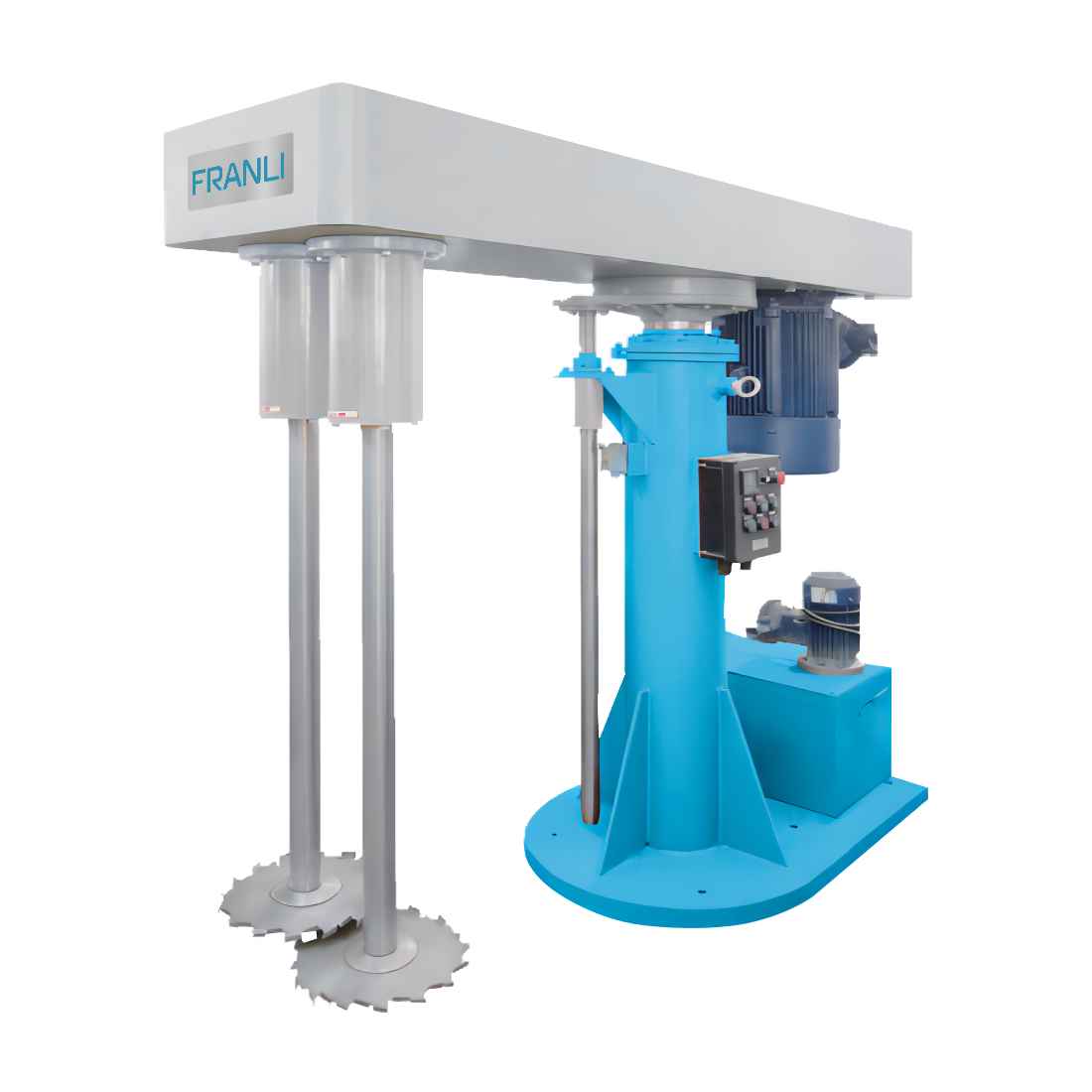
Dispersion Machine
This HSD-D Dispersion Machine with two shafts for mixing and dispersing materials to reach higher efficiency. This machine should be installed jacket tank with a cooling system. The dispersion machine has two shafts working temperature
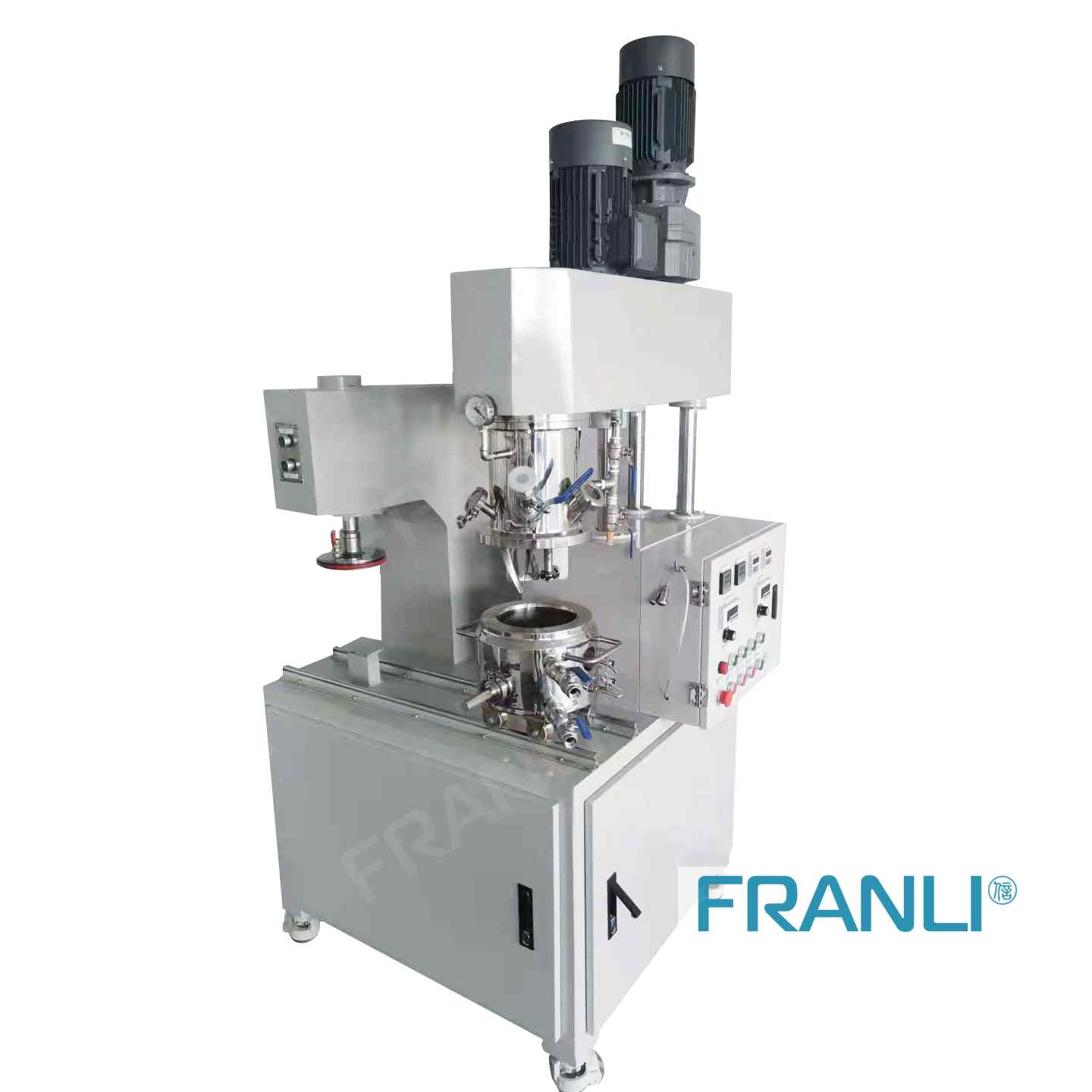
Laboratory Double Planetary Mixer
Laboratory double planetary mixer is a kind of non-standardized strong mixing and mixing equipment developed by FRANLI for universities, research institutes, and factory laboratories.
News
Laboratory Reactor: Guide to Stirring System
The laboratory reactor is composed of a pot body, a pot cover, an agitator, a jacket, a support and transmission device, a shaft seal device, etc.
Grinding Media for Bead Mill | Zirconia Beads & Zirconium Silicate Beads
Bead mills mainly use grinding balls as media, and use impact, extrusion, and friction to achieve the final grinding effect, which mainly depends on the size and hardness of the grinding beads, the filling rate of the grinding beads, and the collision frequency adjustment between the grinding beads and the particles.
Overview of Laboratory Reactor
Laboratory reactors, also known as lab reactors, are essential tools in scientific research, product development, and process optimization. These reactors provide a controlled environment for conducting chemical reactions, mixing, dispersing, and homogenizing processes.
Bead mills | Manufacturing technology in various industries
Bead mills, also known as sand mills or grinding mills, are versatile machines widely used across various industries for the wet grinding and dispersion of solid particles in liquid media.
Ribbon Blender Mixer Equipment
A ribbon blender mixer, also known as a ribbon mixer or horizontal ribbon blender, is a powerful industrial machine designed for thorough and efficient blending of various materials.
What is A Stainless Steel Reactor?
Stainless steel reactors are essential equipment in various industries, including chemical, pharmaceutical, biotechnology, and food processing.