Home » What Is A High Shear Mixer?
What Is A High Shear Mixer?
The high shear mixer is a kind of emulsification homogenizer, which can be said to be an upgraded version of the emulsifier. In the material processing industry, a series of operations such as mixing, emulsification, dispersion, dissolution, and reaction are generally inseparable from mixing equipment such as high shear mixers. For operators of high shear mixers, it is very important to be familiar with relevant parameters such as equipment performance, characteristics, installation, and application.
The relevant parameters of the high shear mixer that users need to know are the following:
working principle of High Shear Mixer:
The high shear mixer is mainly for the emulsification of two immiscible materials. In the whole operation process, the material enters the body, the operator sets the degree of emulsification, and the rotor in the body rotates at a high speed to generate a high tangential speed. Here based on the high-frequency mechanical effect, the reacted material is fixed between the stator and the rotor. At the same time, under the strong shearing force brought by the mechanical operation, centrifugal extrusion is generated to realize the friction between the material and liquid layers. Under a series of comprehensive operations, two incompatible materials can be dispersed and emulsified, which is the working principle of the emulsifier.
Equipment performance and characteristics:
Device application:
Copyright Notice :
This article only represents the author’s point of view.
This article is published under the authorization of the author.
Source: Franli
This article address : What Is A High Shear Mixer?
Related Products
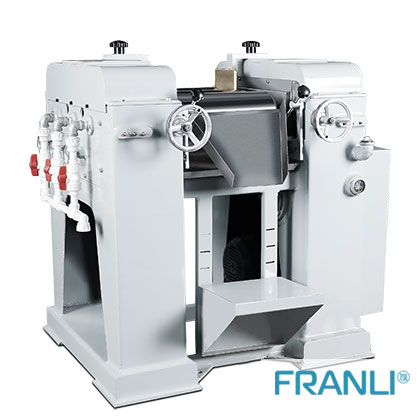
Manual 3 roll mill
FRANLI Manual three roll mill is widely used in milling paste material including paint, inks, China ink, pigment, coatings, food, cosmetics, and so on. (Not applicable for roller corrosion material). It is also used in cable material, artificial plastics, soap…
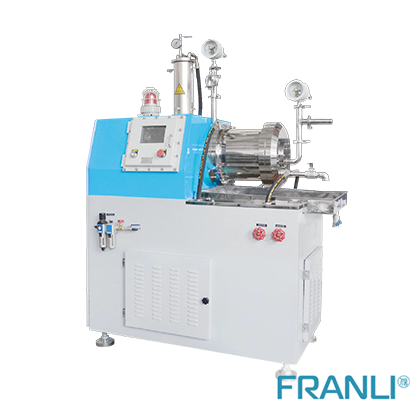
Turbine bead mill
FRANLI turbine bead mill is a kind of nano mill, which is mainly used in medicine, food industry, agrochemicals, cosmetics industry, papermaking, life sciences, microbiology, fillers, and other industries.
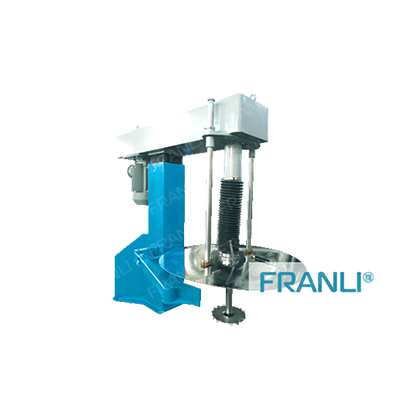
Hydraulic Lifting High Speed Disperser
The hydraulic lift high speed disperser has the characteristics of simple operation and high flexibility. The hydraulic lifting high speed disperser is suitable for the production of paints, inks, coatings, dyes, papermaking, etc.
News
Laboratory Reactor: Guide to Stirring System
The laboratory reactor is composed of a pot body, a pot cover, an agitator, a jacket, a support and transmission device, a shaft seal device, etc.
Grinding Media for Bead Mill | Zirconia Beads & Zirconium Silicate Beads
Bead mills mainly use grinding balls as media, and use impact, extrusion, and friction to achieve the final grinding effect, which mainly depends on the size and hardness of the grinding beads, the filling rate of the grinding beads, and the collision frequency adjustment between the grinding beads and the particles.
Overview of Laboratory Reactor
Laboratory reactors, also known as lab reactors, are essential tools in scientific research, product development, and process optimization. These reactors provide a controlled environment for conducting chemical reactions, mixing, dispersing, and homogenizing processes.
Bead mills | Manufacturing technology in various industries
Bead mills, also known as sand mills or grinding mills, are versatile machines widely used across various industries for the wet grinding and dispersion of solid particles in liquid media.
Ribbon Blender Mixer Equipment
A ribbon blender mixer, also known as a ribbon mixer or horizontal ribbon blender, is a powerful industrial machine designed for thorough and efficient blending of various materials.
What is A Stainless Steel Reactor?
Stainless steel reactors are essential equipment in various industries, including chemical, pharmaceutical, biotechnology, and food processing.