Home » What is a three roll mill?
What is a three roll mill?
Three Roll Mill
Details of Three Roll Mill
- Two types: handwheel and digital control gap
- Safe scraper socket, Emergency-stop
- Space-saving desktop models
- Drip tray for easy cleaning
Application: Paint, Adhesive, Battery, Pharmaceutical industry, Cosmetic
The three roll mill is mainly used for the grinding of various paints, inks, pigments, plastics, cosmetics, soaps, ceramics, rubber, electronic pastes, and other fluid slurries and paste-like materials.
The working principle of the three roll mill
The three roll mill is mainly composed of an electric motor, transmission device, drum, frame, feeding and discharging device, adjustment device, cooling system, and other components, and has three rollers installed on the iron frame. The material can be selected according to different materials, generally, there are ceramic rollers, stainless steel rollers, marble rollers, etc., and it can be installed horizontally or slightly inclined. The state of the grinding material of the three roller mills is mainly through the mutual extrusion of the surfaces of the three rollers, and the friction and shearing action of different speeds, to achieve the best effect of grinding and dispersion. The steel drum can be hollow and cooled by water. Due to the different rotation directions of the three drums (the rotation speed increases sequentially from the feeding roller to the discharging roller), it produces a good grinding and dispersing effect.
Grinding slurry using a three roll mill
By adjusting the distance between the three rollers of the three-roller, the slurry has corresponding pressure and shearing force during grinding, and also easily overcomes the cohesive force between the powder particles, breaking into fine particles and fully dispersed in solvents and resins. When the particles enter the gap between the rollers, the shear force of the three roll mills is the largest in the tangential direction of the roller contact part. In actual operation, the large particles or agglomerates in the slurry are just beginning When put into the feed port of the three roll machine, it cannot enter between the rollers, and it continues to perform a “rod-like” rotating motion until the volume of the slurry on the roller is very small, and the oversized particles enter the roller. During the grinding process, it is crushed or adhered to the surface of the roller (so at the end of each grinding, the slurry on the roller needs to be shoveled with a spatula and re-entered for grinding to ensure the uniformity of grinding).
Precautions for operating a three roll mill
The three roller mills are high-pressure (very small roll distance) wet grinding equipment, so safe operation is very important. When the three rollers are working, the non-workers on site need to keep a certain distance from the three rollers. Beware of personal limbs and foreign objects (clothing, shovels) getting caught in the feed rollers or other gaps, resulting in personal safety problems.
How to choose a three roll mill?
Choosing the right three roll mill has always been the most common problem for many users, which not only affects the user’s experience but such as human and material resources, production requirements, etc. When the manufacturer meets the after-sales service and the price is moderate, the quality, size, and feeding method of the three roller mills are more things we need to think about.
(1) The quality of the three roller mill
The quality problem of the three roller mill often exists on its three rollers, and different rollers will choose different materials for forging according to the material, such as alloy steel, ceramics, marble, etc. Different forging methods will also affect the material of the rollers. For example, the commonly used forging method in the past was the cold casting method, but now the centrifugal casting method is used. The new method can obtain a 10-18mm thick anti-wear surface This kind of surface layer has super wear resistance and can be repaired multiple times, generally, 0.3-0.5mm each time, and at least 3-4 times can be repaired. replaced or corrected. The hardness of the damage-resistant layer on the surface of the roller is controlled by the metal composition, and the good hardness is generally in the range of 550-600 Bush hardness.
(2) Dimensions of the rollers of the three roller mill
For the machining of the surface of the roller, the main problem is the height of the roller (that is, the circumferential length of the section in the middle of the roller is greater than the circumference of the two ends). The distribution on the line is uneven, so the material is unevenly discharged.
(3) Feeding method of the three roller mill
In the operation of the three roller mills, the feeding problem has always been one of the most labor-intensive tasks. It should be known that the feeding method is generally to shovel the material in the barrel little by little and put it into the feeding port by manpower. The large-scale feeding manpower can still be solved, but the large-scale feeding needs to be solved in another way, at this time, a hopper is needed. As a high-quality three roller mill manufacturer, FRANLI has dumped, pumping, and extrusion feeding devices, that can be customized according to the strength of the materials used.
Influence of parameter setting on grinding effect
(1) Set the pressure of the three roll mill
Adjusting the pressure between the rollers is the most important step in the operation of the three roller mills. When the machine is started, if it is a model with a fixed middle roller, it is necessary to adjust the pressure of the feeding roller and the discharging roller, so that the slurry is in the grinding process. If the pressure is too large or too small, the phenomenon of uneven discharge will occur. You can judge whether the pressure is reasonable according to the discharge state.
When grinding the material, it is generally ground several times according to the fineness requirements of the final product, and the set pressure of the three roller mills is usually increased one by one to ensure that the wetting and dispersing process of the agglomerated particles is a “gradual” process. This makes it more stable and controllable.
(2) Set the temperature of the three roller mill
When using a three roller mill, the adjustment of the temperature of the rollers is also very important, which includes two aspects. First, the rollers themselves are rubbed against each other, and the rollers are also rubbed with the slurry, which leads to the increase of the temperature of the rollers, and then The temperature of the slurry increases as the temperature of the roll increases so that the decrease in viscosity affects the output. On the other hand: if the slurry temperature is too high, the temperature difference between the slurry and the ambient temperature is too large, which will easily cause condensed water to condense on the surface of the product and affect the performance of the product.
Blades of a three roll mill
The blade must be flat. The uneven blade is easy to wear on the surface of the roller irregularly. At the same time, there may be too much local friction, which leads to the local temperature of the roller being too high (accelerating the wear and aging process of the surface of the roller).
The width of the knife edge is appropriate. The width refers to the width of the bevel of the knife edge. If the knife edge is too wide, it is easy to curl the edge. Or production efficiency); too narrow, and the front is not sharp, affecting the discharge efficiency.
Installation position: The installation position of the blade is generally on the horizontal connection line between two adjacent rollers. Too high or too low will affect the output. The angle of contact between the blade and the roller is also very important. This angle refers to the angle between the blade and the contact point. Too small is easy to wear, and too large is easy to wear the blade. When the new blade is just used, the angle can be smaller, and then gradually during use. Increase the angle to find a balance between efficiency and cost.
Welcome to send inquiry to us and let’s make a win win business together !
Guidelines For Three Roll Mill
Three roll mills are widely used in a variety of chemical industries, from medium to high viscosity productions. FRANLI machine can break open all kinds of pigment, UV ink, offset ink, decorative paints, and Lubricants, it also can catch the greatest fineness in cosmetics/ lipstick and electronics industries.
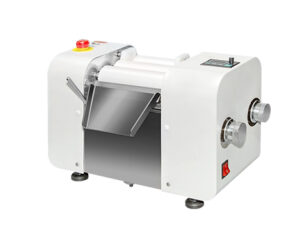
Three Roll Mill For Carbon Black|High Grinding & Dispersion
Three roll mill is the main equipment for grinding colored carbon black, as it is used extensively in rubber, plastics, paints, and inks, and some carbon black is added.
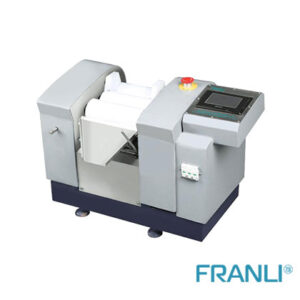
Laboratory Three Roll Mill|PLC Control System & Experimental
The laboratory three roll mill is equipped with the most advanced PLC functions to continuously improve the operability of the most primitive production equipment.
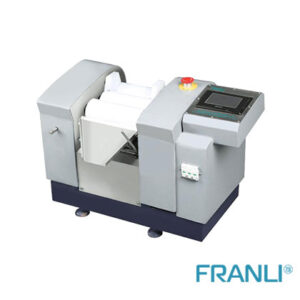
Three Roll Mill For Grease
The three roll mill plays a vital role in the grinding of grease. Grease is essentially a kind of lubricating oil, which is a solid or semi-solid product formed by one or more thickeners through the grinding and dispersing action of a three roll mill.
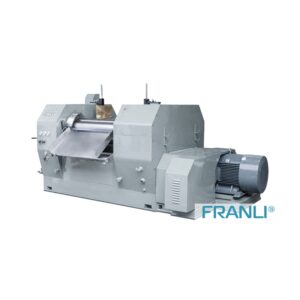
Three Roll Mill For Attapulgite
Three roll mill is the main equipment for grinding attapulgite. The attapulgite is ground and dispersed mainly because it is a natural colloid. Even if the size of the attapulgite reaches 0.1mm, it cannot be easily dispersed by the machine, so the final state of attapulgite formation has been greatly developed.
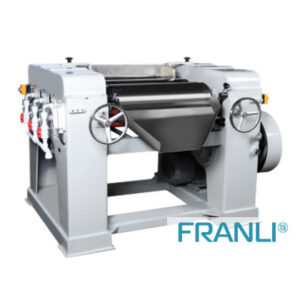
Rolls of a three-roll mill
The three-roll mill is mainly used for grinding materials of various viscosities and is one of the best wet grinding equipment. The dispersing and emulsification effect of the three-roll mill is excellent, especially for ink, paint, colloid, chocolate, plastic, cosmetics, etc., whether it is liquid slurry or paste material, the three-roll mill can work easily.
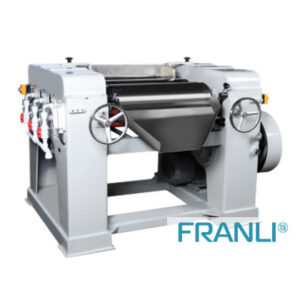
3 roll mill|Failure of the roll shaft & pulley
The 3 roll mill is a grinding and dispersing equipment, which plays an irreplaceable role in improving the quality of coating products.