Home » Comparison of the vertical sand mill and horizontal sand mill
Comparison of the vertical sand mill and horizontal sand mill
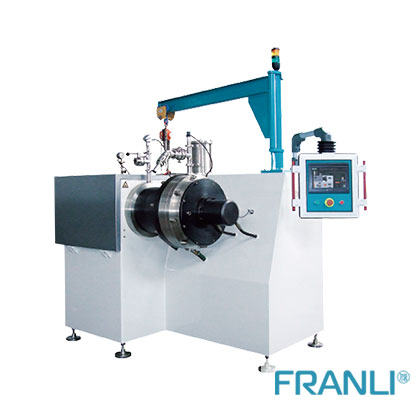
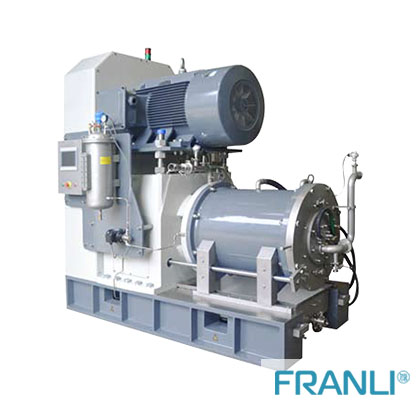
According to the layout of the grinding drum, it can be divided into vertical sand mills and horizontal sand mills. These are two very common styles. Next, we will learn more about the characteristics, advantages, and working principles of the two sand mills.
The vertical sand mill is mainly composed of a feed system, grinding drum, grinding disc, transmission, and electric control system.
Working principle of vertical sand mill
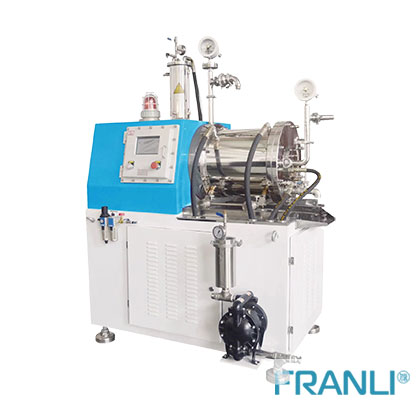
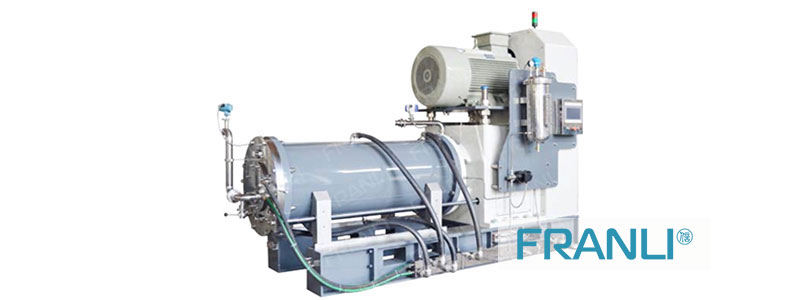
Vertical sand mill VS horizontal sand mill
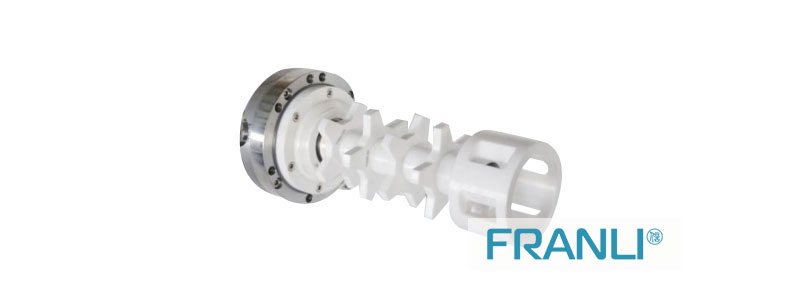
• Manufacturing difficulty
• Material
In terms of manufacturing difficulty and manufacturing cost, vertical sand mills have more advantages. In addition, the vertical sand mill does not take up space, and the operation is very convenient, which is suitable for materials with various viscosities. If you have a small budget or do not have high requirements for the fineness of the material, the vertical sand mill will be a very cost-effective choice.
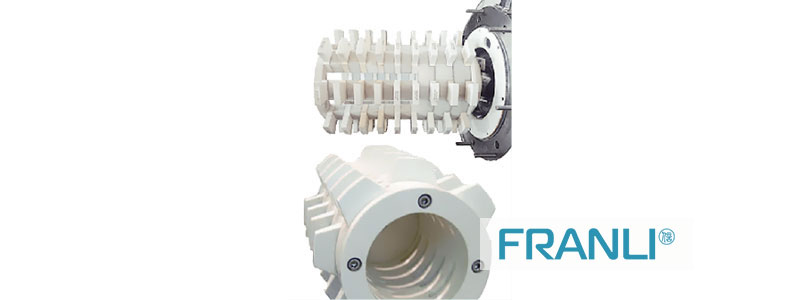
• Grinding fineness
The grinding medium (beads) in the vertical sand mill is affected by gravity and tends to accumulate to the bottom of the grinding cavity, resulting in a less uniform particle size distribution of the ground material, resulting in a better grinding effect at the bottom than at the top. This is like a bucket of stones, the stones on the bottom of the bucket are ground finer than those on the top of the bucket.
The horizontal sand mill can well overcome the influence of gravity on the medium. Because the feed of the horizontal sand mill is generally from the left to the right, the grinding force of the material in the barrel is the same, the particle size distribution of the output material will be more uniform, and the grinding fineness is generally up to 1μm.
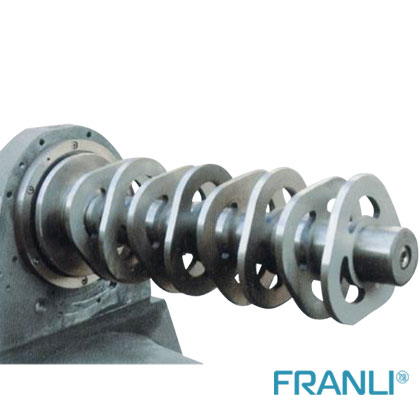
• The cost
• Scope of application
At present, sand mills are developing in the direction of large batches, refinement, high purity, and low energy consumption. Equipment maintenance is the key to extending the life of mechanical products, and it is also related to the stability and efficiency of production. Understand the common faults of sand mills and their solutions to reduce production losses caused by unnecessary equipment downtime.
Copyright Notice :
This article only represents the author’s point of view.
This article is published under the authorization of the author.
Source: Franli
This article address : The connection between ink and sand mill
Related Products
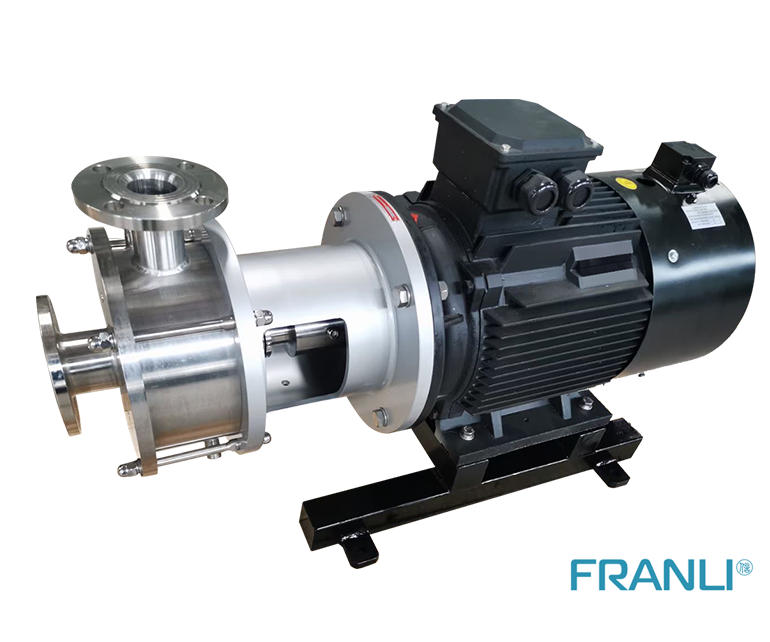
Inline Homogenizer
The Inline homogenizer is mainly used for mixing and homogenizing materials, dispersing, and emulsifying, and it is versatile and versatile. The inline homogenizer is generally used as a primary and intermediate material for mixing, and homogenizing.
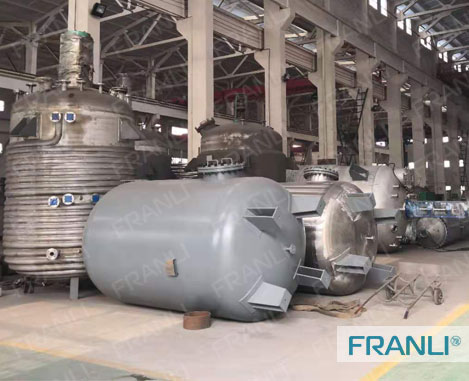
Industrial Chemical Reactor
The working principle of the industrial chemical reactor is that the reaction solvent can be put into the inner layer for stirring reaction, and the interlayer can be passed through different cold and heat sources (refrigerated liquid, hot water, or hot o
News
Laboratory Reactor: Guide to Stirring System
The laboratory reactor is composed of a pot body, a pot cover, an agitator, a jacket, a support and transmission device, a shaft seal device, etc.
Grinding Media for Bead Mill | Zirconia Beads & Zirconium Silicate Beads
Bead mills mainly use grinding balls as media, and use impact, extrusion, and friction to achieve the final grinding effect, which mainly depends on the size and hardness of the grinding beads, the filling rate of the grinding beads, and the collision frequency adjustment between the grinding beads and the particles.
Overview of Laboratory Reactor
Laboratory reactors, also known as lab reactors, are essential tools in scientific research, product development, and process optimization. These reactors provide a controlled environment for conducting chemical reactions, mixing, dispersing, and homogenizing processes.
Bead mills | Manufacturing technology in various industries
Bead mills, also known as sand mills or grinding mills, are versatile machines widely used across various industries for the wet grinding and dispersion of solid particles in liquid media.
Ribbon Blender Mixer Equipment
A ribbon blender mixer, also known as a ribbon mixer or horizontal ribbon blender, is a powerful industrial machine designed for thorough and efficient blending of various materials.
What is A Stainless Steel Reactor?
Stainless steel reactors are essential equipment in various industries, including chemical, pharmaceutical, biotechnology, and food processing.