Home » How Ointment Mill Works With Your Own Eyes
How Ointment Mill Works With Your Own Eyes
Ointment Mill Grinders are the essential need for industries which have larger exports around the universe. The following describes instruments that can measure the roll separating force, torque, and the magnitudes of the front and rear tube tensions.
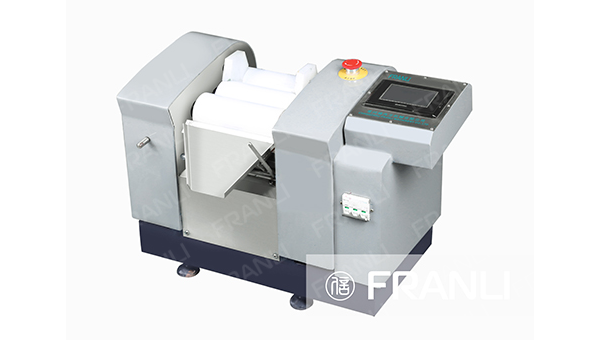
Ointment mill
Ointment Mill Liner Materials
Mining mineral resources by the crusher, mill ore deep processing of fine magnet separation, and roasting can significantly improve their utilization of Pre-crusher and fine processing equipment for various types of milling equipment. The development of large quantities of minerals processing trends will require that crusher, mill product production, and processing efforts have greater levels of improvement. This led the crusher and mill production enterprises to increase technology research and development and introduce more efficient milling machinery.
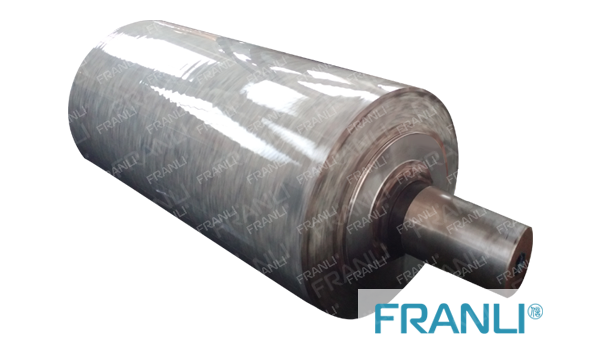
ointment mill roller
Energy-saving Ointment Mill
The ball mill is an important piece of equipment for regrinding. It is widely used to grind cement, silicate products, new building material, fireproof material, chemical fertilizers and black and nonferrous metals, glass, ceramics, and other materials.
This Ointment Mill has two warehouses and is horizontally type with a tubular running system. This machine is grid-type, and its outside runs in gear. The material enters the first warehouse through a spiral arrangement. There is a scale board (or ripple scale board) in this warehouse. Different steel balls of different specifications are installed on this scale board. When the barrel body turns, it produces centrifugal forces. The steel ball is then carried to a height and falls to cause the material to grind or strike. After being ground coarsely in the first warehouse, the material is moved to the second warehouse, where it will be reground with the steel ball or skateboard. Finally, the powder is ejected by the output material board, and the final products are ready.
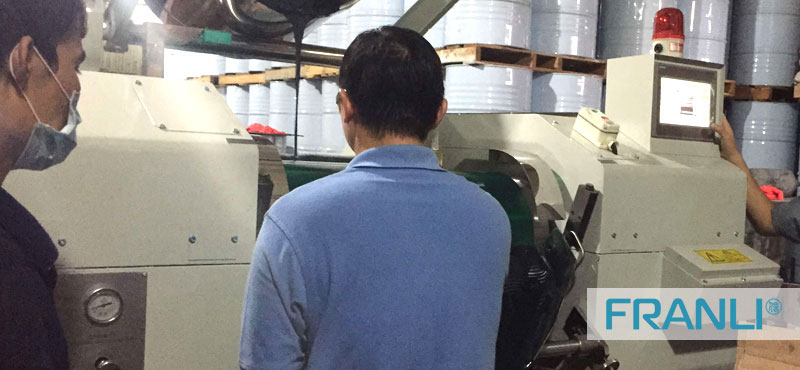
On-site explanation of three roll mill
Ball mill benefits and features
Ball mill
Rod mill
Franli hopes that these will provide useful information. It is shown how to design the optimal roll drive configuration. This article discusses the design details of the mechanical drive system for a single-stand stand. Also, the arrangements to apply constant front and back tensions for the tube regardless of the tube speed. This single-strand design mimics the behavior of a single stand in multi-strand production lines. It is also indicated in the design of the roll groove profile.
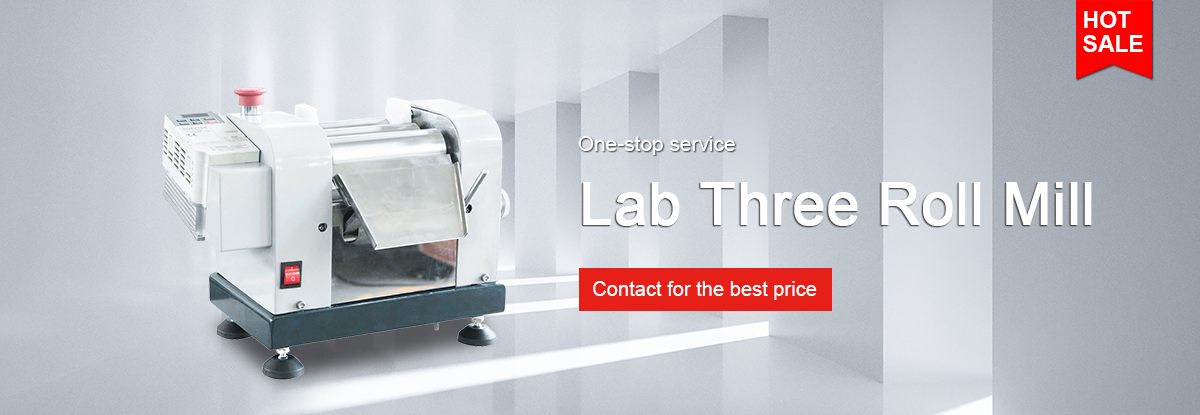
Copyright Notice :
This article only represents the author’s point of view.
This article is published under the authorization of the author.
Source: Franli
This article address: What is a bead mill?
Related Products
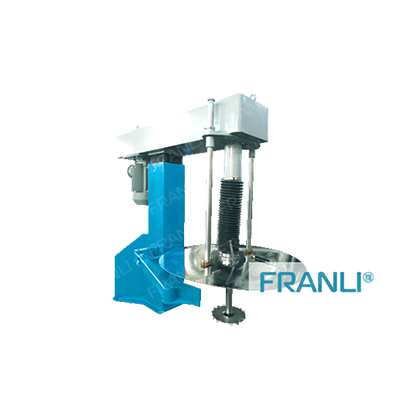
Hydraulic Lifting High Speed Disperser
The hydraulic lift high speed disperser has the characteristics of simple operation and high flexibility. The hydraulic lifting high speed disperser is suitable for the production of paints, inks, coatings, dyes, papermaking, etc.
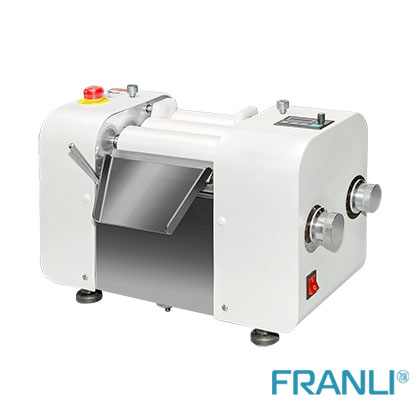
3 Roll Mill: Manual, Hydraulic, Lab
3 Roll Mill is a great tool that is used to mix, refine, and disperse any material through three horizontal rolls situated opposite sides with different speeds.
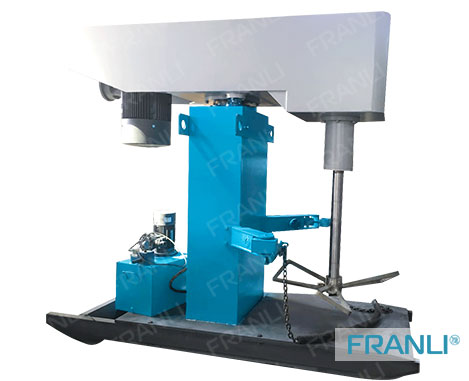
Butterfly Disperser
This kind of butterfly mixer is used in offset ink, putty etc industry. The butterfly dispersing mixer is a product with the functions of dispersing and stirring (wall scraping) developed on the basis of a single-axis hydraulic lifting disperser.
News
Laboratory Reactor: Guide to Stirring System
The laboratory reactor is composed of a pot body, a pot cover, an agitator, a jacket, a support and transmission device, a shaft seal device, etc.
Grinding Media for Bead Mill | Zirconia Beads & Zirconium Silicate Beads
Bead mills mainly use grinding balls as media, and use impact, extrusion, and friction to achieve the final grinding effect, which mainly depends on the size and hardness of the grinding beads, the filling rate of the grinding beads, and the collision frequency adjustment between the grinding beads and the particles.
Overview of Laboratory Reactor
Laboratory reactors, also known as lab reactors, are essential tools in scientific research, product development, and process optimization. These reactors provide a controlled environment for conducting chemical reactions, mixing, dispersing, and homogenizing processes.
Bead mills | Manufacturing technology in various industries
Bead mills, also known as sand mills or grinding mills, are versatile machines widely used across various industries for the wet grinding and dispersion of solid particles in liquid media.
Ribbon Blender Mixer Equipment
A ribbon blender mixer, also known as a ribbon mixer or horizontal ribbon blender, is a powerful industrial machine designed for thorough and efficient blending of various materials.
What is A Stainless Steel Reactor?
Stainless steel reactors are essential equipment in various industries, including chemical, pharmaceutical, biotechnology, and food processing.