Home » Kneader: New kneading equipment for high-viscosity materials
Efficient Kneader|Kneader Manufacturers & Suppliers
When talking about Kneaders unit and efficiency, the unit is particularly suitable for plasticizing and mixing pure rubber, elastomers, recycled rubber, and plastics. Its low viscosity allows it to integrate a wide range of materials.
Working principle and design features
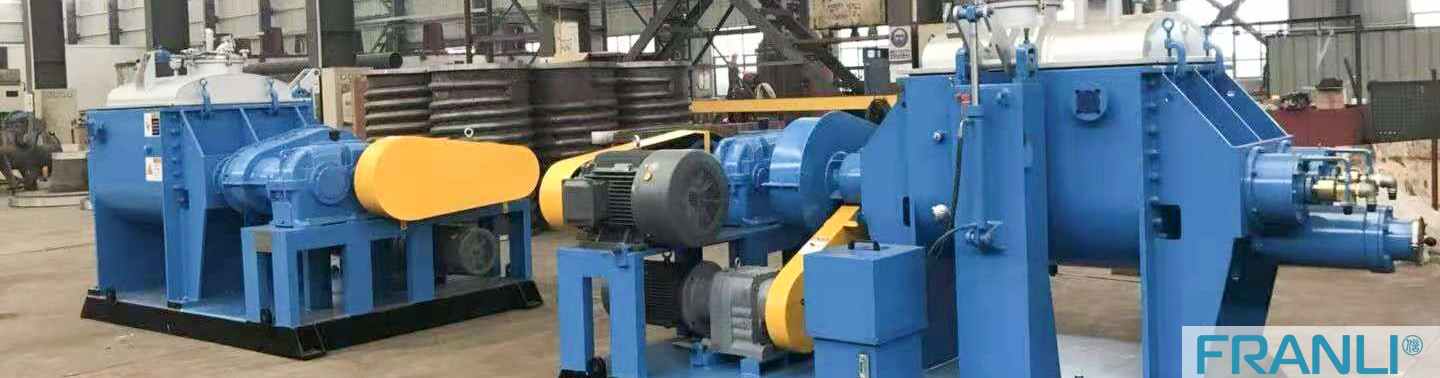
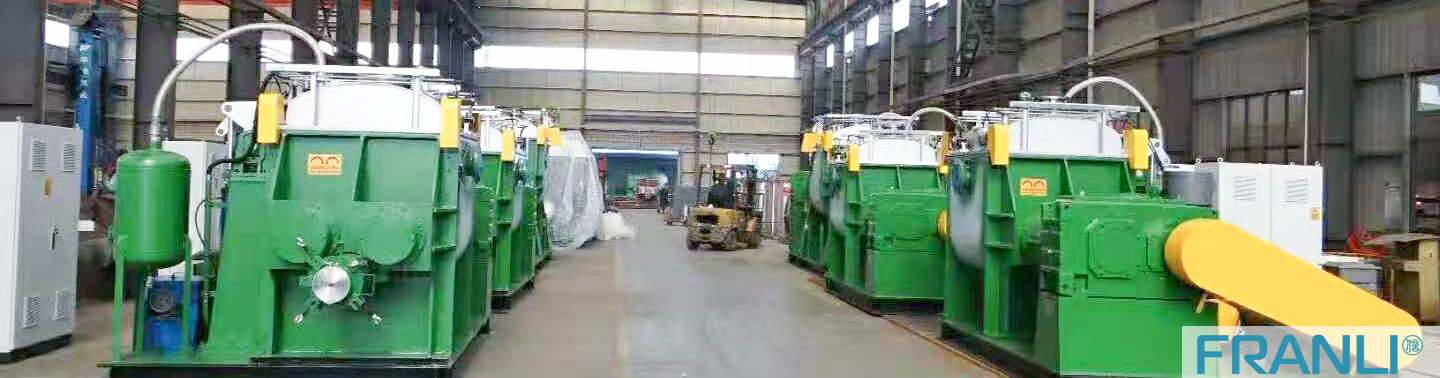
Lubrication system
• The machine's lubrication system consists of three elements:
• Lubrication of the gearbox
• Lubrication of the worm wheel of the tilting machine
• Lubrication of the worm
• The individual tool
Lubrication system
Setting, adjustment, and control of the operation
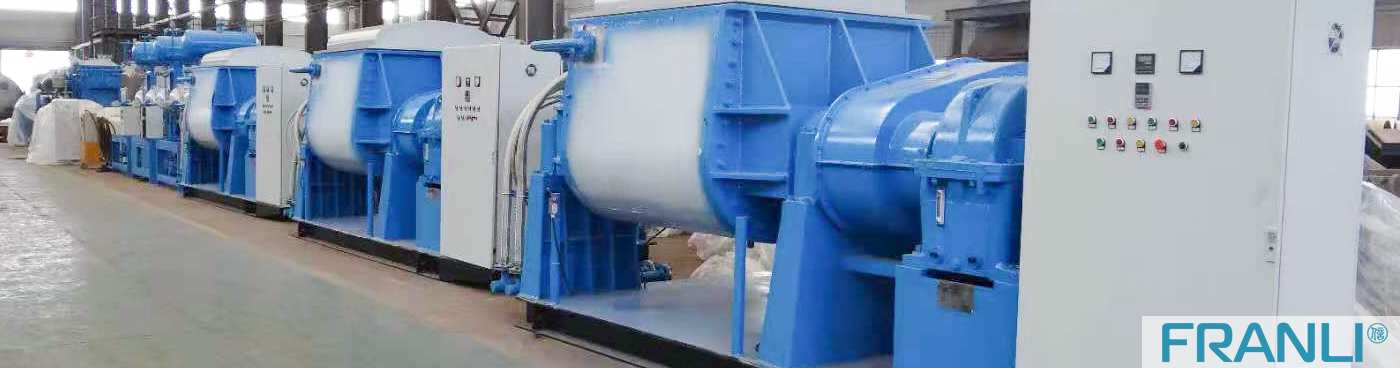
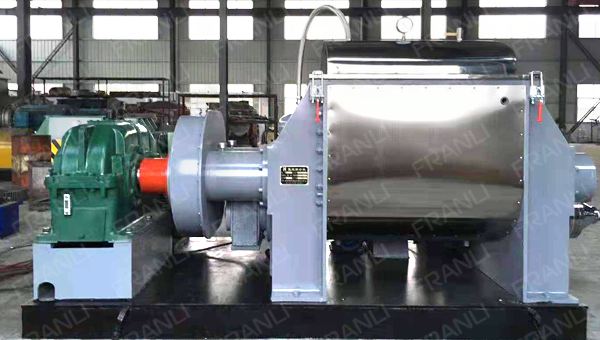
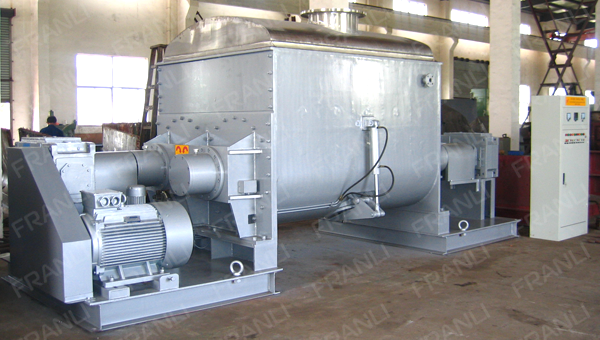
The load test is divided into three parts:
4) 70% of the effective material power is used
5) a whole load test is performed, and rubber kneader machine price is fixed. The load test ensures that the gears work stably, without jerking or abnormal noise. Each shift section is versatile and reliable.
After the work is stopped, the gears’ meshing is checked, and if everything is normal, the machine is ready for production and use. The most reputable firm that possesses various sorts of machines with top notch quality and proper functioning is undoubtedly Franli.
Copyright Notice :
This article only represents the author’s point of view.
This article is published under the authorization of the author.
Source: Franli
This article address : Efficient Kneader|Kneader Manufacturers & Suppliers
Related Products
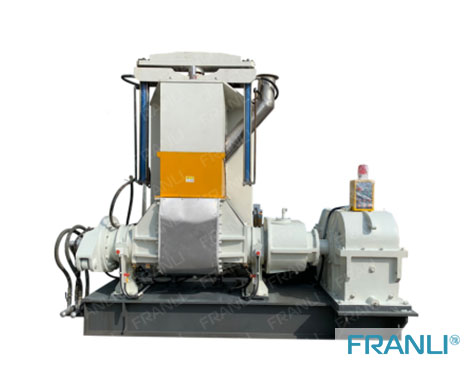
Dispersion Kneader
The dispersion kneader is suitable for the mastication of rubber and plastics, and the mixing of various rubber materials and plastics.
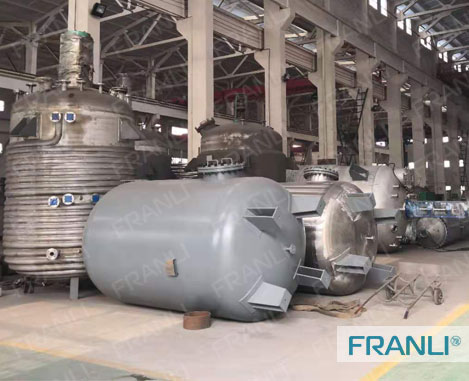
Industrial Chemical Reactor
The working principle of the industrial chemical reactor is that the reaction solvent can be put into the inner layer for stirring reaction, and the interlayer can be passed through different cold and heat sources (refrigerated liquid, hot water, or hot o
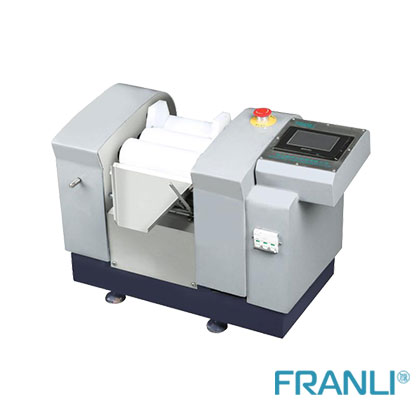
Ointment Mill
The ointment mill is also called Lab three roll mill. It is mainly used for the fine grinding of high-viscosity liquid slurries such as various paints, coatings, plastics, etc.
News
Laboratory Reactor: Guide to Stirring System
The laboratory reactor is composed of a pot body, a pot cover, an agitator, a jacket, a support and transmission device, a shaft seal device, etc.
Grinding Media for Bead Mill | Zirconia Beads & Zirconium Silicate Beads
Bead mills mainly use grinding balls as media, and use impact, extrusion, and friction to achieve the final grinding effect, which mainly depends on the size and hardness of the grinding beads, the filling rate of the grinding beads, and the collision frequency adjustment between the grinding beads and the particles.
Overview of Laboratory Reactor
Laboratory reactors, also known as lab reactors, are essential tools in scientific research, product development, and process optimization. These reactors provide a controlled environment for conducting chemical reactions, mixing, dispersing, and homogenizing processes.
Bead mills | Manufacturing technology in various industries
Bead mills, also known as sand mills or grinding mills, are versatile machines widely used across various industries for the wet grinding and dispersion of solid particles in liquid media.
Ribbon Blender Mixer Equipment
A ribbon blender mixer, also known as a ribbon mixer or horizontal ribbon blender, is a powerful industrial machine designed for thorough and efficient blending of various materials.
What is A Stainless Steel Reactor?
Stainless steel reactors are essential equipment in various industries, including chemical, pharmaceutical, biotechnology, and food processing.