Home » Three Roll Mill: Grinding & Dispersing
Three Roll Mill: Grinding & Dispersing
Three roll mill is the most effective equipment for grinding and dispersing high viscosity materials. Three roll mills can be divided into lab three roll mills and production-type three roll mills. Mainly used in the production of paint, ink, pigment, plastic, and another slurry. Its working principle is to achieve the grinding effect through the surface extrusion of three horizontal rollers and friction at different speeds.
Features of three roll mill
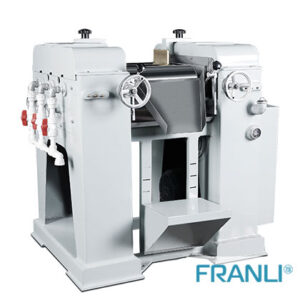
Minimum set-up spacing for three roll mills
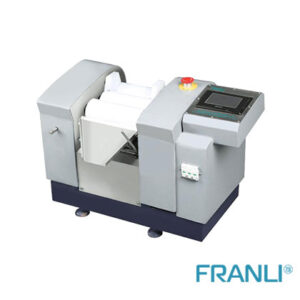
3 features of the three roll mill
Copyright Notice :
This article only represents the author’s point of view.
This article is published under the authorization of the author.
Source: Franli
This article address : Three Roll Mill: Grinding & Dispersing
Related Products
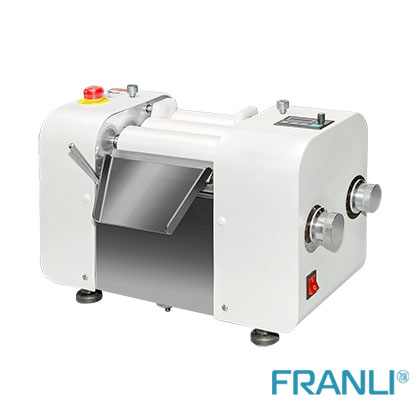
3 Roll Mill: Manual, Hydraulic, Lab
3 Roll Mill is a great tool that is used to mix, refine, and disperse any material through three horizontal rolls situated opposite sides with different speeds.
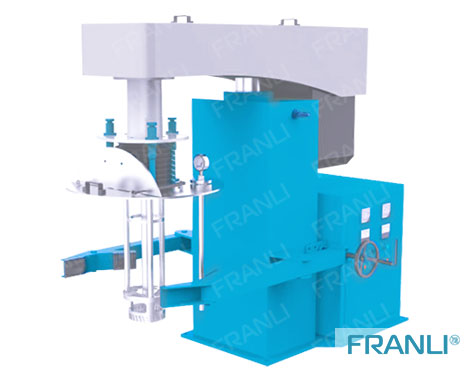
High Shear Mixer
High Shear Mixer is to disperse one or more phases into another continuous phase through efficient, fast, uniform and other processes, and under normal circumstances each phase is insoluble.
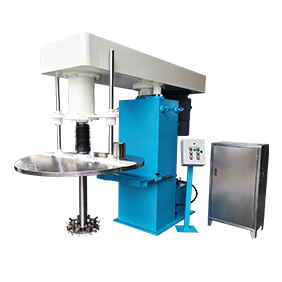
High Speed Disperser
Architectural waterproof coating production equipment The preparation process of the high-speed disperser machine mainly includes the dispersion of pigments and fillers, grinding, coating preparation, toning, etc.
News
Laboratory Reactor: Guide to Stirring System
The laboratory reactor is composed of a pot body, a pot cover, an agitator, a jacket, a support and transmission device, a shaft seal device, etc.
Grinding Media for Bead Mill | Zirconia Beads & Zirconium Silicate Beads
Bead mills mainly use grinding balls as media, and use impact, extrusion, and friction to achieve the final grinding effect, which mainly depends on the size and hardness of the grinding beads, the filling rate of the grinding beads, and the collision frequency adjustment between the grinding beads and the particles.
Overview of Laboratory Reactor
Laboratory reactors, also known as lab reactors, are essential tools in scientific research, product development, and process optimization. These reactors provide a controlled environment for conducting chemical reactions, mixing, dispersing, and homogenizing processes.
Bead mills | Manufacturing technology in various industries
Bead mills, also known as sand mills or grinding mills, are versatile machines widely used across various industries for the wet grinding and dispersion of solid particles in liquid media.
Ribbon Blender Mixer Equipment
A ribbon blender mixer, also known as a ribbon mixer or horizontal ribbon blender, is a powerful industrial machine designed for thorough and efficient blending of various materials.
What is A Stainless Steel Reactor?
Stainless steel reactors are essential equipment in various industries, including chemical, pharmaceutical, biotechnology, and food processing.