Home » Grinding process of different types of bead mills
Grinding process of different types of bead mills
A massive range of tools for the bead mill machine can help to get milling done. The original class of the bead mill was used here in terms of milling and grinding purposes. These machines then turned into the centers of the machining with the automatic tool enriching it along with the carousels as well as the tool magazines out there with the capabilities of the CNC machining as well as the cooling systems associated with the housings. Vertical machining centers, as well as horizontal centers, are noteworthy aspects of the complete bead milling process.
Multi-Tasking Machines
With the help of the live tooling for the occasional and lathes use in terms of the milling cutters and turning operations were made possible with the integration of the milling here. A new class of machining tools was then led to the creation of it with the bead milling process that was designed specifically for facilitating the milling as well as the turning under similar work surfaces.
Milling
The process of cutting where the cutter will be removing the materials from the surfaces of the workpieces here is done through the milling process with the help of the bead grinding machine. The cutter for milling is moved perpendicular, usually to its axis, to help the cutting to take place all around the perimeter of the milling cutter here, unlike that of the drilling done where their tool is being moved all around the axis of the rotation here.
Different Classes Of Bead Milling Process
The action of cutting generally occurs mainly at the corner ends of that of the cutter here in the face of milling done with the help of a bead mill. The cutting action in the circumferential milling takes on the circumference of the milling cutter so that the cross-sectional path to the surface milled is shaped accordingly.
Comparison Of the Bead Mills
So, it is extremely important to have an understanding of the differences lying between the horizontal well as vertical bead mills. The tasks performed by these two kinds of bead mill are often the same as it works according to the bead mill design. These machines do have their own set of pros and cons, and it is essential to note the differences here.
Vertical Bead Mill
The common kind of bead mill design having a vertically oriented cutting head as well as the spindle holding and rotating the cutting tools that are relative to that of the workpieces here is what this mill is generally used as.
In terms of the unilateral projects, including the work with the larger metal plates along with the sinking matrices is where these mills are the ideal ones. Each set of the bead mill has its own unique offerings here.
Turret mill: The table moves perpendicularly and parallels to the spindle here in terms of the turret mill. It is extremely versatile here as you are considering the way it is able to manipulate the position of the material present in both directions here.
Bed mill: The material here is moved perpendicular to that of its axis here. The spindle here is attached to its vertical axis to help it move up and down as required with the help of the bead mill working principle.
The following are the significant features of the vertical bead mill machines:
(1) Popularity: The machines here can make up the major part of the milling machines offered by the bead mill manufacturers. They are extremely affordable compared to that of the horizontal mills in terms of making a smart investment here that would pay of extremely well.
(2)Ease of use: The operators here get better visibility in times of operations with the construction of the vertical bead mill. Programming here is extremely easy thanks to the CNC controls that are extremely user-friendly. These are the aspects that the bead mill manufacturers keep in mind while constructing this kind of machine. Operators, therefore, will not be wasting any time in terms of operations and focus mainly on making sure that the specifications of the project are met with the highest of the standards here. The machines here would be operated by professionals who are able to complete the project in a safer way.
(3)Production benefits: In terms of finishing off the larger sheets, the visibility that is offered by the bead mill is extremely great. It is quite well-suited for the lesser tasks of complexities that need the smaller amounts offered with the ease of the use of the machine here. In terms of fast work done by the bead mill, this machine is considered to be the ideal choice.
Horizontal Bead Mill
Here in this machine, the spindle here removes materials by pressing against the workpiece here and is quite similar to that of the construction. These differ a lot from the vertical bead mill devices in a myriad of ways. Orientation of the spindle is the vital difference between the two millers here. There is also a vertical orientation of the spindle here for the horizontal mills and vertical for the vertical bead mills. The horizontal machines are mounted over the cutting head on the spindle that is oriented horizontally, capable of selecting the removal of material from the workpiece to place in simpler terms.
Features Of Horizontal Mills
(1)Chip evacuation: When the cut is in progress, gravity is sure to aid in the removal of the chips due to the position of the mills here. It will be translating into the end products with the clean surfaces bringing later the much less needed productions here.
(2)Solid construction: The bead mills here are able to tackle the larger productions where the machine parts of the bead mill are built to last longer.
The horizontal bead mills are often manufactured and supplied by the well-reputed and well-known bead mill manufacturer, Franli. They are responsible for the growing number of machines that are used widely for grinding and milling.
Copyright Notice :
This article only represents the author’s point of view.
This article is published under the authorization of the author.
Source: Franli
This article address:Grinding process of different types of bead mills
Related Products
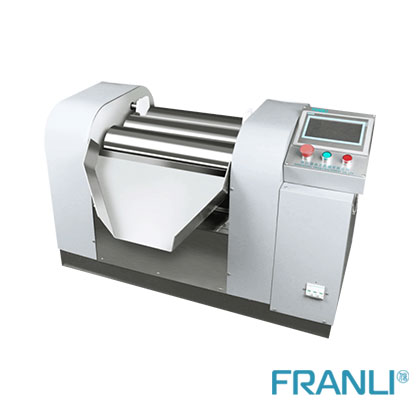
Digital Control Three Roll Mill
The roller of the digital control three roll mill is made of zirconia ceramic material and equipped with a frequency conversion speed regulating device to meet the grinding needs of different materials.
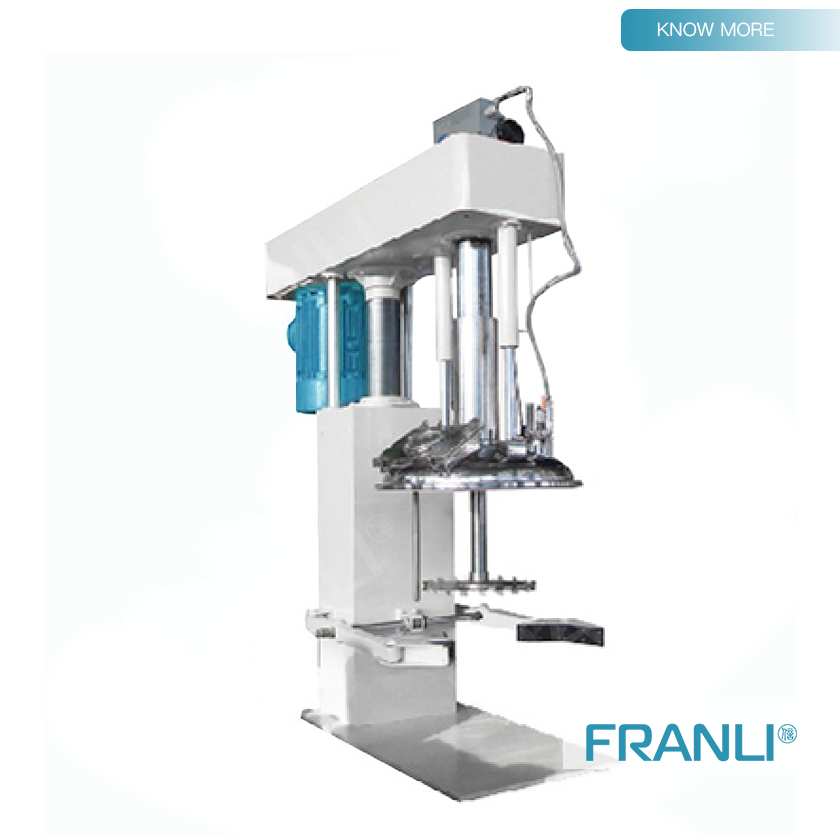
Vacuum Disperser
The function of a vacuum disperser reduces bubbles and solvent volatilization, faster material defoaming, and improves dispersion fineness. Easily operation, strong frame, high vacuum <-0.07mpa.
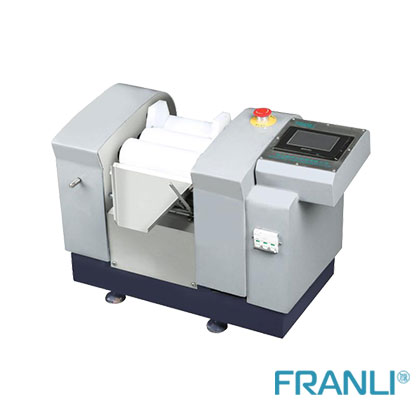
Three roll mill
Three roll mills are widely used in a variety of chemical industries, from medium to high viscosity productions. FRANLI machine can break open all kinds of pigment, UV ink, offset ink, decorative paints, and Lubricants, it also can catch the greatest fine
News
Laboratory Reactor: Guide to Stirring System
The laboratory reactor is composed of a pot body, a pot cover, an agitator, a jacket, a support and transmission device, a shaft seal device, etc.
Grinding Media for Bead Mill | Zirconia Beads & Zirconium Silicate Beads
Bead mills mainly use grinding balls as media, and use impact, extrusion, and friction to achieve the final grinding effect, which mainly depends on the size and hardness of the grinding beads, the filling rate of the grinding beads, and the collision frequency adjustment between the grinding beads and the particles.
Overview of Laboratory Reactor
Laboratory reactors, also known as lab reactors, are essential tools in scientific research, product development, and process optimization. These reactors provide a controlled environment for conducting chemical reactions, mixing, dispersing, and homogenizing processes.
Bead mills | Manufacturing technology in various industries
Bead mills, also known as sand mills or grinding mills, are versatile machines widely used across various industries for the wet grinding and dispersion of solid particles in liquid media.
Ribbon Blender Mixer Equipment
A ribbon blender mixer, also known as a ribbon mixer or horizontal ribbon blender, is a powerful industrial machine designed for thorough and efficient blending of various materials.
What is A Stainless Steel Reactor?
Stainless steel reactors are essential equipment in various industries, including chemical, pharmaceutical, biotechnology, and food processing.