Home » What is a ointment mill ?
What is a ointment mill ?
Ointment Mill
Details of Ointment Mill
- Two types: handwheel and digital control gap
- Safe scraper socket, Emergency-stop
- Space-saving desktop models
- Drip tray for easy cleaning
Application: Paint, Adhesive, Battery, Pharmaceutical industry, Cosmetic
In this current economic scenario, most of the companies are consistently looking for the new technologies, processes, and innovative equipment to add value to the development process of the organization that will reduce their expenses. A three-roll ointment mill is also one of the innovative technologies, made with three horizontally placed rolls that rotating in different directions to break the viscous & fine particles into same size.
A triple roll ointment mill is a well-known machine that utilizes the power created by shears made by three evenly placed rolls turning in opposite ways and at various rates comparative with one another to blend, refines, scatter, or homogenize thick materials fitted inside the machine.
The ointment mill has been demonstrated to be the best, which saw broad advancement in the nineteenth century. These incorporated the single-roll plant and the five-roll plant. The single-roll plant works by passing the material between the roll and a decent bar squeezing against the roll. The five-roll factory consolidates four progressively more modest in-running nips. Thus, contrasted with the three-roll plant, it permits the utilization of bigger agglomerates as a component of the main material. However, it is more messy and costly.
How do the three roll ointment mills operate?
The three nearby parts of a three-roll plant that consists of the focus roll, cover roll, and feed roll continuously rotate at higher rates. Material, typically as glue, is used between the feed roll and the middle roll. The greater part glues first than the remaining parts within the area of freed location, though there is a small space between the rolls. In fact, the portion which is enduring the part of the running nozzle encounters extremely high shear power. It is because of the unprecedented revolution rates of the rolls present there.
The remaining material parts on the middle roll pass within the middle and cover the roll. In this process, a higher shear power lies in between because of the greater rotation frequency of the cover roll and; basically, a tiny gap is there in the focus and feed rolls.
The difference between the rolls is precisely maintained by using pressurized water. Normally, the gap is far more prominent than the molecule size. In certain activities, some distance gets diminished bit by bit to accomplish the ideal degree in scattering.
The three roller ointment mill has three rollers mounted on an iron edge with the center in a straight line. It can be installed horizontally and slightly shifted. The crushing impact is achieved by commonly pressing the surfaces of the three horizontal rollers and rubbing them at various speeds. The steel drum can be empty and cooled by water.
The material is added at the middle of the back roll and center roll. Since the three rollers rotate in various ways, the rotational speed increases from the back to the front; a good grinding activity is produced. After the material is ground, it is scratched off by a scrubber set before the front roller.
Where is the three-roll ointment mill being used?
With the improvement in innovation, they are additionally used to create link covers, gadgets, cleansers, and counterfeit plastics.
A three-roll ointment mill is generally used for dispersion and, at the same time, is also used for grinding. The roller in the ointment mill are of different sizes and also operates on different speed, the directions of the rollers produce the sheer force that creates dispersion and grinds the particles mixed.
The semi-viscous materials are used in the three-roll ointment mill as dispersion material within a media-like cream. This ointment mill is the type of machine tool that utilizes the sheer force produced by the horizontally placed rolls, which rotates in different directions with variant speed to refine, dispense, mix, and turn the particles into similar sizes.
Special applications of three roll ointment mill
Little bench models are used for bench-top improvement work, lab work, and low volume creation. Bigger seat and floor models are worked to meet diverse creation built to meet different production needs from pilot plants to large volume productions.
Specific benefits of this process are that it permits high-viscosity glues to be processed. The high surface contact with the cooled rollers allows the temperature to stay low despite the high amount of dispersion work being placed in. A remarkable advantage is that the huge open space of glue on the rollers causes a loss of volatiles.
What are the advantages of three roll ointment mills?
The three roll ointment mill utilized in the dispersion system ensures that 100% of the product is passed through both shear zones.
• The shear rate between the rollers is the decisive factor for the cycle.
• This is determined by the roller dividing and the circumferential speed.
• Agglomerates and powder clusters are separated and homogenized.
• The more controlled the energy input, the more exact the processing.
Challenges faced by three roll ointment mills
The three-roll ointment mill has been used in a wide range of businesses, from ink, paint, and food, to high-tech industries like gadgets, energy storage, and energy transformation. Wherever, in the coating industry, where smaller groups and batches and shading changes are frequently required, three roll ointment mills are perhaps the best arrangement.
Three roll ointment mills have been used to accomplish the necessary particle size or coloristic properties. Maintaining the three-roll mill is frequently done by press-out systems or siphons. Here, cleaning ability is one of the significant benefits of the three roll ointment mills. It is important to check whether it is realistic to produce small batches of different colors or not.
With new-age three roll ointment mills processes, the accomplishment of this innovation will continue. Cleanroom capabilities, high adaptability, and high accuracy will open a wide range of new opportunities in the pharmacy industry. Reproducibility is one of the important keys to being successful in any industry. Scaling up from generally small lab sizes to enormous production machines is conceivable in a completely mechanized plant climate. One of the best characteristics of the three roller ointment mill is that every viscous particle gets converted into similar size that makes the configuration easy to be handled by the users. For more details, you can visit the official site of Franli.
Welcome to send inquiry to us and let’s make a win win business together !
Guidelines For Three Roll Mill
Three roll mills are widely used in a variety of chemical industries, from medium to high viscosity productions. FRANLI machine can break open all kinds of pigment, UV ink, offset ink, decorative paints, and Lubricants, it also can catch the greatest fineness in cosmetics/ lipstick and electronics industries.
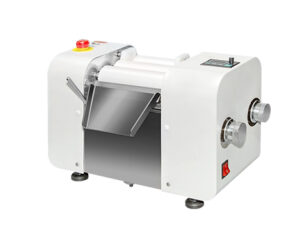
Three Roll Mill For Carbon Black|High Grinding & Dispersion
Three roll mill is the main equipment for grinding colored carbon black, as it is used extensively in rubber, plastics, paints, and inks, and some carbon black is added.
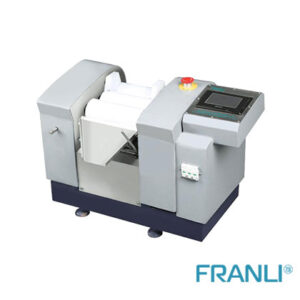
Laboratory Three Roll Mill|PLC Control System & Experimental
The laboratory three roll mill is equipped with the most advanced PLC functions to continuously improve the operability of the most primitive production equipment.
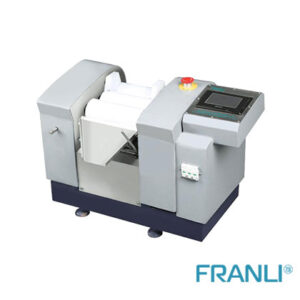
Three Roll Mill For Grease
The three roll mill plays a vital role in the grinding of grease. Grease is essentially a kind of lubricating oil, which is a solid or semi-solid product formed by one or more thickeners through the grinding and dispersing action of a three roll mill.
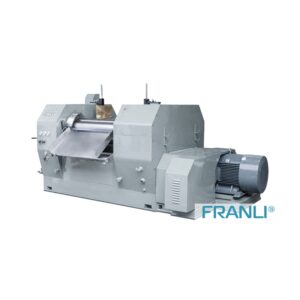
Three Roll Mill For Attapulgite
Three roll mill is the main equipment for grinding attapulgite. The attapulgite is ground and dispersed mainly because it is a natural colloid. Even if the size of the attapulgite reaches 0.1mm, it cannot be easily dispersed by the machine, so the final state of attapulgite formation has been greatly developed.
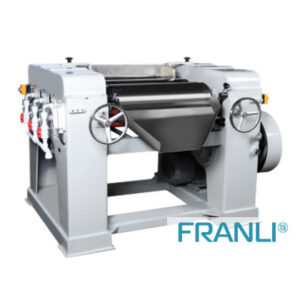
Rolls of a three-roll mill
The three-roll mill is mainly used for grinding materials of various viscosities and is one of the best wet grinding equipment. The dispersing and emulsification effect of the three-roll mill is excellent, especially for ink, paint, colloid, chocolate, plastic, cosmetics, etc., whether it is liquid slurry or paste material, the three-roll mill can work easily.
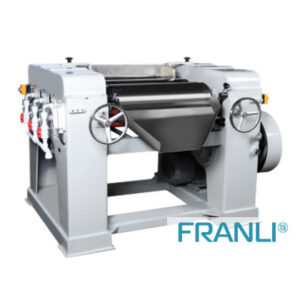
3 roll mill|Failure of the roll shaft & pulley
The 3 roll mill is a grinding and dispersing equipment, which plays an irreplaceable role in improving the quality of coating products.