Home » How to make a installation after get bead mill
How to make a installation after get bead mill
We should take care of the installation for the bead mill, how to easily install the bead mill?
Use four hanged ring bolts as the lifting support points to carry out installation work.
The electric console should be installed out of the explosion zone.A special foundation for the machine is not required. The machine is only required to install at the solid ground and holds level.When you position the machine, you should take the following into consideration:
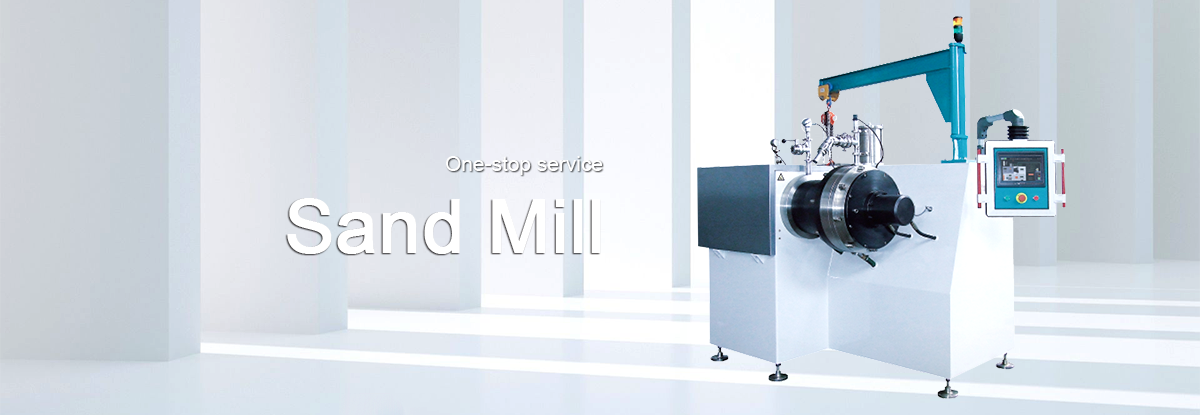
bead mill (Sand mill)
2)It is easy for material-in pipe, cooling water pipe, air compressing pipe to install and join.
3)It is easy for dynamic devices and control wires to install and link.
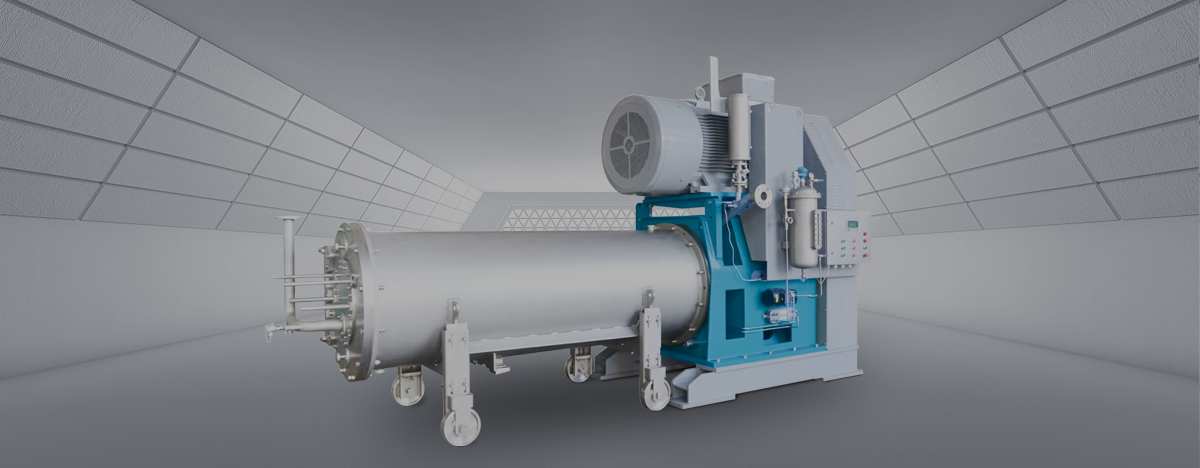
bead mill
3. Assistant system
1) Cooling water system
2)Compressed air
3)Electric system
Main motor rotation direction should meet with marked direction, i.e.when you open the back shell, you face to belt wheel clockwise.
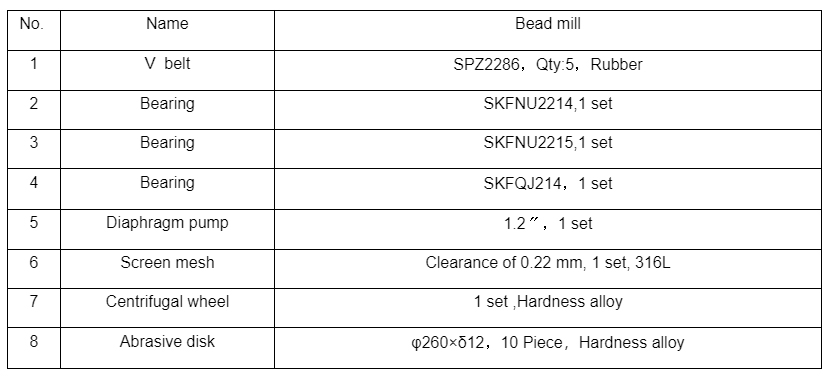
(Optional when user purchase the spare parts)
BEAD MILL Safety Instructions
(2) In addition to those stated in the operating instructions, observe the generally valid, legal, and otherwise binding regulations for accident prevention! These types of liability can apply, for example, to the handling of hazardous materials or the wearing of protective clothing.
(3) Operate the machine only when there are no technical problems and only in a safety-conscious manner, as directed, in accordance with the operating instructions! Above all, immediately attend to any problems, which could adversely affect safe operation.
(4) The manufacturer accepts no responsibility for damage resulting from material properties and reactions of the product being processed. The user alone bears the risk.
(5) Observe all notices concerning safety and hazards which appear on the machine and keep them in a legible condition!
(6) Backfitting or changes on the machine must only be carried out after consulting the manufacturer. Spare parts must comply with the technical requirements stipulated by the manufacturer. This is always guaranteed with original spare parts. The use of non-original spare parts from other suppliers results in the loss of liability for any damages resulting thereof.
(7) Only operate the machine with all protective devices, e.g. emergency cutout, safety limit switch, noise reduction, suction devices, in place and in a functional state!
(8) Before switching on the machine, make sure that no one is endangered by the start-up.
The following safety regulations apply in particular to machines with freely accessible, rotating shaft:
• Protect hair against trapping hazard by wearing a hairnet;
• wear safety glasses;
• wear tight-fitting working clothes;
• take off watch, finger rings, bracelets or necklaces, etc.
(9) If the machine is completely shut down for maintenance or repair, it must be secured against an unexpected restart:
• lock the primary control device and remove the key and/or
• place a warning sign at the main switch.
(10) For assembly work above body height, use ladders and work platforms provided or those meeting safety requirements. Do not climb on machine parts!
(11) Use caution when handling hot products and machine parts, e.g. product pipelines or those which are heated, non-insulated areas of the grinding tank, turbo-coupler, due to the danger of burning. This is also valid for tanks and pipelines cooled to extremely low temperatures.
(12) Before cleaning the machine with water or other cleaning agents, cover or tape all openings that should be protected from moisture due to safety or operational reasons.
Especially at risk are electro-motors and switch cabinets. The covers are to be completely removed after cleaning!
(13) During loading use only hoisting equipment, load-lifting devices, and transport vehicles with sufficient bearing capacity!
(14) Machines must only be transported and assembled by the qualified skilled staff! For safety reasons please make sure that the machine is lifted as low as possible during trans
port! It is not allowed to stay under overhead loads! Make sure that the machine is fixed safely, this applies in particular to top-heavy machines!
(15) Disconnect the machine from all external energy supplies even for minor changes of position!
Before restarting the machine, reconnect it to the power supply according to regulations!
(16) Work on electrical units or machinery materials may only be performed by an electrician or under the direction of an electrician according to the electro-technical regulations and the respective accident prevention specifications.
(17) The electrical equipment for a machine is to be maintained and operated according to regulations and to be constantly monitored. Necessary work should be undertaken immediately. An electrical unit may not be operated if it shows signs of a defect through which operators or third parties could be endangered.
(18) Machines and plant parts, on which inspection, maintenance, or repair is performed, must be connected free of voltage.
(19) Tampering and modifications, which violate the test and acceptance specifications, are not allowed on structural parts or components that are approved for use in the Ex area or for Ex protection.
(20) Welding, burning, and grinding work may only be carried out on the machine with authorization. I.e. when no danger of fire or explosion exists.
(21) Eliminate the pressure before opening machine sections and lines that are under pressure (e.g. grinding tank, sealing pressure unit).
(22) Dangers for people with heart pacemakers:
• There is a high risk of crushing.
• Strong magnetic fields can disturb the function of pacemakers!
• A minimum distance of 2 m must be maintained.
Copyright Notice :
This article only represents the author’s point of view.
This article is published under the authorization of the author.
Source: Franli
This article address : How to make a installation after get bead mill
Related Products
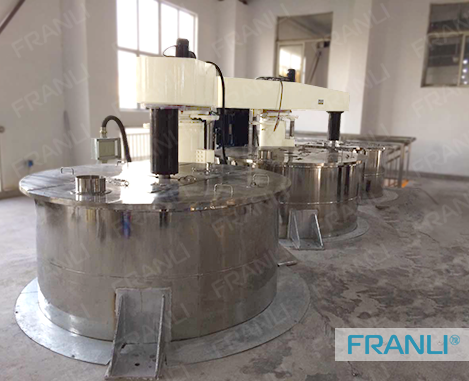
Platform Type High Speed Disperser
Platform type high-speed disperser is mainly used for high production material. Normally the high-speed disperser is installed between two tanks, easily mixing material in two tanks. also another type.
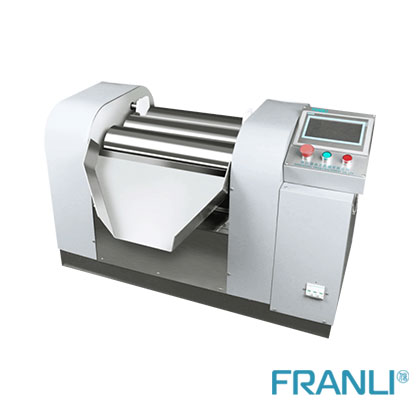
Digital Control Three Roll Mill
The roller of the digital control three roll mill is made of zirconia ceramic material and equipped with a frequency conversion speed regulating device to meet the grinding needs of different materials.
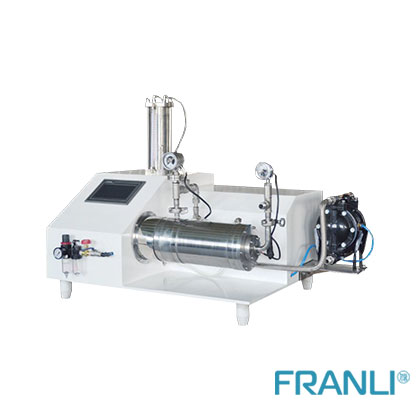
Lab bead mill
FRANLI Lab bead mill is widely used in coatings, inks, fuels, non-metallic mineral ultrafine powder, magnetic recording materials, and other industries.
News
Laboratory Reactor: Guide to Stirring System
The laboratory reactor is composed of a pot body, a pot cover, an agitator, a jacket, a support and transmission device, a shaft seal device, etc.
Grinding Media for Bead Mill | Zirconia Beads & Zirconium Silicate Beads
Bead mills mainly use grinding balls as media, and use impact, extrusion, and friction to achieve the final grinding effect, which mainly depends on the size and hardness of the grinding beads, the filling rate of the grinding beads, and the collision frequency adjustment between the grinding beads and the particles.
Overview of Laboratory Reactor
Laboratory reactors, also known as lab reactors, are essential tools in scientific research, product development, and process optimization. These reactors provide a controlled environment for conducting chemical reactions, mixing, dispersing, and homogenizing processes.
Bead mills | Manufacturing technology in various industries
Bead mills, also known as sand mills or grinding mills, are versatile machines widely used across various industries for the wet grinding and dispersion of solid particles in liquid media.
Ribbon Blender Mixer Equipment
A ribbon blender mixer, also known as a ribbon mixer or horizontal ribbon blender, is a powerful industrial machine designed for thorough and efficient blending of various materials.
What is A Stainless Steel Reactor?
Stainless steel reactors are essential equipment in various industries, including chemical, pharmaceutical, biotechnology, and food processing.