Home » Why choose our Franli three-roll mill?
Why choose our Franli three-roll mill?
• Roller thickness of alloy. Which is our popular advantage, many customers asked the lower price and strong competition, while have you check the roller thickness? Our alloy roller thickness is 60-65mm, while some small three roll mill factory thickness is 45mm. What disadvantages if choose lower thickness roller? The factory has to offer you rollers with middle over higher, both sides lower, then can outlet material. But if you choose such a higher height roller, which means higher pressure. If higher pressure, then the pipe connection must be tightly connected, or your oil will be leaking.
• We choose V-type oil sealing for Oil tank, which is made by an injection molding machine. Life of V type is longer, cant is changed shape, won’t leaking oil. Normal O type sealing ring is easily leaking oil after several years.
• Three roll mill’s knife is imported from Japan.
• Hydraulic oil tank, which is cast iron part, don’t choose oil tank by a screw connection.
Service of FRANLI
• Needs testing again before shipment, check the discharging features and capacity, fineness of the material.
• Oversea installation and training in your factory, if you have several similar viscosity materials, we can set up the formulas into a PLC system.
l We will teach how to safty operation machine, and maintain three roll mill.
• Warranty is 2 years since you received the machines.
• Free offer the spare parts of three roll mill.
• Our engineer will regularly come to check three roll mill every year. • Full life support for your machines.
Save your cost of FRANLI
• The steel frame of three roll mill, and wooden case cover.
• Easily come to check our factory, near shanghai international airport.
• Long-cooperation with branded parts, get a good price of ABB, SIEMENS.
• Free blades of three roll mill.
Copyright Notice :
This article only represents the author’s point of view.
This article is published under the authorization of the author.
Source: Franli
This article address : Why choose our Franli three-roll mill?
Related Products
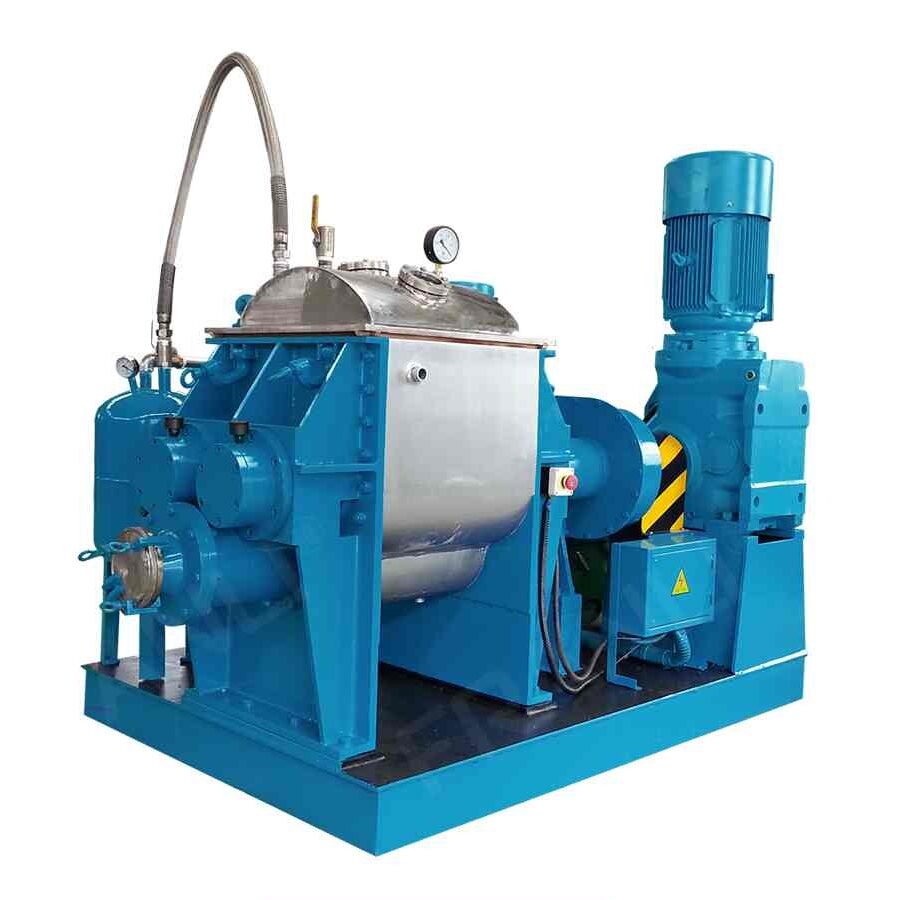
Z Blade Mixer
The Z blade mixer is made for extensive mixing, kneading, and stabilizing strong and high viscous materials, such as bubble gum bases, bread, caramel mass, body wash platform, and glue.
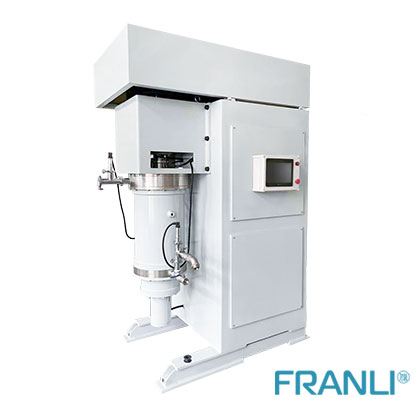
Pearl Mill
The pearl mill grinding chamber with pins, specially designed grinding shaft. We install an advanced cooling system for high temperature of viscosity material. Pearl mill has a German mechanical seal, NSK bearings. Which avoids the leaking of material.
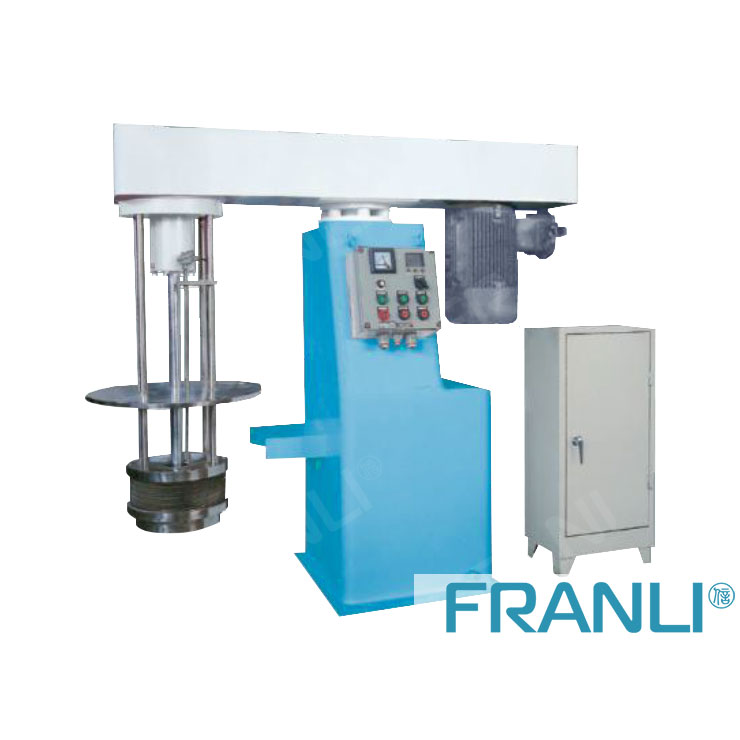
Immersion Mill
FRANLI immersion mill is a new type of discontinuous ultrafine mill integrating grinding and dispersing. After many studies and data, it is shown that this immersion mill is especially suitable for the production and grinding of small batches and multi-variety products.
News
Laboratory Reactor: Guide to Stirring System
The laboratory reactor is composed of a pot body, a pot cover, an agitator, a jacket, a support and transmission device, a shaft seal device, etc.
Grinding Media for Bead Mill | Zirconia Beads & Zirconium Silicate Beads
Bead mills mainly use grinding balls as media, and use impact, extrusion, and friction to achieve the final grinding effect, which mainly depends on the size and hardness of the grinding beads, the filling rate of the grinding beads, and the collision frequency adjustment between the grinding beads and the particles.
Overview of Laboratory Reactor
Laboratory reactors, also known as lab reactors, are essential tools in scientific research, product development, and process optimization. These reactors provide a controlled environment for conducting chemical reactions, mixing, dispersing, and homogenizing processes.
Bead mills | Manufacturing technology in various industries
Bead mills, also known as sand mills or grinding mills, are versatile machines widely used across various industries for the wet grinding and dispersion of solid particles in liquid media.
Ribbon Blender Mixer Equipment
A ribbon blender mixer, also known as a ribbon mixer or horizontal ribbon blender, is a powerful industrial machine designed for thorough and efficient blending of various materials.
What is A Stainless Steel Reactor?
Stainless steel reactors are essential equipment in various industries, including chemical, pharmaceutical, biotechnology, and food processing.