Home » Three Roll Mill for Lipstick
Three Roll Mill for Lipstick
Three Roll Mill
The three roll mill is mainly used for grinding and dispersing materials, and it is mainly used for the manufacture of slurries such as coatings, inks, pigments, and plastics. The working principle of the three roll mill is to achieve the grinding effect by squeezing the surface of the horizontal three-roller and rubbing at different speeds. Three roll mill is the most effective grinding and dispersing equipment for high viscosity materials.
Details of Three Roll Mill
- TRS machine transfer gears that soak in oil (oil box). Keeping longer life of the operation, less noise.
- Cooling control system: TRS three roller machine installed thermometer, easily check material temp. Three rolls are normally connected with Chiller.
- Cooling system: an individual cooling system for each roller.
- hydraulic control: hydraulic control pressure blades, roller gaps, etc.
- Optional installation:PLC system with SIEMENS touching screen, FRANLI engineer set formulas of grinding according to different viscosity materials.
Application: Paint, Adhesive, Battery, Pharmaceutical industry, Cosmetic
In the process of processing materials, heating and cooling may be required. How does the three roll mill achieve this function? How is the three roll mill used in the process of manufacturing lipstick?
The rolls of a three roll mill can be cooled or heated by injecting cooling water/coolant or heat transfer oil into the roll core. We have a customer who uses heat transfer oil to heat the drum of our machine to 60°C.
Lipsticks and lip balms have higher percentages of fine and coarse particles, because some particles may be repeatedly dispersed due to dispersing forces, while others are not dispersed at all. The three roll mill is the most effective. For each three roll mill, the reduction of particle size and the dispersion of agglomerates are accomplished by the combined action of the rolling pressure between the rollers and the high shear force caused by different roller speeds. Since the entire material is filled into the roller gap, the particle size is precisely controlled and narrowly distributed. Through the adjustment of the roller spacing, the particle size can be easily and accurately processed to the micron level. Therefore, compared with other grinding equipment, the three roll mill can effectively improve the particle size distribution and make the particle size distribution more concentrated.
Application of three roll mill in lipstick production
The production of the lipstick is divided into four main stages, the first and second stage will use a three roll mill. The basic raw materials for making lipsticks include waxes, oils, pigments/pigments. A typical raw material ratio is 20/30% wax, 50/70% grease and 5/15% pigment. In the first stage, the pigment needs to be mixed with an appropriate amount of oil (the ideal ratio of pigment to oil is two parts oil and one part pigment), and then the mixture is ground with a three roll mill to uniformly disperse the pigment polymer. In the second stage, the uniformly dispersed pigment and grease mixture is added to the dissolved wax and remaining oil (or a small amount of aromatherapy can be added) and then reprocessed with a three roll mill to obtain the desired particle size (usually 20 microns) ). A three-roll mixture of uniformly dispersed pigment and oil is added to the dissolved wax and remaining oil (alternatively, a small amount of aromatics can be added) and reprocessed through a three roll mill to obtain the desired particle size (usually 20 microns).
Problems with using a three roll mill lipstick
1. Pigment grinding, since pigments are mostly powder, although the particles are relatively fine, they are often aggregated into lumps, and it is difficult to disperse them evenly when they are directly added to the oil matrix. Therefore, the pigments used must be ground beforehand. In order to make the grinding smooth, it is often necessary to add a small amount of liquid oil to the pigment and mix it, and then use mechanical grinding.
2. The colorant is mixed with the oil base. Generally, the dye is added to the solvent and heated and melted, and then the ground pigment and wax raw materials are added. After melting, the semi-solid oil is added, stirred evenly, and ground while hot; degassing Then add spices and other accessories.
Welcome to send inquiry to us and let’s make a win win business together !
Guidelines For Three Roll Mill
Three roll mills are widely used in a variety of chemical industries, from medium to high viscosity productions. FRANLI machine can break open all kinds of pigment, UV ink, offset ink, decorative paints, and Lubricants, it also can catch the greatest fineness in cosmetics/ lipstick and electronics industries.
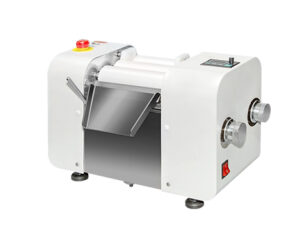
Three Roll Mill For Carbon Black|High Grinding & Dispersion
Three roll mill is the main equipment for grinding colored carbon black, as it is used extensively in rubber, plastics, paints, and inks, and some carbon black is added.
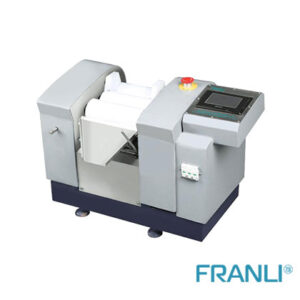
Laboratory Three Roll Mill|PLC Control System & Experimental
The laboratory three roll mill is equipped with the most advanced PLC functions to continuously improve the operability of the most primitive production equipment.
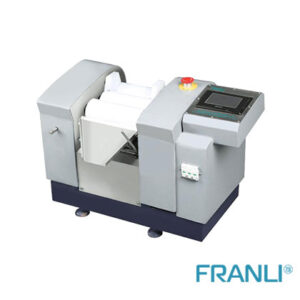
Three Roll Mill For Grease
The three roll mill plays a vital role in the grinding of grease. Grease is essentially a kind of lubricating oil, which is a solid or semi-solid product formed by one or more thickeners through the grinding and dispersing action of a three roll mill.
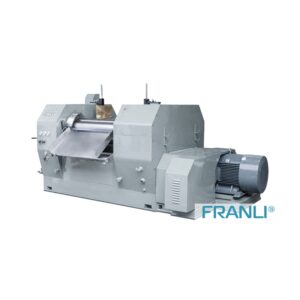
Three Roll Mill For Attapulgite
Three roll mill is the main equipment for grinding attapulgite. The attapulgite is ground and dispersed mainly because it is a natural colloid. Even if the size of the attapulgite reaches 0.1mm, it cannot be easily dispersed by the machine, so the final state of attapulgite formation has been greatly developed.
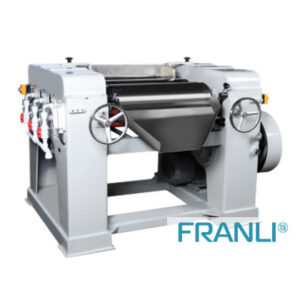
Rolls of a three-roll mill
The three-roll mill is mainly used for grinding materials of various viscosities and is one of the best wet grinding equipment. The dispersing and emulsification effect of the three-roll mill is excellent, especially for ink, paint, colloid, chocolate, plastic, cosmetics, etc., whether it is liquid slurry or paste material, the three-roll mill can work easily.
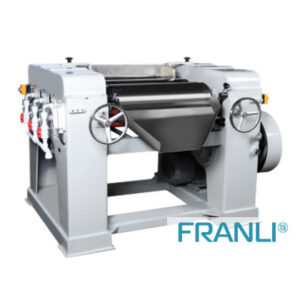
3 roll mill|Failure of the roll shaft & pulley
The 3 roll mill is a grinding and dispersing equipment, which plays an irreplaceable role in improving the quality of coating products.