Sand Mill Machine|Sand Mill For Paint
The sand mill machine is a wet superfine grinding equipment, which is developed from the ball mill and is widely used in the production process of superfine powder (sub-micron powder). sand mill machines have different classification methods: according to the structure and shape of the mixing shaft, it can be divided into disc type, rod type, and rod-disc type (that is, bump type). According to the layout of the grinding cylinder, it can be divided into vertical and horizontal. According to the volume of the cylinder, it can be divided into the laboratory, small, medium, large, and super large.
Advantages of sand mill:
- low grinding fineness
- Wide range of applications
- high working efficiency
Application

Coating

Cosmetic

Battery

Graphite

Agrochemistry

Adhesives
Frequently Asked Questions
Many factories and enterprises spent tens of thousands of yuan to buy a sand mill for paint. After using it for less than two months, various problems occurred in the sand mill. The rotors and stators have been worn so badly that many types of equipment are almost paralyzed and can no longer be used. What is the reason for this? How to buy a machine with the most cost-effectiveness?
The standard for judging the quality of a sand mill generally starts from two aspects:
- The material used in the manufacture of the sand mill.
- The manufacturer’s process for producing the sand mill.
how to judge the quality of the material?
First of all, we have to manufacture the sand mill under normal use, but the sand mill is still largely damaged. The main reason for the lack of wear resistance must be the material problem of the machine:
l In order to reduce the cost and sales price of the machine, the manufacturer of the sand mill generally chooses low-grade raw materials, so it is also very important to choose a high-quality sand mill manufacturer.
l For the same material, the processing technology is different, and the hardness of the sand mill will be different, whether it is high wear-resistant alloy steel or polymer, cemented carbide, polyurethane, and ceramics. But not all high wear-resistant alloy steels, cemented carbides, polyurethanes, and ceramics are created equal. Under normal circumstances, the higher the processing cost, the better the quality.
The quality of the material is generally difficult to judge accurately by intuition. But we also can’t do destructive testing. Under normal circumstances, a test machine can be judged immediately. For example, discoloration when grinding white, and when grinding those special raw materials such as carbon black iron-red titanium cyan blue, the fineness does not meet the requirements, and the gloss is not good. This is because the originally selected sand mill and the materials you are grinding are not reasonable. According to the viscosity, hardness, color, and fineness of the grinding materials, different grinding inner barrels, grinding media, and zirconium bead diameters should be selected.
The cost price of high-quality materials is definitely much higher, so the price of the whole machine should also increase a lot. Relatively speaking: the higher the price, the better the quality of the machine! So, will the price of domestic machines and the quality of imported machines be just a slogan? no! In addition to process improvement, there is one more important point – the essential difference between high-quality domestic machines and imported machines! That is the material of the grinding inner barrel and the grinding medium, the complexity of the grinding structure, the sealing method, the size of the motor and the quality of the motor, etc.
If the material is not good enough, the following problems often occur:
- The fineness is not enough
- The gloss is not bright enough
- Easy to change color
- The purity of the finished product is not enough
- Reduced efficiency
- Increase energy consumption
Of course, when choosing the material of the grinding medium and the grinding inner barrel, you should actually provide you with the material of the grinding medium and the material of the grinding inner barrel according to the viscosity, hardness, required fineness, and chromaticity of the grinding material, etc. Choose the best sander for you
For example, the advantage of alloy steel is that the price is relatively cheap, but it may have a certain impact on the color of the material. For example, polyurethane is soft and hard. If your material has a high hardness and can be adapted to work at high temperatures, then polyurethane can be very It is suitable for your choice, which can greatly reduce the wear on the inner barrel and sand grinding disc of the sand mill, and greatly improve the service life of the sand mill.
If the only disadvantage of the higher-end silicon carbide grinding inner barrel is fear of freezing and expansion, that is, if you forget to put water in winter, the inner barrel will freeze and crack.
The material of ceramics is expensive but has a wide range of applications, which does not affect the grinding quality, including grinding fineness, whiteness, wear, etc. so the so-called “what you pay for what you pay for” is essentially the difference between these materials. Unless you’re producing very low-end paint and paint products and you don’t plan to produce good quality paint in the short term, it’s still a good idea to get it right the first time!
Sand mill is one of the key pieces of equipment for fine material preparation. It is also called bead mill or ball mill. It is also called agitated ball mill (a combination of agitating shaft ball mill) abroad.
In principle, sand mills, ball mills, and mixers all use the grinding medium to give it enough kinetic energy under the action of the high-speed rotation of the dispersing blades, so that the impact and extrusion between the grinding medium and the grinding material will generate shear force. To the grinding effect. With the high-performance cooling system and automatic control system, the sand mill can realize continuous processing and continuous discharging of materials, which can greatly improve production efficiency.
There are many types of sand mills, and they have gone through different stages of development from birth to maturity. With the continuous iterative innovation of technology, grinding equipment with different styles and principles have gradually appeared on the market to meet different production needs.
According to the layout of the grinding drum, it can be divided into vertical sand mills and horizontal sand mills. These are two very common styles. Next, we will learn more about the characteristics, advantages, and working principles of the two sand mills.
The vertical sand mill is mainly composed of a feed system, grinding drum, grinding disc, transmission, and electric control system.
Working principle of vertical sand mill
When the vertical sand mill is working, most of the grinding cylinder is filled with grinding media, which is made of ceramics or special materials, and the shape is spherical particles of different sizes. Add the material from the bottom of the vertical silo and mix it with the grinding medium. The stirring shaft is driven by the transmission system to stir the mixture of materials and media at an appropriate speed. Due to the friction and collision between the grinding media, the material is ground, and after a certain residence time, a slurry with a particle size distribution meeting the requirements is obtained.
The horizontal sand mill mainly has the following components: machine base, main shaft components, grinding device, cooling device, control system, auxiliary device, etc. It is a continuous production ultrafine grinding and dispersing machine with a horizontal cylinder, which is widely used It is used for grinding fluid slurry in paint, coating, ink, electronics, ceramic materials, and other industries.
Horizontal sand mill working principle
The horizontal sand mill uses a material pump to feed the solid-liquid phase mixture that has been pre-dispersed and wetted by the mixer into the cylinder. The material and the grinding medium in the cylinder are stirred by a high-speed rotating disperser so that The solid particles and the grinding media produce stronger collision, friction, and shearing effects with each other to achieve the purpose of accelerating the grinding of fine particles and dispersing aggregates. After grinding and dispersing, the material passes through a dynamic separator to separate the grinding media and flows out of the discharge pipe. The horizontal sand mill is especially suitable for dispersing and grinding products with high viscosity and fine particle size requirements.
Vertical sand mill VS horizontal sand mill
The application of sand mills in the industrial field is becoming more and more extensive, and people’s research on them is becoming more and more in-depth. Whether it is a vertical sand mill or a horizontal sand mill, its structure is constantly being improved, and only by understanding the characteristics of the two pieces of equipment can we choose a cost-efficient product that meets the production requirements according to the needs.
Manufacturing difficulty
From the perspective of manufacturing difficulty, the vertical sand mill does not require the use of mechanical seals, so it is easier to manufacture and the manufacturing cost is correspondingly lower.
Material
In terms of materials, vertical sand mills generally use ordinary materials, while horizontal sand mills generally use tungsten carbide metal materials with better materials.
In terms of manufacturing difficulty and manufacturing cost, vertical sand mills have more advantages. In addition, the vertical sand mill does not take up space, and the operation is very convenient, which is suitable for materials with various viscosities. If you have a small budget or do not have high requirements for the fineness of the material, the vertical sand mill will be a very cost-effective choice.
Compared with the vertical sand mill, the horizontal sand mill has a relatively high price, but its advantages are also obvious.
Grinding fineness
From the perspective of grinding fineness, the grinding effect of horizontal sand mills is often better, which can meet the fineness requirements of the product. This difference is limited by the structure of the vertical sand mill.
The grinding medium (beads) in the vertical sand mill is affected by gravity and tends to accumulate to the bottom of the grinding cavity, resulting in a less uniform particle size distribution of the ground material, resulting in a better grinding effect at the bottom than at the top. This is like a bucket of stones, the stones on the bottom of the bucket are ground finer than those on the top of the bucket.
The horizontal sand mill can well overcome the influence of gravity on the medium. Because the feed of the horizontal sand mill is generally from the left to the right, the grinding force of the material in the barrel is the same, the particle size distribution of the output material will be more uniform, and the grinding fineness is generally up to 1μm.
The cost
When shutting down, the grinding media (beads) of the vertical sand mill gather at the bottom of the grinding chamber. When the machine is turned on, the blades will have strong friction with the beads. Because the grinding beads are too concentrated, it is very easy to break the beads. The horizontal type has a lower probability of such a situation.
Scope of application
Vertical sand mills are more suitable for manufacturing products that require relatively low product requirements but require high output. A horizontal sand mill is suitable for some grinding products with higher precision and fineness.
At present, sand mills are developing in the direction of large batches, refinement, high purity, and low energy consumption. Equipment maintenance is the key to extending the life of mechanical products, and it is also related to the stability and efficiency of production. Understand the common faults of sand mills and their solutions to reduce production losses caused by unnecessary equipment downtime.
Hot sale sand mill(Bead mill)
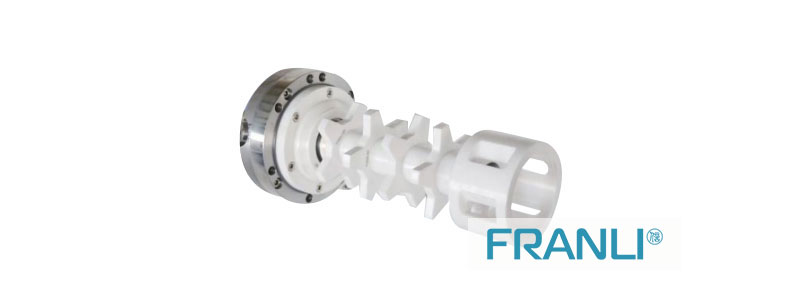
• Easy installation of the bead mill machine: The best features of this bead mill machine are: You can easily install it wherever you want. This task is so simple, and effortless. And due to this feature, it is extremely popular among other equipment. You can find the bead mill working principle so effective, and you can perform all the mixing tasks effectively without adding so much effort. As this machine is very bulky and cheap, it needs only a few minutes to install. In this way, you can reduce the labor charges and other exhausting jobs. So, you can stay worry-free about how to install this machine? As the company has made this task easier for you.
• Efficient work performance of this bead mill machine: As we know, the bead mill working principle has been created in such a way that you can achieve higher and efficient work performance on this bead mill machine. If you are looking for quality and stable work, these bead mill machines are the best option to get a consistent mixture of any particular material. You can use this bead mill for paint, ink, and coating industries. And, it is a comfortable and easy method to perform all the mixing and dispersing activities without wasting so much time. So, here bead mill working process is so necessary to obtain the desired results for the company.
• Contains grinding media of 2-3 mm size: It is the necessary feature of the bead mill working process as it includes the grinding media. In this area, grinding and other dispersing activities take place that they turn into a fine mixture. You can use a bead mill for paint, ink, and coating industries, where mixing works have been done regularly. It contains grinding media of 2-3 mm size that is enough to transform all the material to a smooth and fine paste. For this purpose, bead mill manufacturers have added advanced technology to this machine to provide consistent and quality work performances for the company. In this way, you can get a higher productivity ratio. And you can reach the peak of the higher conversion rate. Thus, these bead mill machines are ideal for fabrication companies to get their desired goals with full efficacy.
• Easy operation of the bead mill machine: It is a great feature of this SMP Agitator bead mill machine as bead mill manufacturers create this bead mill machine with advanced technology. And, with this quality, the operation of this sand grinding mill is extremely comfortable. You do not need to call any professional to do the same, and you can do it yourself without adding so much effort. So, it is another best feature to consider about this bead mill machine.
• Easy to clean the bead mill machine: This sand grinding mill is remarkably best for the fabrication companies to enhance the overall growth and production. As we know, while we use any bead mill machine, we need to clean it so that we can get hygienic work performance. For this purpose, companies manufacture this bead mill machine in a way that you can clean it comfortably without making yourself exhausted. You can go through the bead mill pdf and other relative documents that provide you the guidelines of clean this bead mill machine.
• Easy to maintain the bead mill machine: Maintaining is also a matter of concern as it requires your time and money. For this purpose, you can check the bead mill pdf and manual provided by the company at the time of purchase. You can either contact the company or read the manual carefully to know all the information about the bead mill machine. And, you can find this process is extremely simple to perform. So, you can get this bead mill machine without spending so many amounts on it. And, in this way you can concentrate on the work performance of the company.
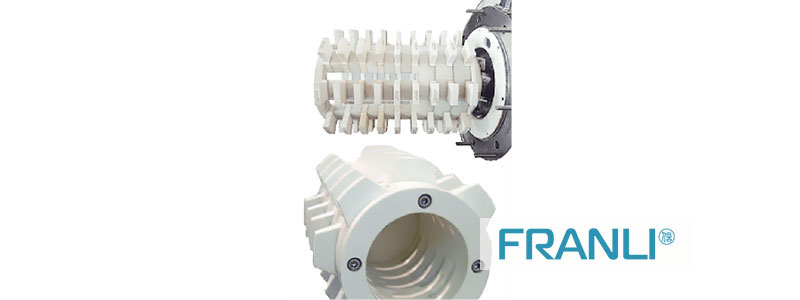
Also, you can use SMP Agitator bead mill in paint industry, ink, and other coating work companies to make all the mixing and grinding activities easier and more manageable. To get this bead mill machine, you search for those companies that deal in these machines and other equipment. For this purpose, you can get a quote or related other information about the bead mill machine.
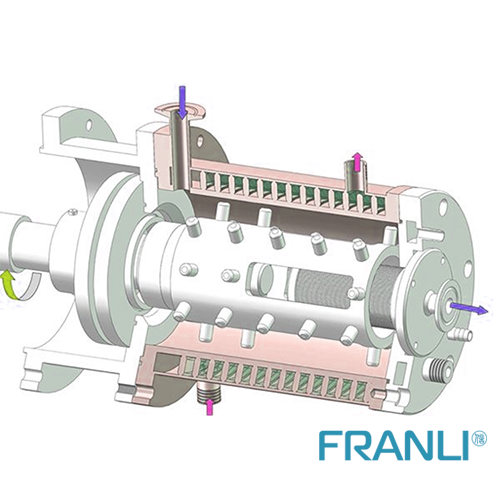
Hydraulic TRH type
Hydraulic Three Roll Mill, which is a full hydraulic auto-controlling system equipment. 1- Cooling system: an individual cooling system for each roller. 2- hydraulic control: hydraulic control pressure blades, roller gaps, etc. 3- Optional installation:PLC system with SIEMENS touching screen, FRANLI engineer set formulas of grinding according to different viscosity materials.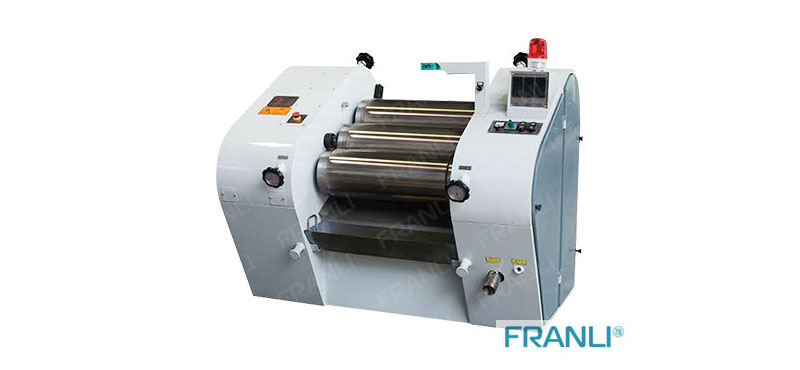
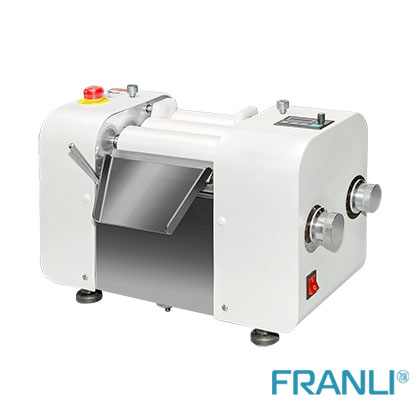
Vertical type for Grinding Powder
Also, we have a vertical three-roll mill for grinding powder and chocolate. We have 3 rollers, 4 rollers, and even 5 rollers, which are all vertical types. We export to the soap industry and chocolate companies.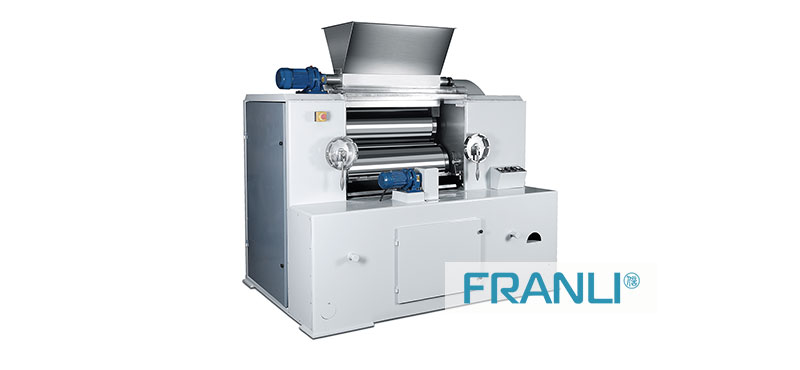
Heating type
Franli also offers a heating hydraulic three roll mill for rubber, EVA, PVS, and color masterbatch. As this type of machine grinds high viscosity material, we specially design the gear quality. This type is been Heated by oil or steam. Franli three roll mill machine are full automatic PLC controlling, hydraulic system, stable operation, reliable quality. We choose the international brand parts. Standrad parts, ABB VFD, Siemens Motor, SKF or NSK bearings, SEW or Nord reducer. A roller is 45-55mm thickness of metal, cast steel. You can widely choose ceramic, alloy, granite rollers for your material. If you have several formulas of material, we can set up formulas in the PLC system, your workers only need to choose numbers on touching the screen, don’t need to waste time to adjust the rollers’ gap or the pressure of the blade.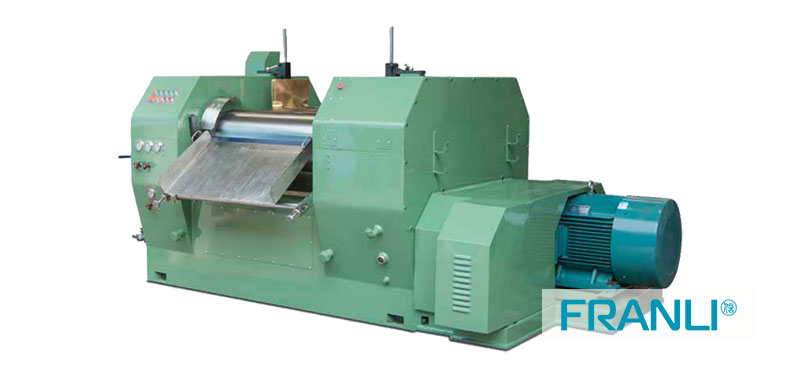
Related production lines
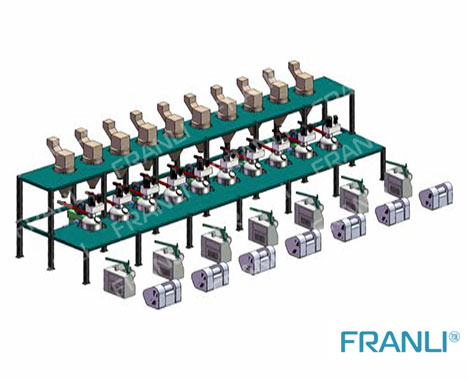
Offset Ink machine line
FRANLI is specialized in offset ink full line production for 20+ years. Helped customer save the cost, save the man power, also save the space.
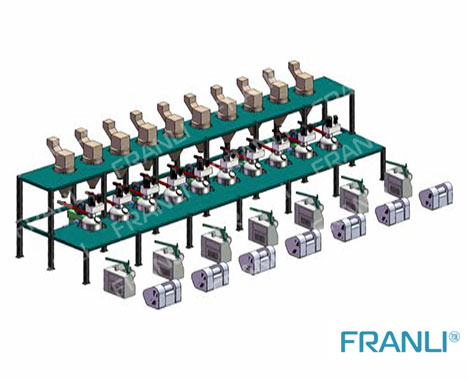
Offset Ink machine line
FRANLI is specialized in offset ink full line production for 20+ years. Helped customer save the cost, save the man power, also save the space.
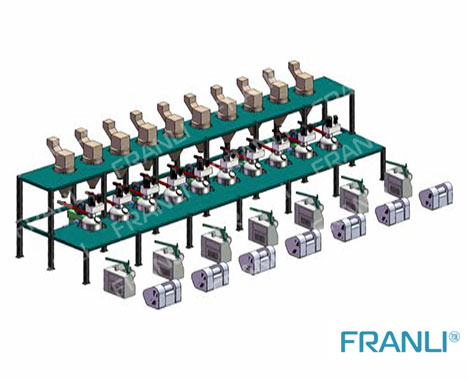
Offset Ink machine line
FRANLI is specialized in offset ink full line production for 20+ years. Helped customer save the cost, save the man power, also save the space.
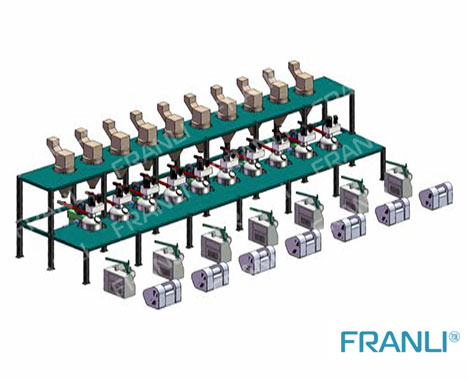
Offset Ink machine line
FRANLI is specialized in offset ink full line production for 20+ years. Helped customer save the cost, save the man power, also save the space.
Guidelines For Sand Mill
The sand mill machine adopts the eccentric disc grinding structure and is arranged in a certain order. This system overcomes the shortcomings of the uneven distribution of the grinding media of the traditional grinding machine so that the grinding media can get the maximum energy transfer and the grinding efficiency is high.
The sand mill machine adopts a double end face with a forced cooling mechanical seal, which has a good sealing effect and reliable operation. The separation system adopts a large-flow LDC dynamic grating-slit separator. Under large-flow conditions, the discharge port will not be blocked, and the flow area is large. The gap range is 0.05-2.0mm, so the grinding media of the sand mill machine can be more than 0.1mm.
The sand mill machine adopts disc type or pin type, closed cavity design, and the grinding disc is installed on the stirring shaft in a certain order, which overcomes the shortcomings of uneven distribution of grinding media and poor particle size distribution after grinding in traditional horizontal sand mill machines. The material enters the grinding chamber under the action of the feed pump. The inlet is designed at one end of the drive connection flange. The flow direction of the material is opposite to the bottom end of the mechanical bearing, which greatly reduces the pressure on the mechanical seal and prolongs its service life. In the high-speed operation of the eccentric disk of the stirring shaft, the mixture of the material and the grinding medium undergoes high-efficiency relative movement. As a result, the solid particles of the material are effectively dispersed, sheared, and ground and the final product is obtained after the dynamic large-flow rotor gap separation filter. Depending on the product grinding process, the sand mill machine can adopt independent batch cyclic grinding and tandem grinding processes.
Agitator sand mill machine with the horizontal grinding chamber for continuous dispersion and fine wet-milling of semi-liquid to highly viscous, pumpable products.
The sand mill machine output depends on the product and the required fineness and lies between 100 -700kg/h.
The necessary energy for dispersion and grinding is transmitted to the grinding beads via easily exchangeable agitator discs mounted on an agitator shaft. The material to be milled is constantly fed into the sand mill machine by a separate product pump.
A dynamic gap separator retains the grinding beads inside the sand mill machine. which efficiency is determined by the energy input to the grinding chamber and the optimal exploitation of this energy for the dispersion and grinding process. Because of its optimal geometry, the grinding chamber of the sand mill machine achieves a high degree of efficiency.
Related production lines
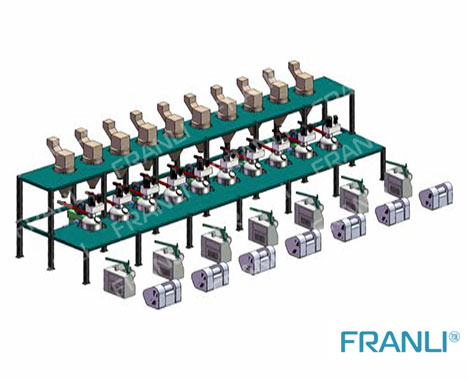
Offset Ink machine line
FRANLI is specialized in offset ink full line production for 20+ years. Helped customer save the cost, save the man power, also save the space.
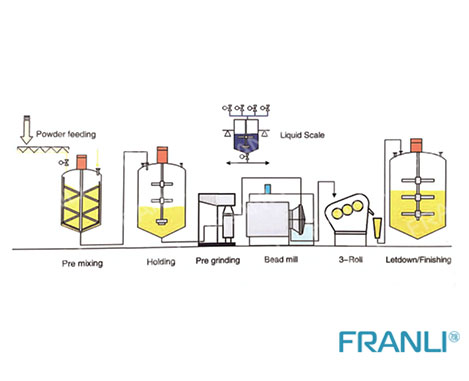
Offset Ink, UV Ink machine line
The FRANLI engineering company, offer the full set of UV INK Production Line, we can make the full drawing according with your factory size, formulas, weather and safety system.
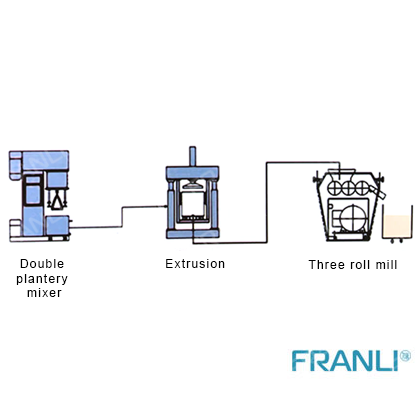
PCB INK Machine line
FRANLI supplies all equipments for the production of PCB inks, from the powder feeding station to the filling part.
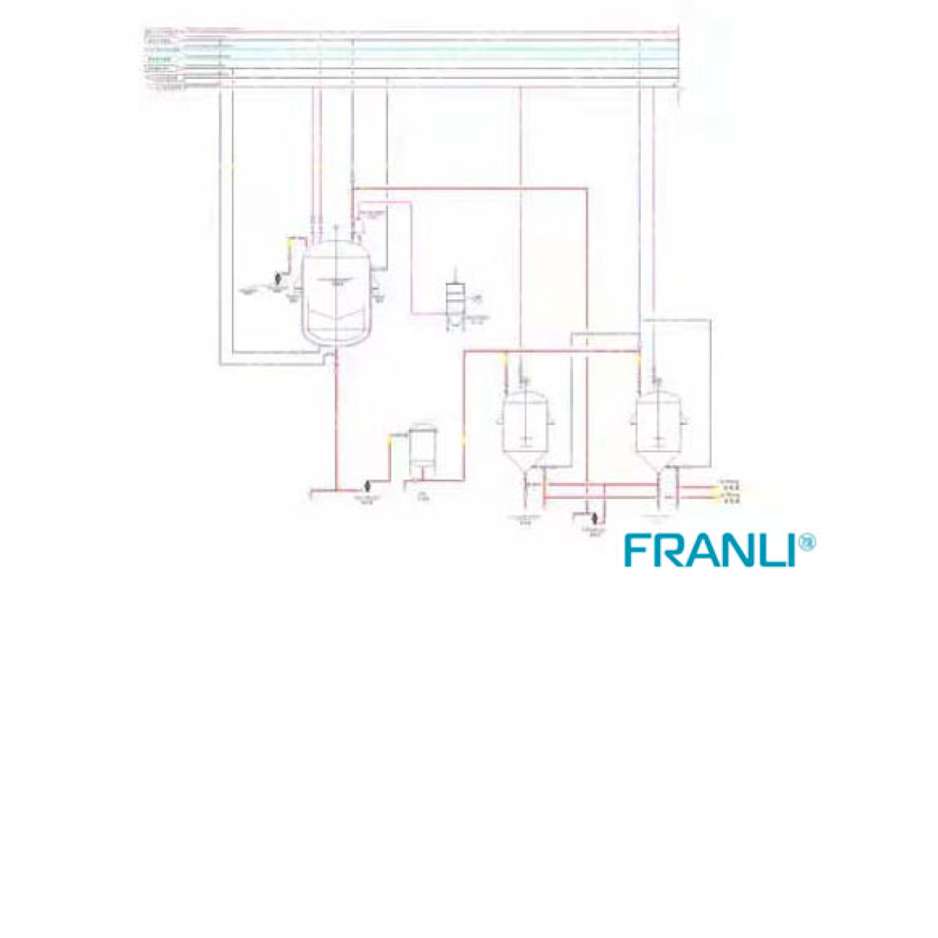
EW-pesticide line
The EW production line mainly mixes raw materials, solvents, and emulsifiers through a reactor (oil-based).
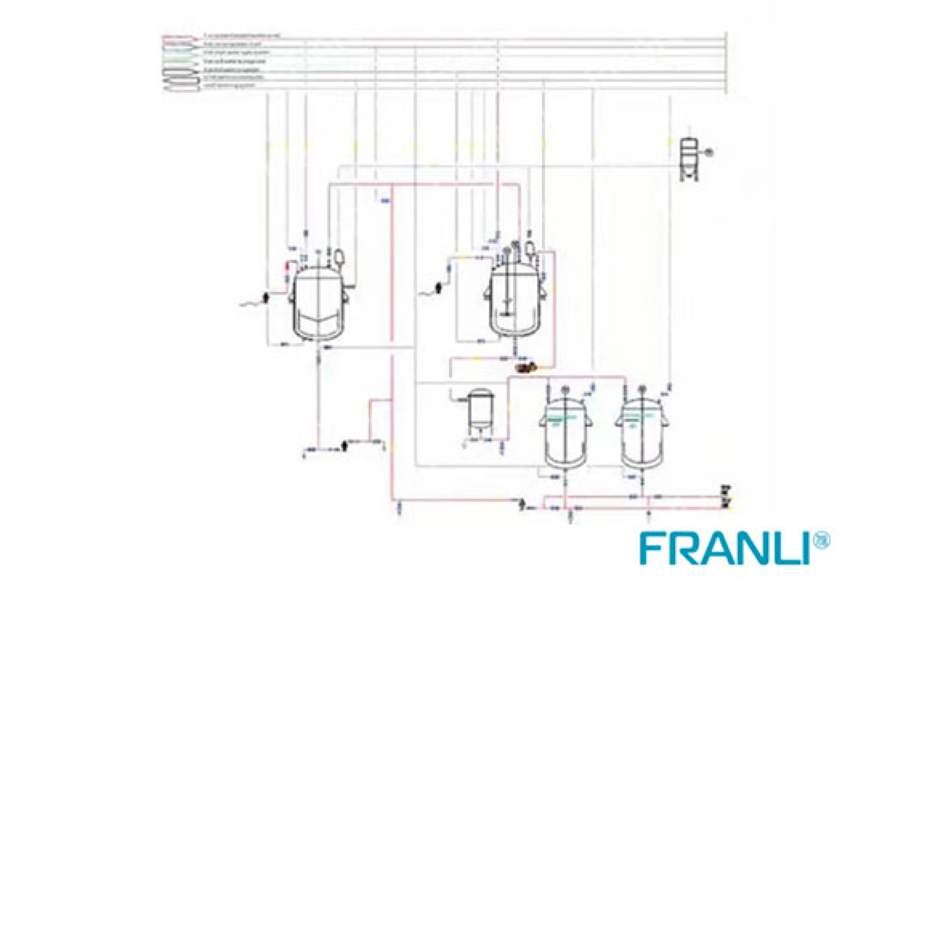
SL_EC pesticide line
The EC production line is mainly composed of an agitator mixer, bag filter, filling machine, etc.
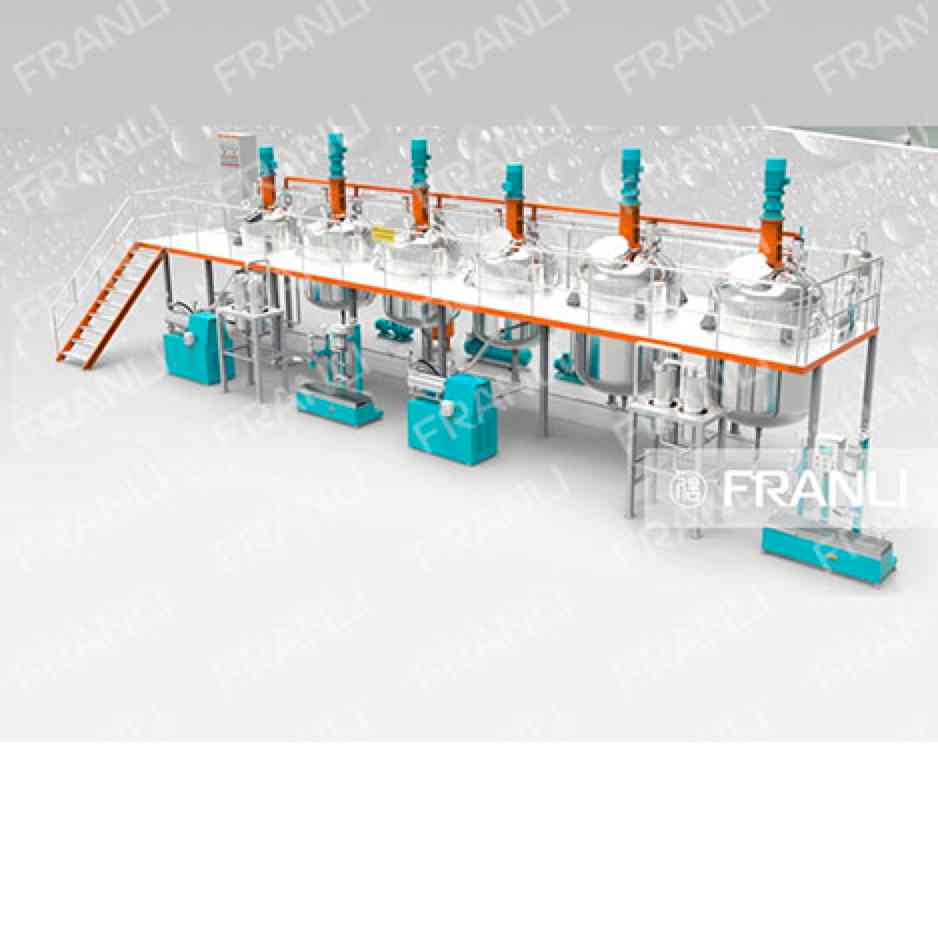
Automotive Paint machine line
The automotive paint machine line is mainly for the production and grinding of automotive paint, Automotive paint has many layers, such as Primer/electrophoretic layer, Medium coat, Colored coat, and Clearcoat.
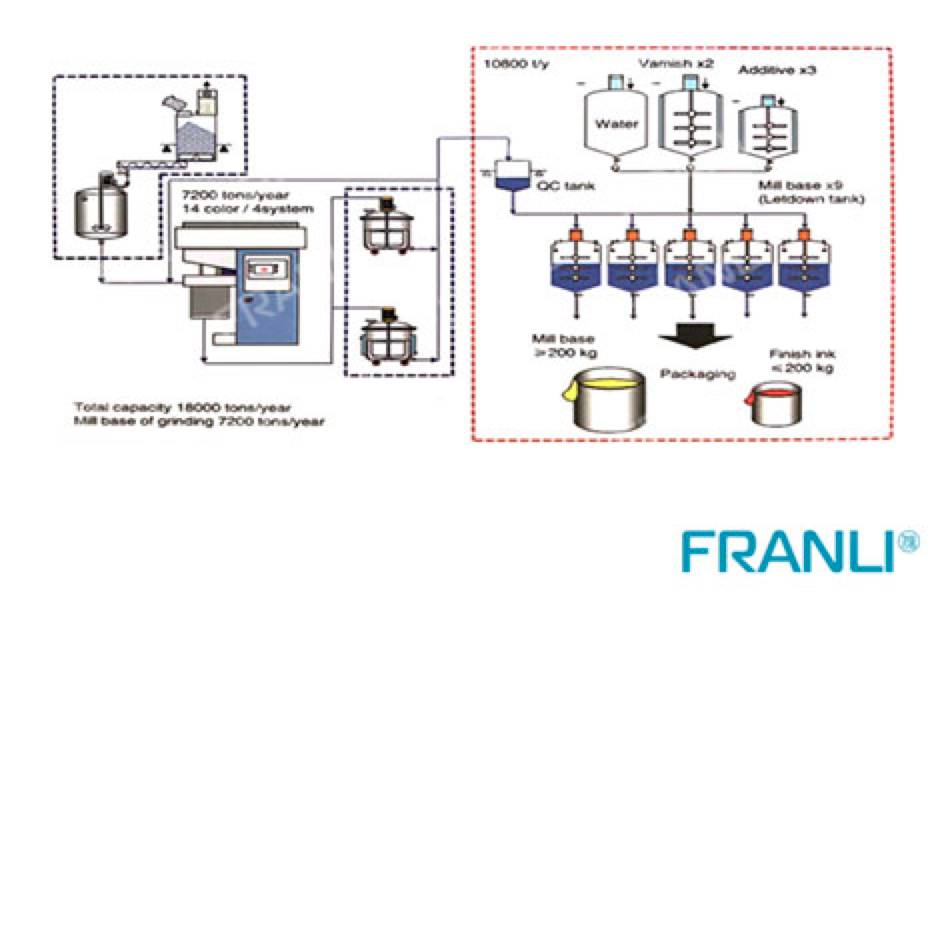
Digital Ink machine line
Franli has professional experience for digital ink machine line, we offered hundreds customers to expand production, or build up new project.