Home » Agitator Bead Mill | Unique Wet Grinding Technology
Agitator Bead Mill | Unique Wet Grinding Technology
Bead Mill
The agitator bead mill is an advanced particle size reduction machine that utilizes a unique agitation process to grind materials into ultra-fine powders. Ideal for applications requiring micron or sub-micron level grinding, the agitator bead mill offers precise and reproducible size reduction results. Its wet grinding technology is also gentle on heat-sensitive materials.
Application: Paint, Adhesive, Battery, Pharmaceutical industry, Cosmetic
Agitator bead mills are highly versatile and efficient milling machines used in a wide range of industries for the wet grinding and dispersion of materials. These mills are equipped with an agitator, a cylindrical grinding chamber, and grinding beads made from various materials such as stainless steel, glass, or ceramics. The agitator bead mill’s special wet grinding technology ensures the production of high-quality dispersions and fine particles, making it an ideal choice for applications in areas such as paint and coating ingredients, inks and pigments, materials for additive manufacturing, adhesives and sealants, ceramics, and agrochemicals.
How does it work?
Inside the agitator bead mill’s grinding chamber, a rotating agitator shaft is fitted with discs and pins that create a cascading motion when spinning at high speeds. Hardened steel grinding beads are circulated and agitated within the chamber along with the material to be ground. As the beads tumble and collide with each other and the grinding chamber walls, they subject the target material to an intense frictional grinding action. The liquid is continuously added to the chamber during operation to keep the material in suspension and lubricated. This wet grinding process helps control temperature buildup to prevent damage to heat-sensitive materials.
The agitator bead mill’s ability to handle materials with high viscosity, high solid content, and high refining requirements makes it suitable for continuous or circulating processes. The machine can be equipped with a wide range of grinding bead materials with diameters ranging from 0.2 to 2.5 mm, allowing for the optimization of the wet-grinding unit for specific applications. The agitator bead mill’s dominance in the field of nano-scale wet milling is evident, and it offers high throughput rates even for highly viscous products.
The actual dispersion system in a bead mill consists of a milling chamber and an agitator; the milling chamber is filled with the grinding beads (material e.g., stainless steel, glass, or ceramics). The wetting of the surface of the solid matter to be processed by liquid components of the mill base, the mechanical division of agglomerates into smaller agglomerates and primary particles, and the stabilization of primary particles, agglomerates, and aggregates against renewed attraction are the three partial steps that run in parallel during the dispersion process.
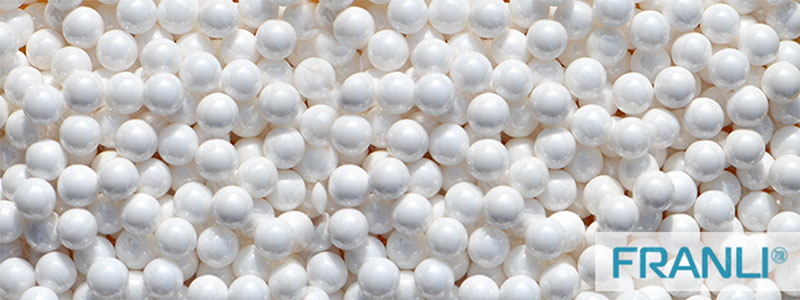
Key Benefits
– Ultra-Fine Particle Size Reduction
The agitator bead mill is capable of grinding materials down to D97 particle sizes as fine as 2 microns or less. This level of fineness is required for applications in many industries including pharmaceuticals, cosmetics, coatings, and more.
– Precise and Reproducible Results
The agitator bead mill’s grinding mechanism produces consistent, reproducible particle size distributions. Tight process controls allow replicating results batch after batch for quality-critical applications.
– Gentle on Heat-Sensitive Materials
Wet grinding in a liquid carrier controls friction and temperature, protecting materials that could otherwise degrade from heat. This makes the agitator bead mill suitable for heat-sensitive actives.
– Continuous or Batch Operation
The mill can run continuously to produce materials on demand or be used in a batch mode of operation to fill specific production needs.
– Variable Production Capacity
Models are available with grinding chamber volumes from 0.5 to 80 liters, providing flexibility to scale production capacity as needed.
– Closed System Design
A closed grinding chamber design helps prevent contamination during size reduction of pharmaceuticals or other products requiring purity.
– Automated Process Controls
Programmable logic controls allow the automation of operating parameters and the collection of production data for consistent quality.
– Easy Material Handling
Materials can be directly fed or pumped into the agitator bead mill in slurry or dry form. Discharge is also direct from the milling chamber.
– Low Energy Consumption
The agitator bead mill’s efficient grinding action consumes less energy per unit of production than many other milling technologies.
– Minimal Maintenance Needs
The mill features a simple yet robust design with few moving parts. Routine maintenance like changing grinding beads is quick and easy to perform.
Applications
The agitator bead mill finds wide use across many industries thanks to its ability to precisely micronize materials while protecting heat-sensitive components. Here are some common applications:
Pharmaceuticals: Grinding active pharmaceutical ingredients (APIs), excipients, nutritional supplements, and more to the fine particle sizes required for optimal bioavailability in tablets and other drug delivery forms.
Cosmetics: Micronizing pigments, minerals, and other components in cosmetic formulas like sunscreens, lotions, and makeup to achieve the proper aesthetic and performance characteristics.
Food Processing: Grinding spices, flavors, colorants, and other ingredients to nano sizes for enhanced dispersion in foods and beverages.
Coatings: Reducing the particle size of pigments, extenders, and other solids to improve properties like color strength, gloss, and opacity in paints, inks, and other coating systems.
Ceramics: Milling raw ceramic materials to fine, consistent sizes is important for achieving desired material densities and physical properties during firing.
Chemicals: Micronizing technical materials like catalysts, absorbents, and fillers to develop or enhance their reactivity and functional performance.
The agitator bead mill offers a unique wet grinding technology capable of precisely and reproducibly reducing particle sizes down to the micron and sub-micron levels. Its gentle processing approach suits it well-suited for heat-sensitive materials across industries like pharmaceuticals, cosmetics, food, and coatings. Contact us to learn how an agitator bead mill can optimize your size reduction needs.
Welcome to send inquiry to us and let’s make a win win business together !
Guidelines For Bead Mill
Bead Mill(sand mill) helps many factories to improve production. Grinding for low viscosity, well-flowing material. Self-cycling cooling system. Don’t need the cooling pump. Franli produces Disc Bead Mill, Pin Bead mill, Turbine Nano Bead mill, etc. Optional material of inner chamber and disc: hardness Alloy, Zirconia, PU.
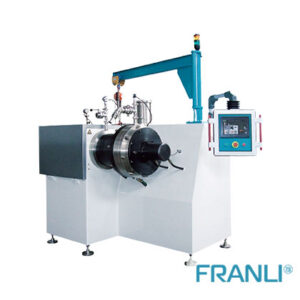
DYNO MILL – A DYNAMIC WAY TO GRIND EASIER
Dyno mill is nothing but an agitator bead mill. It is widely used in the production of paints, coatings, agrochemistry, and pharmaceutical products.
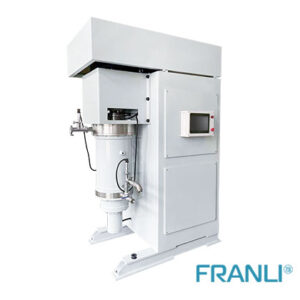
Role of Pearl Mill in the Nano Industry
Pearl Mill can handle both high and low viscosity materials. One is for Nano grinding materials, while the other is for high viscosity materials like offset ink. The operation of the Pearl Mill is straightforward, and all maintenance; may be handled quickly and efficiently. Adding grinding media from the feeding hole is simple.
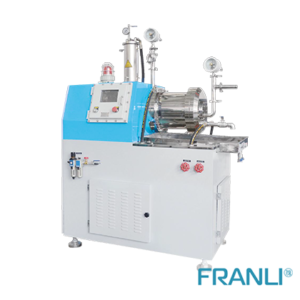
Guide to Bead Mills
The Bead mill is one of the main grindings and dispersing equipment in paint production. Bead mills for coatings are mainly divided into four categories: vertical, horizontal, basket, and special-shaped bead mills.
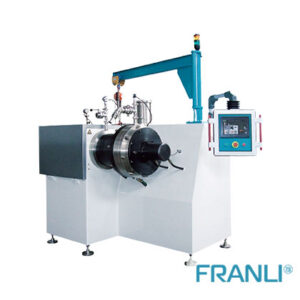
Dyno Mill|Coating & Inks
Dyno mill is a type of bead mill machine which is used in the coating industry specifically, in the manufacturing of inks products.
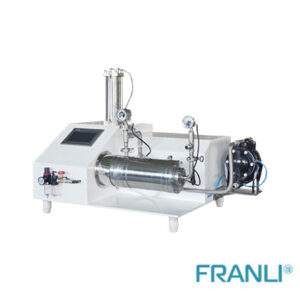
The structure and type of laboratory bead mill
The laboratory bead mill in the chemical experimental equipment, also known as the lab sand mill, is a kind of grinding equipment compared with the bead mill for industrial production.
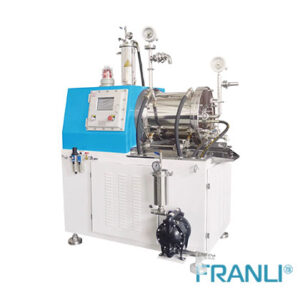
High Viscosity Material Grinding – Bar Pin Bead Mill
The bar pin bead mill is a machine suitable for ultra-fine dispersion and nano-scale grinding of water-based and solvent-based materials. The bar pin bead mill is one of the most widely used production types of equipment. With its very stable performance and sophisticated technology, it has been recognized by a wide range of users. The key thing to know is the characteristics of the bar pin bead mill, which is also the key to people’s favor of it.