Important Factors for Selecting a Three Roll Mill
What Are Three Roll Mills?
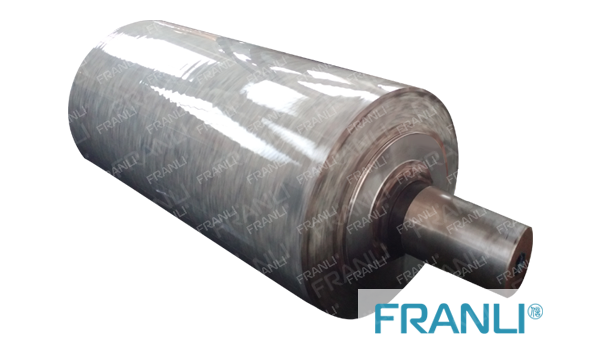
The roller part of the three roll mill
Brands and Sizes of three roll mills
Over 95% of the three roll mills in North America presently in production are limited to a few brands. The notable mentions include ANTHONY, DAY, KENT, ROSS, BUHLER, and LEHMANN. Some of the other notable brands include COX, INQUE, MOLTENI, MERCURY, and GERMAN LEHMANN.
Additionally, you could also find many other independent and reputed manufacturers of TRMs from India, China, and Korea. The three-roll mills by these brands differ in terms of size according to the area of application. TRMs can be applicable for lab and pilot projects as well as small production, mid-production, and large production use cases.
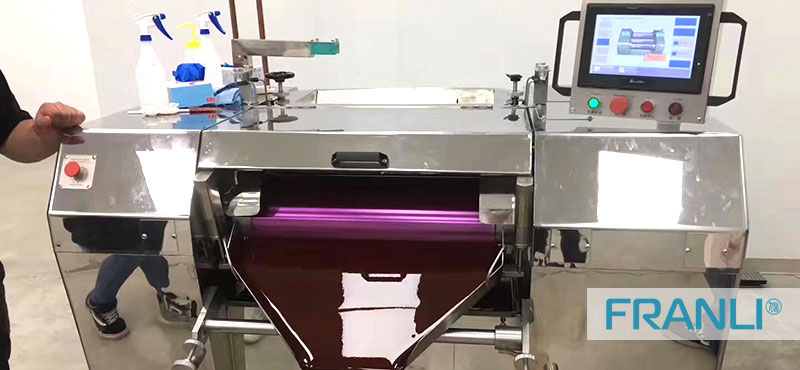
three roll mill
Endplate Systems
· DAY-style endplates
· ANTHONY-style endplates
· KENT-style endplates
When you are trying to look for three roll mills, you need to take note of the endplate systems. The different endplate systems serve distinct use cases, and you can choose the TRMs on the basis of your requirements. Let us take an overview of the types of endplates you can find in three roll mills.
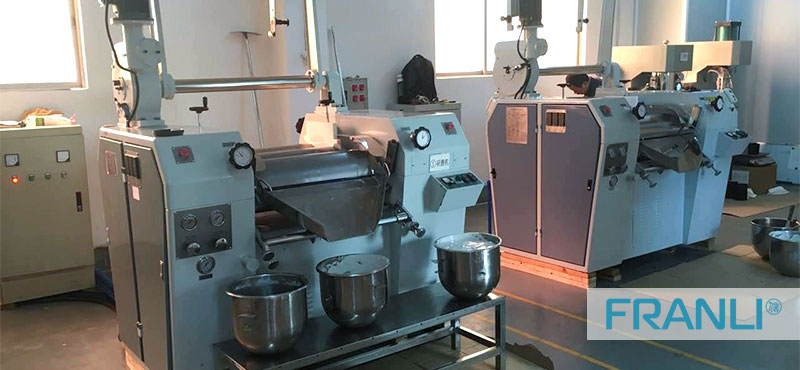
three roll mill
DAY-style Endplates
ANTHONY-style Endplates
KENT-style Endplates
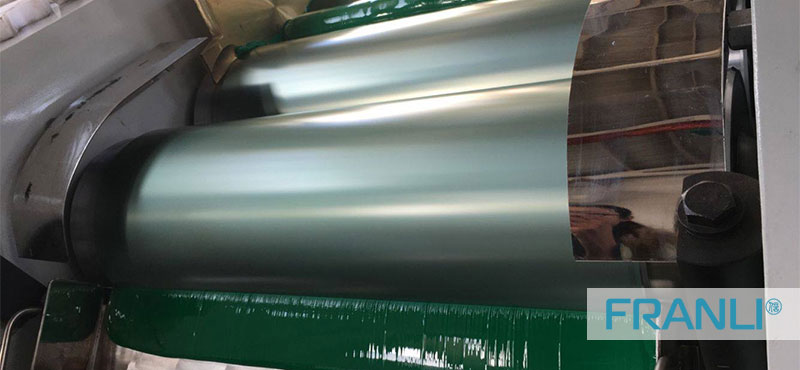
Three roll mill at work
Configurations of the Roll
On the other hand, the vertical configuration needs lesser floor space in comparison to inclined configuration. The inclined and vertical configurations have their in-running nip at a lower level than the horizontal configured TRM. The basic underpinning for this specification is the support for easier feeding of product to the feed nip at a lower level.
As you can notice, the choice of three roll mills can be quite difficult. However, you have the flexibility of choosing from different choices which are tailored for different applications. If you want to find the best three roll mills for your chemical or industrial manufacturing or processing plant, Franli can help you find the ideal choices. Contact now for consultation regarding your requirements and identifying the suitable pick among three roll mills for you. Grab the chance to own a revolutionary piece of industrial equipment right now!
Copyright Notice :
This article only represents the author’s point of view.
This article is published under the authorization of the author.
Source: Franli
This article address : Important Factors for Selecting a Three Roll Mill
Related Products
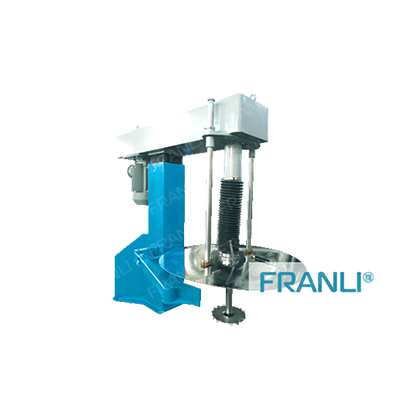
Hydraulic Lifting High Speed Disperser
The hydraulic lift high speed disperser has the characteristics of simple operation and high flexibility. The hydraulic lifting high speed disperser is suitable for the production of paints, inks, coatings, dyes, papermaking, etc.
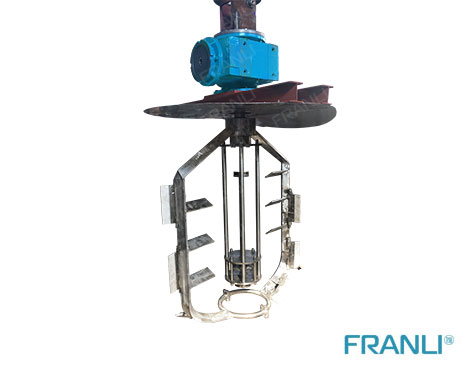
Platform Twin Shaft Disperser
This platform twin shaft disperser also named concentric double-shaft multi-function mixer, which is an industrial-grade model developed by FRANLI based on the concentric double-shaft mixer, which integrates powerful mixing, dispersion or emulsification,
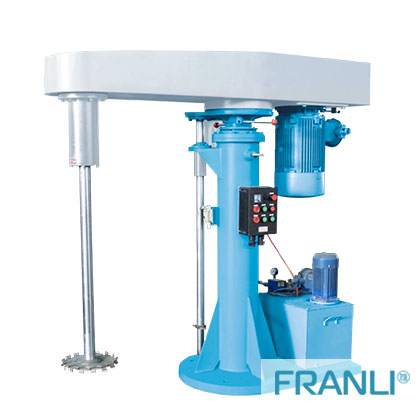
HSD High Speed Disperser
FRANLI high-speed disperser is widely used in coatings, paints, dyes, inks, latex paints, adhesives, papermaking, silica gel, putty powder, color pastes, and other chemical industries, and it can be used with three-roll mills, bead mills, and reactors.
News
Laboratory Reactor: Guide to Stirring System
The laboratory reactor is composed of a pot body, a pot cover, an agitator, a jacket, a support and transmission device, a shaft seal device, etc.
Grinding Media for Bead Mill | Zirconia Beads & Zirconium Silicate Beads
Bead mills mainly use grinding balls as media, and use impact, extrusion, and friction to achieve the final grinding effect, which mainly depends on the size and hardness of the grinding beads, the filling rate of the grinding beads, and the collision frequency adjustment between the grinding beads and the particles.
Overview of Laboratory Reactor
Laboratory reactors, also known as lab reactors, are essential tools in scientific research, product development, and process optimization. These reactors provide a controlled environment for conducting chemical reactions, mixing, dispersing, and homogenizing processes.
Bead mills | Manufacturing technology in various industries
Bead mills, also known as sand mills or grinding mills, are versatile machines widely used across various industries for the wet grinding and dispersion of solid particles in liquid media.
Ribbon Blender Mixer Equipment
A ribbon blender mixer, also known as a ribbon mixer or horizontal ribbon blender, is a powerful industrial machine designed for thorough and efficient blending of various materials.
What is A Stainless Steel Reactor?
Stainless steel reactors are essential equipment in various industries, including chemical, pharmaceutical, biotechnology, and food processing.