Basket Mill Machine
What is a FRANLI Basket Mill? Our basket mill combines dispersing and grinding into a single machine that is suitable for grinding liquid materials with medium to low viscosity. It is a batch-type industrial production machine with an appropriate and reasonable basket structure that is simple to clean and change colors and varieties. A lab basket mill is an essential equipment for small batch production. The lifting structure uses an integrated hydraulic tank as an actuator, resulting in stable lifting, environmental friendliness, and no leakage. A basket Mill is an excellent grinding machine for a wide range of materials and colors. The machine has changed traditional production processing by combining dispersing and milling two processes into one, significantly shortening the production process. A Basket Mill is widely used in inks, paints coatings production, and also in other related industries.
Advantages of basket mill:
- Low energy
- No hot spots
- Controlling constant temperature
- Easy to use
Application

Coating

Cosmetic

Battery

Graphite

Agrochemistry

Adhesives
Hot sale basket mill
Guidelines For Basket Mill
Principle of Operation of a Basket Mill
Basket mills have a rotating basket that uses centrifugal force to accelerate the grinding media, similar to how passengers on an amusement park ride lean against a wall while the ride rotates at high speeds. Unlike the ride, which simply holds passengers in place, the basket has a disc with pegs to allow for grinding.
The basket’s top, bottom, and sides are perforated to allow the product to enter. The grinding disc is attached to a shaft that is centered in the basket drive shaft in the center of the basket. This inner shaft is braked to keep the disc from rotating along with the beads and product. The sieve basket revolves around the stationary grinding disc. The grinding beads fill the basket to about 80% to 85% of its volume. The centrifugal force compresses the beads against the grinding disc as the basket rotates. The shearing forces for dispersion are generated by the fixed disc, moving bead mass, and rotating basket. Turbulence is created by the blocks mounted to the top and bottom of the basket, as well as the grinding disc, to allow for greater shearing force. For coatings dispersions, steel, glass, or ceramic beads with a diameter of 1.2 mm for a smaller basket and 2 mm for a larger basket work best. However, the size of the beads is ultimately determined by the basket’s slot sizes.
Designing Mechanism of basket mill
Improvements in basket mill design have increased productivity and produced finer dispersion quality, with slot widths as small as 0.5 mm. The new design improves pumping rate and media compression performance significantly. A higher re-circulating rate is obtained by increasing the pumping rate through the basket. This means that the batch volume is processed more frequently through the basket, resulting in a narrower particle size distribution or a cleaner grind. The increased pumping rate also eliminates any settling issues that may have arisen in the process tank. The media compression zone is also increased in newer basket designs. One disadvantage of older designs was the size and shape of the basket. The basket was a solid cylinder with a large diameter and a narrow height. There are two potential issues with this design.
With very low-viscosity products, a high basket speed occasionally resulted in a vortex that entered only the basket’s periphery. This left the basket’s center empty and exposed to high frictional heat, resulting in premature media wear and, in some cases, a dried fused media slug that locked the basket against the stationary disc.
The second issue was with viscous materials, which tended to slide off the top and bottom plates and never enter the basket for dispersion. The top and bottom plates remain solid in updated designs. The hollow center of the basket, similar to a centrifugal pump, uses centrifugal force to force the material through the grinding area. The material is required to pass through the grinding zone. The turbulence created by the fixed rods attached to the fixed disc is provided by the fixed rods. This design allows for a significant increase in basket speed. Higher basket speed results in better batch circulating and media compression. A finer particle size distribution results from greater media compression. If a large vortex forms, there is no longer a problem because the center of the basket is now empty of grinding media.
Steps involved in Dispersion
Premixing: Premixing is the first step in achieving optimal coating dispersion. Premixing is, in fact, as important as any other milling operation. As with all basket mills, the product is premixed with a high-speed dissolver (HSD).
Priming: The premixed batch is delivered to the TopMill. The basket is lowered into the batch and cycled on and off several times. Air bubbles rise from the batch during this process. Priming the batch and pre-grinding the solids are critical steps in de-aeration to avoid a foamy batch.
Grinding: The basket is then set to run at full speed. The basket’s speed is controlled by a supplied Variable Frequency Drive (VFD), with the maximum speed determined by power consumption or vortex level. The batch size on a 50 horsepower machine, for example, can range from 45 to 220 gallons. When a smaller batch size is used, the basket speed slows down.
A larger batch size results in a faster basket speed and thus faster production. In the end, both small and large batches require roughly the same amount of time – one to four hours. One possible source of concern is that the material in the tank is not circulating through the basket. The basket acts as an impeller, similar to a high-speed dissolver. In the batch tank, the product flows in a vortex with the same characteristics as the HSD process. Higher viscosity products are handled by increasing the radius of the basket with pumping blades. The basket is removed from the batch once the desired grind quality has been achieved. At this point, the basket is briefly rotated to spin or centrifuge the majority of the remaining product from the basket. The batch yield is nearly 100% with this design. This reduces waste and the amount of cleaning required.
Fields of Application
Basket Mills are widely used in the production
- Paints for decoration (indoor & outdoor)
- Outdoor coatings with a textured surface.
- Coatings for industrial protection.
- Paint for road markings.
- Coatings for marine containers.
- Coatings and paints for the aerospace industry.
- The artist paints.
- Colorants.
- Coatings for coils and cans Liquid inks.
- Inks that are based on oil
- Chemicals used in construction
- Waterproof coatings.
- Sealants
- Chemicals used in construction
To know about more customized designs of basket mills, click this link to visit the official website of FRANLI – a manufacturer who specializes in selling different machines including lab basket mills.
Related production lines
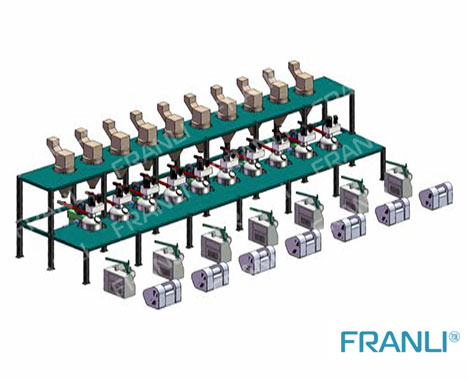
Offset Ink machine line
FRANLI is specialized in offset ink full line production for 20+ years. Helped customer save the cost, save the man power, also save the space.
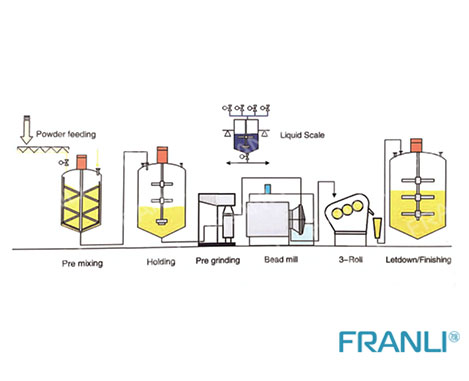
Offset Ink, UV Ink machine line
The FRANLI engineering company, offer the full set of UV INK Production Line, we can make the full drawing according with your factory size, formulas, weather and safety system.
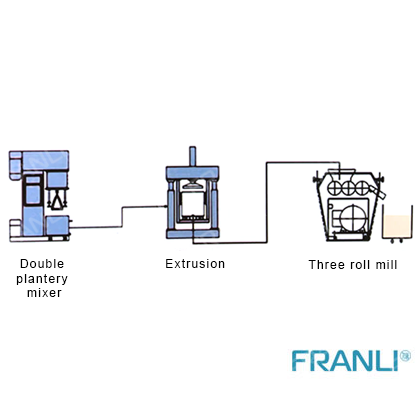
PCB INK Machine line
FRANLI supplies all equipments for the production of PCB inks, from the powder feeding station to the filling part.
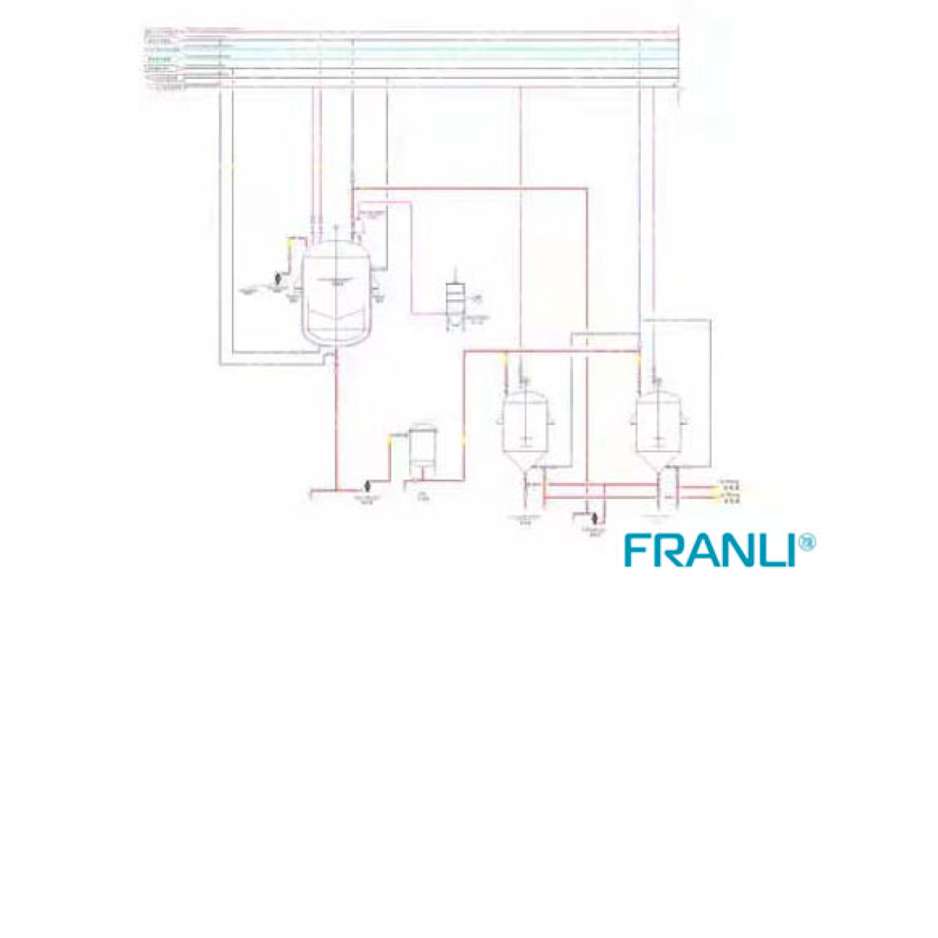
EW-pesticide line
The EW production line mainly mixes raw materials, solvents, and emulsifiers through a reactor (oil-based).
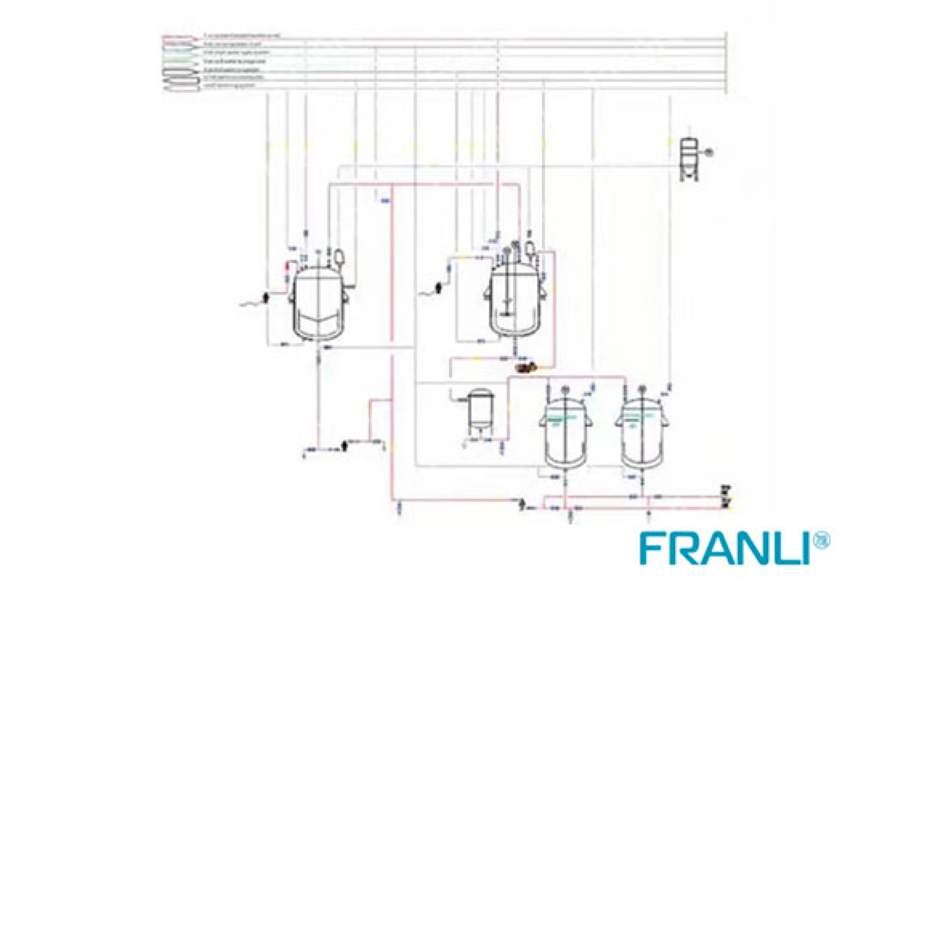
SL_EC pesticide line
The EC production line is mainly composed of an agitator mixer, bag filter, filling machine, etc.
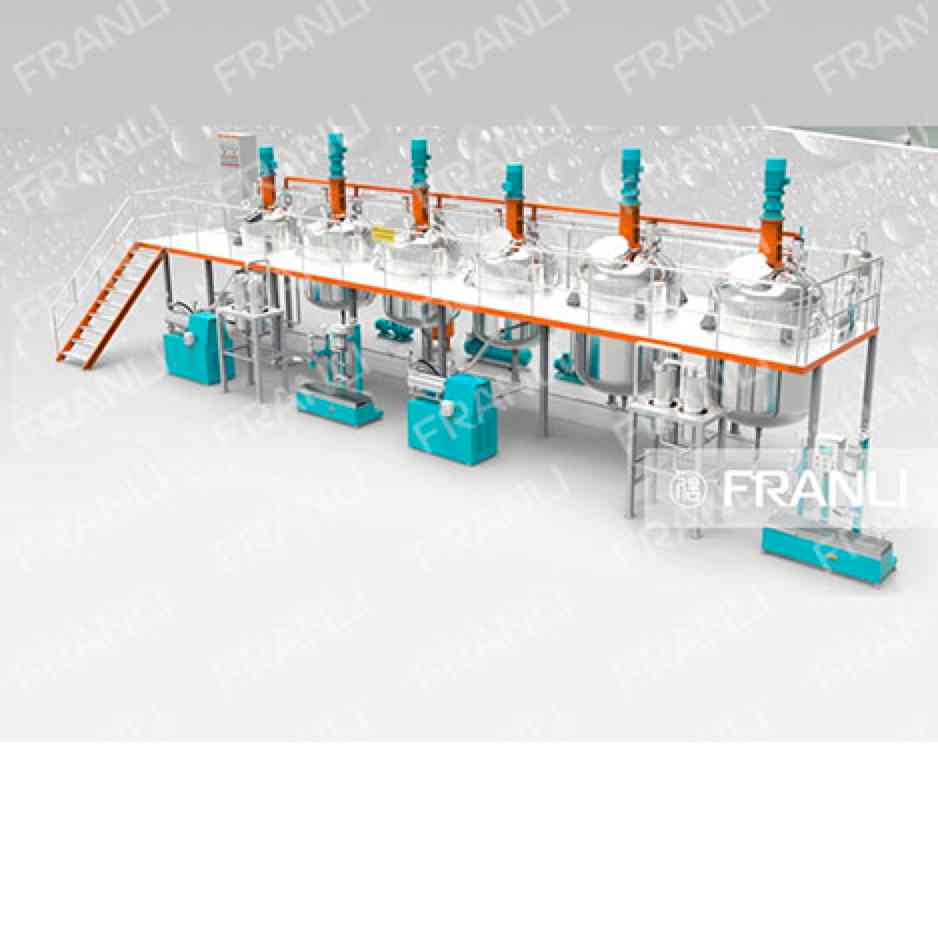
Automotive Paint machine line
The automotive paint machine line is mainly for the production and grinding of automotive paint, Automotive paint has many layers, such as Primer/electrophoretic layer, Medium coat, Colored coat, and Clearcoat.
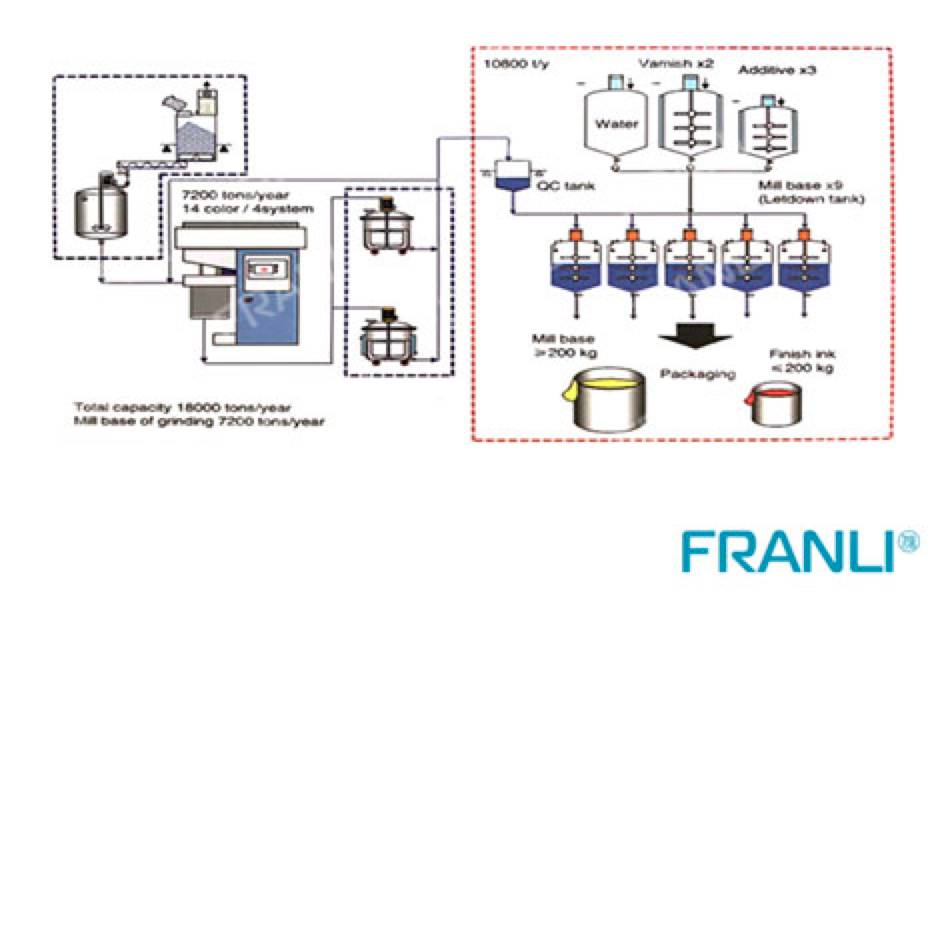
Digital Ink machine line
Franli has professional experience for digital ink machine line, we offered hundreds customers to expand production, or build up new project.