Home » The use process of the three roll mill
The use process of the three roll mill
Under normal circumstances, the material of the roller of the three roll mill is the centrifugal casting of chilled cast iron, and the surface hardness is above HS70°; the diameter of the roller is high-precision grinding, which is precise and fine, and the grinding fineness of the material can reach 15um. Therefore, it is possible to produce uniform and fine high-quality products. SM405, S260 type.
Three roll mills are used for mass production, and models S150 and S65 are used for small batches or laboratory use.
1. Preparation of the three roll mill:
① Check whether the position and locking of each component are normal, inject lubricating oil according to the point shown in the figure and turn on the power
②Adjust the front, rear, left, and right handwheels to observe whether the roller linkage is normal
③Remove the dirt on the roller surface: wipe with soft paper or clean cotton yarn, release the knob of the baffle plate
④ Adjust the gap between the front and rear rollers and the middle roller to 0.5 mm and then start the power supply to idle for 1–2 minutes.
2. Working rules of the three roll mill:
①After starting the operation, adjust the gap between the middle and rear rolls to 0.3 mm, press the baffle plate, add the slurry appropriately, visually inspect the coloring depth, fine-tune the rear rollers so that the coloring is evenly distributed over the rollers, and then lock the fixing nut.
②Adjust the handwheel of the front roller with both hands at the same time, so that the front roller slowly touches the middle roller and the surface of the front roller is evenly colored, then lock the fixing nut, and then adjust the angle of the material plate so that it is properly pressed on the roller surface, and the slurry can be uniform. discharge. Check the uniformity of the discharge and the particle size of the finished product, and continue to fine-tune the front and rear rollers until the particle size of the finished product reaches the predetermined requirements. The scraper should be returned in time before and after.
3. After the work of the three roll mill stops:
Remove the paint and clean it in time, wipe the roller and related parts, loosen the scraper and baffle, apply a small amount of oil, and then cover with wax paper for protection.
4. Precautions for three roll mill:
① The surface of the roll is strictly prohibited from bumping and scratching, and it is strictly forbidden for all kinds of metal objects and hard impurities to enter the running roll.
②The working temperature range of the roll: ordinary type: -5°C~100°C, heating type: 20C~220°C
③Roll and roller in normal working time: Gap range: (Reference) Middle and rear roller gap: 0.02~0.25mm, Middle and front roller gap: 0.01~0.25mm.
④ The peak angle of the baffle is strictly prohibited from being damaged, and the contact pressure with the roll surface should be appropriate during adjustment. There are three rollers mounted on an iron frame. The center is in a straight line. Can be installed horizontally, or slightly inclined. The grinding effect is achieved by the mutual extrusion of the surfaces of the three horizontal rollers and friction at different speeds. The steel drum can be hollow and cooled by water. The material is added between the middle roll and the rear roll. Because the rotation directions of the three drums are different (the rotation speed increases sequentially from the back to the front), a good grinding effect is produced. After the material is ground, it is scraped off by a scraper installed in front of the front roller.
Copyright Notice :
This article only represents the author’s point of view.
This article is published under the authorization of the author.
Source: Franli
This article address : The use process of the three roll mill
Related Products
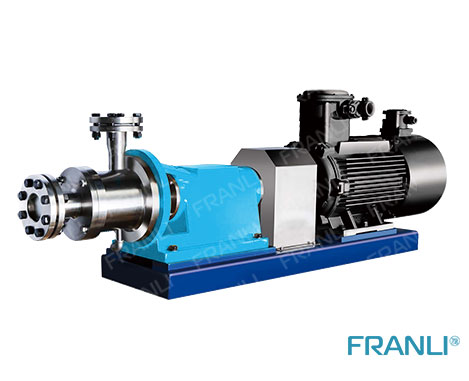
Inline Emulsifier
The inline emulsifier is composed of three sets of stators (two layers, four layers, and six layers) in the working cavity, which has higher processing accuracy, large processing capacity, and wide processing viscosity range.
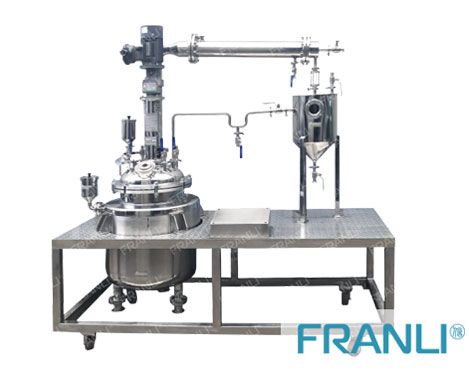
Chemical Reactor
The usual understanding of the chemical reactor is a container with physical or chemical reactions. Through the structural design and parameter configuration of the container, the heating, evaporation, cooling
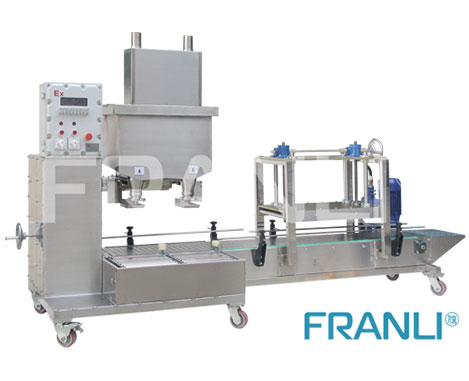
Paint Filling Machine
The paint industry has its own special design paint filling machine, normally choose weight type filling machine. One color needs one set of filling machine; also can filling different color of the painting, while it should be installed hopper
News
Laboratory Reactor: Guide to Stirring System
The laboratory reactor is composed of a pot body, a pot cover, an agitator, a jacket, a support and transmission device, a shaft seal device, etc.
Grinding Media for Bead Mill | Zirconia Beads & Zirconium Silicate Beads
Bead mills mainly use grinding balls as media, and use impact, extrusion, and friction to achieve the final grinding effect, which mainly depends on the size and hardness of the grinding beads, the filling rate of the grinding beads, and the collision frequency adjustment between the grinding beads and the particles.
Overview of Laboratory Reactor
Laboratory reactors, also known as lab reactors, are essential tools in scientific research, product development, and process optimization. These reactors provide a controlled environment for conducting chemical reactions, mixing, dispersing, and homogenizing processes.
Bead mills | Manufacturing technology in various industries
Bead mills, also known as sand mills or grinding mills, are versatile machines widely used across various industries for the wet grinding and dispersion of solid particles in liquid media.
Ribbon Blender Mixer Equipment
A ribbon blender mixer, also known as a ribbon mixer or horizontal ribbon blender, is a powerful industrial machine designed for thorough and efficient blending of various materials.
What is A Stainless Steel Reactor?
Stainless steel reactors are essential equipment in various industries, including chemical, pharmaceutical, biotechnology, and food processing.