Home » What is the difference between dyno mill and static bead mill?
What is the difference between dyno mill and static bead mill?
Effective grinding linear speed V8mS=(3.14)*D(rotor diameter)*R(equipment speed)
The first generation disc rotor of bead mill for wet milling
The rotor adopts a standard disc structure, the diameter between the disc and the disc is very small, the linear velocity is far less than 8m/s, and the gap between the disc and the disc is small, the material convection is poor which lead to grinding dead corner.
Second generation eccentric disc rotor on Bead mill in wet milling
The rotor of the bead mill adopts an eccentric disc structure, which indirectly increases the rotor diameter and increases part of the linear speed. In addition, the gap between the discs increases, which increases the convection velocity of materials in the grinding chamber, and indirectly solves the problem of partial grinding dead angle. However, there are still some dead corners in the grinding process, and the efficiency is 30% higher than that of the eccentric disc.
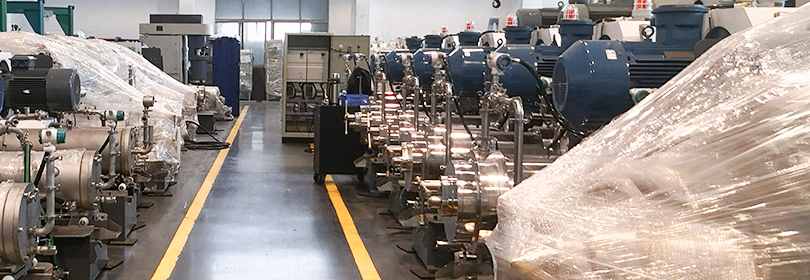
Bead Mill Warehouse
Bead mill - discharge method
Static screen discharge is the key point in the wet milling process of bead mill
Advantages: Large discharge area, high efficiency, can add zirconium beads of 0.3mm or more, and the fineness of bead mill grinding is smaller than the dynamic gap
Disadvantages for Static screen discharge of bead mill: It is easy to block the screen, and can only grind low-viscosity materials. The screen does not have a cleaning function and needs to be cleaned and replaced regularly
About the “Comparison of Double Mechanical Seal Vs Single Mechanical Seal ” in bead mill equipment
1.single mechanical sea of bead mill– Shaft seal: The disadvantage is that a leak that occurs in the shaft seal oil will run into the grinding barrel resulting in material contamination. The entire shaft seal shall be replaced in case of leakage
2.Double sides mechanical sea of bead mill: it is composed of a moving ring (tungsten carbide) and a stationary ring (silicon carbide). The external mechanical seal coolant (the added coolant is the same as the solvent for grinding materials) is used to cool the rotating ring and stationary ring. Leakage will not contaminate the grinding materials. in the future, when maintenance, we need to replace the moving ring only and do not need to replace the whole static ring, save the maintenance cost.
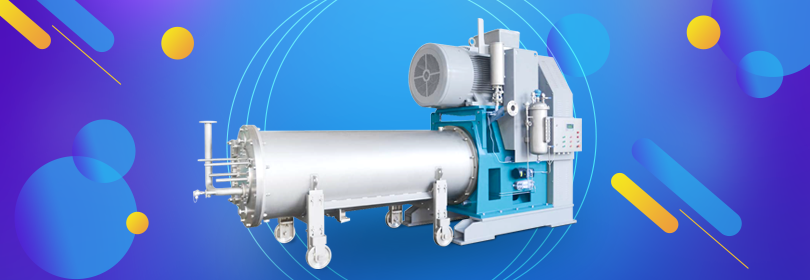
Copyright Notice :
This article only represents the author’s point of view.
This article is published under the authorization of the author.
Source: Franli
This article address : What is the difference between dyno mill and static bead mill?
Related Products
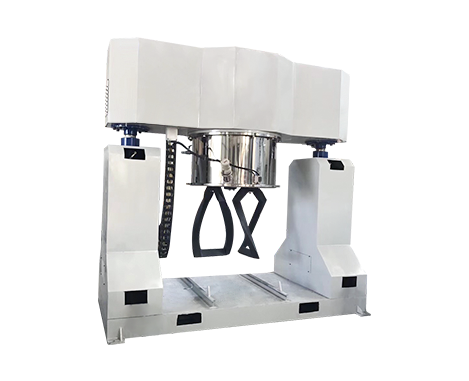
Double planet mixer
Double planet mixer is a new type of mixing equipment with high performance, high speed, easy cleaning, and maintenance. The two agitators of the equipment revolve around the axis while rotating.
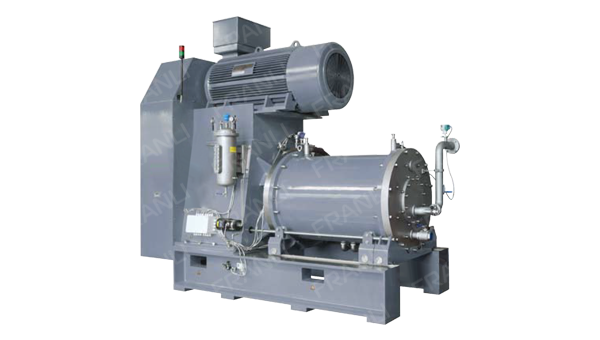
Agitator bead mill
Agitator bead mill’s pins are uniform distributed type, pre-milling your material when feeding material into chamber. The agitator bead mill has a stronger power motor, material milled by bead, and pins in the chamber.
News
Laboratory Reactor: Guide to Stirring System
The laboratory reactor is composed of a pot body, a pot cover, an agitator, a jacket, a support and transmission device, a shaft seal device, etc.
Grinding Media for Bead Mill | Zirconia Beads & Zirconium Silicate Beads
Bead mills mainly use grinding balls as media, and use impact, extrusion, and friction to achieve the final grinding effect, which mainly depends on the size and hardness of the grinding beads, the filling rate of the grinding beads, and the collision frequency adjustment between the grinding beads and the particles.
Overview of Laboratory Reactor
Laboratory reactors, also known as lab reactors, are essential tools in scientific research, product development, and process optimization. These reactors provide a controlled environment for conducting chemical reactions, mixing, dispersing, and homogenizing processes.
Bead mills | Manufacturing technology in various industries
Bead mills, also known as sand mills or grinding mills, are versatile machines widely used across various industries for the wet grinding and dispersion of solid particles in liquid media.
Ribbon Blender Mixer Equipment
A ribbon blender mixer, also known as a ribbon mixer or horizontal ribbon blender, is a powerful industrial machine designed for thorough and efficient blending of various materials.
What is A Stainless Steel Reactor?
Stainless steel reactors are essential equipment in various industries, including chemical, pharmaceutical, biotechnology, and food processing.