Home » How to choose a suitable stainless steel reactor?
How to choose a suitable stainless steel reactor?
Stainless Steel Reactor
Details of Stainless Steel Reactor
- Using the latest reaction technology
- It has high temperature resistance, corrosion resistance, and high durability.
- Heating methods include steam, electric heater, high temperature heat transfer oil
- Using jacket, half pipe, fan coil, and other structures
Application: Chemicals, pharmaceuticals, dyes, pesticides, petroleum, food additives, etc.
Convenient material, temperature, pressure, and other indicators also change according to specific needs. Because the internal medium reacts violently in the pressure vessel, the stainless steel reactor is a relatively dangerous reaction vessel. Applicable to various resins, such as computer motherboards, inkjet photos, and other materials are processed after synthesis in a reaction kettle, which is a chemical reaction vessel in layman’s terms.
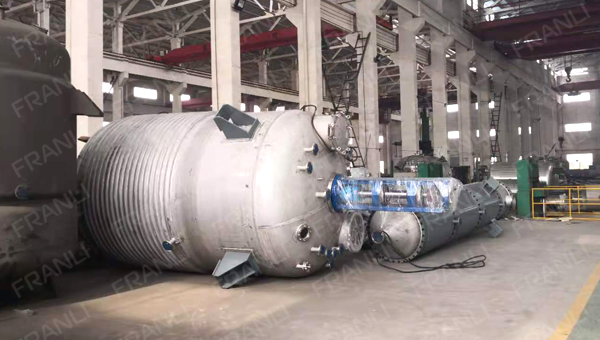
Selection of sealing form of the stainless steel reactor
1. First of all, the basis for sealing selection must be clarified: the first is the working pressure in the kettle, and the second is the nature of the working material. Another is the operating temperature of the device.
2. Secondly, it is necessary to clarify the types of seals used in stainless steel reactors: there are two types of seals used in reactors, commonly known as shaft seals, the first is packing seals, and the second is mechanical seals. Mechanical seals are divided into single machine seals (that is, single seals) End face mechanical seals) and double machine seal (i.e. double end face mechanical seal). The complete set of single machine seals also includes a water jacket, while the double mechanical seal is more complicated. In addition to the water jacket (must have circulating cooling water), it also includes supporting brackets, a balance tank, etc.
3. How to choose a suitable seal: Under the conditions of normal temperature and pressure, where the material is not volatile and non-flammable, and explosive, the packing seal should be selected; when the pressure is less than 4 kg, the material is generally volatile, inflammable and explosive Under the conditions of use, it is necessary to choose a single machine seal; under the conditions of use where the working pressure exceeds 4 kg (but less than 10 kg), and the material is highly volatile, flammable and explosive, a double mechanical seal must be selected.
4. Advantages and disadvantages of various seals: stuffing seals are the cheapest, but only suitable for the most common conditions of use and materials; single machine seals are moderately priced and can be used in most conditions of use; Must be used under working conditions.
Finally, we also need to consider our situation. If you choose a double-machine seal when you can use a packing seal or a single-machine seal, it will cause unnecessary waste in price; The production safety and economic benefits leave serious hidden dangers. Therefore, it is very important to choose a suitable sealing form according to the conditions of use. Determining a suitable sealing form can not only ensure that the conditions of use are met, but also avoid unnecessary waste.
A qualified stainless steel reactor needs to meet the requirements of normal operation, good performance, no damage to internal parts, quality compliance, clean main body, complete parts, and accessories, etc. before it can be applied to the work and production of the enterprise.
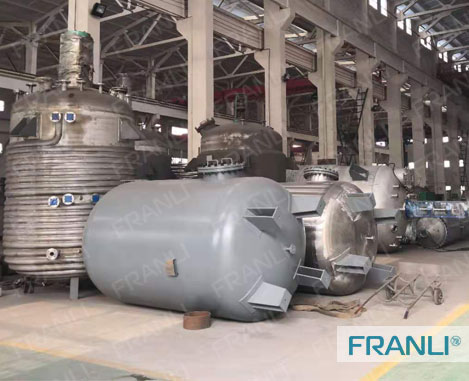
The quality of the stainless steel reactor
1. Normal operation and good performance
① The production capacity of the equipment can reach more than 90% of the design requirements;
②A pressure vessel license is required for the autoclave;
③ There should be no noise in the mechanical transmission, the agitator, and the heating coil in the equipment, and the inner parts of the pressure tube should have no collision and leave a gap according to the regulations;
④ The equipment is operating normally without abnormal vibration;
⑤ The temperature of the reducer is normal, and the bearing temperature should meet the regulations;
⑥The lubrication is good, the oil quality meets the requirements, and the oil level is normal;
⑦Spindle seals and reducers, pipelines, pipe fittings, valves, man (hand) holes, flanges, etc. have no leakage.
2. The internal parts are not damaged, and the quality meets the requirements.
① The material selection of the main parts such as the kettle body, shaft seal, agitator, and inner and outer coils meets the requirements of the drawings;
②The kettle body, shaft seal, agitator, internal and external coils, and other main parts are installed and coordinated, and the wear and corrosion limits should meet the maintenance regulations;
③The inner lining of the kettle does not leak or bulge, and the inner coil device is fastened and reliable.
3. The main body is neat, and the accessories are complete and easy to use
① The main body and accessories are clean, the foundation is solid, and the insulation paint is complete and beautiful;
② Pressure-reducing valves, safety valves, steam traps, control valves, automatic control instruments, ventilation, explosion-proof, safety protection, and other facilities are complete, sensitive, and easy to use, and should be checked and calibrated regularly;
③Pipe fittings, pipelines, valves, brackets, etc. are installed reasonably, horizontally and vertically, and painted clearly;
④ All bolts should be fully buckled, neat, and fastened.
Welcome to send inquiry to us and let’s make a win win business together !
Guidelines For Stainless Steel Reactor
FRANLI has several complete stainless steel reactor production lines. Our stainless steel reactor adopts the latest infinitely variable speed reducer device, the sealing device can be a mechanical seal, and the heating and cooling can adopt the structure of a jacket, half pipe, fan coil, etc., The heating methods include steam, electric heater, and high-temperature heat transfer oil to achieve different safe processing environments such as acid resistance, heat resistance, wear resistance, and corrosion resistance.
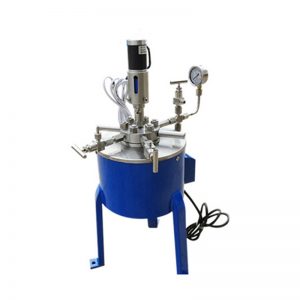
Laboratory Reactor: Guide to Stirring System
The laboratory reactor is composed of a pot body, a pot cover, an agitator, a jacket, a support and transmission device, a shaft seal device, etc.
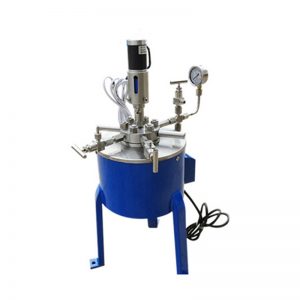
Overview of Laboratory Reactor
Laboratory reactors, also known as lab reactors, are essential tools in scientific research, product development, and process optimization. These reactors provide a controlled environment for conducting chemical reactions, mixing, dispersing, and homogenizing processes.
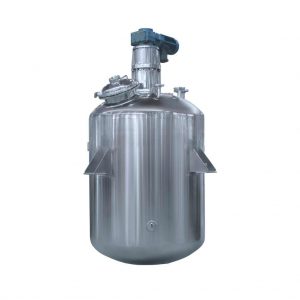
What is A Stainless Steel Reactor?
Stainless steel reactors are essential equipment in various industries, including chemical, pharmaceutical, biotechnology, and food processing.
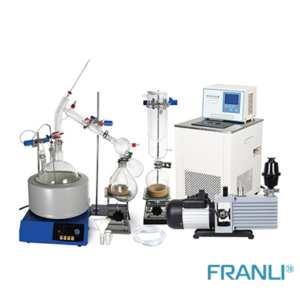
Glass Reactor & Chemical Equipment
Glass reactors are essential equipment widely used in the chemical, pharmaceutical, and biotechnology industries. They come in various types, suitable for different applications.
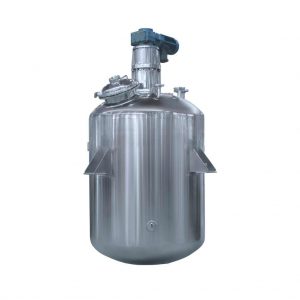
Operating Guide for Laboratory Reactors
Laboratory reactors play a crucial role in chemical research and development. Understanding the proper operating procedures is essential to ensure accurate results and maintain a safe working environment.
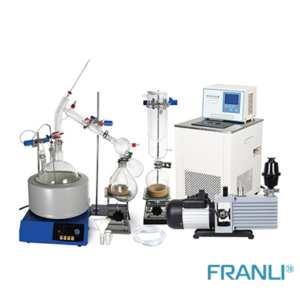
Glass Reactors and Selection of Stirring Blades
Glass reactors, also referred to as glass reaction vessels, are vessels made from high-quality borosilicate glass material.