Home » The development of sand mills in the coating industry
The development of sand mills in the coating industry
In recent years, the rapid development of the coating industry in various countries has exposed some urgent problems that need to be solved. Such as overcapacity, rapid growth, outstanding safety, and environmental protection issues, increased energy constraints, and arduous tasks in energy conservation and emission reduction.
Therefore, coating companies are speeding up the elimination of old products and backward technologies, and continue to invest in research and development of high-performance, high-quality, and high-value-added new products that meet environmental protection requirements. The requirements of energy conservation and environmental protection have prompted coating companies to upgrade their equipment and provide them with new development opportunities.
Taking paint sand mills as an example, most coating equipment companies no longer produce open vertical paint sand mills with severe solvent volatilization and excessive noise. Instead, they follow the trend of environmental protection and vigorously develop closed paint sand mills. The feeding, dispersion, grinding, matching, and packaging of the closed-circuit production process are also regarded as the development direction of the industry.
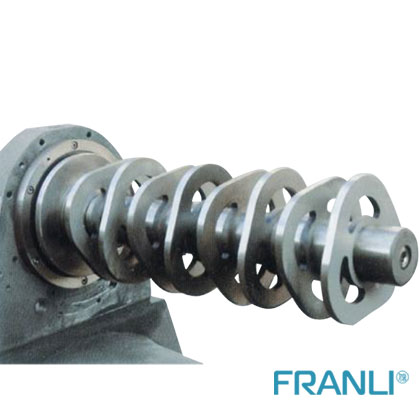
In addition, due to the wide application field and scope of liquid coatings, many coating companies have more stringent requirements for the use of sand mills. As the most influential new media information service platform in the coatings industry, after an in-depth understanding of the pain points of the sand mill industry, the coating procurement network selected a company with stable performance and no prolonged downtime, good sealing, and not easy to leak and block; internal structure (such as Screens, separation systems, etc.) are reasonably designed to effectively ensure that the ground materials meet the accepted standards of high precision and purity, to provide valuable reference cases for coating companies that need to purchase sand mills.
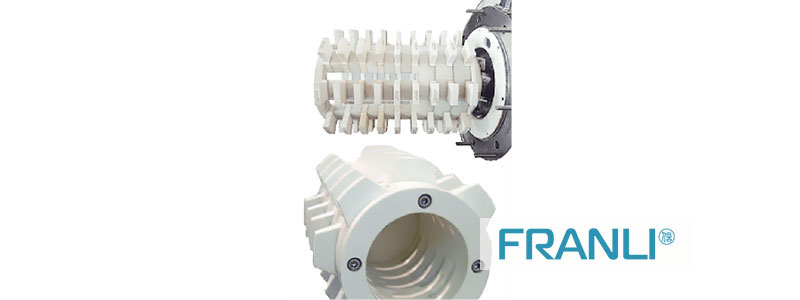
Rod-pin type high-efficiency nano-sand mill series products are suitable for sub-micron and nano-level grinding of materials, high-efficiency grinding structure, scientific energy density distribution, improve material grinding efficiency, make materials reach nano-level, and are widely used in nano-new materials, Ceramic ink, electronic ceramics, dyes, color pastes, pesticides, alumina, zirconia, and other industries.
The rod-pin type high-efficiency nano-sand mill performed well in the tomato pigment grinding test. The original particle size was 8um, and the particle size was reduced to about 700 nm after one cycle, which realized the particle size for customers by reducing the wear on the core parts of the machine. Acceptance target with diameter less than 1um. So, why does its “charm” improve efficiency and solve the problem of fineness to make customers favor it?
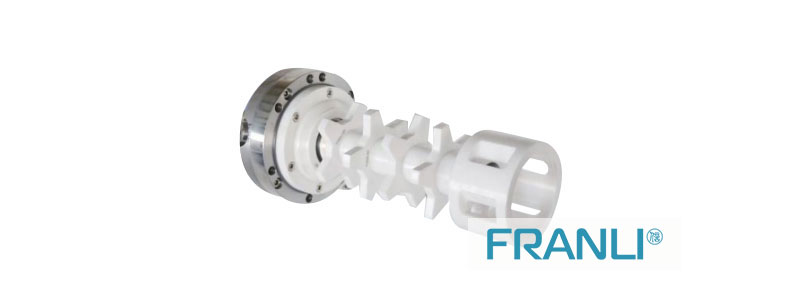
It is reported that the compact structure design makes the product easy to operate, practical, and beautiful; the rod-pin structure design, the rotor rod pin produces a strong impact on the grinding medium and acts on the material, and the material is forced to grind and disperse to achieve rapid and fine grinding of the material.
The advanced large-flow separation screen structure ensures high-efficiency production without clogging; the integrated double-end mechanical seal can select lubricants according to the material characteristics; the high wear-resistant grinding inner cylinder and the disperser can be easily replaced, and the materials are alloy steel, ceramics, Polymer, stainless steel, and other options; spiral water circulation channels, multi-part cooling water settings, excellent heat dissipation performance; full explosion-proof button control and scientific PLC touch screen control are optional; feed pressure, discharge temperature, machine Multi-part safety control such as the liquid level of the lubricating oil tank.
Copyright Notice :
This article only represents the author’s point of view.
This article is published under the authorization of the author.
Source: Franli
This article address : The development of sand mills in the coating industry
Related Products
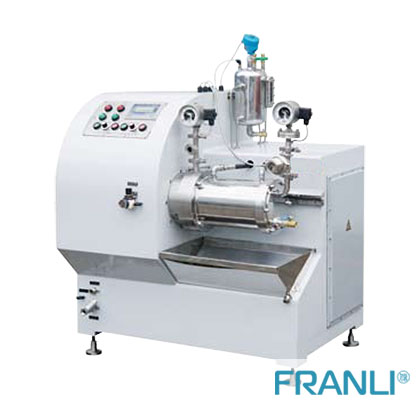
Bead Mill Machine
Bead mill machine is a microscopic and nanotechnology grind and dispersion device. The particulates are ground and/or distributed by the collisions and friction stress of the beading within the bottom chamber.
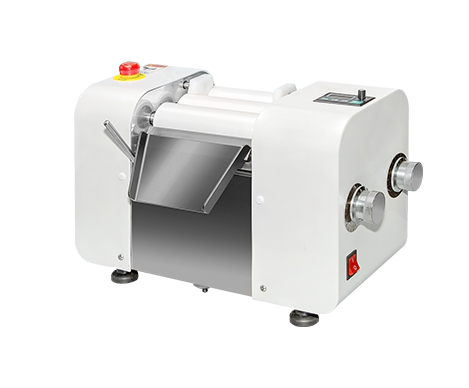
Ceramic Three Roll Mill
The ceramic three roller mill mainly uses the surface of three rollers to grind and disperse at different speeds to make the ground material reach the required grinding fineness. The three roller mill is suitable for the grinding of ink, paint, paint, lipstick, chocolate, soap, and other materials, and it is mainly composed of a roller, a machine base, a guide cover, a discharge knife plate, a feeding copper knife, a cooling system, etc. The fineness of the material grinding can be adjusted by the screw on the base.
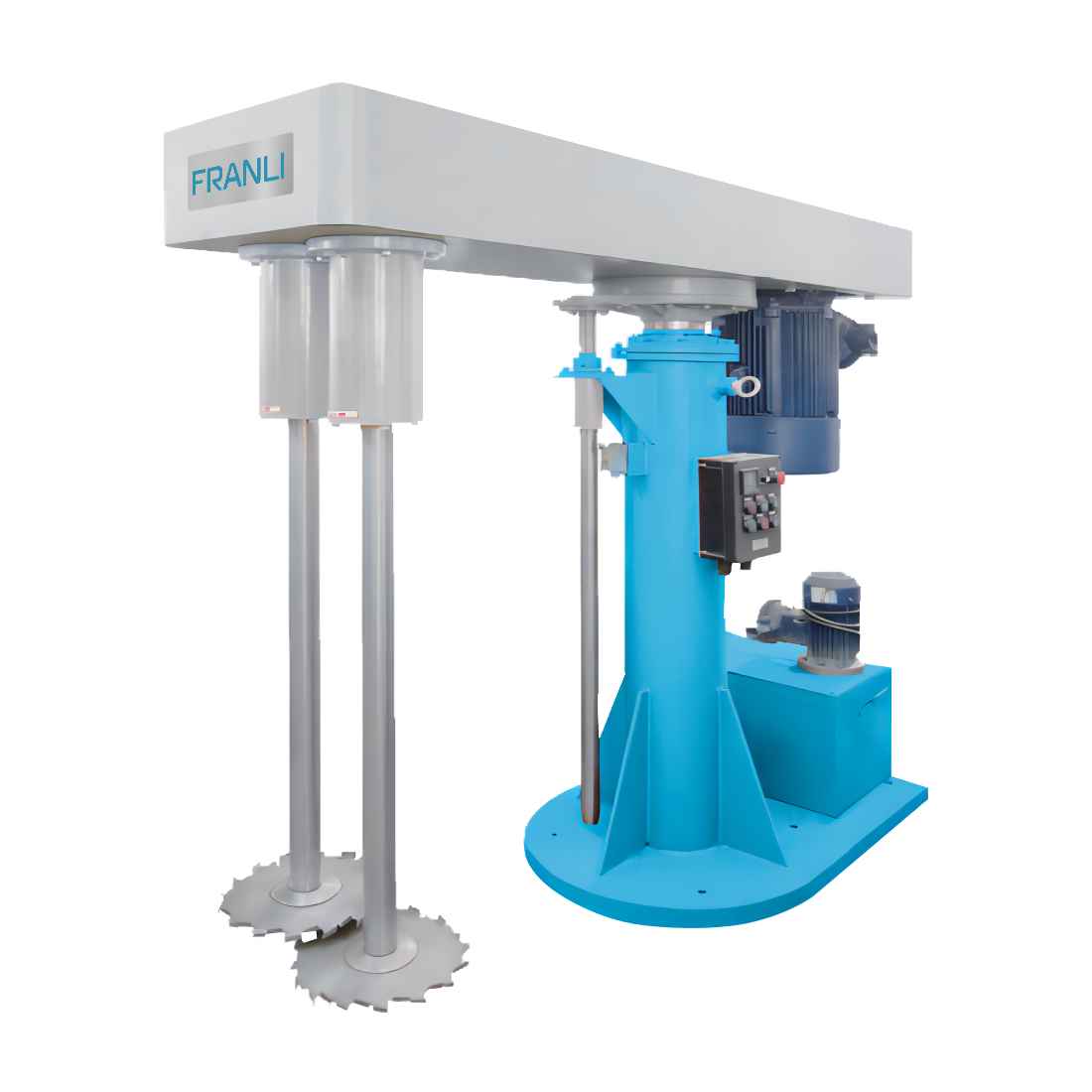
Dispersion Machine
This HSD-D Dispersion Machine with two shafts for mixing and dispersing materials to reach higher efficiency. This machine should be installed jacket tank with a cooling system. The dispersion machine has two shafts working temperature
News
Laboratory Reactor: Guide to Stirring System
The laboratory reactor is composed of a pot body, a pot cover, an agitator, a jacket, a support and transmission device, a shaft seal device, etc.
Grinding Media for Bead Mill | Zirconia Beads & Zirconium Silicate Beads
Bead mills mainly use grinding balls as media, and use impact, extrusion, and friction to achieve the final grinding effect, which mainly depends on the size and hardness of the grinding beads, the filling rate of the grinding beads, and the collision frequency adjustment between the grinding beads and the particles.
Overview of Laboratory Reactor
Laboratory reactors, also known as lab reactors, are essential tools in scientific research, product development, and process optimization. These reactors provide a controlled environment for conducting chemical reactions, mixing, dispersing, and homogenizing processes.
Bead mills | Manufacturing technology in various industries
Bead mills, also known as sand mills or grinding mills, are versatile machines widely used across various industries for the wet grinding and dispersion of solid particles in liquid media.
Ribbon Blender Mixer Equipment
A ribbon blender mixer, also known as a ribbon mixer or horizontal ribbon blender, is a powerful industrial machine designed for thorough and efficient blending of various materials.
What is A Stainless Steel Reactor?
Stainless steel reactors are essential equipment in various industries, including chemical, pharmaceutical, biotechnology, and food processing.