Horizontal sand mill
The horizontal sand mill adopts a cyclic grinding process, and according to European advanced design standards, FRANLI’s horizontal sand mill has the characteristics of better control ability, high energy conversion rate, and large flow rate, which can achieve nano-level grinding requirements. The range of particle size distribution is narrow. Widely used in gravure inks, automotive coatings, coil coatings, ceramics, inks, inkjets, color filter separators, functional ceramics, lithium battery materials, thermal paper, anti-corrosion coatings, wood coatings, etc., covering a wide range of fields, Can almost meet all needs of nano-scale wet grinding.
Advantages of horizontal sand mill:
- low grinding fineness
- Wide range of applications
- high working efficiency
Application

Coating

Cosmetic

Battery

Graphite

Agrochemistry

Adhesives
Hot sale sand mill(Bead mill)
Guidelines For Sand Mill
The sand mill machine adopts the eccentric disc grinding structure and is arranged in a certain order. This system overcomes the shortcomings of the uneven distribution of the grinding media of the traditional grinding machine so that the grinding media can get the maximum energy transfer and the grinding efficiency is high.
FRANLI Machinery keeps improving according to the needs of different industries. This horizontal sand mill can not only improve efficiency and reduce labor but also has made outstanding achievements in environmental protection. The adjustable dynamic separator used is made of high wear-resistant powder alloy, which has the characteristics of self-cleaning and adjustable gaps. Users can choose 0.1mm grinding media, which creates effective conditions for the grinding effect of the product.
The working process of the FRANLI horizontal sand mill
Under normal circumstances, we need to configure the original slurry first, after a simple grinding, pump it into the circulating mixing tank, and transport it through the bottom pump into the horizontal sand mill. The material enters the circulation while being ground by the sand mill. The tank and the unground materials are quickly stirred and mixed under the action of the mixer, and then pumped into the sand mill through the bottom again. After multiple cycles, the final effect that the user wants to achieve is achieved. The volume of the tank can reach 1/4 of the flow rate of the sand mill.
Advantages and characteristics of horizontal sand mill
- The horizontal sand mill adopts a brand-new static centrifugal separation device, which has a large flow rate to ensure smooth and stable discharge.
- Completely realize the nano-level grinding effect, and can use the grinding medium of 0.1mm or more.
- According to different products, different materials can be selected, such as silicon carbide, zirconia, polyurethane, cemented carbide, etc.
- The arrangement of the cylinder and the rotor refers to the golden ratio as the standard, which effectively reduces the degree of wear on itself, and on the other hand, it expands the energy utilization rate and achieves the best grinding state.
- The whole machine has been optimized and upgraded many times, and the overall stability of the equipment has been improved.
- Multiple cooling modes can effectively reduce the heat problem caused by grinding.
FRANLI’s new horizontal sand mill has a complete grinding function, and far surpasses the traditional sand mill, raising the wet grinding effect to another level. Our engineers provide 24-hour functional consultation and effect testing and provide formulas for the grinding effect of various materials.
Related production lines
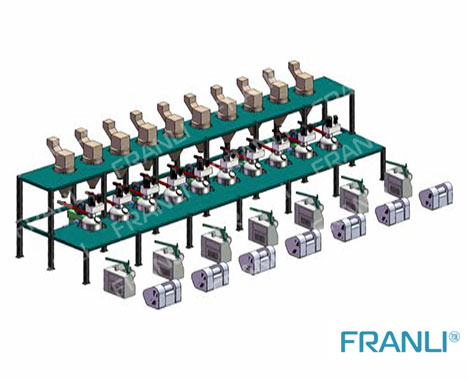
Offset Ink machine line
FRANLI is specialized in offset ink full line production for 20+ years. Helped customer save the cost, save the man power, also save the space.
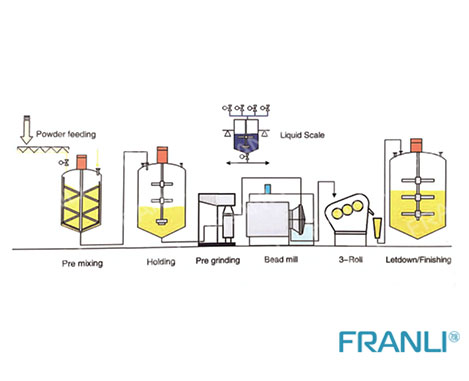
Offset Ink, UV Ink machine line
The FRANLI engineering company, offer the full set of UV INK Production Line, we can make the full drawing according with your factory size, formulas, weather and safety system.
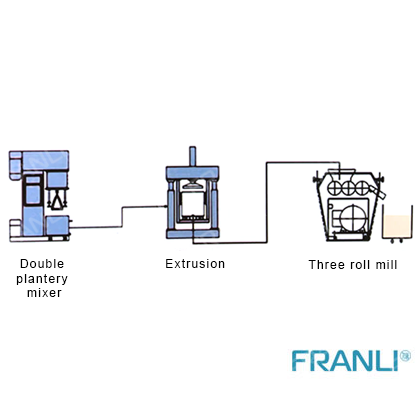
PCB INK Machine line
FRANLI supplies all equipments for the production of PCB inks, from the powder feeding station to the filling part.
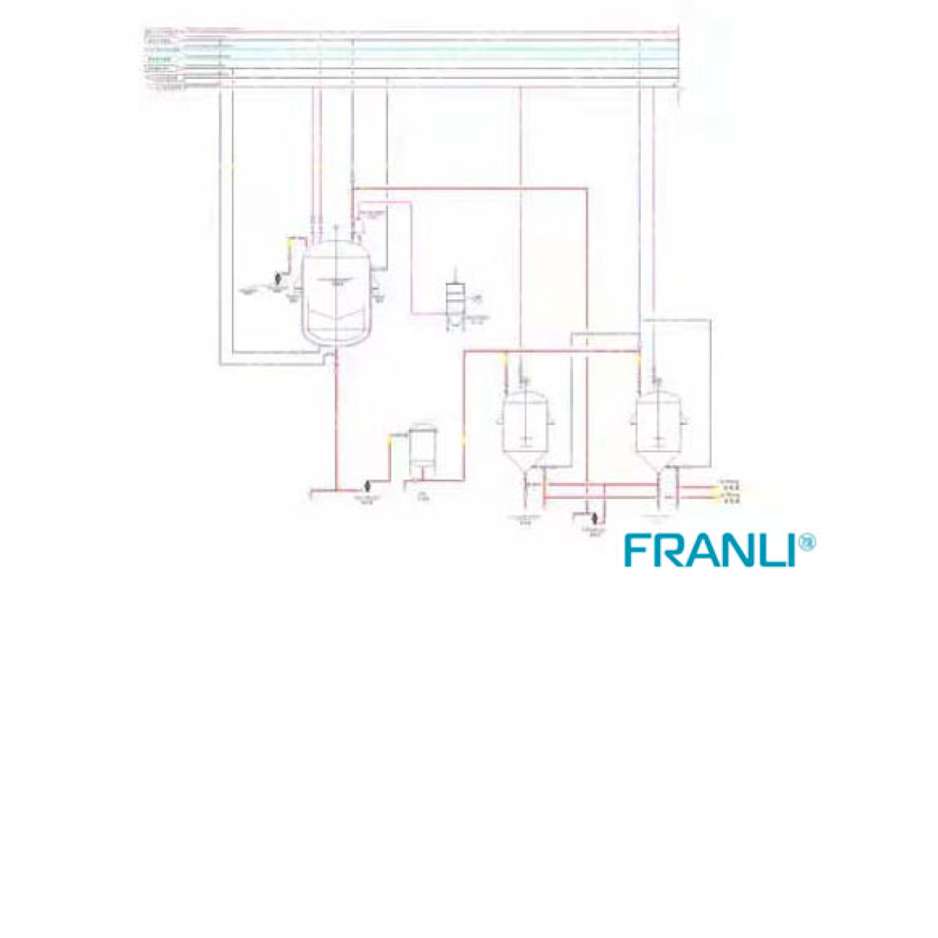
EW-pesticide line
The EW production line mainly mixes raw materials, solvents, and emulsifiers through a reactor (oil-based).
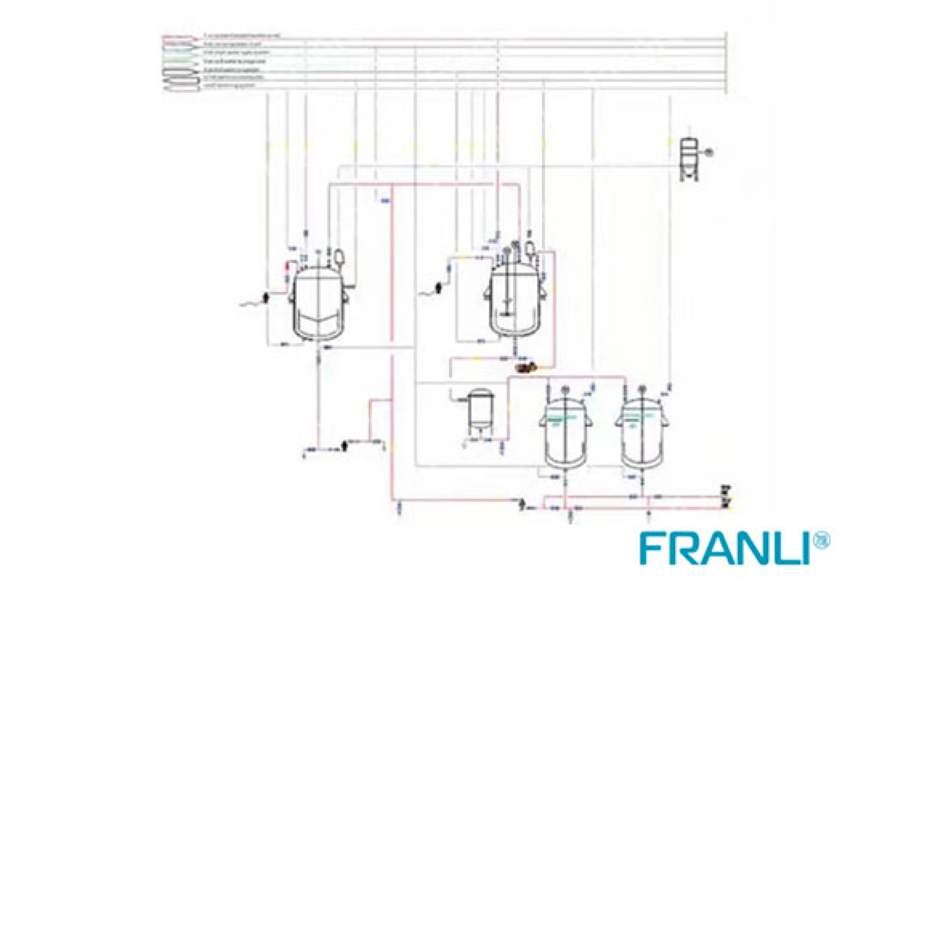
SL_EC pesticide line
The EC production line is mainly composed of an agitator mixer, bag filter, filling machine, etc.
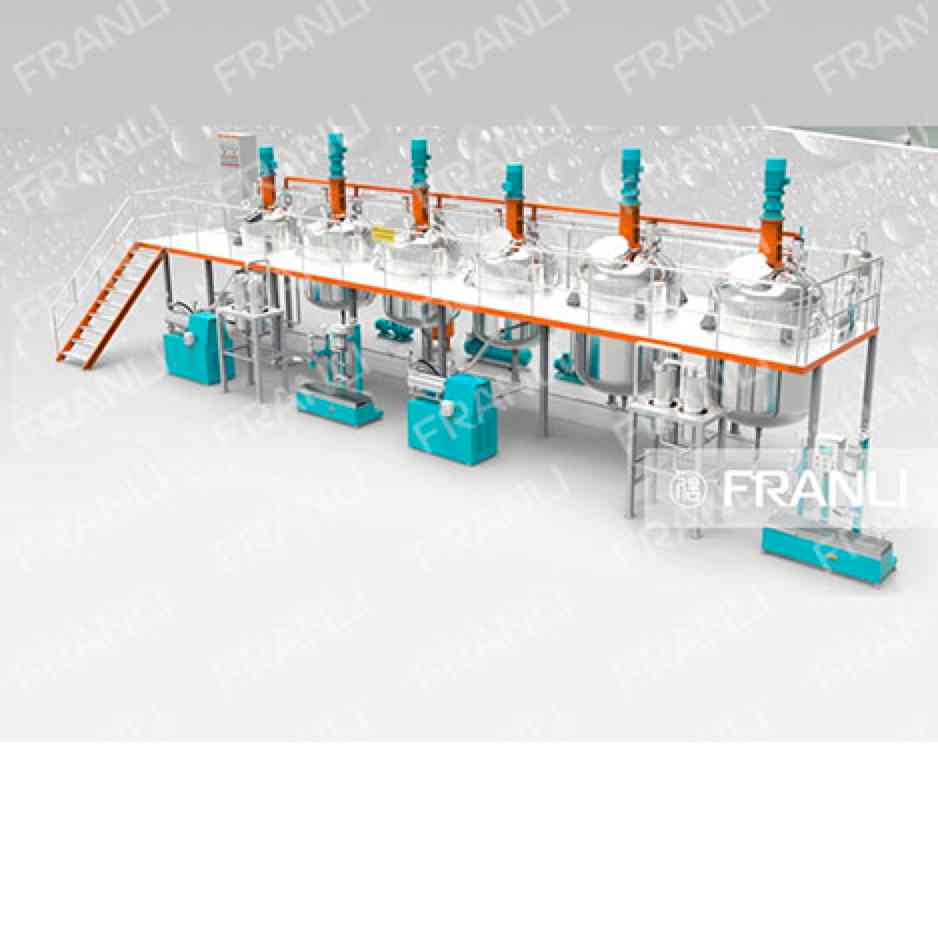
Automotive Paint machine line
The automotive paint machine line is mainly for the production and grinding of automotive paint, Automotive paint has many layers, such as Primer/electrophoretic layer, Medium coat, Colored coat, and Clearcoat.
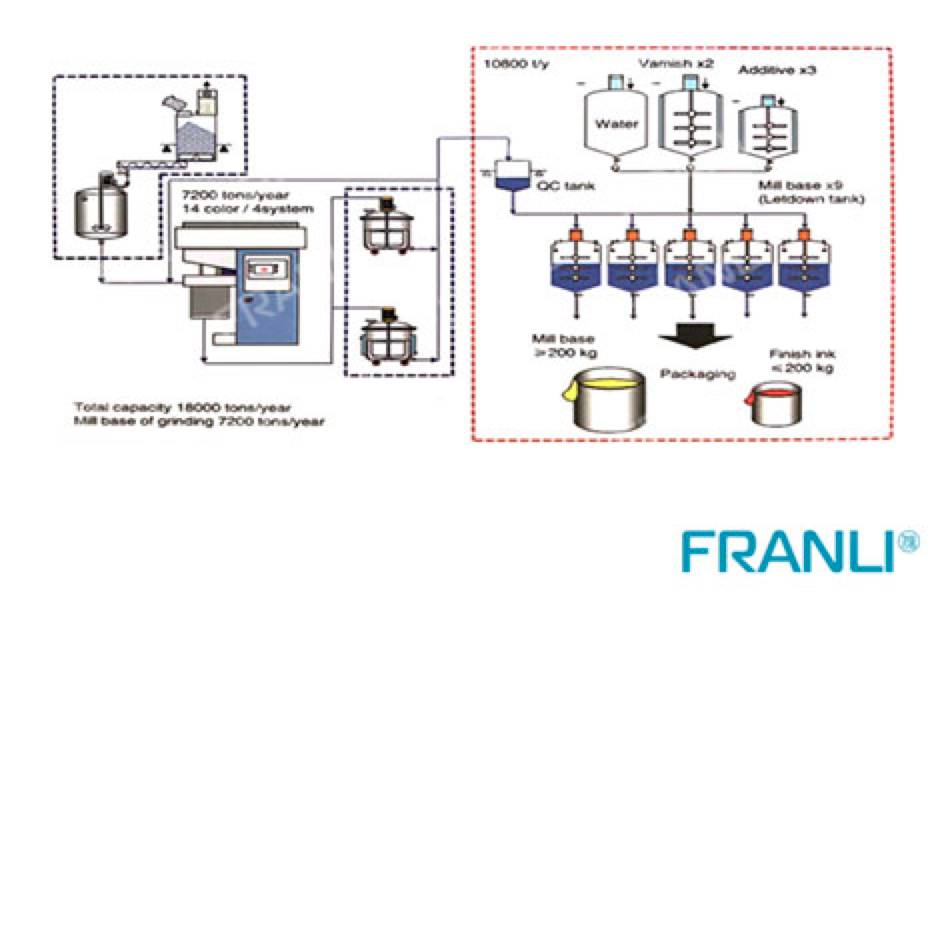
Digital Ink machine line
Franli has professional experience for digital ink machine line, we offered hundreds customers to expand production, or build up new project.