Home » Three roll mill for paint, new energy, electronic paste
Three roll mill for paint, new energy, electronic paste
Can bases, as well as coil coatings being produced through three roll mills, can be one of the best examples of the same. Three roll mills are also quite used when it comes to coating systems that are heat-sensitive in nature. Specifically, it’s the massive cooling surface, as well as significant temperature control of these three roll mills, that makes it suitable for coating systems that are heat-sensitive in nature.
Functionality of contemporary three rolls mills
Post-pre-dispersion, finer dispersing occurs over the three roll mills. In general, the three roll mills demand a couple or three passes in order to attain the desired size of particle or the desired characteristics regarding the colors. These three roll mills are mostly fed using the pumps. However, the biggest advantage of the three roll mill is certainly the cleanliness.
In fact, with ability to produce tiny batches of various colors, the level of productivity can be significantly grown. Apart from these, zero cross-contamination is also one of the key advantages. Very nominal level of hold-up, along with fixed stress, is also the crucial feature. Things have gone even more enchanting through the advent of automated systems in modern times. These are much superior in standard in comparison to traditional systems.
The primary function of three roll mills obviously is a distinguishing speed attained among three rolls. In fact, difference between number two and three rolls can be twice or four times superior in comparison to the difference between the initial and second rolls. Here the dispersion occurs at the second nip.
The initial nip handles the feeding of the second nip. However, the rolls need to be perfectly positioned. In those occasions where level of viscosity and product’s track is significant enough for generating pressure, it becomes essential for the rolls to get pressed together. When the level of viscosity is nominal or in case of the shear sensitivity cases, the rolls must not get pressed together.
It’s the differential speed as well as steady volume flow over the rolls that the initial and second nip possess identical ratios equivalent to that of the speed of roll. In short, when the rolls must be positioned due to a lower level of viscosity, the settings have to differ between the initial and the second one.
Superior flexibility
The dispersion occurs within the shear field on the roll length. Till when the size of the particle remains smaller in comparison to nip, the level of impact on the particles within the suspension remains zero. This aspect provides uniformity to the dispersing process. At the same time, it also makes it adjustable in terms of pressure or roll position. With the help of shear stress, the single-particle is not going to get hampered.
It means there is no change in shape, a certain surface, as well as the size of an irregular phase. This is crucial for various applications. Metal plates and ceramic pastes can be the best examples in this regard where it is not felt essential to alter the size of the particle or the surface of the ceramic within the suspension. Various raw materials remain in specification and must not get hampered through the course of dispersion, which means using explicitly the shear stress.
Optimized press mode makes it high on demand
Demand for three roll mills has significantly grown. Specifically, those mills with optimized pressure mode, as well as gap mode, are high on demand. Starting from those with mid-level to superior viscosity, these are useful everywhere. Modern-day three roll mills are capable of functioning on quite a nominal level line force on pressure mode or to straightaway change to gap mode. To operate three roll mills on gap mode basically is about positioning the rolls correctly and adjacently.
Traditional hydraulic cylinders do come with a comparatively higher level of internal friction. This turns things challenging to handle the line force at a lower level. In fact, it gets impossible on most occasions. However, contemporary machines are developed with friction of considerably lower levels. In fact, it is now possible to deal with line forces at even 3 N/mm.
Factors making it more powerful
The prime segment of roll pressing is the eccentric shaft. A massive angle of rotation of the shaft causes a nominal variation in position of the axes. This indicates superior accuracy in distance setting among the roll shafts. The shaft can increase the force to more than 20 times.
In short, a nominal force in roll pressing causes massive pressure among the rolls. This is the reason behind the greater use of pneumatic rather than hydraulic. Noteworthy here is that a pneumatic motor can alter the eccentric shaft angle that alters the gap between roll shafts, as well as the gap among the rolls.
While functioning with a gap, the control unit of the contemporary roll mills shifts the motors towards the setting valve. The machine is not capable of measuring the real gap among the rolls. Rather, it simply shifts the step motors onto a setting value that is meant for a specific position as far as roll shafts are concerned. Calibration of increment occurs when the machine starts, which indicates that the rolls are mildly touching or the pressure level is nominal.
All said and done, it is evident that the modern-day three roll mills make it apparent that the technology can really make it big in forthcoming future. Greater ability of cleaning, superior flexibility, and higher accuracy can make this equipment much more significant than ever. Most importantly, these roll mills encourage the process of scaling up. Starting from small-scale units to larger scale ones, these machines can be convenient on all occasions.
Franli can be the one-stop destination for all those looking for quality three roller mills. They can provide various models of high-end three roll mill, assuring smooth functioning and better cleaning.
Copyright Notice :
This article only represents the author’s point of view.
This article is published under the authorization of the author.
Source: Franli
This article address:Three roll mill for paint, new energy, electronic paste sand mill
Related Products
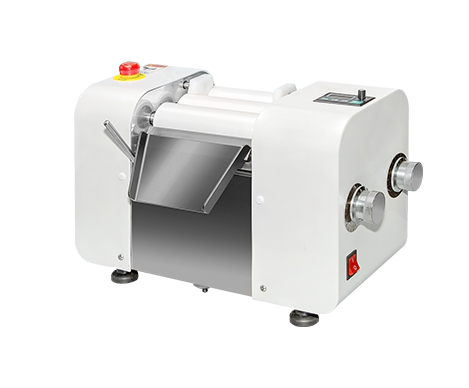
Ceramic Three Roll Mill
The ceramic three roller mill mainly uses the surface of three rollers to grind and disperse at different speeds to make the ground material reach the required grinding fineness. The three roller mill is suitable for the grinding of ink, paint, paint, lipstick, chocolate, soap, and other materials, and it is mainly composed of a roller, a machine base, a guide cover, a discharge knife plate, a feeding copper knife, a cooling system, etc. The fineness of the material grinding can be adjusted by the screw on the base.
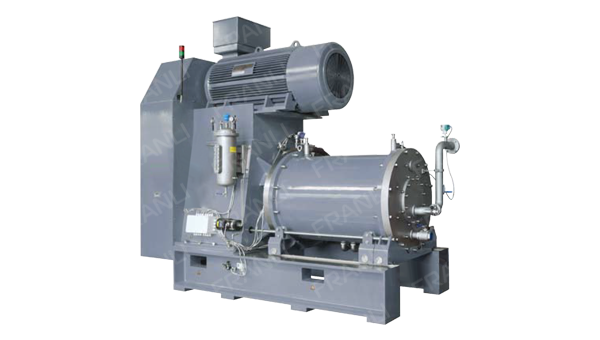
Agitator bead mill
Agitator bead mill’s pins are uniform distributed type, pre-milling your material when feeding material into chamber. The agitator bead mill has a stronger power motor, material milled by bead, and pins in the chamber.
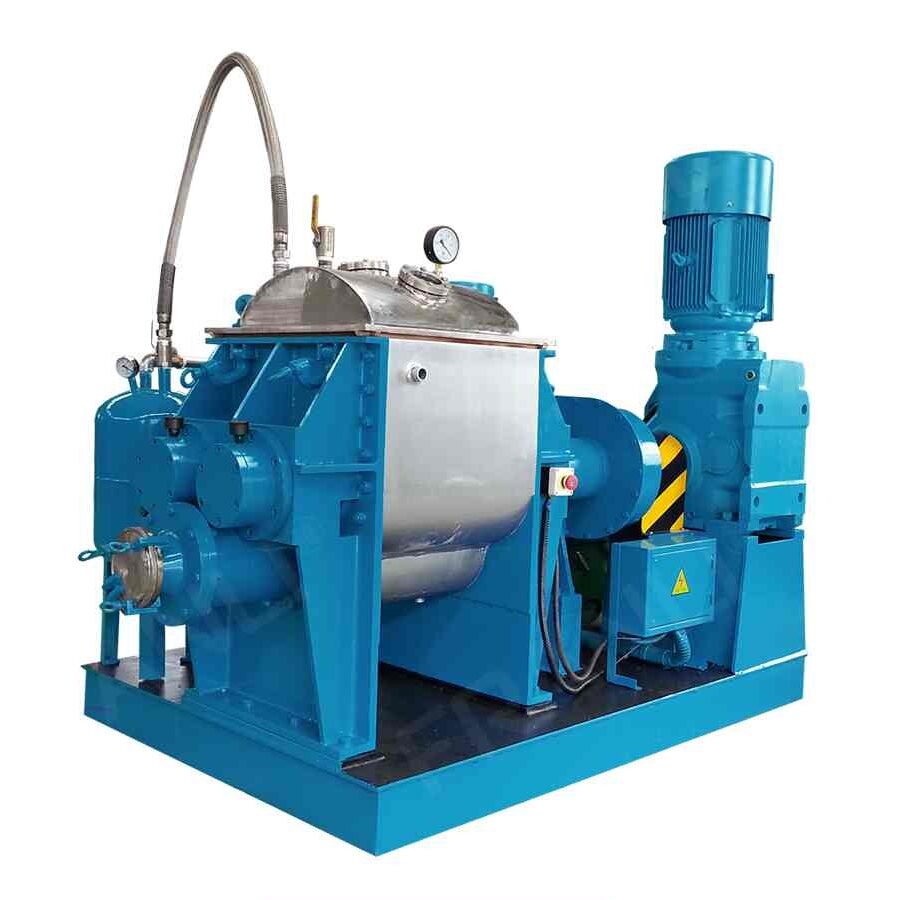
Z Blade Mixer
The Z blade mixer is made for extensive mixing, kneading, and stabilizing strong and high viscous materials, such as bubble gum bases, bread, caramel mass, body wash platform, and glue.
News
Laboratory Reactor: Guide to Stirring System
The laboratory reactor is composed of a pot body, a pot cover, an agitator, a jacket, a support and transmission device, a shaft seal device, etc.
Grinding Media for Bead Mill | Zirconia Beads & Zirconium Silicate Beads
Bead mills mainly use grinding balls as media, and use impact, extrusion, and friction to achieve the final grinding effect, which mainly depends on the size and hardness of the grinding beads, the filling rate of the grinding beads, and the collision frequency adjustment between the grinding beads and the particles.
Overview of Laboratory Reactor
Laboratory reactors, also known as lab reactors, are essential tools in scientific research, product development, and process optimization. These reactors provide a controlled environment for conducting chemical reactions, mixing, dispersing, and homogenizing processes.
Bead mills | Manufacturing technology in various industries
Bead mills, also known as sand mills or grinding mills, are versatile machines widely used across various industries for the wet grinding and dispersion of solid particles in liquid media.
Ribbon Blender Mixer Equipment
A ribbon blender mixer, also known as a ribbon mixer or horizontal ribbon blender, is a powerful industrial machine designed for thorough and efficient blending of various materials.
What is A Stainless Steel Reactor?
Stainless steel reactors are essential equipment in various industries, including chemical, pharmaceutical, biotechnology, and food processing.