Bead Mill Machine
Bead mill machine is a microscopic and nanotechnology grind and dispersion device. The particulates are ground and/or distributed by the collisions and friction stress of the beading within the bottom chamber, which is agitation by spinning the shafts. The grinding committee’s output features a filtering mechanism that separates beads from grains, allowing for the continued manufacture of small particles while keeping beading within the container. Bead mill machines are among the numerous technologies used throughout the laboratories for milling, neutralising, and homogenising materials. Bead mill machines are commonly sometimes used homogenise materials that are challenging to destabilize using traditional mechanical laboratories. Tumours, hearts, e-coli, yeast, bone, skin, cartilage, spores, seeds, and soil are among the types of samples. Bead mill machines also could recover nucleotide acids that play an important role from complicated microorganisms, including microalgae, mycobacterium, and phytoplankton.
Advantages of bead mill:
- low grinding fineness
- Wide range of applications
- high working efficiency
Application

Coating

Cosmetic

Battery

Graphite

Agrochemistry

Adhesives
Frequently Asked Questions
The bead mill is one of the most advanced and efficient grinding equipment with wide material adaptability. The entire grinding cavity has a narrow space, and the gap between the levers is small. It has the characteristics of intensive grinding energy. It is equipped with a high-performance cooling system and automatic control system. , it can easily realize the long-term processing and continuous discharge of materials. After the continuous upgrading and transformation of franli engineers, the production efficiency of the bead mill can reach twice that of the ordinary bead mill. A bead mill, also known as a sand mill, is mainly used for wet grinding of chemical liquid products, electronic paste, ink, and paint. According to the performance, bead mills can be divided into horizontal bead mills, basket bead mills, vertical bead mills, etc.
The bead mill is mainly composed of the body, the grinding drum, the sanding disc (lever), the grinding medium, the motor, and the feeding pump. The franli bead mill manufacturer sets the function of controlling the speed of the feeding, mainly for the control of the feeding pump, not only that, the grinding media of the bead mill can be of different types. For example, the commonly used grinding media are generally divided into zirconia beads, glass beads, zirconium silicate beads, etc. The grinding effect of different grinding media is also different.
Bead mill design principle:
The bead mill adopts an eccentric disc grinding structure and is arranged in sequence. The system overcomes the disadvantage of uneven distribution of grinding media in traditional grinding machines, enabling the grinding media to obtain large energy transfer and high grinding efficiency. Sealing, good sealing effect, and reliable operation, the separation system adopts a large flow ldc dynamic grid slot separator, the discharge port will not be blocked under large flow conditions, the flow area is up to 0.05-2.0mm, and 0.1 mm can be used. Grinding media above mm.
The franli horizontal bead mill adopts the closed design of the eccentric disc grinding chamber. The grinding discs are installed on the stirring shaft in sequence, which overcomes the disadvantages of uneven distribution of grinding media and poor particle size distribution after grinding in traditional horizontal bead mills. Under the action of the material pump, it enters the grinding chamber. The design of the inlet is at one end of the drive connection flange. The flow direction of the material is opposite to the bottom end of the mechanical bearing, which greatly reduces the pressure on the mechanical seal and prolongs its service life. During the high-speed operation of the eccentric disk, the mixture of the material and the grinding medium move relatively, so that the solid particles of the material are effectively dispersed, sheared, and ground, and after passing through the dynamic large-flow rotor gap separation filter, the product with perfect fineness is obtained. Due to different products, the grinding process has certain differences. The factory can adopt independent batch circular grinding and series grinding processes.
Features of franli bead mills
- The medium distribution in the grinding chamber of the horizontalbead millis uniform, the grinding efficiency is high, the start-up with load is easy, the operation is convenient, and it can be designed to be large. However, the energy density (installed power per unit volume) is low, so the grinding fineness is limited;
- The medium distribution of the verticalbead millis uneven, the grinding efficiency is low, and it is difficult to start with the load. The advantage is that there is no mechanical seal and the structure is simple;
- The horizontal bar grindingbead millhas high energy density, short grinding cylinder, large filtering area of media separator, short material residence time, good heat dissipation effect, high grinding efficiency, and narrow product particle size distribution. Generally used for large flow circulating grinding process of difficult-to-grind materials;
- The vertical barbead millnot only has pins arranged on the stirring shaft but is also often arranged on the inner wall of the cylinder. High energy density and high grinding strength. Mainly used for high viscosity materials, such as offset printing ink, and uv ink production.
Franli is a bead mill manufacturer and supplier with 20+ manufacturing experience. Its bead mills have several invention patents and obtained several certificates, helping factories in dozens of countries to solve the grinding problems and efficiency, if you are looking for a suitable bead mill manufacturer, you can get in touch with franli directly.
The Bead Mill is a machine that mixes beads in a cylindrical vessel to crush, break, and disperse tiny particles in a chamber. The propeller of the mill initiates bead motion, which instigates intense shear force and impact on the particles. Moreover, this machine works best for the dispersion and grinding of particles into nanometer sizes within the chamber. The particles can be discharged either by dry or wet technology. This bead Mill has been modified to grind many materials, including pebbles, ceramic balls and steel balls. It has nanotechnology that crushes and disperses the particles uniformly with the aid of shaft and shear force. The exit of the crushing chamber has a separating structure that aids in the separation of bead particles. We can say the bead mill is the most reliable machine for getting fine production particles.
There are two types of bead mill machines; a dry mill and a wet mill machine. Dry mill machines work by employing a system that releases particles into the air or gas atmosphere. A wet mill machine employs the same system as a dry mill machine but the fine particles are released in a liquid state. These machines are one of the most efficient means of processing fine particles into the micron and nanometer size range. The Bead mill machine can be operated in discrete or continuous mode, depending on the machine design.
Vertical bead mill
This type of bead mill machine is designed for nanoparticle-sized materials, Such as semiconductor material, silicon carbon, inkjet and LCD material. The mill has both high and low viscosity materials. Operating this machine is fast, simple and easy. With an instruction manual, one can maintain it safely. The grinding materials are added to the feeding hole without any complications. The grinding speed is also high and has a dynamic separator at the exit.
This type of bead mill machine has tetragonal zirconium which is made up of micron and sub-micron zirconia and yttrium oxide as raw materials. The mill has been designed to grind beads for ultra-fine grinding and dispersion of zero pollution materials, high viscosity and hard materials. Nano zirconia beads and high purity zirconia beads are the two types. Nano zirconia beads are utilized in high-end materials such as anode and cathode materials for new energy batteries. Paints, electrical paste, coatings, and a variety of other commonly used products contain high purity zirconia particles. This machine is advantageous because it has good roundness and a smooth surface. It is very tough and high impact-resistant, so it cannot easily break during a high-speed operation. It also has a high density, hence an efficient grinding process.
The pearl mill
This machine works with both high and low viscous materials. High viscosity materials are used in the production of offset ink, printing ink, screen printing, and any other high viscous material. Additionally, low viscosity materials are used in the manufacturing of automotive paint, topcoat, and any other low-viscous material. The machine has an advanced cooling system to monitor high-temperature materials. A German-made mechanical seal and NSK bearing are installed to prevent material from leaking. It has the best grinding effect due to the conic grinding and mixing tanks. It also has a self-cleaning and high precision separation ring to filter out beads at the exit end.
The Dyno mill
The dyno mill is mostly used in the ink production industry. The machine operates by grinding, crushing, and dispersing large particles into smaller and uniformly sized particles. The dyno mill machine is easy to run since it is supplied along with guiding manuals.
Agitator mill
The agitator mill machine is commonly applied in the battery sector, ceramic materials, mineral pigments, and medicines. The milling machine has a strong power rotor and a pin in the chamber to facilitate high-speed spinning. The mill is well-known for its high output and dependable operation.
Frameworks that support the Bead Mill machine’s functionality
Bead separation:
Part of a bead mill’s working principle is bead separation, which is critical to its efficiency. A machine separates the beads into nano- and microparticles as part of this process using a mill. For the mill to produce fine particles of a specific material, it is a vital component. It also improves the smoothness and convenience of your grinding process.
The milling machine’s power and size:
It stores the mill machine’s power, which is used by the bead mill operating principle to carry out crushing operations. This force is determined by the task’s quality and varies in proportion to the project’s size.
Mill machine speed:
Mill machine speed is also a required parameter for all grinding and dispersion procedures to be completed at a certain speed. The transformation of different materials into nano and microparticles necessitates varied speeds.
Tank for mixing:
You may have noticed a mixing tank available in the mill machine while working with it. The mixing tank aids in uniformly mixing the material and transforming it into micro and nanoparticles.
An installed cooling system
A cooling system is installed in the bead mill machine to aid in the preservation of the material’s temperature. These are very useful for the mill machine itself because if the temperature rises too high, the mill machine and the workers around it may be in danger.
Mill machine design
This bead mill machine is available in a variety of designs and sizes on the market. Every mill machine is unique, but one thing unites them: they all operate in the same way. The operation is the same as with all mill machines, and they are simple to use. Some milling machines are vertical, while others are horizontal.
Furthermore, Franli is the most dependable automation company, offering every bead mill design and other equipment available at a competitive price. The company guarantees its products’ quality and durability, and the best after-sales service.
Verdict:
Mill machines are an essential part of any fabrication business. With nanotechnology, getting nano and microparticles is easy. The available companies can provide you with every bead mill design and size.
Hot sale Bead mill
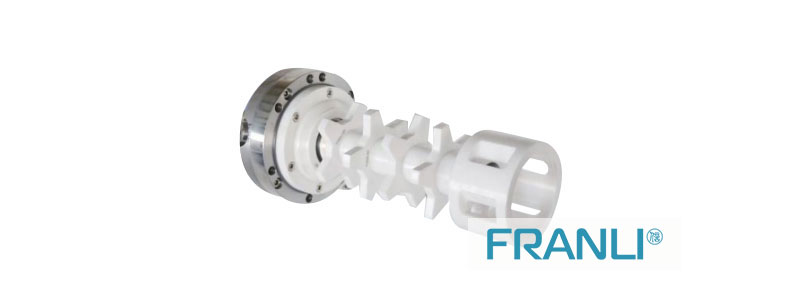
• Easy installation of the bead mill machine: The best features of this bead mill machine are: You can easily install it wherever you want. This task is so simple, and effortless. And due to this feature, it is extremely popular among other equipment. You can find the bead mill working principle so effective, and you can perform all the mixing tasks effectively without adding so much effort. As this machine is very bulky and cheap, it needs only a few minutes to install. In this way, you can reduce the labor charges and other exhausting jobs. So, you can stay worry-free about how to install this machine? As the company has made this task easier for you.
• Efficient work performance of this bead mill machine: As we know, the bead mill working principle has been created in such a way that you can achieve higher and efficient work performance on this bead mill machine. If you are looking for quality and stable work, these bead mill machines are the best option to get a consistent mixture of any particular material. You can use this bead mill for paint, ink, and coating industries. And, it is a comfortable and easy method to perform all the mixing and dispersing activities without wasting so much time. So, here bead mill working process is so necessary to obtain the desired results for the company.
• Contains grinding media of 2-3 mm size: It is the necessary feature of the bead mill working process as it includes the grinding media. In this area, grinding and other dispersing activities take place that they turn into a fine mixture. You can use a bead mill for paint, ink, and coating industries, where mixing works have been done regularly. It contains grinding media of 2-3 mm size that is enough to transform all the material to a smooth and fine paste. For this purpose, bead mill manufacturers have added advanced technology to this machine to provide consistent and quality work performances for the company. In this way, you can get a higher productivity ratio. And you can reach the peak of the higher conversion rate. Thus, these bead mill machines are ideal for fabrication companies to get their desired goals with full efficacy.
• Easy operation of the bead mill machine: It is a great feature of this SMP Agitator bead mill machine as bead mill manufacturers create this bead mill machine with advanced technology. And, with this quality, the operation of this sand grinding mill is extremely comfortable. You do not need to call any professional to do the same, and you can do it yourself without adding so much effort. So, it is another best feature to consider about this bead mill machine.
• Easy to clean the bead mill machine: This sand grinding mill is remarkably best for the fabrication companies to enhance the overall growth and production. As we know, while we use any bead mill machine, we need to clean it so that we can get hygienic work performance. For this purpose, companies manufacture this bead mill machine in a way that you can clean it comfortably without making yourself exhausted. You can go through the bead mill pdf and other relative documents that provide you the guidelines of clean this bead mill machine.
• Easy to maintain the bead mill machine: Maintaining is also a matter of concern as it requires your time and money. For this purpose, you can check the bead mill pdf and manual provided by the company at the time of purchase. You can either contact the company or read the manual carefully to know all the information about the bead mill machine. And, you can find this process is extremely simple to perform. So, you can get this bead mill machine without spending so many amounts on it. And, in this way you can concentrate on the work performance of the company.
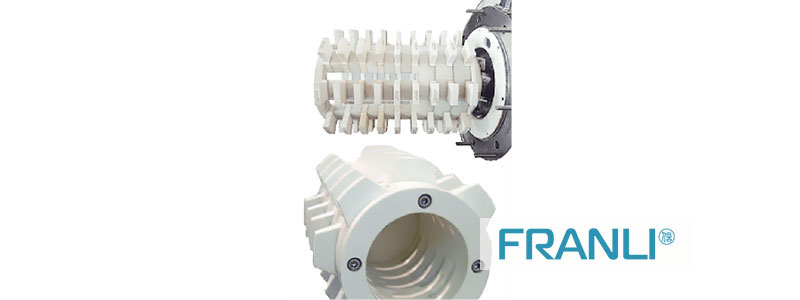
Also, you can use SMP Agitator bead mill in paint industry, ink, and other coating work companies to make all the mixing and grinding activities easier and more manageable. To get this bead mill machine, you search for those companies that deal in these machines and other equipment. For this purpose, you can get a quote or related other information about the bead mill machine.
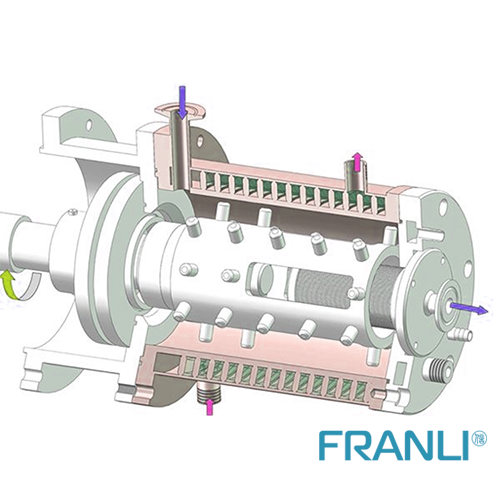
Hydraulic TRH type
Hydraulic Three Roll Mill, which is a full hydraulic auto-controlling system equipment. 1- Cooling system: an individual cooling system for each roller. 2- hydraulic control: hydraulic control pressure blades, roller gaps, etc. 3- Optional installation:PLC system with SIEMENS touching screen, FRANLI engineer set formulas of grinding according to different viscosity materials.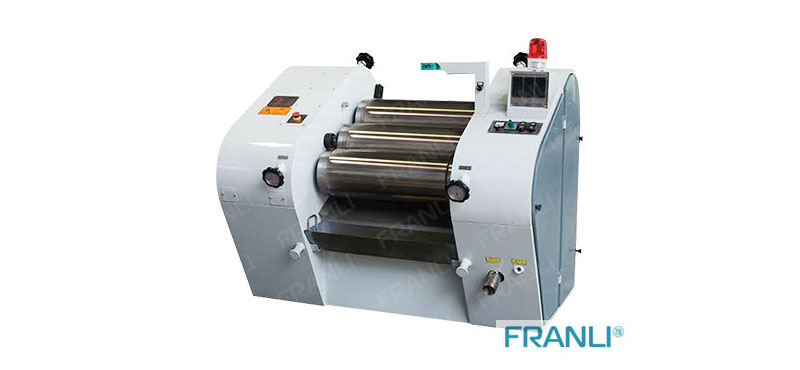
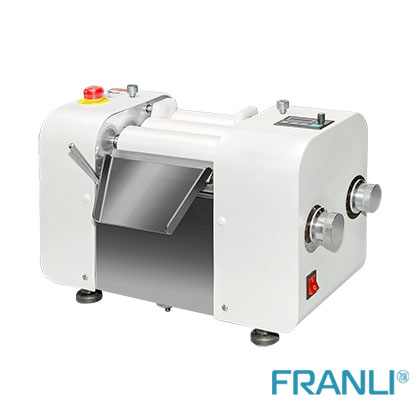
Vertical type for Grinding Powder
Also, we have a vertical three-roll mill for grinding powder and chocolate. We have 3 rollers, 4 rollers, and even 5 rollers, which are all vertical types. We export to the soap industry and chocolate companies.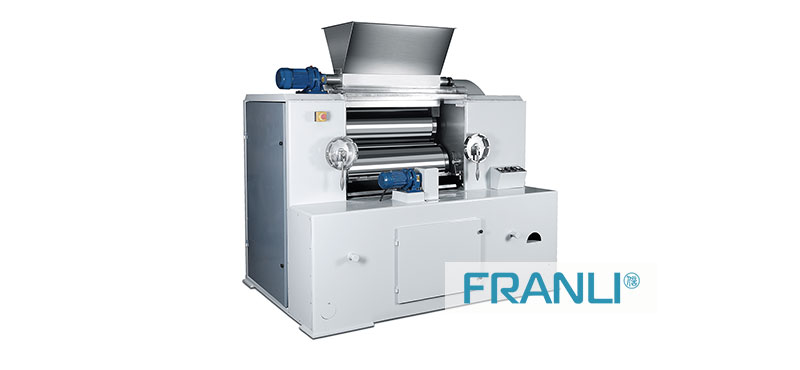
Heating type
Franli also offers a heating hydraulic three roll mill for rubber, EVA, PVS, and color masterbatch. As this type of machine grinds high viscosity material, we specially design the gear quality. This type is been Heated by oil or steam. Franli three roll mill machine are full automatic PLC controlling, hydraulic system, stable operation, reliable quality. We choose the international brand parts. Standrad parts, ABB VFD, Siemens Motor, SKF or NSK bearings, SEW or Nord reducer. A roller is 45-55mm thickness of metal, cast steel. You can widely choose ceramic, alloy, granite rollers for your material. If you have several formulas of material, we can set up formulas in the PLC system, your workers only need to choose numbers on touching the screen, don’t need to waste time to adjust the rollers’ gap or the pressure of the blade.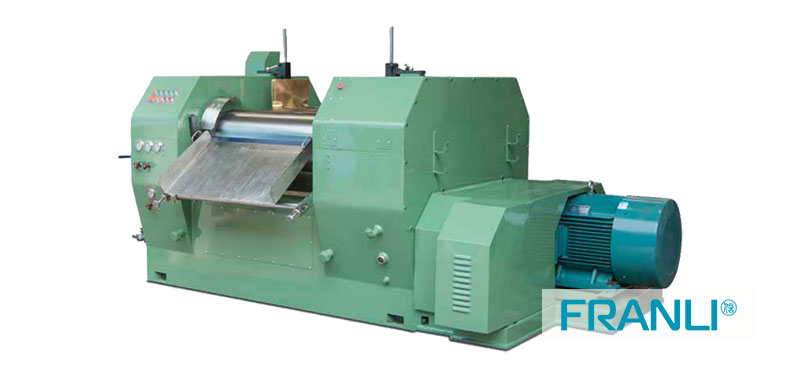
Related production lines
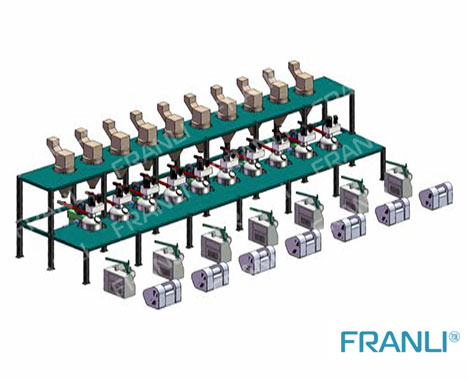
Offset Ink machine line
FRANLI is specialized in offset ink full line production for 20+ years. Helped customer save the cost, save the man power, also save the space.
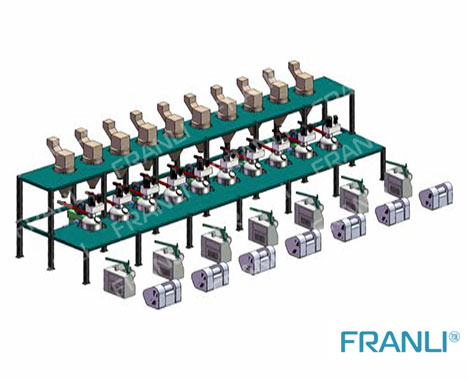
Offset Ink machine line
FRANLI is specialized in offset ink full line production for 20+ years. Helped customer save the cost, save the man power, also save the space.
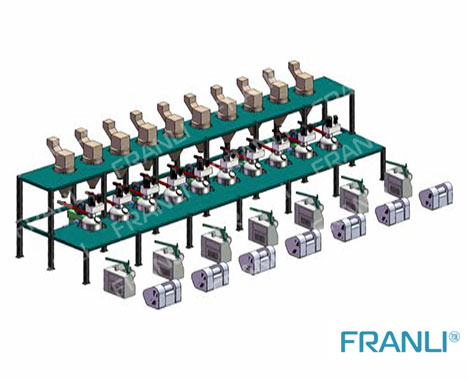
Offset Ink machine line
FRANLI is specialized in offset ink full line production for 20+ years. Helped customer save the cost, save the man power, also save the space.
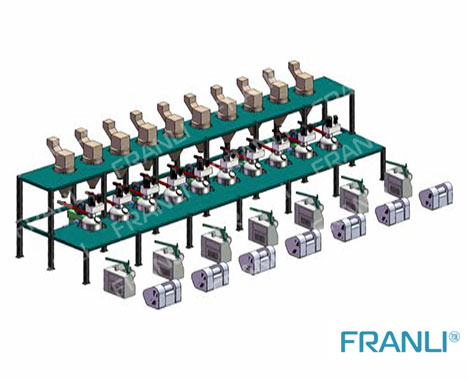
Offset Ink machine line
FRANLI is specialized in offset ink full line production for 20+ years. Helped customer save the cost, save the man power, also save the space.
Guidelines For Bead Mill
Bead mill is essential equipment for any fabrication company, where mixing, grinding, and dispersing activities happens regularly. If you want fine and even work performance, this SMP Agitator bead mill is the must-buy equipment for this process. With the help of this SMP Agitator bead mill, you can obtain speedy and stable activities of the company without adding so much effort.
Microscopic glass, ceramics, or stainless beads are used in Bead mill machines. Those beads, together as the sampling medium, are put in a beaker. Shake or swirling is used to aggressively circulate the jar, beads, and material. As the beads hit both the cells quickly, the samples are disrupted. The use of polishing beads and the rotating action results in a quicker and much more consistent lysis buffer procedure for biological materials. A greater volume proportion of beads to colonies usually results in quicker cell lysis. The beads descend by gravitational force in the jar once the grinding cycle is completed, and the resultant mash is readily extracted using a dropper. Since they use throwaway beads and collection tubes, Bead mill machines are largely merged, independent. Sampling techniques of overexpressing or smaller are limited among most stirring Bead mill machines. Multiple specimens, on the other hand, can be handled at the same moment. Heating may be an issue utilizing Bead mill machine, however many of today’s modern models come with refrigeration towers and equipment as options.
How do you pick the right sort of bead mill machine?
To generate modern materials nanocomposite, AlN nanostructures have been spread in cooling water using a bead mill machine. Such a device diffuses materials via directly impacting aggregates of nanotechnology with threads of a certain diameter that are cycled inside the grinding container via additional Lorentz force. The ideal operating characteristics of a bead mill machine operation were determined using a mathematical formula to look at population balances. This processes model’s dynamic model yielded two equations subgroups, indicates the relative power of such mill’s coagulate or breaking phenomenon.
Bead mill machine – An Insight
Generally, supersonic bead mill machines are best suited to limited water sampling operations. These seem to be more appropriate in greater quantities and may be expanded up to the point, although the technique does not grow along with others yet they are seldom used in manufacturing. Cleaning your sensor around every operation may even be a moment if you do need to analyse several materials throughout quick order. That’s also particularly true when you’re worried about the infection and will need to wash everything thoroughly every time. There are various cup trumpets on the market that allow supersonic power to be delivered to a measured relative even without an instrument interacting directly with them. All those are beneficial for reducing bridge, but they’re only appropriate for low-volume projects that don’t need greater treatment mills.
Manufactures of bead mill machines
We provide a wide selection of bead mill machine, all of which are made from high-quality raw materials to assure the best outcome in the finished result. Its splashing show includes some good agitation disks that aids in efficient electron transport from the major engines to the grinder beads. This also allows solid material to be broken down into a more grounding state. As a result, our bead mill machine could be praised for their high energy efficiency, excellent result, and smooth grinding result.
- A bead mill machine is a flexible wet milling system that has been particularly built.
- Increased water rates are ensured by a specialized centrifuge separation process, which also achieves a significant level of crushing.
- Technology with cooling and heating systems for precise heating and cooling.
- Micro grinding of even the toughest materials is very productive as a result.
- Suitable for both aqueous and preservative sludges.
As a result, paint manufacturers may utilise this fantastic and adaptable mixing machinery to assist their clients in applying a sufficient liquid foundation to the required steel surface. You may rest easy knowing that the machine is made using grading metals, mild steel, metal alloys, and silver by industry requirements. Chose this particular machine to establish a strong foundation for high-quality painting.
Bead mill machine working Principle
The shafts with agitation disks are housed in the horizontal hammer mill of such a bead mill machine. The column is packed with a zirconia grinding medium, with a double functioning piping system that prevents material leaking. A diaphragmatic pumping or a screws pump moves the materials through into the container. The agitation disks transfer the energy needed for dispersing and milling to the crushing beads. The mill is constantly supplied by the pumps. The length of time the substance spends within the container is determined by the flow rate.
A cartridge is used to keep the milled beads within the chambers. Its mill’s performance is enhanced by making the most of the power supplied into the chambers for dispersal and milling.
Applications:
Wet milling of fluids and pigments inserts is done with bead mill machines. They’ve been around for a long time and are frequently used in the paints and chemicals industry. The bead mill machine is a member of the impeller and ideologue families. The ideologue has entirely transformed the conventional grinding machine in the liquid milling of coatings and adhesives because this presses & diffuses constantly and so more effectively.
- Inks for printing
- Chemicals found in leather
- Inks for flexo printing
- Inkjet printers
- Paints
- Preparations for pigment
- Filler
- Chemicals used in agriculture
- Coatings magnetic
- Pharmaceuticals
- Coatings for Thermal Paper
- Chocolate
Franli has a collection of large bead mill machine models that can manage nearly any sort of dispersal. Franli’s dispersion equipment is well-suited to a variety of sectors, including aerospace, microelectronics, agrochemicals, cosmetics, digital printing, and medical device applications.
With bead mill machines, Franli has the research & design expertise and also the manufacturing capability to generate fine solid dispersion. To manage any dispersal assignment, Franli offers an R&D bead-milling simulation, nanoparticle mills, manufacturing mills, and government characterisation facilities.
Related production lines
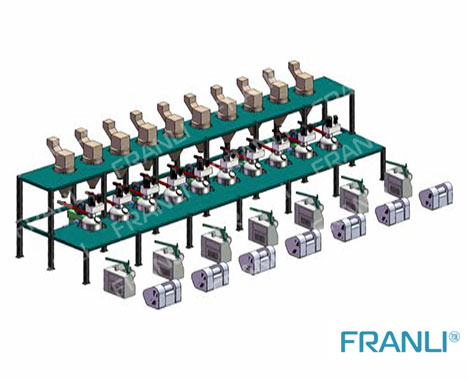
Offset Ink machine line
FRANLI is specialized in offset ink full line production for 20+ years. Helped customer save the cost, save the man power, also save the space.
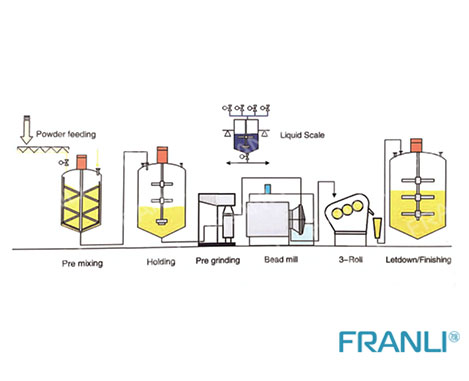
Offset Ink, UV Ink machine line
The FRANLI engineering company, offer the full set of UV INK Production Line, we can make the full drawing according with your factory size, formulas, weather and safety system.
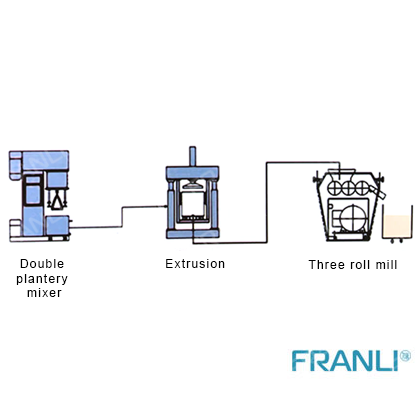
PCB INK Machine line
FRANLI supplies all equipments for the production of PCB inks, from the powder feeding station to the filling part.
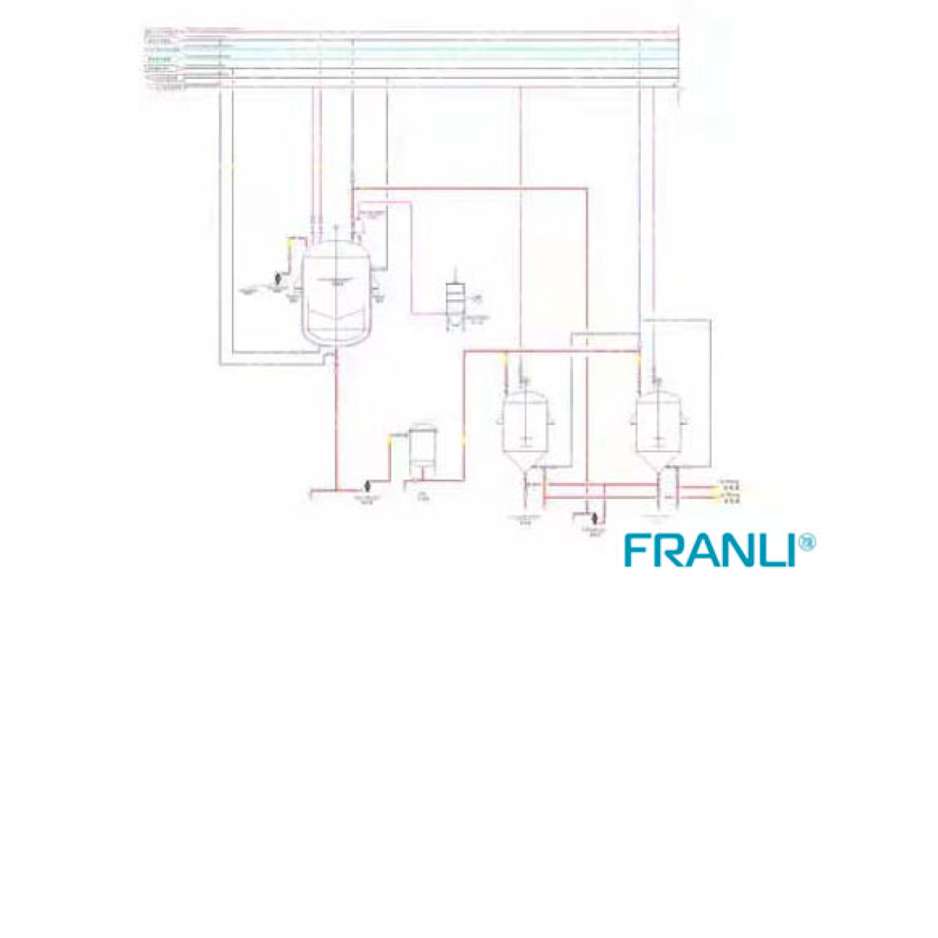
EW-pesticide line
The EW production line mainly mixes raw materials, solvents, and emulsifiers through a reactor (oil-based).
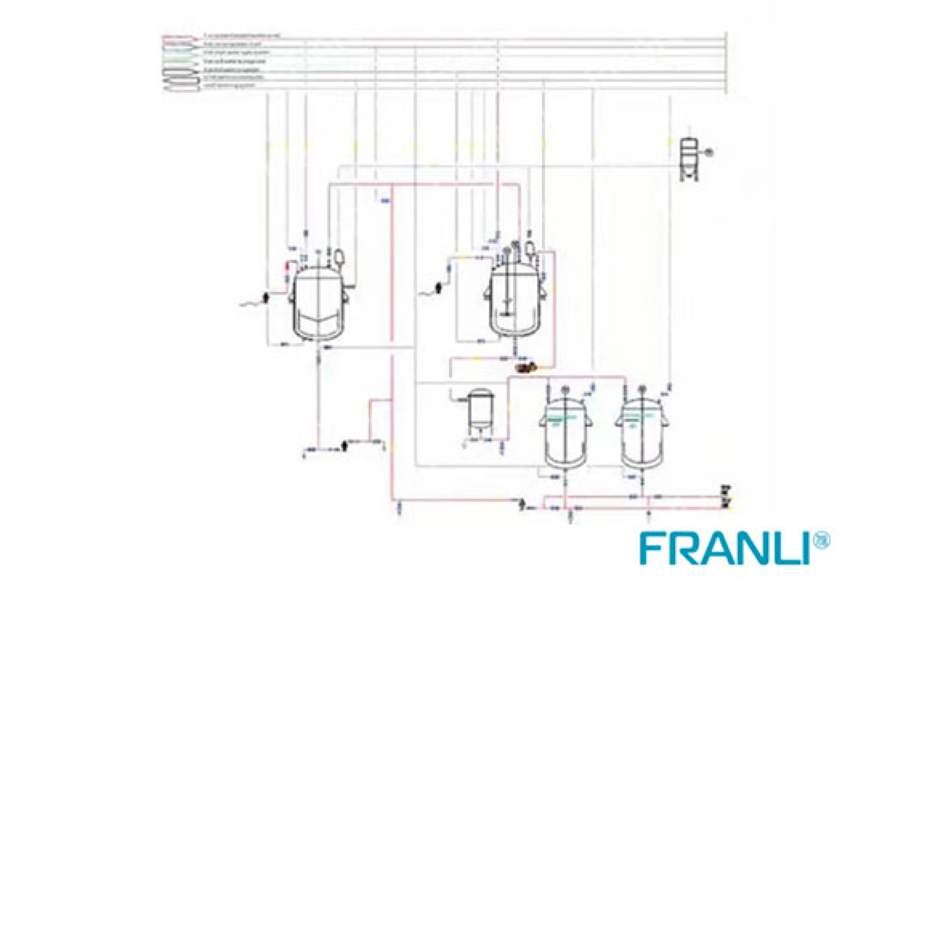
SL_EC pesticide line
The EC production line is mainly composed of an agitator mixer, bag filter, filling machine, etc.
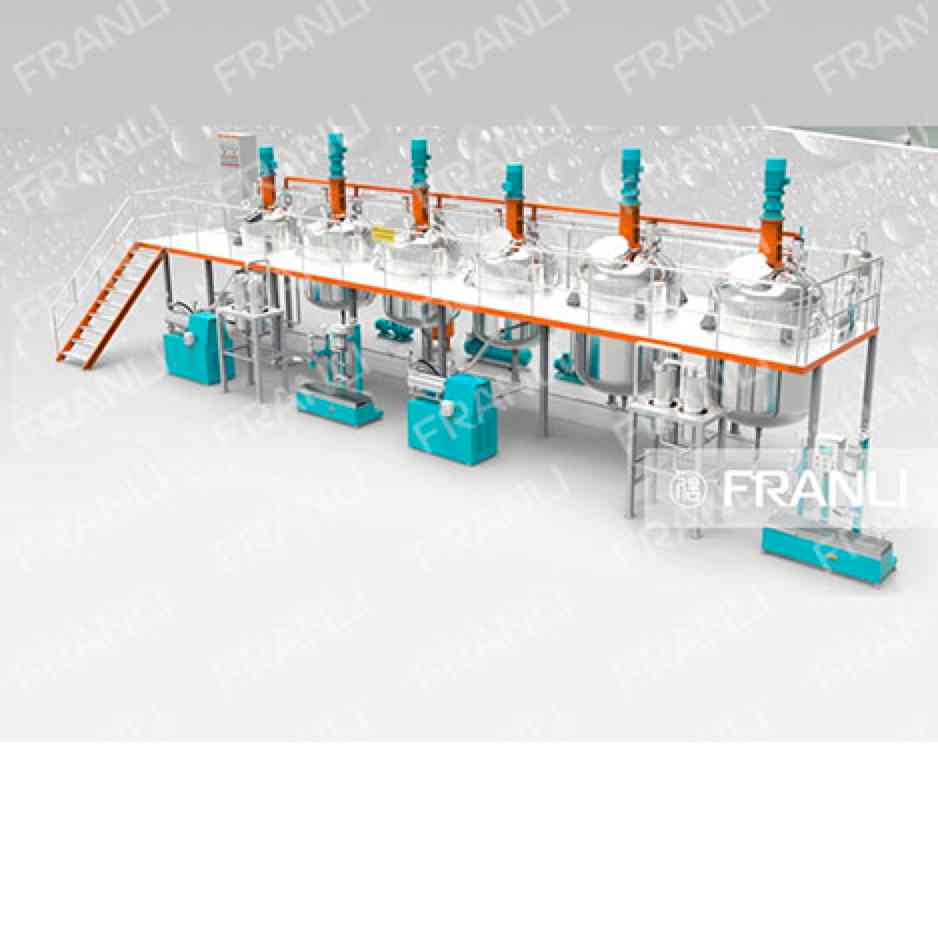
Automotive Paint machine line
The automotive paint machine line is mainly for the production and grinding of automotive paint, Automotive paint has many layers, such as Primer/electrophoretic layer, Medium coat, Colored coat, and Clearcoat.
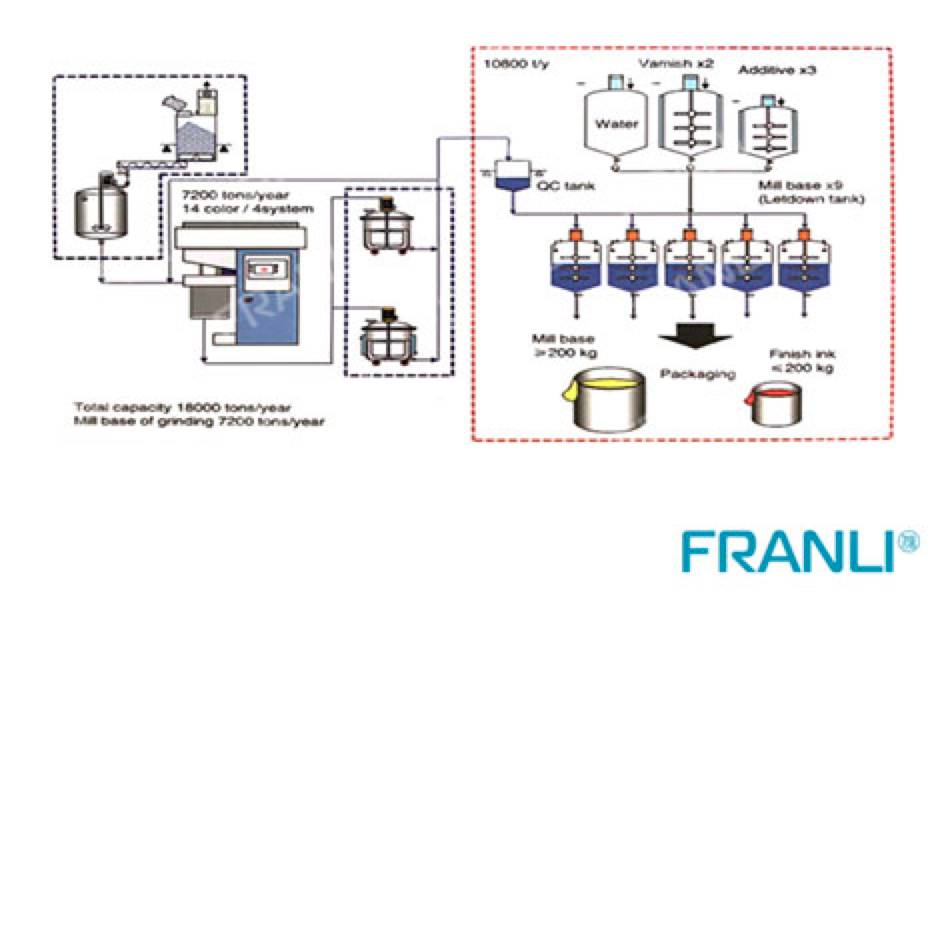
Digital Ink machine line
Franli has professional experience for digital ink machine line, we offered hundreds customers to expand production, or build up new project.