Zirconia beads for sale|Zirconia beads price
Zirconia beads, also known as zirconia grinding balls, zirconia ceramic balls, zirconia beads, ultra-fine grinding media, zirconia beads, zirconia grinding balls.
Advantages of Zirconia beads:
- High density
- High hardness and good toughness
Application

Coating

Cosmetic

Battery

Graphite

Agrochemistry

Adhesives
Frequently Asked Questions
Sand mill is also called bead mill. A type of grinding and dispersing equipment for solid-liquid phase dispersion of powdery materials and liquid materials. As the grinding medium, a sand mill was initially used, so it was called a sand mill; later, glass beads were used, so it was also called a bead mill. The grinding media currently used are sand grains with rounded corners, beads made of various glass or wear-resistant materials, steel balls, and steel shavings. This kind of wet ultrafine grinding equipment is widely used in the dispersion and grinding of pigments in the ink production process.
A rotating shaft is axially inserted into the vertical or horizontal cylinder, and several grinding discs, rings, or pins are installed radially on the rotating shaft. The cylinder is filled with grinding media with a particle size of 0.6-2mm. The simplified version is equipped with a jacket with cooling water in the middle to absorb and dissipate the heat generated during the grinding and dispersing process. The material is pumped into the barrel, together with the grinding medium, it is strongly stirred by the high-speed rotating grinding disc, and it is thrown along the disc to the wall of the cylinder and back again. The slurry flow reciprocates between the discs so that the solid material is gradually evenly dispersed in the liquid material. middle. The method of unloading varies with the viscosity of the material. Generally, the suspension can be used to flow out through a screen with slit holes, and the width of the holes is 1/2-1/3 of the grinding medium. The bead mill is a device that uses hard and wear-resistant zirconium beads, glass beads, etc. to rotate in a closed cavity to grind pigments.
Different types of ink used bead mills in different structures
Intaglio ink production generally uses pin rods (5-50 liters) or disc bead mills (10-100 liters).
Rotary offset printing inks generally use vertical rod type (5—130 liters) or horizontal disc type bead mills (60 to 500 liters), while the production of ultra-high viscosity sheet-fed inks often uses high energy density cone bead mills or three roll mills.
Inkjet inks (inks and pigment solvent-based inks) generally use high-energy-density pin-type (horizontal or vertical) bead mills and turbo-centrifugal nano-bead mills.
The new bead mill is the main grinding and dispersing equipment in the ink production process. The bead mill is a fully enclosed grinding equipment with automatic feeding, automatic temperature, and pressure control devices, and can carry out continuous production operations.
When the bead mill is running, the rotor agitates the meson (beads) to move at a high speed, and the high-speed running medium and the grinding cavity plays a role of dispersion through impact, friction, and shear. The vertical bead mill is a fully enclosed type, which can continuously grind and disperse granular and non-granular solid materials in liquid.
The structure and characteristics of the bead mill are:
①For grinding different varieties, the computer can input the pump flow rate, heating time, grinding chamber pressure, material temperature, and other technical data in advance according to the characteristics of the variety, and then the computer can automatically control it according to the input program.
②The annular groove on the stator can meet the different requirements of the product, and the high-precision special isolation groove can be used for the special viscosity.
③The temperature, pressure, feed pump flow rate of the rotor and stator are automatically displayed, and there are protection devices such as temperature and pressure.
④The grinding efficiency and dispersion degree can be obtained by adjusting the flow rate of the feed pump and the filling amount of the beads.
⑤Due to the use of special and latest technical materials, the grinding area and the isolation area are particularly wear-resistant, and will not affect the hue of the material.
⑥Bead mills usually have safety self-locking and alarm devices, and some faults can be automatically eliminated.
Hot sale bead mill
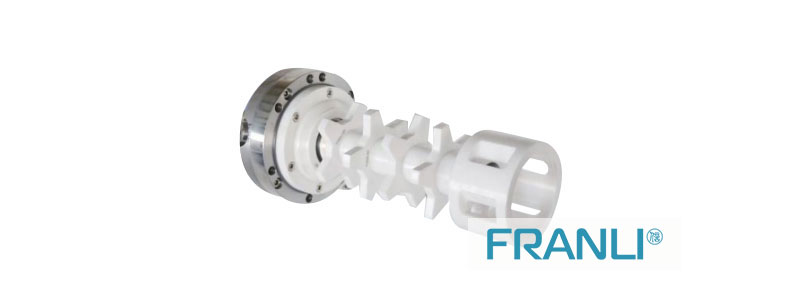
• Easy installation of the bead mill machine: The best features of this bead mill machine are: You can easily install it wherever you want. This task is so simple, and effortless. And due to this feature, it is extremely popular among other equipment. You can find the bead mill working principle so effective, and you can perform all the mixing tasks effectively without adding so much effort. As this machine is very bulky and cheap, it needs only a few minutes to install. In this way, you can reduce the labor charges and other exhausting jobs. So, you can stay worry-free about how to install this machine? As the company has made this task easier for you.
• Efficient work performance of this bead mill machine: As we know, the bead mill working principle has been created in such a way that you can achieve higher and efficient work performance on this bead mill machine. If you are looking for quality and stable work, these bead mill machines are the best option to get a consistent mixture of any particular material. You can use this bead mill for paint, ink, and coating industries. And, it is a comfortable and easy method to perform all the mixing and dispersing activities without wasting so much time. So, here bead mill working process is so necessary to obtain the desired results for the company.
• Contains grinding media of 2-3 mm size: It is the necessary feature of the bead mill working process as it includes the grinding media. In this area, grinding and other dispersing activities take place that they turn into a fine mixture. You can use a bead mill for paint, ink, and coating industries, where mixing works have been done regularly. It contains grinding media of 2-3 mm size that is enough to transform all the material to a smooth and fine paste. For this purpose, bead mill manufacturers have added advanced technology to this machine to provide consistent and quality work performances for the company. In this way, you can get a higher productivity ratio. And you can reach the peak of the higher conversion rate. Thus, these bead mill machines are ideal for fabrication companies to get their desired goals with full efficacy.
• Easy operation of the bead mill machine: It is a great feature of this SMP Agitator bead mill machine as bead mill manufacturers create this bead mill machine with advanced technology. And, with this quality, the operation of this sand grinding mill is extremely comfortable. You do not need to call any professional to do the same, and you can do it yourself without adding so much effort. So, it is another best feature to consider about this bead mill machine.
• Easy to clean the bead mill machine: This sand grinding mill is remarkably best for the fabrication companies to enhance the overall growth and production. As we know, while we use any bead mill machine, we need to clean it so that we can get hygienic work performance. For this purpose, companies manufacture this bead mill machine in a way that you can clean it comfortably without making yourself exhausted. You can go through the bead mill pdf and other relative documents that provide you the guidelines of clean this bead mill machine.
• Easy to maintain the bead mill machine: Maintaining is also a matter of concern as it requires your time and money. For this purpose, you can check the bead mill pdf and manual provided by the company at the time of purchase. You can either contact the company or read the manual carefully to know all the information about the bead mill machine. And, you can find this process is extremely simple to perform. So, you can get this bead mill machine without spending so many amounts on it. And, in this way you can concentrate on the work performance of the company.
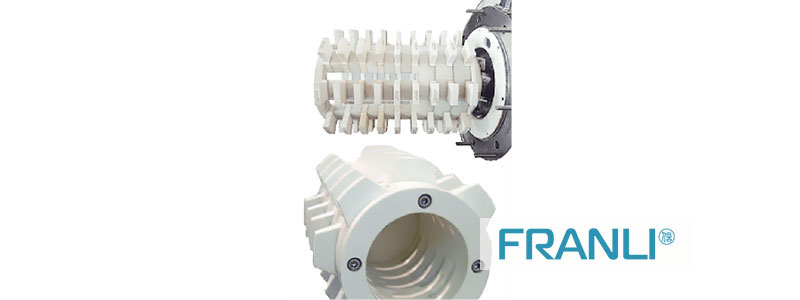
Also, you can use SMP Agitator bead mill in paint industry, ink, and other coating work companies to make all the mixing and grinding activities easier and more manageable. To get this bead mill machine, you search for those companies that deal in these machines and other equipment. For this purpose, you can get a quote or related other information about the bead mill machine.
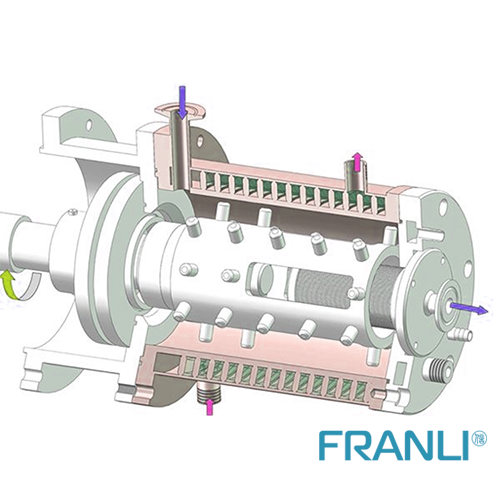
Hydraulic TRH type
Hydraulic Three Roll Mill, which is a full hydraulic auto-controlling system equipment. 1- Cooling system: an individual cooling system for each roller. 2- hydraulic control: hydraulic control pressure blades, roller gaps, etc. 3- Optional installation:PLC system with SIEMENS touching screen, FRANLI engineer set formulas of grinding according to different viscosity materials.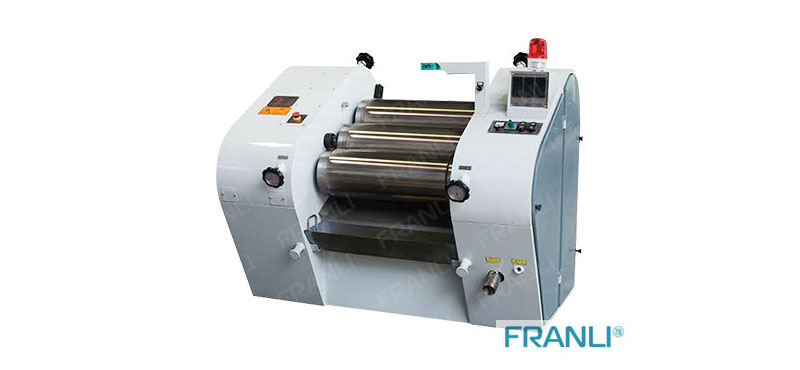
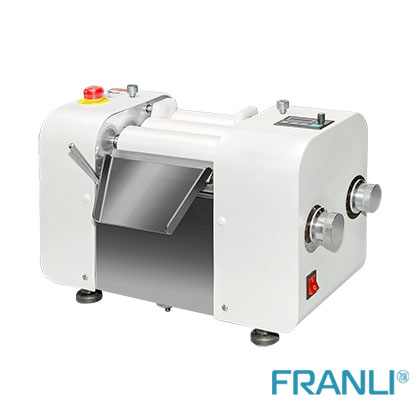
Vertical type for Grinding Powder
Also, we have a vertical three-roll mill for grinding powder and chocolate. We have 3 rollers, 4 rollers, and even 5 rollers, which are all vertical types. We export to the soap industry and chocolate companies.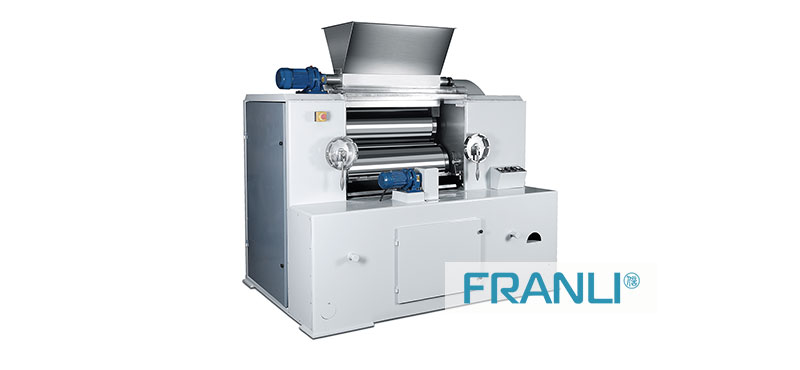
Heating type
Franli also offers a heating hydraulic three roll mill for rubber, EVA, PVS, and color masterbatch. As this type of machine grinds high viscosity material, we specially design the gear quality. This type is been Heated by oil or steam. Franli three roll mill machine are full automatic PLC controlling, hydraulic system, stable operation, reliable quality. We choose the international brand parts. Standrad parts, ABB VFD, Siemens Motor, SKF or NSK bearings, SEW or Nord reducer. A roller is 45-55mm thickness of metal, cast steel. You can widely choose ceramic, alloy, granite rollers for your material. If you have several formulas of material, we can set up formulas in the PLC system, your workers only need to choose numbers on touching the screen, don’t need to waste time to adjust the rollers’ gap or the pressure of the blade.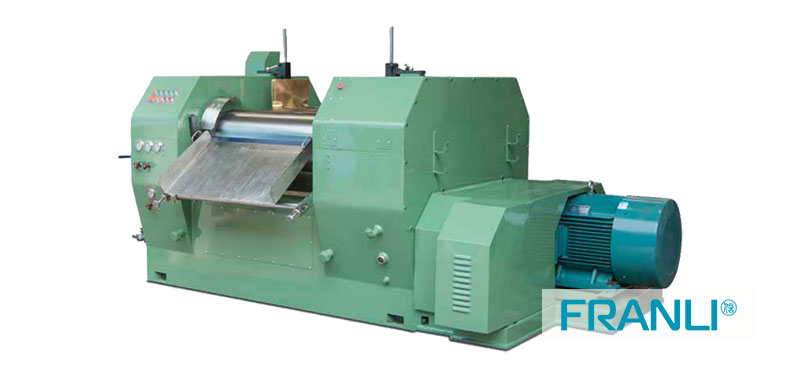
Related production lines
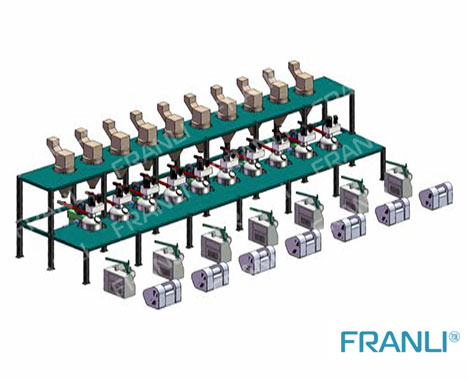
Offset Ink machine line
FRANLI is specialized in offset ink full line production for 20+ years. Helped customer save the cost, save the man power, also save the space.
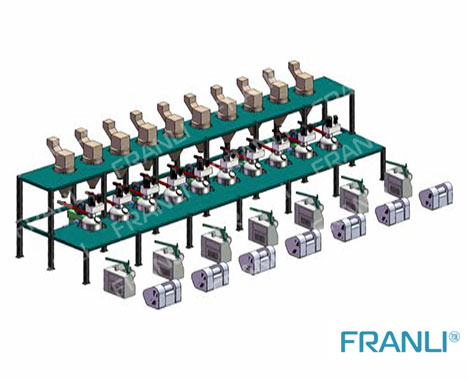
Offset Ink machine line
FRANLI is specialized in offset ink full line production for 20+ years. Helped customer save the cost, save the man power, also save the space.
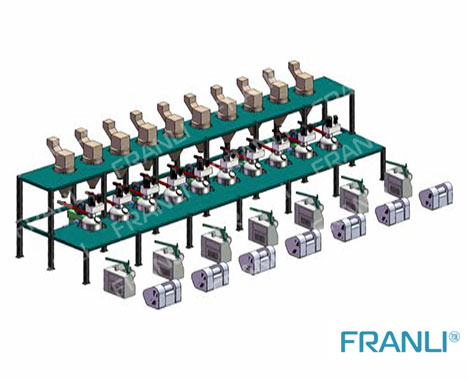
Offset Ink machine line
FRANLI is specialized in offset ink full line production for 20+ years. Helped customer save the cost, save the man power, also save the space.
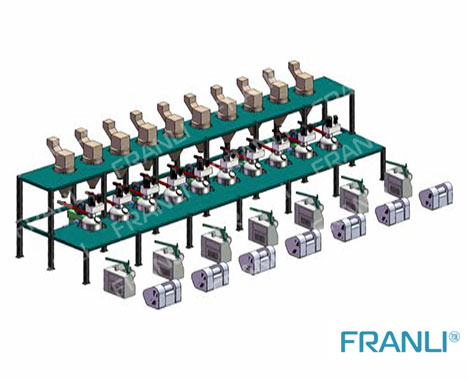
Offset Ink machine line
FRANLI is specialized in offset ink full line production for 20+ years. Helped customer save the cost, save the man power, also save the space.
Technical Parameter
Guidelines For Zirconia beads
Zirconia beads, also known as zirconia grinding balls, zirconia ceramic balls, zirconia beads, ultra-fine grinding media, zirconia beads, zirconia grinding balls.
Characteristics of zirconia beads
Compared with other ceramic grinding media, zirconia beads have three outstanding characteristics: first, high density; Second, it has high hardness; Third, good toughness. Although the purchase cost is relatively large, the comprehensive use cost is very advantageous, especially suitable for the occasions requiring low impurities.
- High density
First of all, the density of zirconia beads is large, so the ratio is large, the impact force is large, and the crushing energy is large. Under the same conditions, the grinding time can be greatly reduced, making the material grinding more efficient.
- High hardness and good toughness
1.The hardness of zirconia ceramic is about 12-14gpa, the strength is up to 800-1000mpa, and the fracture toughness is up to 10MPa
2. Therefore, zirconia beads have high crushing strength and are not easy to be damaged, and their extremely low wear can significantly reduce the introduction of impurities into the ground material. So it is very suitable for sanding mill, high-speed vibration mill and other equipment, especially in some areas sensitive to impurities. Less broken beads and wear, no need to replenish frequently, so the comprehensive use cost is relatively low.
Preparation of zirconia beads
The preparation methods of zirconia beads mainly include pressing, rolling and dropping.
- Press forming
This is a common forming method for large-size zirconia beads, mainly including dry pressing and isostatic pressing.
Dry pressing has the advantages of simple and convenient operation, less investment in technology and capital. However, due to the uneven pressure distribution, the internal distribution of the blank is inconsistent, which affects the comprehensive performance of the product. In order to improve the density of the blank, the method of increasing the pressure is often used in the actual production. However, the higher the pressure is, the better. When the pressure exceeds the limit pressure, the density of billet will decrease, which is caused by spalling.
However, the green body formed by isostatic pressing has high strength, high density and uniformity, which can prepare high performance and high quality grinding medium balls. Therefore, two methods can be combined to produce high performance ceramic balls in industry.
- Roll into a ball
In addition to the cold isostatic pressing process, rolling ball is also an important forming method of ceramic ball. This method has the characteristics of production equipment, raw materials, simple operation, good sphericity and easy sintering. Although the strength of the ball is not as good as that of cold isostatic pressure, the preparation cost is low, and various sizes of balls in the range of 0.1mm-60mm can be produced according to the requirements.
- Droplet balling
For small size zirconia beads (0.05mm to 0.05mm), the green ceramic beads can be formed by titration. The zirconia ceramic beads produced by titration method can be sintered at low temperature without internal pores, and have high density, high strength, high toughness, low wear and other properties. It is suitable for the dispersion and grinding of electrode materials, multilayer ceramic capacitors, paints, coatings and other high-performance materials.
Related production lines
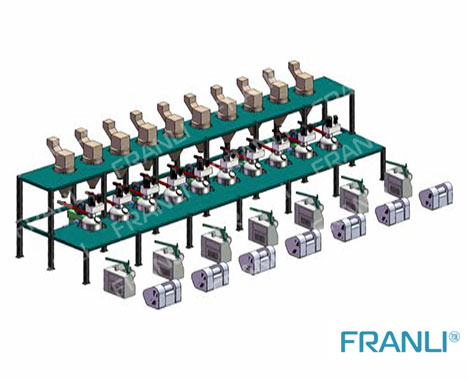
Offset Ink machine line
FRANLI is specialized in offset ink full line production for 20+ years. Helped customer save the cost, save the man power, also save the space.
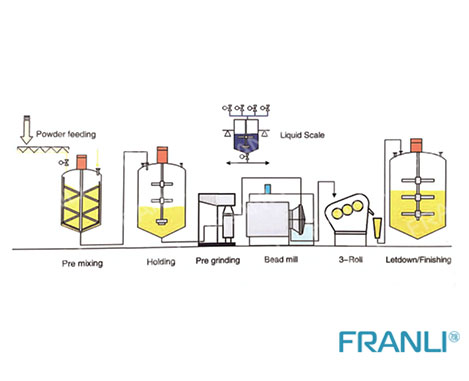
Offset Ink, UV Ink machine line
The FRANLI engineering company, offer the full set of UV INK Production Line, we can make the full drawing according with your factory size, formulas, weather and safety system.
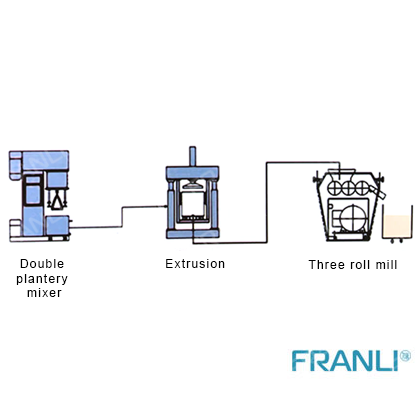
PCB INK Machine line
FRANLI supplies all equipments for the production of PCB inks, from the powder feeding station to the filling part.
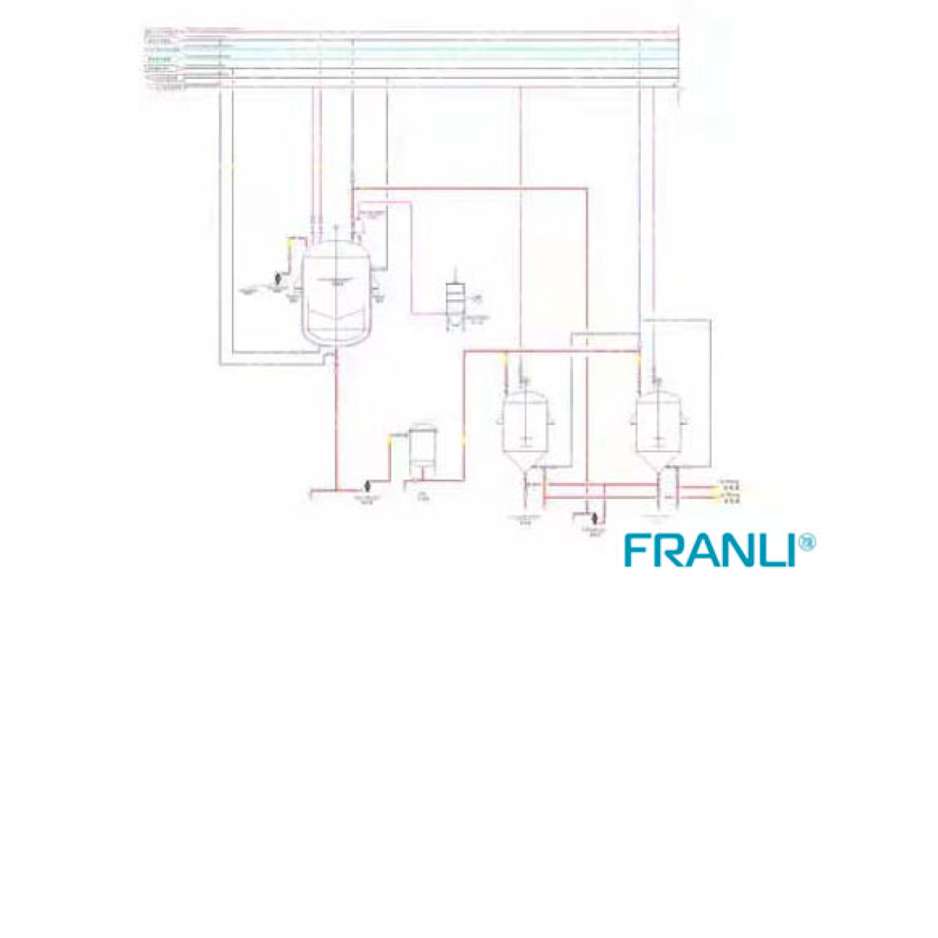
EW-pesticide line
The EW production line mainly mixes raw materials, solvents, and emulsifiers through a reactor (oil-based).
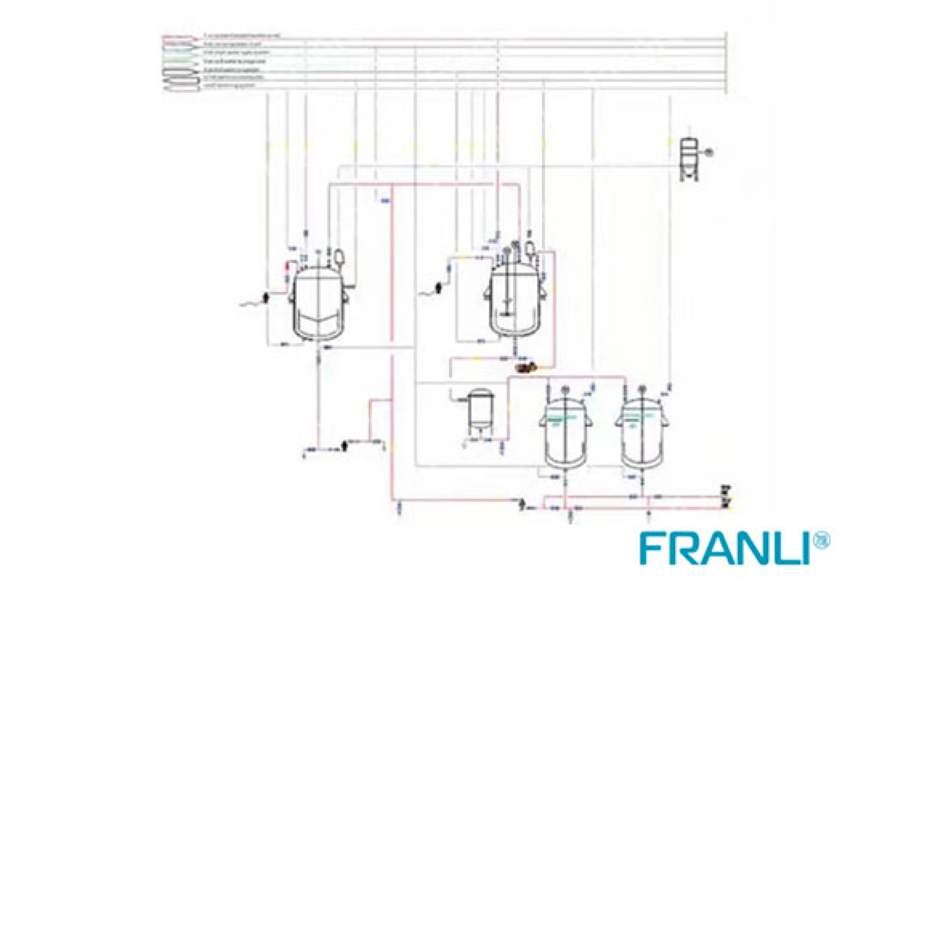
SL_EC pesticide line
The EC production line is mainly composed of an agitator mixer, bag filter, filling machine, etc.
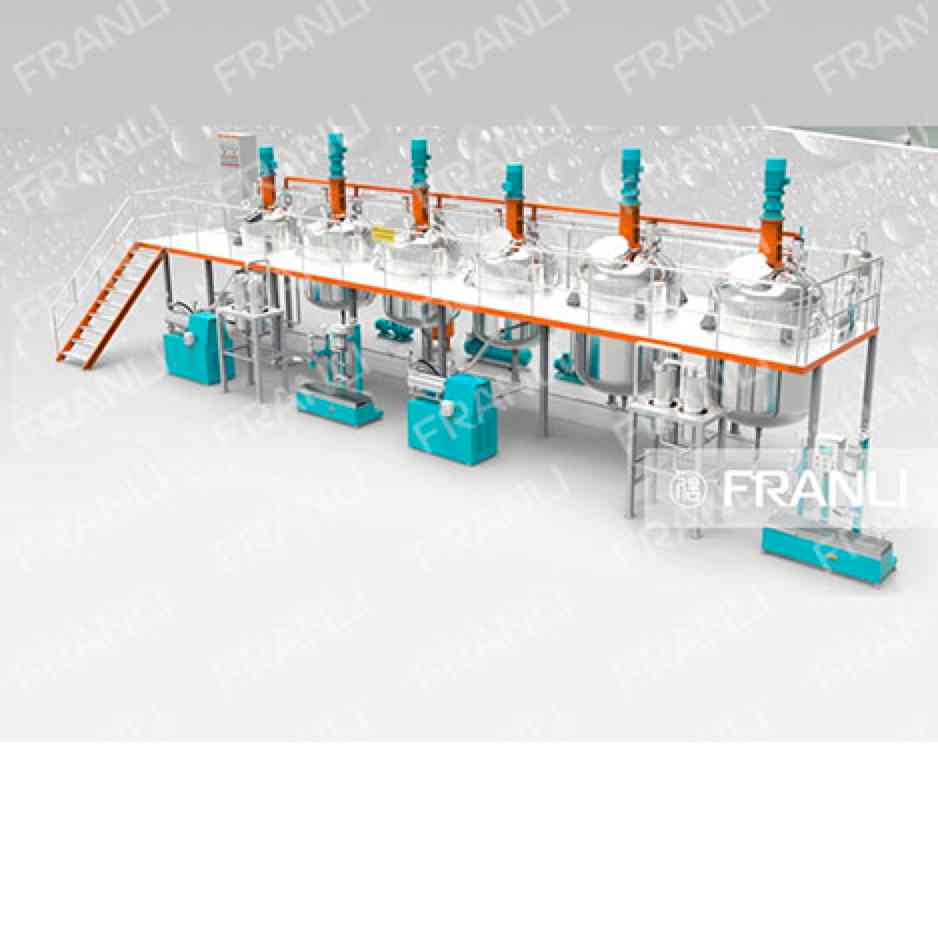
Automotive Paint machine line
The automotive paint machine line is mainly for the production and grinding of automotive paint, Automotive paint has many layers, such as Primer/electrophoretic layer, Medium coat, Colored coat, and Clearcoat.
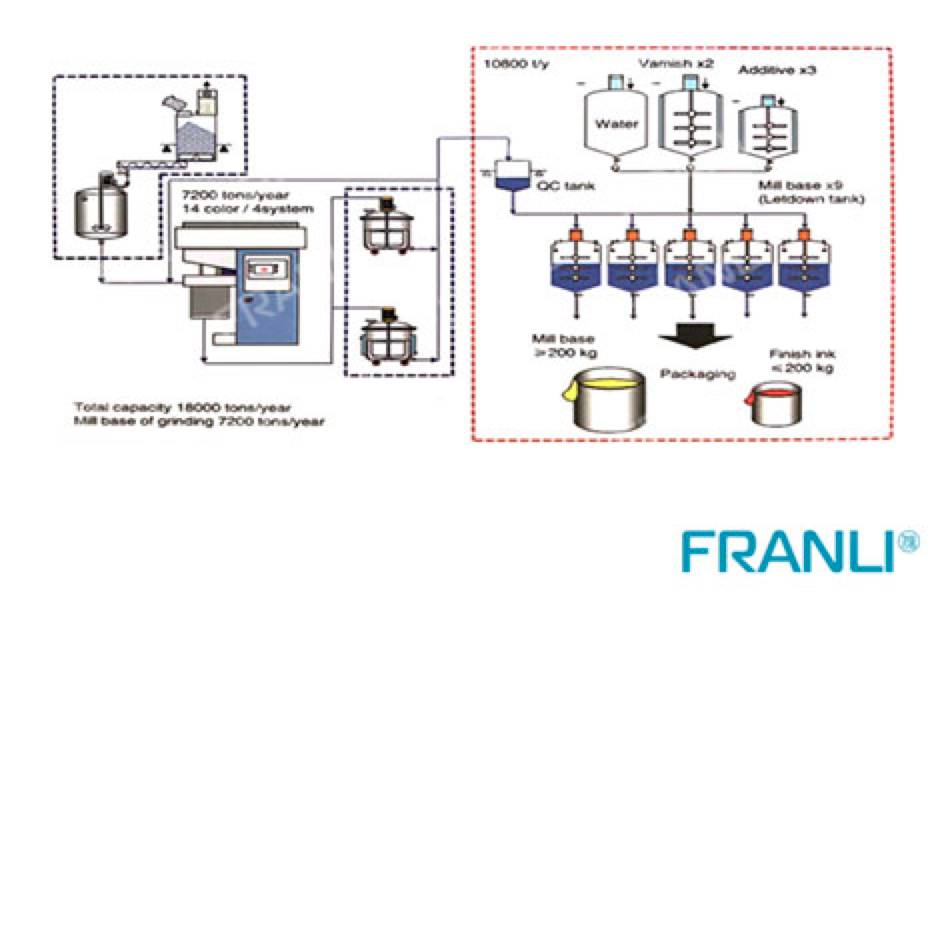
Digital Ink machine line
Franli has professional experience for digital ink machine line, we offered hundreds customers to expand production, or build up new project.