Home » Grinding media of different types of sand mills
Grinding media of different types of sand mills
The bead mill is used in the core stage of the production process in the coating and ink industry. Quality requirements from customers are becoming more and more demanding, and cost pressures are also increasing. The use of standard grinding methods has led to a continuous decline in profits, and the choice of cheaper raw materials will cause problems in the grinding process, such as clogging the screen, being out of range of particle size distribution, and longer grinding cycles. Saving production raw materials and pigments will lead to the opposite effect-increased costs and quality problems.
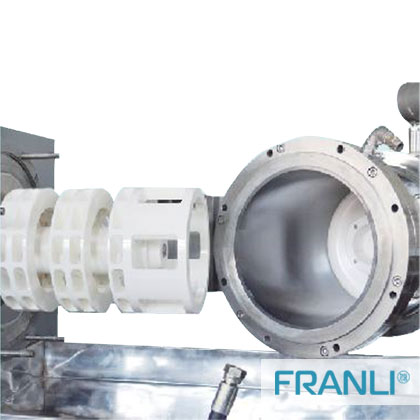
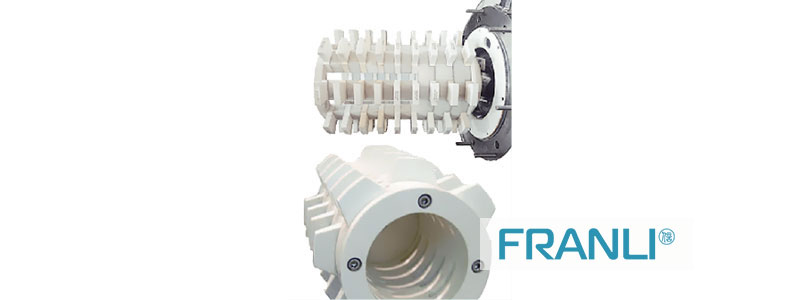
Advantages of using laboratory sand mill
• The residual amount is small, about 30ML in total.
• Easy to clean, it can be cleaned in 5min.
• High efficiency, each test is about 15min, the traditional test is about 4H; disassembly is convenient, about 5min, equipment disassembly, and zirconium bead replacement.
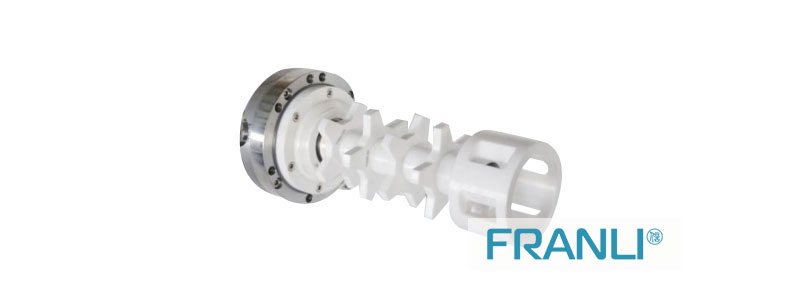
Selection of vertical sand mill media
But this must also consider the ink pumping speed because the ink is fed into the cylinder at a fast speed, the media will turn a little higher, so that there is more space above the media, that is, the amount of grinding media should be appropriately small a little.
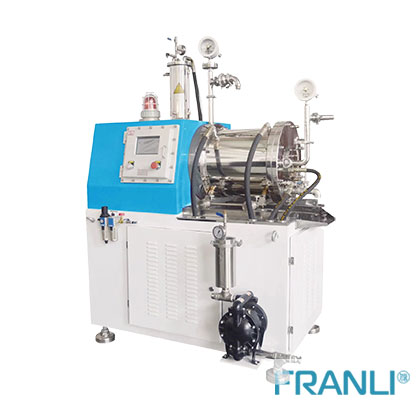
Selection of media for horizontal sand mill
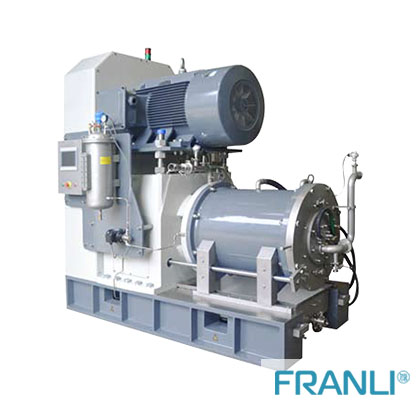
Sand mill is currently the most widely adaptable, most advanced, and most efficient grinding equipment. The grinding cavity is the narrowest, the gap between the levers is the smallest, and the grinding energy is the most intensive. With the high-performance cooling system and automatic control system, it can achieve continuous material Continuous processing and discharge greatly improve production efficiency.
In addition, no matter which kind of sand mill is used, the ink entering the sand mill must be well pre-dispersed so that the working efficiency of the sand mill can be brought into full play. Because the sheer force of the grinding media to break the pigment aggregates (or pigment particles) is inversely proportional to the size of the pigment aggregates between the media, that is, the smaller the pigment aggregates, the greater the shearing force between the media and the grinding And the dispersion effect is also the best.
Copyright Notice :
This article only represents the author’s point of view.
This article is published under the authorization of the author.
Source: Franli
This article address : Grinding media of different types of sand mills
Related Products
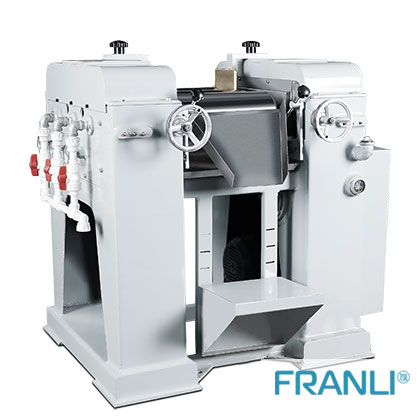
Manual 3 roll mill
FRANLI Manual three roll mill is widely used in milling paste material including paint, inks, China ink, pigment, coatings, food, cosmetics, and so on. (Not applicable for roller corrosion material). It is also used in cable material, artificial plastics, soap…
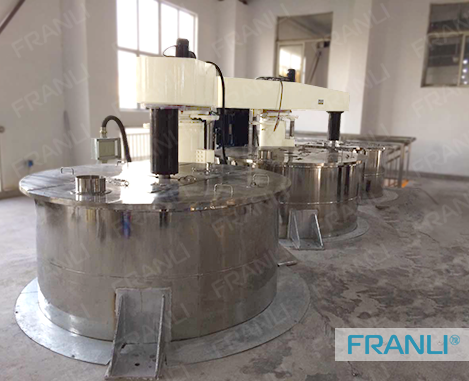
Platform Type High Speed Disperser
Platform type high-speed disperser is mainly used for high production material. Normally the high-speed disperser is installed between two tanks, easily mixing material in two tanks. also another type.
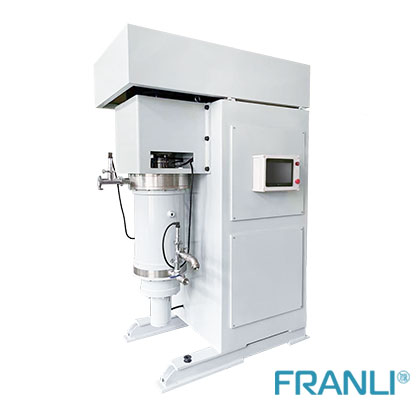
Vertical Bead Mill
Vertical Bead Mill has high viscosity material and low viscosity material. One for nano grinding material, another one for high viscosity material such as offset ink.
News
Laboratory Reactor: Guide to Stirring System
The laboratory reactor is composed of a pot body, a pot cover, an agitator, a jacket, a support and transmission device, a shaft seal device, etc.
Grinding Media for Bead Mill | Zirconia Beads & Zirconium Silicate Beads
Bead mills mainly use grinding balls as media, and use impact, extrusion, and friction to achieve the final grinding effect, which mainly depends on the size and hardness of the grinding beads, the filling rate of the grinding beads, and the collision frequency adjustment between the grinding beads and the particles.
Overview of Laboratory Reactor
Laboratory reactors, also known as lab reactors, are essential tools in scientific research, product development, and process optimization. These reactors provide a controlled environment for conducting chemical reactions, mixing, dispersing, and homogenizing processes.
Bead mills | Manufacturing technology in various industries
Bead mills, also known as sand mills or grinding mills, are versatile machines widely used across various industries for the wet grinding and dispersion of solid particles in liquid media.
Ribbon Blender Mixer Equipment
A ribbon blender mixer, also known as a ribbon mixer or horizontal ribbon blender, is a powerful industrial machine designed for thorough and efficient blending of various materials.
What is A Stainless Steel Reactor?
Stainless steel reactors are essential equipment in various industries, including chemical, pharmaceutical, biotechnology, and food processing.