Wet Bead Mill|Bead Mill For Sale
Wet bead mills are used for grinding and dispersing granular materials to micro and nano-scale grinding. It has the characteristics of simple operation, high separation efficiency, high grinding fineness, and is equipped with an advanced cooling system to achieve large flow production.
Application:
New energy nanomaterials, coatings, medicines, cosmetics, etc.
Advantages of wet bead mill:
- low grinding fineness
- Wide range of applications
- high working efficiency
Application

Coating

Cosmetic

Battery

Graphite

Agrochemistry

Adhesives
Frequently Asked Questions
For achieving a great finer range of gauge powders, the toll processors have a range of wet and dry milling processes with the help of the bead mill.
Wet grinding is often the process that is quite preferred for the size of particle reduced to that of a finer scale down to their micrometer and even the range of a bead mill machine, and it is also termed as the wet media milling process.
In terms of improving processability and the efficacy of the ingredients active in nature as that of the agrochemicals and pharmaceuticals, fine milling with the help of bead mill machine, micronization along nanonization can be quite useful here.
For getting the extremely smaller size of the particles and higher surface area of the particles here in terms of achieving the greatest possible vibrancy along with the opacity of the pigments within the coatings, inks, and even cosmetics can be used by the bead mill.
Wet milling here can assist the bead mill manufacturers in terms of getting higher value for the minor quantities of the valuable substances that can be resulting in considerable savings over the raw materials is that we can get here.
dyno mill
Operations of wet grinder
Bead mill, bead grinding machine, batch mills are also categorized under the wet milling machines by the bead mill manufacturers. Wet milling needs several distinctive steps that can change on the basis of varied characteristics of the raw feed, unlike that of the dry mechanical milling processes.
The experts of wet milling understand the variables that are included in the bead grinding machine for milling processes. It can include the milling of the media sizes and types, ingredients, ratios of the liquid slurry, speed of the mills, etc.
SMP agitator bead mill
STEP 1: WETTING
The initial step that is included under wet grinding eliminates air from the surface of the raw feed to make sure the particles to be in complete contact with that of the liquid slurry. It is extremely important to mill in the most effective way as it needs the liquid with lower surface tension than that of the free surface energy of the solids here.
It massively depends on the material being milled with the help of a bead mill, and this is important to go ahead and select the right kind of liquid here.
STEP 2: CHARGING THE MEDIA MILL
The solid particles are suspended within the liquid to be able to collide with each other, along with the milling media of the bead grinding machine being the raw feed within the liquid slurry circulating through the bead mill. The size of the particle is thereby reduced with the shear forces along with the impact here.
They are generally based on the material characteristics of the raw feed along with the desired size of the final particle here in terms of the milling media size and the type. The bead mill here includes the following components:
- Glass
- Steel
- Tungsten carbide
- Ceramic
- Zirconium oxide
- Polymer resins
The final size of the particle, along with the morphology, is also impacted well by the size of the grinding media. In terms of determining the ideal combination of the speed, time, and media before scaling up for the complete production on the larger bead mill design, the smaller-scaled processing trials are performed.
STEP 3: DEAGGLOMERATION
There are raw materials out there that have the tendencies or clumping together in the best manner. They should be separated from each other or even deagglomerated for dispersing the solid particles within the liquid milling slurry of the bead mill design.
STEP 4: DISPERSION IN LIQUID
Complete dispersion of the solid particles all over the liquid slurry makes sure of the uniformity of the bead mill once deagglomeration is done of the raw feed. It can have a great effect on the efficiency of the milling that follows the bead mill working principle. It greatly impacts the viscosity and is quite relative to that of the solid raw feed included here.
For avoiding the flocculation as well as sedimentation, the dispersed raw feeds within the liquid slurry often have the requirement for being stabilized. Dispersion additives usually do the job in accordance with the bead mill working principle for the materials that include the inorganic pigments along with the ores here. Expertise matters the most here in terms of selection as well as the quantities of the stabilizers and others associated with the bead mill.
STEP 5: WET GRINDING
The liquid here is dispersed with the solids that are circulated in the bead mill with the grinding media till achieving the final size of the particle as well as the grind gauge and surface characteristics achieved here in this step here. In the hands of an expert operator of the equipment, this also needs multiple passes along with adjustments to the speed of the bead milling process.
The materials here are duly analyzed for the assurance and process control in this step of the bead milling process. It can help make sure of the timely completion of the projects without the need of waiting for the tests as well as the analysis from the other labs here with the capabilities of the bead mill.
STEP 6: SEPARATION
The media and the material within the bead mill achieve the size specifications here with the screening of the slurry separating the milling media from that of the products here.
STEP 7: DEGASSING OR DRYING
The end-users of the material here are degassed or even dried, depending on the milling process. They are released effectively with the degassing of the liquid that makes sure of all the air or gases that are entrapped here. When the resulting final product remains dispersed in the liquid here is when this process is used.
There is a team of experts from Franli who are offering the milling processes irrespective of whether it is for wet or dry milling, and this can help you effectively achieve fruitful outcomes here. You can surely trust the decisions being made with great interests in your mind irrespective of the industry, raw materials, and others. These are the significant theories and practicalities associated with the bead mill.
It is mesmerizing onto the number of products included in our daily lives that have undergone the grinding process. Grinding with the help of a bead mill is the main step to get the important products for marketing in their right form ranging from breakfast cereal to cold medicine to cement and paint.
There are significant challenges as well as benefits associated with wet and dry grinding with the help of a bead mill machine, including the two of the commonest ones that are effective in terms of grinding methods. We are going to break them down effectively along with discussing them all here in this article.
Exploring the definitions of grinding, micronization, milling, wet/dry, and likewise
They are relatively interchangeable in terms of grinding and milling with bead mill machine. You may regularly refer to the process of milling if you know a piece of tool which is known to be the bead mill used here. Grinding might also be used as the general way in terms of describing it, while the other may not be quite familiar with it. It is better not to get caught up as there is no single difference between the two here.
So, what do we understand by micronization here within the technology of particles? The term here is a lot more specific, mainly referring to the reduction in particles in the size range of sub-10 micron. So, every micronizing is associated with grinding, but not all grinding is going down to the particle level of micronizing for the bead milling process.
So, what is the level of a nanometer in terms of particle reduction here in the bead milling process? The sizes are almost as equal to 1,000 nanometers as it refers here to the sizes that are almost less than 1 micron. It is better to note that the average size of the nano here is approximately 200-500 nanometers.
The terminologies involved here with the wet and dry grinding are often the overarching words describing basically each of the two other bead mill working principles here. The processes here are quite different, although the goals here lie to be the same. Dry grinding under the bead mill working principle makes use of the contact of the particle to particle for the reduction in size along with getting the wet grinding involved here with dispersing of the bead mill into the liquid with the use of solid grinding media in terms of reduction in size.
Similarities & differences between wet and dry grinding
It is relatively a process that is quite simple in terms of dry grinding used by bead mill manufacturers. Material is traveling within an area that is contained, impacting the rest of the particles here as well as the rotors till it can break into its desired size within any specific number of specialized machines here. Particles are generally dispersed in the liquid slurry, having being crushed with the help of grinding media in terms of dry wet grinding.
Dry grinding is making use of a single pass process where the material is going in and is expelled once in a bead mill, for instance. There is the slurry that is exposed to the grinding media over and over for a longer time if required till the size desired for the particle is achieved here, being a process of recirculation as used by the bead mill manufacturers.
The one challenge that is pretty common to both dry grinding and wet grinding is the potential wear on the grinding equipment being used for breaking down the material as well as the construction materials, although the methods for grinding are different from one another after the understanding of the bead mill price.
There might be plenty of abrasives within the material that can over time damage the tool here in terms of dry grinding and in knowing the bead mill price. The carrier fluid of the wet grinding or the material here should be compatible chemically with surfactants and solvents that can eat off the grinding media of the equipment as well as the parts that are used for agitating the media itself.
It is extremely important that the grinding media of the equipment do not end up within the product itself, irrespective of it being dry or wet.
Making the right selections
The final application, as well as the performance of the material, is the number one factor for determination while you are deciding between the two methods for the bead grinding machine here.
If there is a specific pyrotechnic material going through the dry grinding is something that needs to be checked. Compared to the wet grinding, the product here has greater characteristics compared to the rest. This alone is enough to go ahead in selecting dry.
The other set of considerations here is the size of the target particle here. Dry grinding allows the particles to head down to the size of a single-digit micron in general. The particles are therefore reduced down to the range of the bead grinding machine by the regular wet grinding method. Wet is the ideal way to achieve your required specifications, while the simplicity of dry grinding would often be considered as the first method included here with the goal of achieving the smaller size.
Considerations to be taken
It arrives simply at the capacity of the size, application, and cost here. Do not lock down a project into wet or dry grinding. In terms of the quantities, can a single grinding method be handled in a better way for the particle size required here?
Packaging is also considered a factor of consideration in terms of the bead mill design. Packaging needs to be able to keep up to a determined number of barrels as grinding is a continuous affair here.
It comes into play here with the need to formulate for the dry as well as wet grinding processes. It is highly efficient in terms of including a lot of particle solid within the mix here since it is extremely obvious. It would be required here in terms of getting additional additives that are detrimental based on the earlier trials as well as the experiences of the bead mill design.
There is a quality of assurance processes within the house that is included within the testing capabilities of the analytical lab. It is vital enough to have the services available for making sure of the end quality of the product while this might not be determining a single method over the rest present here.
It is endless when it comes to the list of materials that can be dry or wet ground with the help of a bead mill.
So, you can name it the way you like, be it grinding or milling, as one thing applies to both the methods proven out, with each needing the upfront guidance of the experts like that of company like Franli and their dedicated capabilities.
Hot sale Bead mill
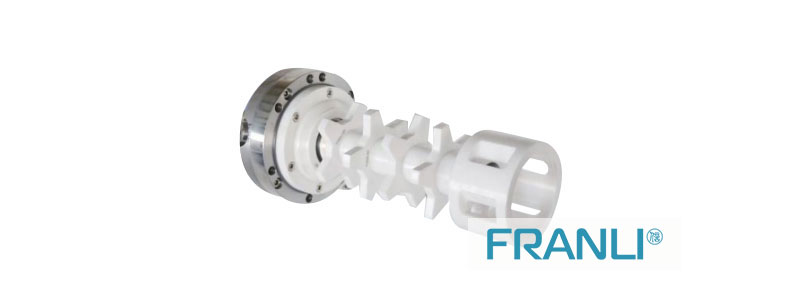
• Easy installation of the bead mill machine: The best features of this bead mill machine are: You can easily install it wherever you want. This task is so simple, and effortless. And due to this feature, it is extremely popular among other equipment. You can find the bead mill working principle so effective, and you can perform all the mixing tasks effectively without adding so much effort. As this machine is very bulky and cheap, it needs only a few minutes to install. In this way, you can reduce the labor charges and other exhausting jobs. So, you can stay worry-free about how to install this machine? As the company has made this task easier for you.
• Efficient work performance of this bead mill machine: As we know, the bead mill working principle has been created in such a way that you can achieve higher and efficient work performance on this bead mill machine. If you are looking for quality and stable work, these bead mill machines are the best option to get a consistent mixture of any particular material. You can use this bead mill for paint, ink, and coating industries. And, it is a comfortable and easy method to perform all the mixing and dispersing activities without wasting so much time. So, here bead mill working process is so necessary to obtain the desired results for the company.
• Contains grinding media of 2-3 mm size: It is the necessary feature of the bead mill working process as it includes the grinding media. In this area, grinding and other dispersing activities take place that they turn into a fine mixture. You can use a bead mill for paint, ink, and coating industries, where mixing works have been done regularly. It contains grinding media of 2-3 mm size that is enough to transform all the material to a smooth and fine paste. For this purpose, bead mill manufacturers have added advanced technology to this machine to provide consistent and quality work performances for the company. In this way, you can get a higher productivity ratio. And you can reach the peak of the higher conversion rate. Thus, these bead mill machines are ideal for fabrication companies to get their desired goals with full efficacy.
• Easy operation of the bead mill machine: It is a great feature of this SMP Agitator bead mill machine as bead mill manufacturers create this bead mill machine with advanced technology. And, with this quality, the operation of this sand grinding mill is extremely comfortable. You do not need to call any professional to do the same, and you can do it yourself without adding so much effort. So, it is another best feature to consider about this bead mill machine.
• Easy to clean the bead mill machine: This sand grinding mill is remarkably best for the fabrication companies to enhance the overall growth and production. As we know, while we use any bead mill machine, we need to clean it so that we can get hygienic work performance. For this purpose, companies manufacture this bead mill machine in a way that you can clean it comfortably without making yourself exhausted. You can go through the bead mill pdf and other relative documents that provide you the guidelines of clean this bead mill machine.
• Easy to maintain the bead mill machine: Maintaining is also a matter of concern as it requires your time and money. For this purpose, you can check the bead mill pdf and manual provided by the company at the time of purchase. You can either contact the company or read the manual carefully to know all the information about the bead mill machine. And, you can find this process is extremely simple to perform. So, you can get this bead mill machine without spending so many amounts on it. And, in this way you can concentrate on the work performance of the company.
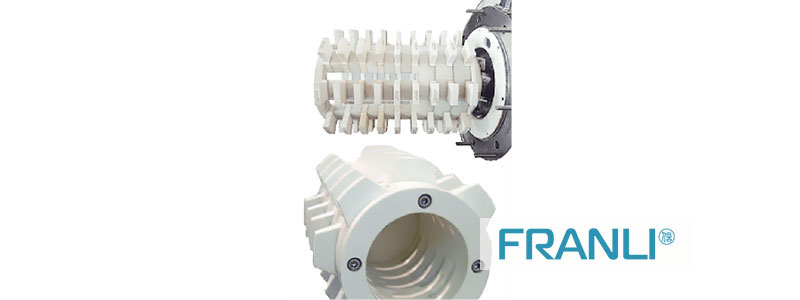
Also, you can use SMP Agitator bead mill in paint industry, ink, and other coating work companies to make all the mixing and grinding activities easier and more manageable. To get this bead mill machine, you search for those companies that deal in these machines and other equipment. For this purpose, you can get a quote or related other information about the bead mill machine.
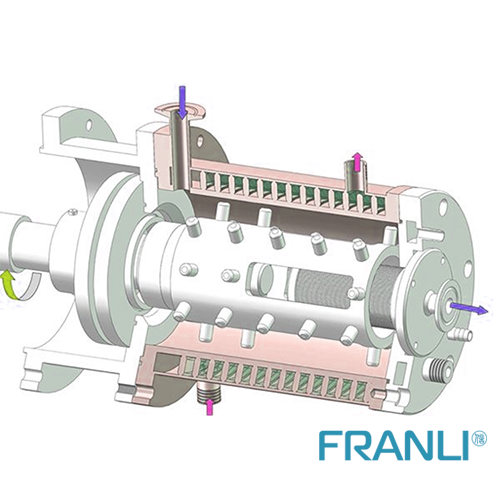
Hydraulic TRH type
Hydraulic Three Roll Mill, which is a full hydraulic auto-controlling system equipment. 1- Cooling system: an individual cooling system for each roller. 2- hydraulic control: hydraulic control pressure blades, roller gaps, etc. 3- Optional installation:PLC system with SIEMENS touching screen, FRANLI engineer set formulas of grinding according to different viscosity materials.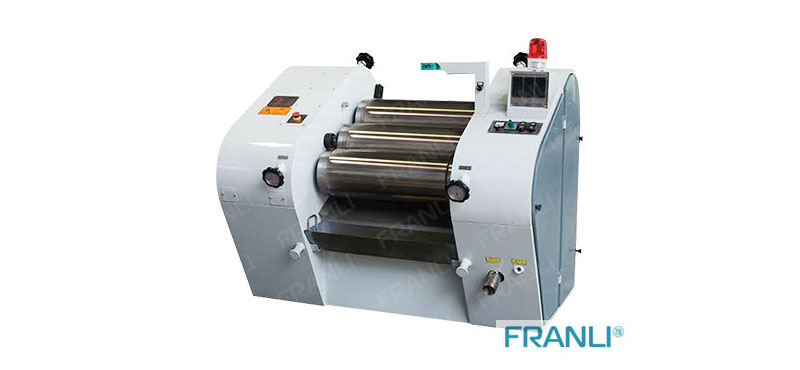
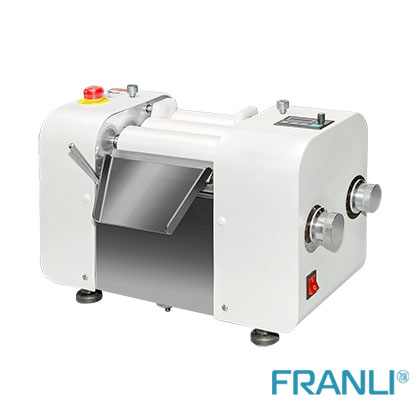
Vertical type for Grinding Powder
Also, we have a vertical three-roll mill for grinding powder and chocolate. We have 3 rollers, 4 rollers, and even 5 rollers, which are all vertical types. We export to the soap industry and chocolate companies.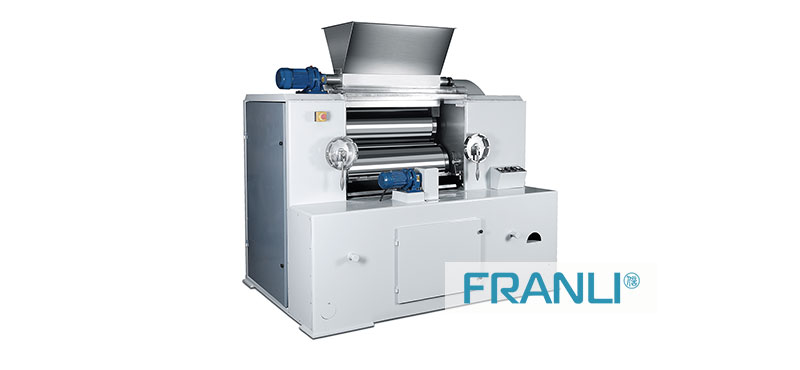
Heating type
Franli also offers a heating hydraulic three roll mill for rubber, EVA, PVS, and color masterbatch. As this type of machine grinds high viscosity material, we specially design the gear quality. This type is been Heated by oil or steam. Franli three roll mill machine are full automatic PLC controlling, hydraulic system, stable operation, reliable quality. We choose the international brand parts. Standrad parts, ABB VFD, Siemens Motor, SKF or NSK bearings, SEW or Nord reducer. A roller is 45-55mm thickness of metal, cast steel. You can widely choose ceramic, alloy, granite rollers for your material. If you have several formulas of material, we can set up formulas in the PLC system, your workers only need to choose numbers on touching the screen, don’t need to waste time to adjust the rollers’ gap or the pressure of the blade.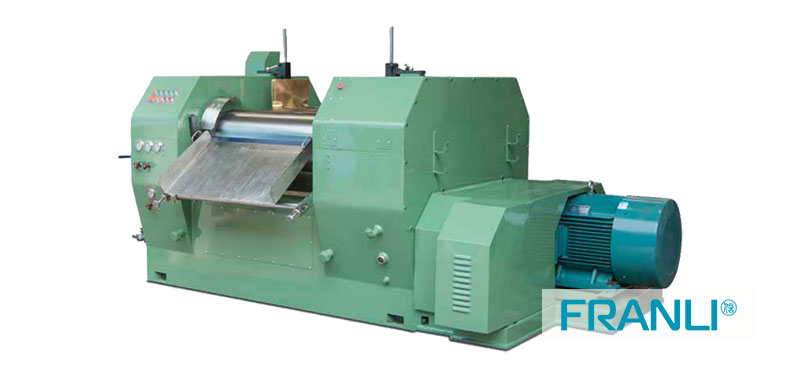
Related production lines
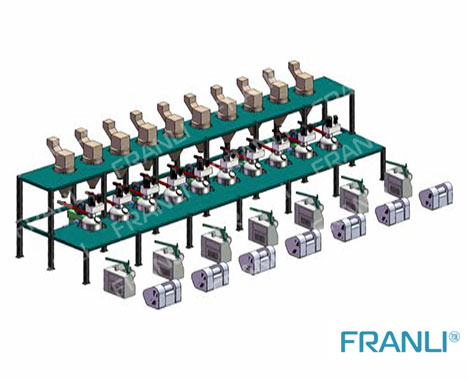
Offset Ink machine line
FRANLI is specialized in offset ink full line production for 20+ years. Helped customer save the cost, save the man power, also save the space.
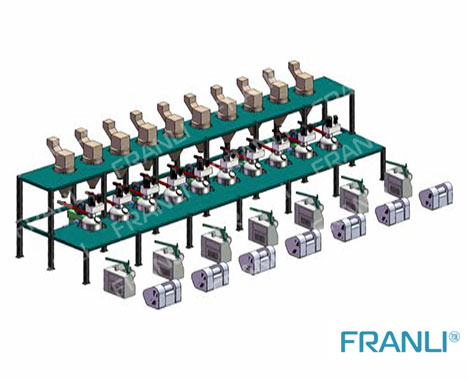
Offset Ink machine line
FRANLI is specialized in offset ink full line production for 20+ years. Helped customer save the cost, save the man power, also save the space.
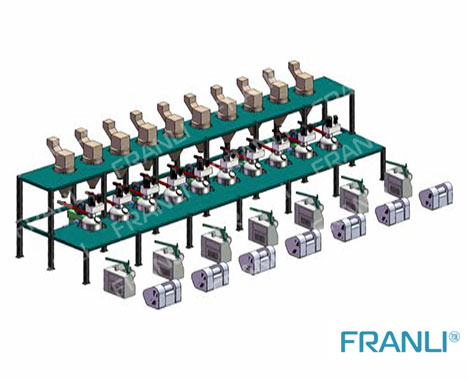
Offset Ink machine line
FRANLI is specialized in offset ink full line production for 20+ years. Helped customer save the cost, save the man power, also save the space.
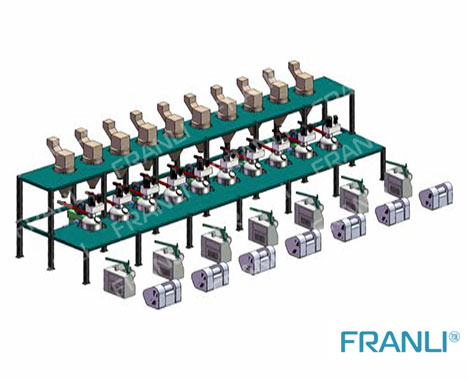
Offset Ink machine line
FRANLI is specialized in offset ink full line production for 20+ years. Helped customer save the cost, save the man power, also save the space.
Guidelines For Bead Mill
Bead mill is essential equipment for any fabrication company, where mixing, grinding, and dispersing activities happens regularly. If you want fine and even work performance, this SMP Agitator bead mill is the must-buy equipment for this process. With the help of this SMP Agitator bead mill, you can obtain speedy and stable activities of the company without adding so much effort.
A Mill that is specially designed for grinding and dispersing particles down to micro and nano scales is termed a wet bead mill. This apparatus agitates beads (grinding media ) in a cylinder-shaped vessel to disperse or grind very minute particles in viscous fluids. The wet bead mill’s rotor causes bead motion, which causes intense shear force and impact on the particles. By optimising the media size, rotor speed, and rotor type, the energy and impact force that materialise the best condition for each material are adjusted. The wet bead mill is used for a variety of tasks, including grinding relatively large particles and dispersing nanoparticles. Particles as small as a micron or a submicron are effectively reduced to finer particles as small as a few tens of nanometers with the help of a wet bead mill.
Application fields of wet bead mill:
A wet bead mill is used to grind food materials, metal oxide for glaze, iron oxide for magnetic tape, dispersing barium titanate for MLCC, and titanium oxide for UV care liquids, among other things. The demand for nanoparticle dispersion has skyrocketed in recent years, particularly in this decade. In addition to traditional applications, wet bead mills are used to disperse particles ranging in size from 20 to 100 nm. Organic pigment dispersions for LC colour filters, zirconia for hard coatings, and barium titanate for advanced MLCCs are examples of such applications.
Dispersing conditions with low impact energy are required for these applications. As a result, the demand for wet bead mills that use microbeads has been increasing. Grinding pharmaceutical nanoparticles is another emerging technology. An efficient grinding with less contamination of metal elements such as zirconium, aluminium, and chromium is required.
How does this bead Mill work?
The principle of operation is that a shaft fitted with grinding discs rotates within a fixed grinding chamber that has been charged with the desired grinding beads. The mill-base is pumped through the grinding chamber, and the high-speed disc rotation moves the beads and mill-base mixture. A slotted screen separates the product from the grinding beads at the outlet.
Bead selection and its importance:
The most important factor in milling practises is bead size. Large beads, larger than 0.5 mm in diameter, are sufficient for grinding micron-size particles into submicron-size particles. Small beads of 0.3 mm or less in diameter are used to grind or disperse submicron or nanometer-sized particles. A large impact is not always required for dispersing, and smaller beads provide faster processing rates as the frequency of contact between a bead and a particle increases. The appropriate impact energy for milling, which is controlled by the bead size, rotor speed, and mass of the beads charged in the mill, is determined by the particle size and hardness.
The frequency of impact between a bead and a particle, which is determined by the rotor speed and bead size, influences the processing rate. The inter-bead space influences the final particle size after milling. The size of the interbead space is proportional to the size of the beads, so smaller beads have a greater chance of contacting the finer particles. It should be noted that the inter-bead space is the area surrounded by beads when they are tightly packed.
grinding process of wet bead mill:
When grinding large or hard particles, high impact energy must be applied to the particles. Because the mass and speed of the beads determine the intensity of the energy, large beads with a high speed are required for grinding large and hard particles. When grinding hard particles such as silica, alumina, and hard natural ores, relatively large beads greater than 0.3 mm in diameter are used as a grinding medium. Large beads, on the other hand, are not always suitable for grinding processing. The size of the beads influences the final particle size. In the case of grinding minute particles as small as 200 nm or finer, beads as small as 0.1 or 0.3 mm are used for grinding. Furthermore, because their larger surface area increases the frequency of impact between beads and particles, smaller beads reduce processing time.
As a result, milling with smaller beads results in a faster processing rate if the particles are soft and the required impact energy is low. When grinding fine particles with diameters of 200 nm or less, the size of the beads is critical. Because the inter-bead space between larger beads is larger, there are fewer opportunities for the particles to come into contact with the beads, resulting in poor grinding efficiency. As a result, practice with small beads is required for grinding fine particles. Beads must be 10 to 30 times the maximum particle size of the raw material and 1,000 to 3,000 times the mean particle size after milling.
Dispersion process of wet bead mill:
The basic concept of bead size selection for dispersing processing is similar to that of grinding processing. The impact energy required for dispersion is controlled so that it does not damage the primary particles while also being sufficient to tear a cluster into primary particles. Damage to the particles is undesirable because each particle is made in the intended size that provides the appropriate properties designed for the final products. The fine fractions act as a binder for re-agglomeration of the particles, so even long-term processing does not complete dispersion. As a result, the impact energy is controlled so that it is neither too strong nor too weak.
Applying low-impact energy via small beads is thus critical for dispersing processing to obtain minimally damaged nanoparticles. Furthermore, small beads provide a high frequency of particle-bead impacts, resulting in a high processing rate. As the primary particles become smaller, it is necessary to select smaller beads in dispersion processing. The ideal bead size is also 1,000 to 2,000 times that of the primary particles. The primary particle size in many cases of modern dispersing practises is 10 to 200 nm, so the bead size to be selected is generally smaller than that for grinding processing.
FRANLI specializes in selling high-speed and more customized dispersers and mixers as well as wet bead mill. The mills they sell are made with reliable parts and are specially designed to meet customer needs.
Related production lines
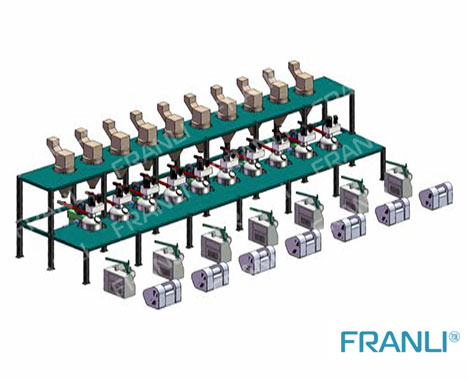
Offset Ink machine line
FRANLI is specialized in offset ink full line production for 20+ years. Helped customer save the cost, save the man power, also save the space.
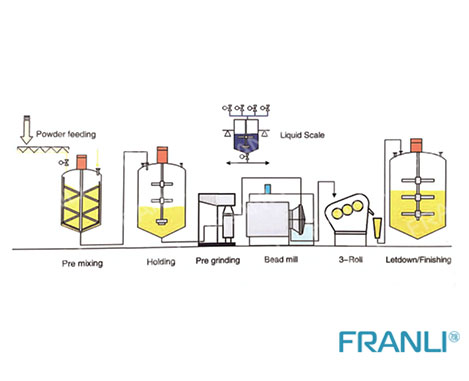
Offset Ink, UV Ink machine line
The FRANLI engineering company, offer the full set of UV INK Production Line, we can make the full drawing according with your factory size, formulas, weather and safety system.
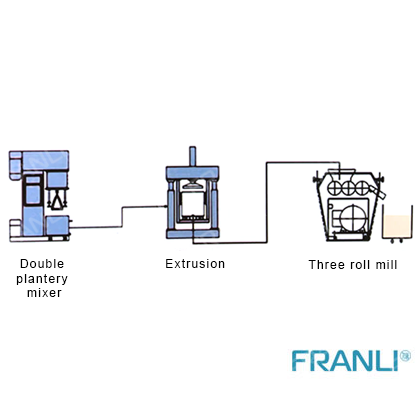
PCB INK Machine line
FRANLI supplies all equipments for the production of PCB inks, from the powder feeding station to the filling part.
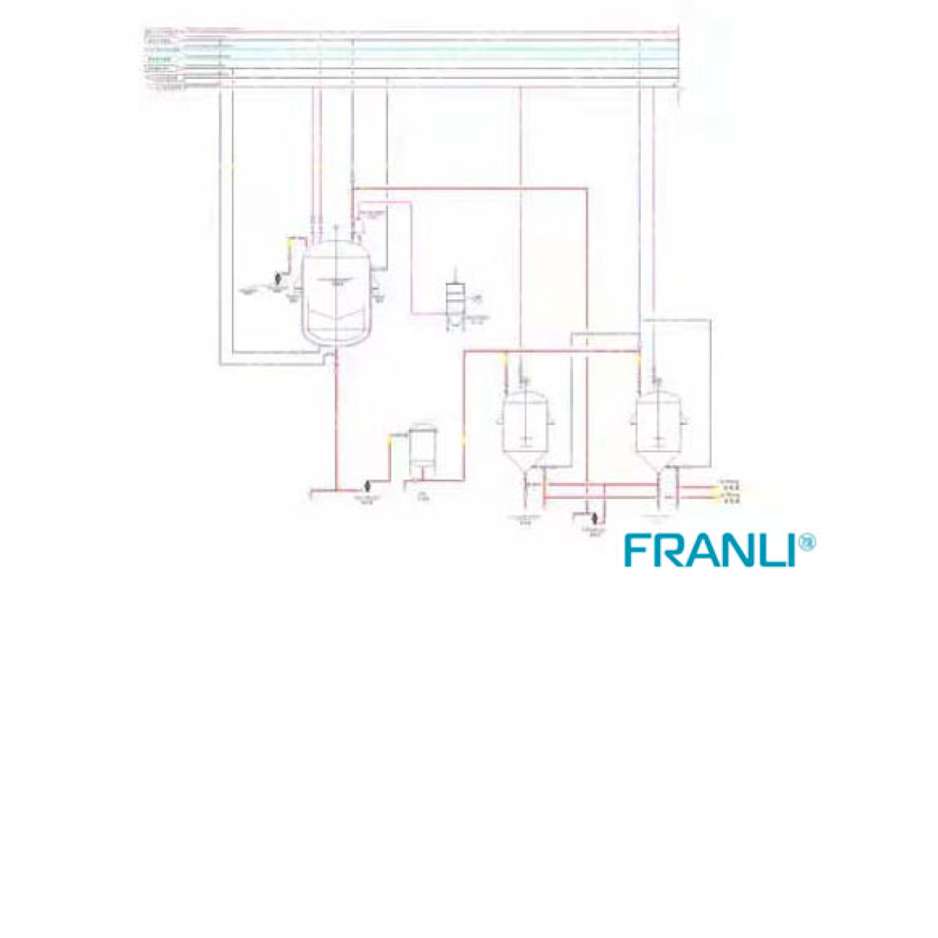
EW-pesticide line
The EW production line mainly mixes raw materials, solvents, and emulsifiers through a reactor (oil-based).
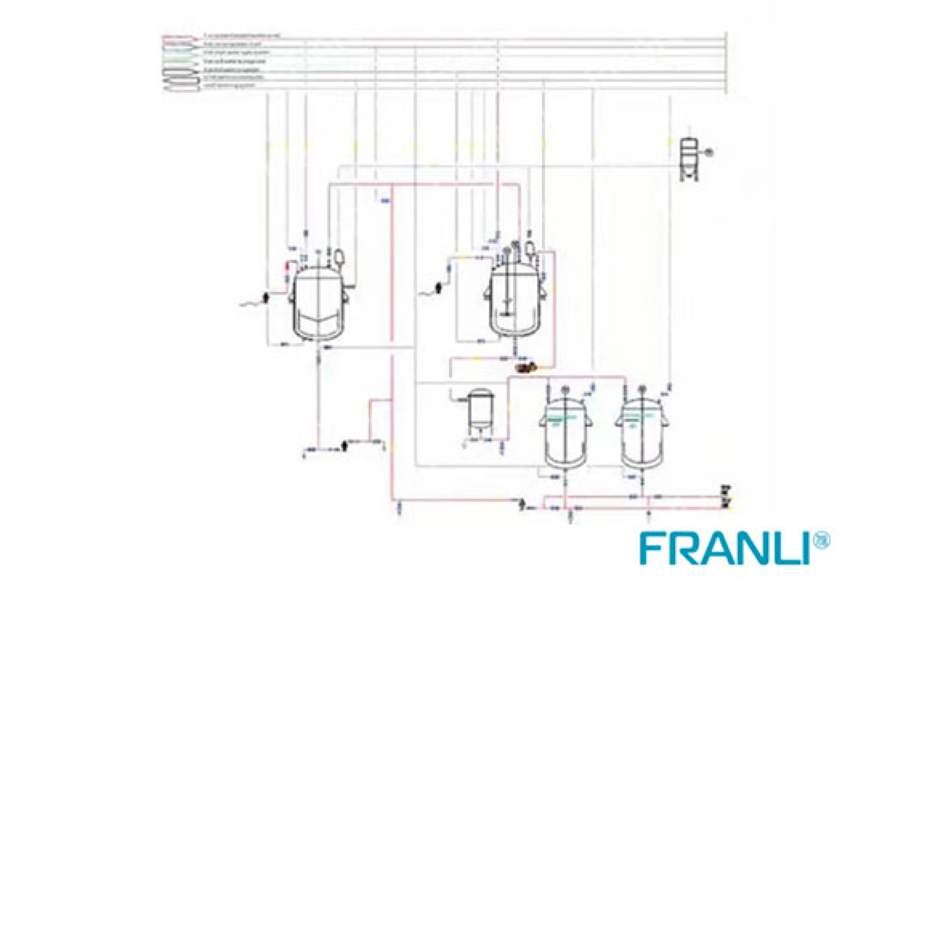
SL_EC pesticide line
The EC production line is mainly composed of an agitator mixer, bag filter, filling machine, etc.
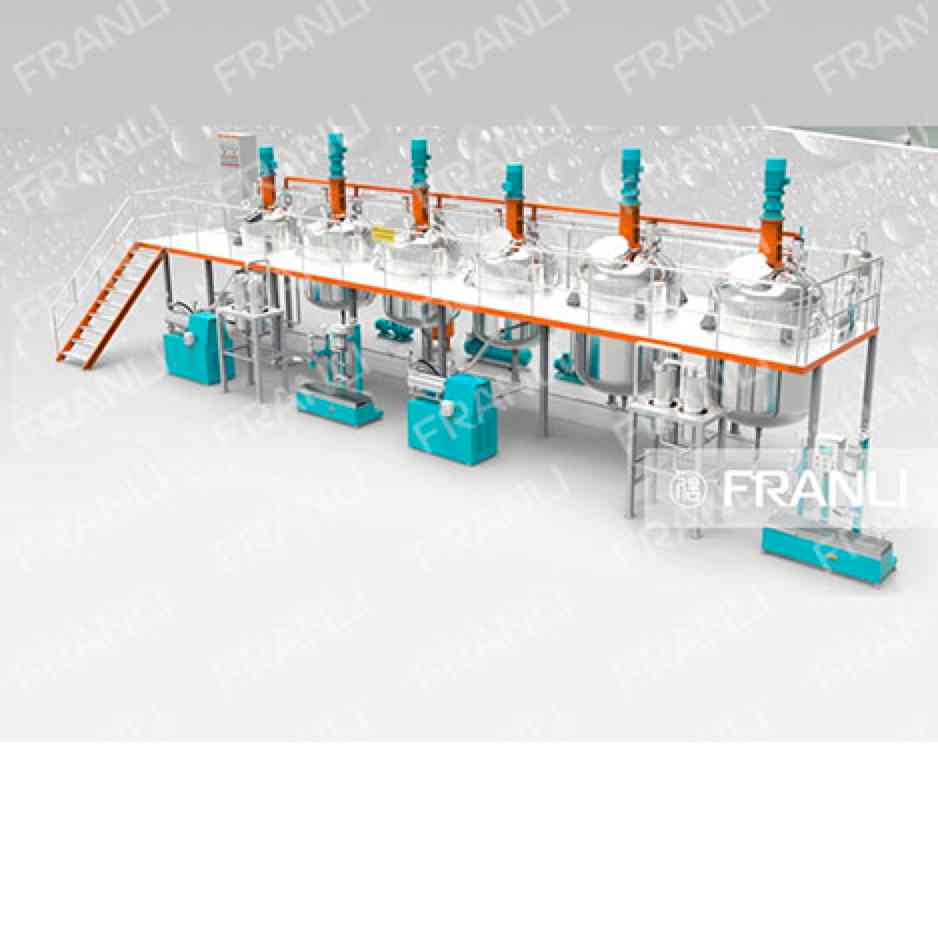
Automotive Paint machine line
The automotive paint machine line is mainly for the production and grinding of automotive paint, Automotive paint has many layers, such as Primer/electrophoretic layer, Medium coat, Colored coat, and Clearcoat.
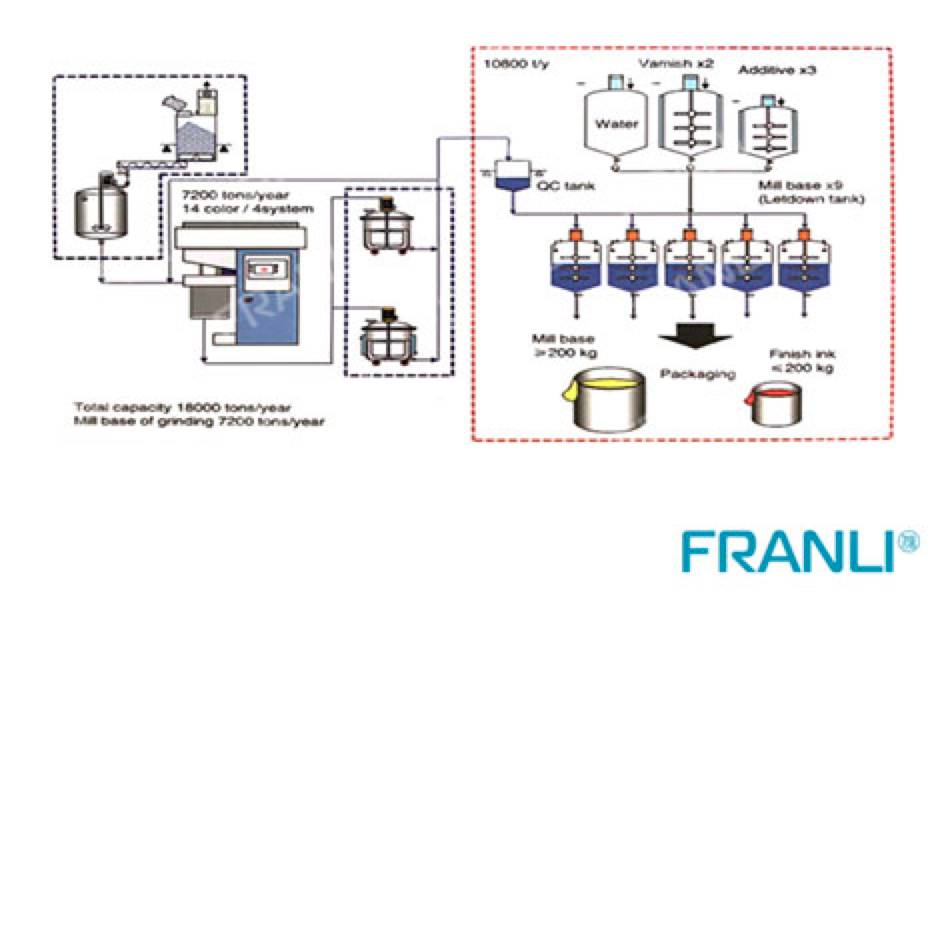
Digital Ink machine line
Franli has professional experience for digital ink machine line, we offered hundreds customers to expand production, or build up new project.