Home » Application of bead mill in the printing ink industry
Application of bead mill in the printing ink industry
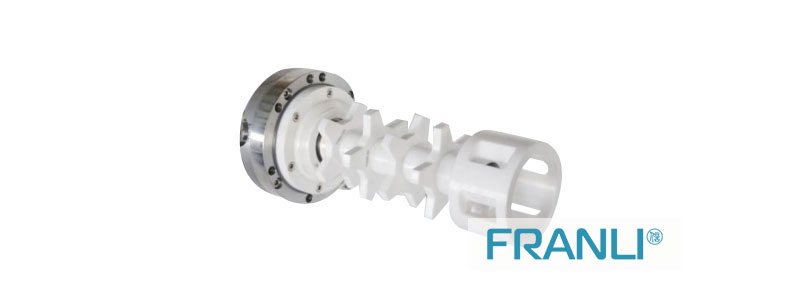
Different types of ink used bead mills in different structures
Rotary offset printing inks generally use vertical rod type (5—130 liters) or horizontal disc type bead mills (60 to 500 liters), while the production of ultra-high viscosity sheet-fed inks often uses high energy density cone bead mills or three roll mills.
Inkjet inks (inks and pigment solvent-based inks) generally use high-energy-density pin-type (horizontal or vertical) bead mills and turbo-centrifugal nano-bead mills.
The new bead mill is the main grinding and dispersing equipment in the ink production process. The bead mill is a fully enclosed grinding equipment with automatic feeding, automatic temperature, and pressure control devices, and can carry out continuous production operations.
When the bead mill is running, the rotor agitates the meson (beads) to move at a high speed, and the high-speed running medium and the grinding cavity plays a role of dispersion through impact, friction, and shear. The vertical bead mill is a fully enclosed type, which can continuously grind and disperse granular and non-granular solid materials in liquid.
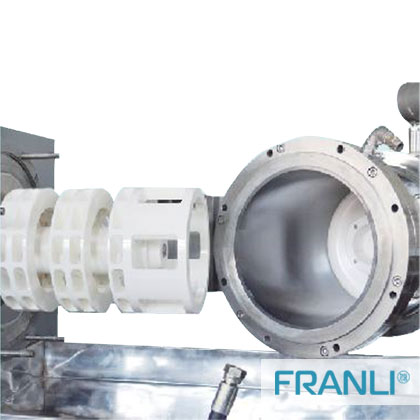
The structure and characteristics of the bead mill are:
When grinding materials, it will generally grind several times according to the fineness requirements of the final product. The setting pressure of the three roll mill is usually increased one by one to ensure that the wetting and dispersing process of the agglomerated particles is a “gradual” process. So it is more stable and controllable.
The structure and characteristics of the bead mill are:
②The annular groove on the stator can meet the different requirements of the product, and the high-precision special isolation groove can be used for the special viscosity.
③The temperature, pressure, feed pump flow rate of the rotor and stator are automatically displayed, and there are protection devices such as temperature and pressure.
④The grinding efficiency and dispersion degree can be obtained by adjusting the flow rate of the feed pump and the filling amount of the beads.
⑤Due to the use of special and latest technical materials, the grinding area and the isolation area are particularly wear-resistant, and will not affect the hue of the material.
⑥Bead mills usually have safety self-locking and alarm devices, and some faults can be automatically eliminated.
Copyright Notice :
This article only represents the author’s point of view.
This article is published under the authorization of the author.
Source: Franli
This article address : Application of bead mill in the printing ink industry
Related Products
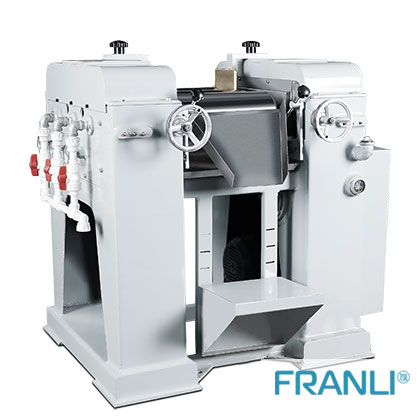
TRS-Three Roll Mill For Lipstick
TRS Three roll mill is widely used in milling paste material including paint, inks, China ink, pigment, coatings, food, cosmetics, and so on.
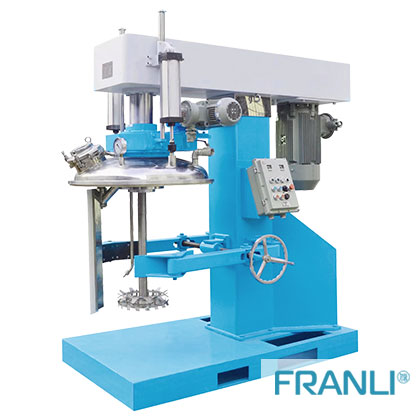
Twin Shaft Disperser
The Twin Shaft Disperser is composed of two sets of mixing devices. Different mixing devices can be designed according to different materials.
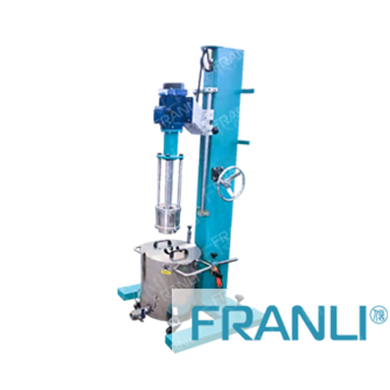
Lab Basket Mill
The lab basket mill is a common equipment for small-scale experiments and scientific research. Suitable for wet grinding of medium and low viscosity materials. It integrates dispersion, grinding, and integration.
News
Laboratory Reactor: Guide to Stirring System
The laboratory reactor is composed of a pot body, a pot cover, an agitator, a jacket, a support and transmission device, a shaft seal device, etc.
Grinding Media for Bead Mill | Zirconia Beads & Zirconium Silicate Beads
Bead mills mainly use grinding balls as media, and use impact, extrusion, and friction to achieve the final grinding effect, which mainly depends on the size and hardness of the grinding beads, the filling rate of the grinding beads, and the collision frequency adjustment between the grinding beads and the particles.
Overview of Laboratory Reactor
Laboratory reactors, also known as lab reactors, are essential tools in scientific research, product development, and process optimization. These reactors provide a controlled environment for conducting chemical reactions, mixing, dispersing, and homogenizing processes.
Bead mills | Manufacturing technology in various industries
Bead mills, also known as sand mills or grinding mills, are versatile machines widely used across various industries for the wet grinding and dispersion of solid particles in liquid media.
Ribbon Blender Mixer Equipment
A ribbon blender mixer, also known as a ribbon mixer or horizontal ribbon blender, is a powerful industrial machine designed for thorough and efficient blending of various materials.
What is A Stainless Steel Reactor?
Stainless steel reactors are essential equipment in various industries, including chemical, pharmaceutical, biotechnology, and food processing.