Home » How to choose the ointment mill suitable for the industry
How to choose the ointment mill suitable for the industry
Ointmen mill is the machinery used to mix, refine, disperse, or homogenize viscous materials fed into the mill with shear forces caused by three horizontal rolls rotatable towards opposite directions and at varying speeds relative to each other. The product is pulled across the roller spaces. Active substances and powder clumps are disrupted and homogenized, eliminating smear and creating topical results. This results in an effective and elegant ointment.
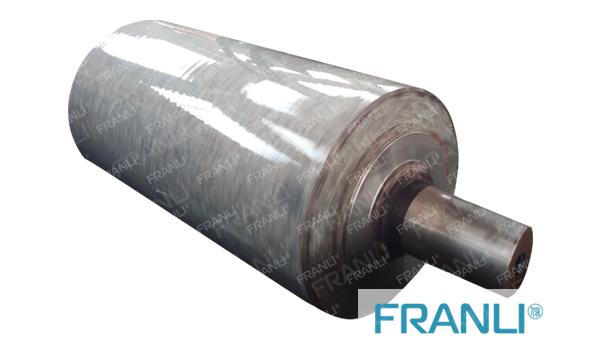
How does it work?
At a progressively greater rate, three adjacent rolls of an Ointment mill, named the feed roll, the middle roll, and the delta roll, rotate. Material is fed between the feed roll and the center roll, typically in paste form. Because the distance between rolls is reducing, most of the paste remains in the feed area initially. Due to the different rotational speeds of the two rolls, the section that makes this by the first running nip experiences very high cistern force. Upon exiting, the material remaining on the middle roll passes between the center roll and the trailing roll through the second nip.
The fast speed of the apron roll and normally smaller space between the feed and the central rolls imposes even more heavy shear force. The processed material is subsequently struck out of the tab roll by a knife blade and the paste rolls through the apron. To maximize dispersion, the frying cycle may repeat numerous times. The spacing between the rolls can be changed and maintained mechanically or hydraulically. The gap distance is typically much larger than the size of the particle. In some operations, the distance between the gaps is gradually lowered to the required dispersion level. Normally, the rollers are water-cooled inside.
Where is it used widely?
Small bench models are used for bench-top development, laboratory work, and low-volume manufacturing. Larger bench and floor models are built to meet a variety of production needs, ranging from pilot plants to high-volume production. This process has the added benefit of milling high viscosity pastes, and the high surface contact with the cooled rollers keeps the temperature low despite the high amount of dispersion work put in. One significant disadvantage is that the large open area of paste on the rollers causes volatiles to be lost.
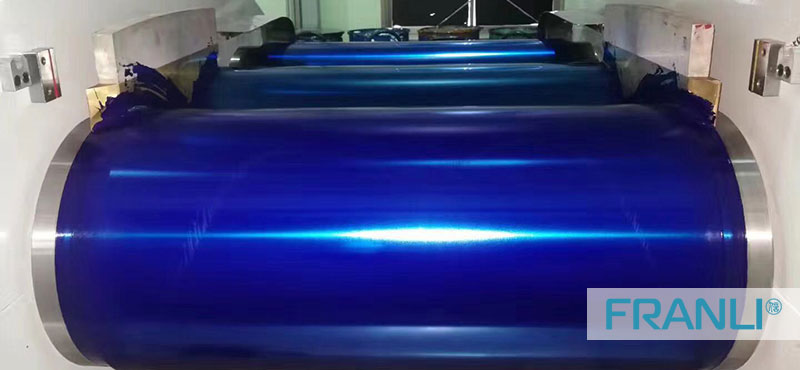
ointment mill roller
Different series of Ointment Mill:
Cooling control system: TRS & TRM three roller machine thermometer installed, easily check the material temperature. Chillers are normally connected to three rolls. Typically by first passing grinding, you can get to 10-20um. While using an ointment mill, transfer gears with grease, and check the chain. However, it is still widely used in the soap and printing industries.
Hydraulic TRH type: Hydraulic Ointment Mill, with a full hydraulic auto-controlling system. Cooling system: each roller has its cooling system. Hydraulic control: hydraulic pressure blades, roller gaps, and so on.
Optional installation: PLC system with SIEMENS touching screen, Engineer set grinding formulas based on different viscosity materials.
TRL Type Lab: Ointment Mill with PLC Touching Screen, which is widely used in the pharmaceutical, ink, cosmetics, and electronics industries. Auto-operation of digital numbers, small size which is the smarter, safer, and faster option which is tailored to meet the needs of various materials
Heating Type: The gear quality for this type of machine is specially designed because it grinds high viscosity material and is heated with oil or steam. ointment mill machines have full automatic PLC control, a hydraulic system, stable operation, and consistent quality. International brand components are selected. ABB VFD, Siemens Motor, SKF or NSK bearings, SEW, or Nord reducers are examples of standard parts. A roller is made of cast steel with a thickness of 45- 55mm. For your material, you can select from a wide range of ceramic, alloy, and granite rollers. If there are several material formulas, we can program them into the PLC system so that your workers only have to choose numbers by touching the screen and don’t have to waste time adjusting the rollers’ gap or the blade’s pressure.
There are several types of feeding systems for different viscosities of material. For example, a feeding pressure machine, also known as an extruder machine. A feeding system with a single reducer motor is installed on top. However, if your material has a very high viscosity and you are producing a small batch, we recommend that you feed the material into the rollers with a manual scrapper.
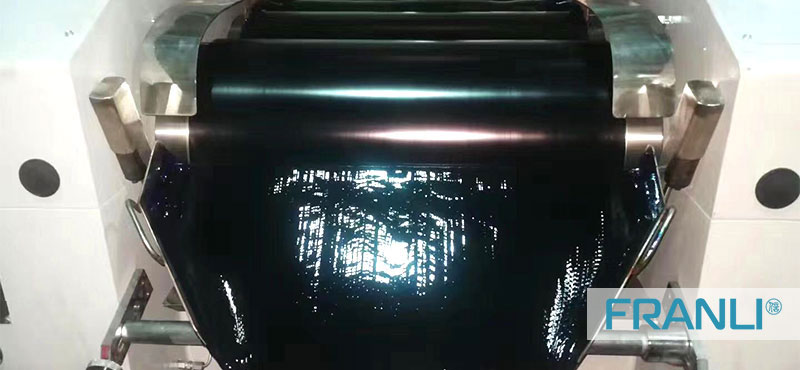
ointment mill feeding port
Merits:
One of the most prominent manufacturers, FRANLI, specializes in Ointment mill designs. They designed their Ointment mill which can break open all kinds of pigment, UV ink, offset ink, decorative paints, and Lubricants. In addition to this, this ointment mill also can catch the greatest fineness in the cosmetics/ lipstick and electronics industries. Coming to the quality control of Ointment mills, they will offer the certification of the machine, before shipment. The roller balance, the thickness of the roll, the heating or cooling system, blade pressure, and full pressure system outlet function for materials has been checked thoroughly. For more details visit their official website.
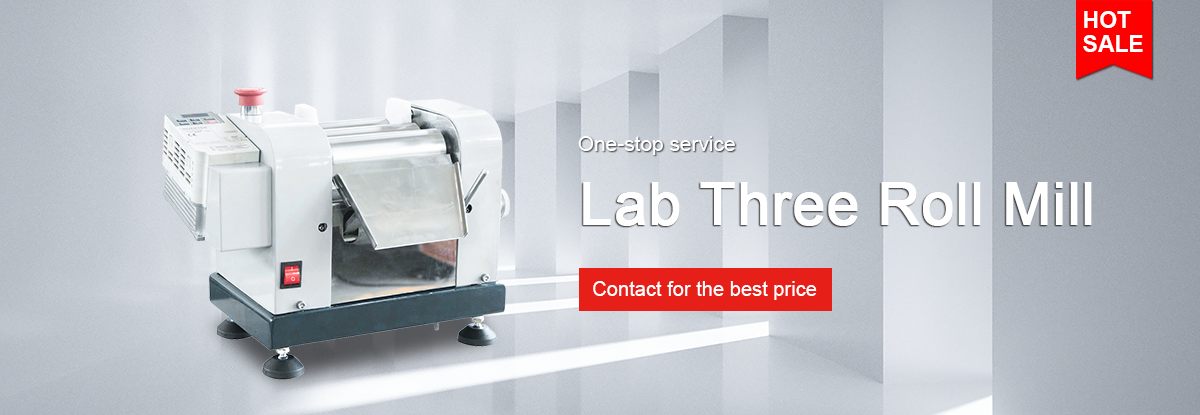
Copyright Notice :
This article only represents the author’s point of view.
This article is published under the authorization of the author.
Source: Franli
This article address : How to choose the ointment mill suitable for the industry
Related Products
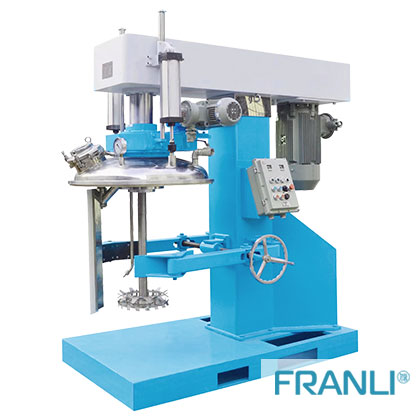
Twin Shaft Disperser
The Twin Shaft Disperser is composed of two sets of mixing devices. Different mixing devices can be designed according to different materials.
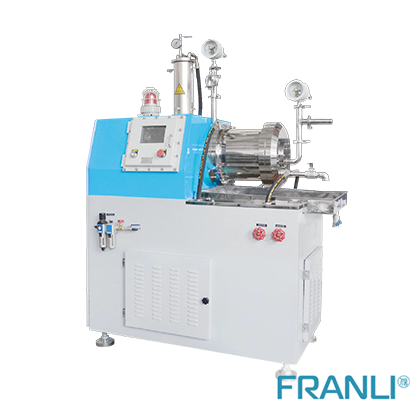
Bead mill for paint
The application fields of liquid coatings are very wide, so a bead mill for grinding high-quality and high-fineness coatings is required.
News
Laboratory Reactor: Guide to Stirring System
The laboratory reactor is composed of a pot body, a pot cover, an agitator, a jacket, a support and transmission device, a shaft seal device, etc.
Grinding Media for Bead Mill | Zirconia Beads & Zirconium Silicate Beads
Bead mills mainly use grinding balls as media, and use impact, extrusion, and friction to achieve the final grinding effect, which mainly depends on the size and hardness of the grinding beads, the filling rate of the grinding beads, and the collision frequency adjustment between the grinding beads and the particles.
Overview of Laboratory Reactor
Laboratory reactors, also known as lab reactors, are essential tools in scientific research, product development, and process optimization. These reactors provide a controlled environment for conducting chemical reactions, mixing, dispersing, and homogenizing processes.
Bead mills | Manufacturing technology in various industries
Bead mills, also known as sand mills or grinding mills, are versatile machines widely used across various industries for the wet grinding and dispersion of solid particles in liquid media.
Ribbon Blender Mixer Equipment
A ribbon blender mixer, also known as a ribbon mixer or horizontal ribbon blender, is a powerful industrial machine designed for thorough and efficient blending of various materials.
What is A Stainless Steel Reactor?
Stainless steel reactors are essential equipment in various industries, including chemical, pharmaceutical, biotechnology, and food processing.