Home » All you need to know of wet grinding with the help of a bead mill
All you need to know of wet grinding with the help of a bead mill
In terms of improving processability and the efficacy of the ingredients active in nature as that of the agrochemicals and pharmaceuticals, fine milling with the help of bead mill machine, micronization along nanonization can be quite useful here.
For getting the extremely smaller size of the particles and higher surface area of the particles here in terms of achieving the greatest possible vibrancy along with the opacity of the pigments within the coatings, inks, and even cosmetics can be used by the bead mill.
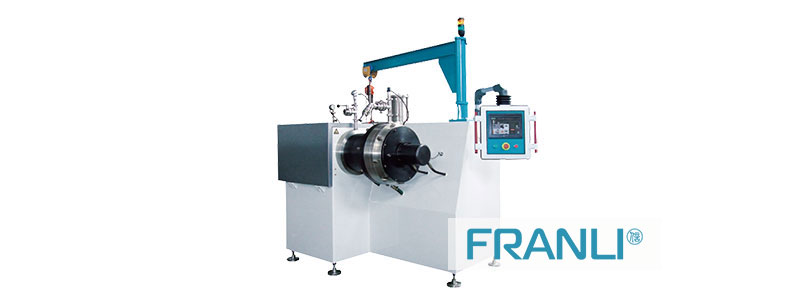
dyno mill
Operations of wet grinder
The experts of wet milling understand the variables that are included in the bead grinding machine for milling processes. It can include the milling of the media sizes and types, ingredients, ratios of the liquid slurry, speed of the mills, etc.
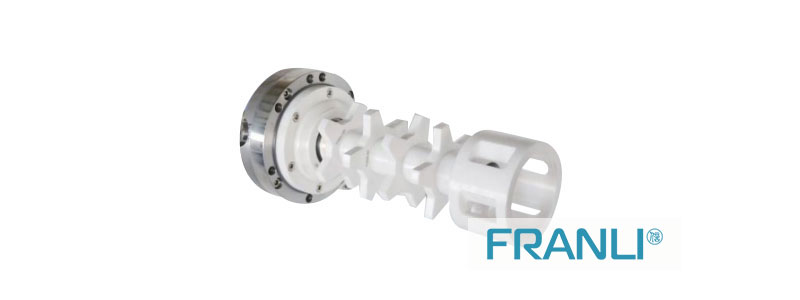
SMP agitator bead mill
STEP 1: WETTING
It massively depends on the material being milled with the help of a bead mill, and this is important to go ahead and select the right kind of liquid here.
STEP 2: CHARGING THE MEDIA MILL
They are generally based on the material characteristics of the raw feed along with the desired size of the final particle here in terms of the milling media size and the type. The bead mill here includes the following components:
· Steel
· Tungsten carbide
· Ceramic
· Zirconium oxide
· Polymer resins
STEP 3: DEAGGLOMERATION
STEP 4: DISPERSION IN LIQUID
For avoiding the flocculation as well as sedimentation, the dispersed raw feeds within the liquid slurry often have the requirement for being stabilized. Dispersion additives usually do the job in accordance with the bead mill working principle for the materials that include the inorganic pigments along with the ores here. Expertise matters the most here in terms of selection as well as the quantities of the stabilizers and others associated with the bead mill.
STEP 5: WET GRINDING
The materials here are duly analyzed for the assurance and process control in this step of the bead milling process. It can help make sure of the timely completion of the projects without the need of waiting for the tests as well as the analysis from the other labs here with the capabilities of the bead mill.
STEP 6: SEPARATION
STEP 7: DEGASSING OR DRYING
There is a team of experts from Franli who are offering the milling processes irrespective of whether it is for wet or dry milling, and this can help you effectively achieve fruitful outcomes here. You can surely trust the decisions being made with great interests in your mind irrespective of the industry, raw materials, and others. These are the significant theories and practicalities associated with the bead mill.
Copyright Notice :
This article only represents the author’s point of view.
This article is published under the authorization of the author.
Source: Franli
This article address : All you need to know of wet grinding with the help of a bead mill
Related Products
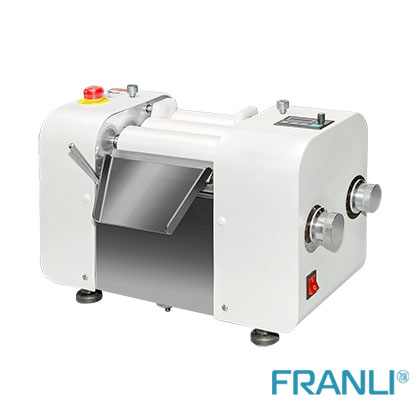
Lab Three Roller Mill
Franli Lab three roll mill machine also has a safety system. Such as hopper with handguard, drip tray with integrated handguard and safety switch, removable for easy cleaning. Also safe scraper socket, Emergency-stop pushbutton. Electronic Brake.
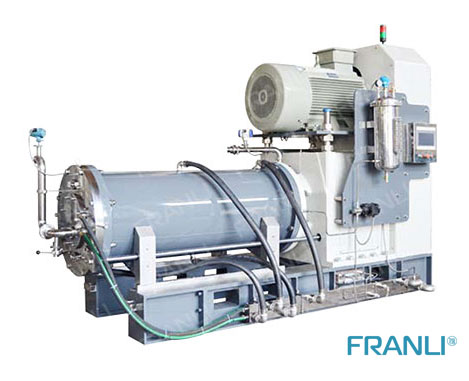
Horizontal Bead Mill
Horizontal Bead Mill is used for the grinding of a solid-liquid two-phase system. In the grinding process, the material is pumped into the Horizontal Bead Mill, and the rotating grinding disc transfers energy to the beads. The beads impact the material an
News
Laboratory Reactor: Guide to Stirring System
The laboratory reactor is composed of a pot body, a pot cover, an agitator, a jacket, a support and transmission device, a shaft seal device, etc.
Grinding Media for Bead Mill | Zirconia Beads & Zirconium Silicate Beads
Bead mills mainly use grinding balls as media, and use impact, extrusion, and friction to achieve the final grinding effect, which mainly depends on the size and hardness of the grinding beads, the filling rate of the grinding beads, and the collision frequency adjustment between the grinding beads and the particles.
Overview of Laboratory Reactor
Laboratory reactors, also known as lab reactors, are essential tools in scientific research, product development, and process optimization. These reactors provide a controlled environment for conducting chemical reactions, mixing, dispersing, and homogenizing processes.
Bead mills | Manufacturing technology in various industries
Bead mills, also known as sand mills or grinding mills, are versatile machines widely used across various industries for the wet grinding and dispersion of solid particles in liquid media.
Ribbon Blender Mixer Equipment
A ribbon blender mixer, also known as a ribbon mixer or horizontal ribbon blender, is a powerful industrial machine designed for thorough and efficient blending of various materials.
What is A Stainless Steel Reactor?
Stainless steel reactors are essential equipment in various industries, including chemical, pharmaceutical, biotechnology, and food processing.