The advantage of the three roll mill instead of ball mill
Are you still using the ball mill process? It’s time to try out the three-roll mill.
It has been proved that in some applications, a Three Roll Mill can effectively replace the traditional ball milling process. Besides, it can also offer a great level of improvement in the overall throughput rate. What’s more? You will witness less amount of energy consumption and better production yield.
The three roll mill has emerged as an effective grinding as well as dispersing equipment to process high viscosity materials. As a result, the machine is widely used for grinding different types of liquid paste and paint materials, for example, plastics, pigments, inks, paints, rubber, ceramics, cosmetics, and more.
Some common issues that you can face while using the ball milling process
Well, there is no doubt that ball milling machines are quite easy to operate, and they are very versatile. In fact, some designs can be used for wet and dry feeds. However, the machines come with multiple drawbacks. For example, it performs a little slower than other milling machines. As a result, the throughput will be a little low. Besides, you may also deal with issues like clogging, higher energy consumption levels, and more. Furthermore, the machines are not easy to clean.
So, do you want to optimize the material milling process? Well, you can always go for a Three Roll Mill. Even though not all the applications that you can perform using a ball mill can be carried out by the three-roll milling, but this is perfect for slurries or pastes having moderate viscosity.
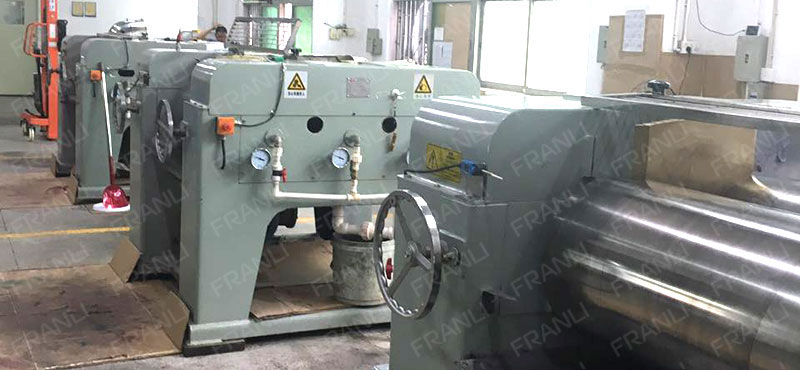
Understanding the theory of operation
Thanks to the adhesion. As the rollers move in a different direction, they create a perfect grinding action. In this machine, the rotational speed will gradually increase sequentially from one roller to another. The shear forces will develop dispersion. You can reduce the distance between the rollers to witness a huge shear, but it can lower the throughput. Once the material is ground or milled, it is scraped from the apron roller using a take-off knife.
In general, most of the roller material of the three roll mill is carefully cast from alloy cast iron. On the other hand, the surface harness will be around HS70 degrees. The roller’s diameter is very precise as well as delicate. As per the experts, using a good quality machine, you can attain a grinding fineness of 15μm.
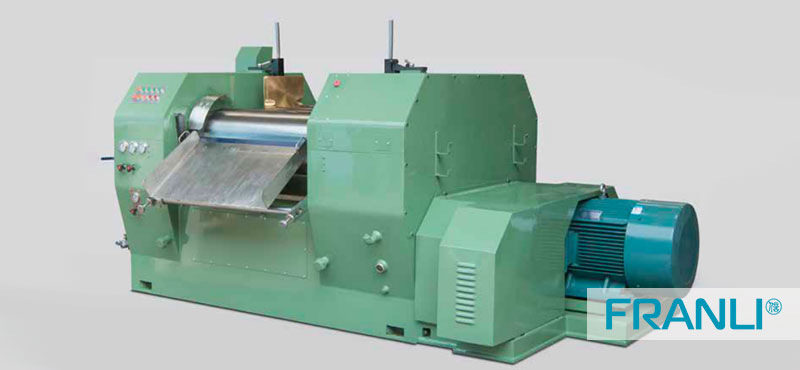
Is the product you are using three-roller mill material?
· You should always remember that the materials you want to use in the machine must have the right element of stickiness to them. As a result, the material will adhere to the roller surface perfectly and will transfer smoothly between the rollers. Before using the material, it is advisable to test it using a machine.
· Another thing you should remember is that a three-roll mill can’t handle powder or any solid material. It has been seen that some manufacturers add solvent to create a good level of wetness and make the material suitable for the machine.
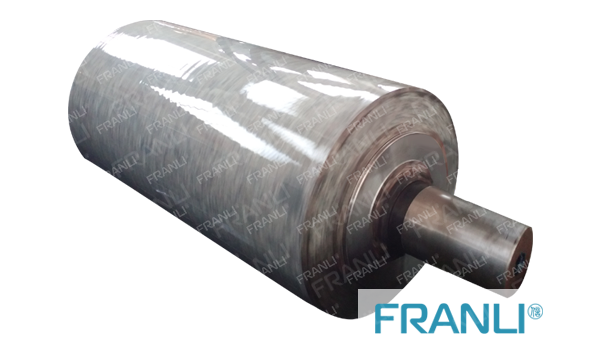
Understanding a sample application
The advanced three roll mill comes with a hydraulic system that can control different parts, such as a pressure roller, discharging blade, two sides holders, and more. As a result, the system can boost up the production capacity compared to other milling processes. There is no need to go through any complex setup process, and you can enjoy higher production.
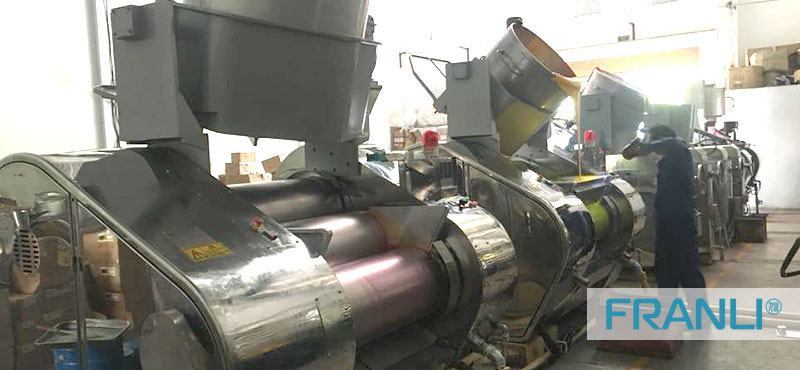
Franli brings you the best machine
Copyright Notice :
This article only represents the author’s point of view.
This article is published under the authorization of the author.
Source: Franli
This article address : What is a bead mill?
Related Products
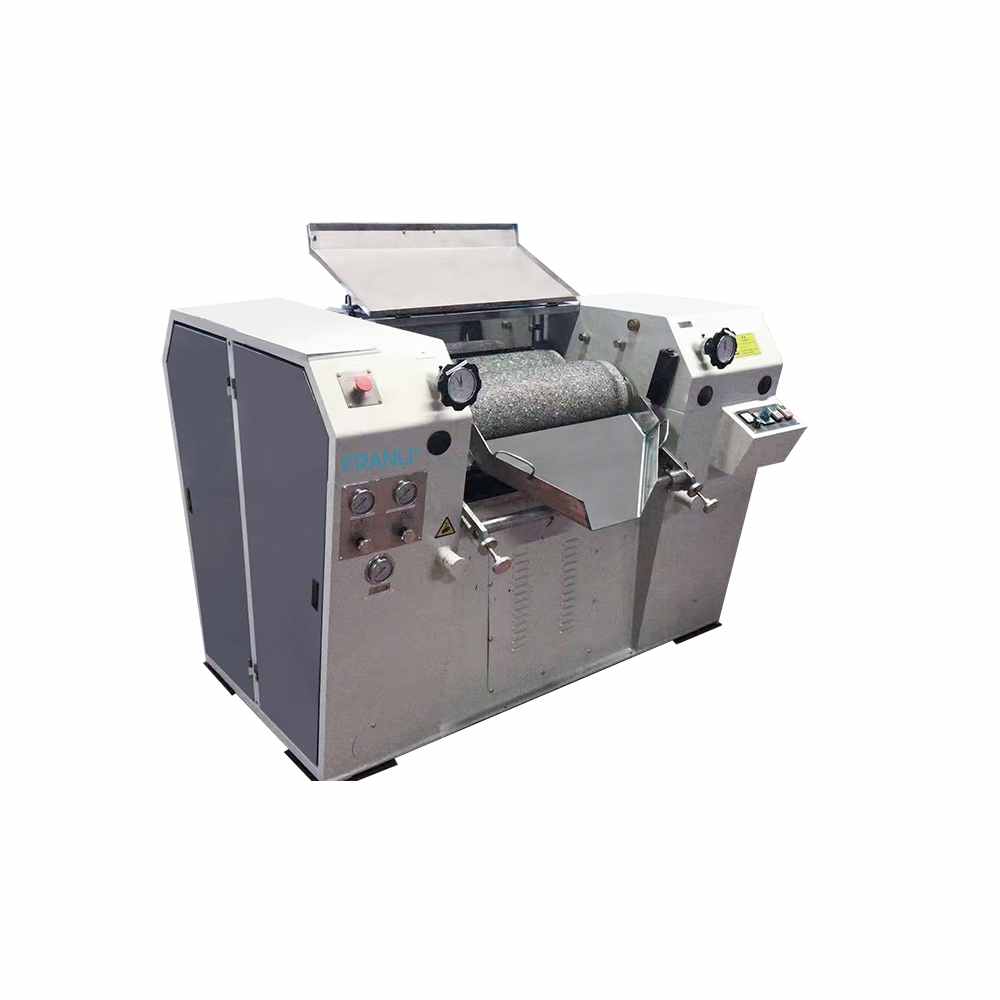
Granite Three Roll Mill
The granite three roll mill is suitable for the grinding of various art pigments, water-based colorants, pasty raw materials, chocolate, vanishing cream, cosmetic pigments, lipsticks, and other materials. It has its unique grinding effect.
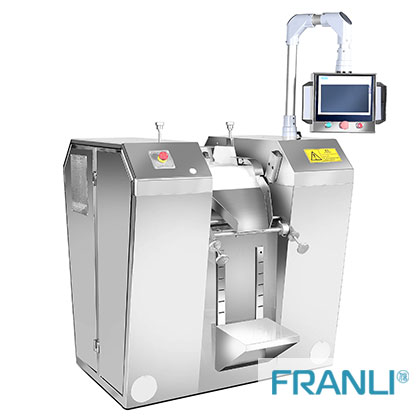
Hydraulic Three Roll Mill
FRANLI Hydraulic three roll mill has a unique Hydraulic system, which controls pressure roller, discharging blade, two sides holders, etc, which system can improve production capacity compared with normal same size three roll mill.
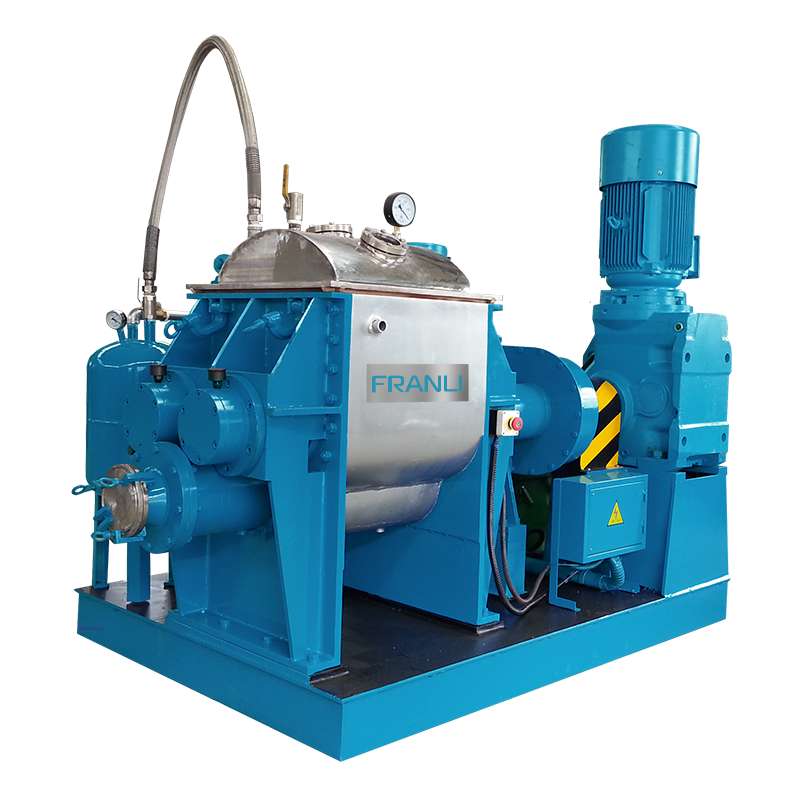
Vacuum Kneader
The vacuum kneader is an ideal equipment that is suitable for high-viscosity material, such as high-viscosity silicone rubber, sealant, gum, cellulose, etc. Also used widely in the Paint, ink, pigment, resin, battery, cosmetic, etc industries.
News
Laboratory Reactor: Guide to Stirring System
The laboratory reactor is composed of a pot body, a pot cover, an agitator, a jacket, a support and transmission device, a shaft seal device, etc.
Grinding Media for Bead Mill | Zirconia Beads & Zirconium Silicate Beads
Bead mills mainly use grinding balls as media, and use impact, extrusion, and friction to achieve the final grinding effect, which mainly depends on the size and hardness of the grinding beads, the filling rate of the grinding beads, and the collision frequency adjustment between the grinding beads and the particles.
Overview of Laboratory Reactor
Laboratory reactors, also known as lab reactors, are essential tools in scientific research, product development, and process optimization. These reactors provide a controlled environment for conducting chemical reactions, mixing, dispersing, and homogenizing processes.
Bead mills | Manufacturing technology in various industries
Bead mills, also known as sand mills or grinding mills, are versatile machines widely used across various industries for the wet grinding and dispersion of solid particles in liquid media.
Ribbon Blender Mixer Equipment
A ribbon blender mixer, also known as a ribbon mixer or horizontal ribbon blender, is a powerful industrial machine designed for thorough and efficient blending of various materials.
What is A Stainless Steel Reactor?
Stainless steel reactors are essential equipment in various industries, including chemical, pharmaceutical, biotechnology, and food processing.