Home » Pearl mill|Reduce material waste
Pearl mill|Reduce material waste
The following would be a few of the methods that can be implemented by the manufacturers in order to minimize the waste brought about by milling:
1: Recycling the Metal Swarf
However, there are a few companies that have already started with the use of specialized equipment that can help recycle and reuse the metal wastes internally. With the processing of the metal waste, it is sent to the other companies with the effective maximization of their potential revenues is the benefit that tags along.
The manufacturers can effectively bypass the expense of transferring their chips to the other company by internalizing the recycling process. It is, however, this method that is not effective for every manufacturer, mainly the ones who deal with several various metal alloys, as they could be well-worth studying for a few of those naturally.
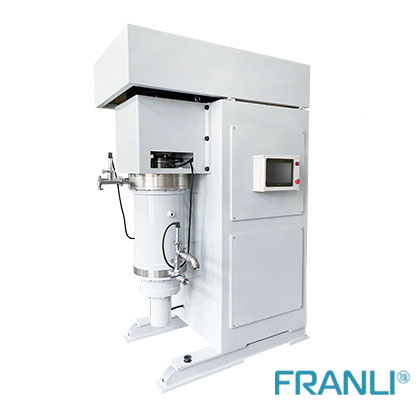
2: Increasing Consistency of the Process
The production of the waste can also be reduced dramatically along with preventing the delays of the production that are caused by the excessive parts of remanufacturing here with the increased consistency over the processes here.
The use of factory automation is one of the ways in which they can make sure of the consistency of the process in terms of the milling operations. Great consistencies can be maintained from part to part in terms of minimizing the need for the reworks to almost nothing that is a lengthy parameter that is programmed within the machines here.
The waste from the metals is therefore reduced significantly.
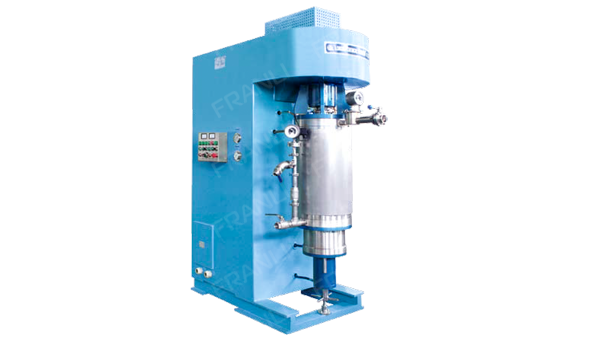
3: Minimizing Physical Prototypes Reliance
The design needs to be worked on with the production line having been retooled with several new parts and the tools that need to be machined all over again here if the first prototype fails here. It can therefore be producing a lot of metal scraps here.
The manufacturers would save a lot of time, resources, and energy, preventing the production of the waste that can be pretty incidental to the prototype of the manufacturing process, eliminating every physical prototype that is present.
In terms of identifying the potential risks and correcting them without the proper need of having to commit for a single inch of wire to get the manufacturing process done is made possible through this.
The manufactures can greatly reduce their metal waste in terms of production of the milling processes. Here are simply a few of the potential ways here.
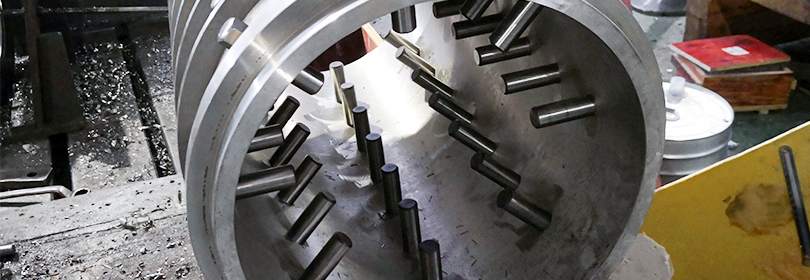
What Is Turning?
The other process included here is boring, involving the use of lathe here. The stationary cutting tool here presses against the rotating workpiece through the process of turning and boring. The turning here is designed for the removal of the material from the exterior region of the workpiece, while the boring is designed specifically for the removal of the material from the interior part of the workpiece here. Boring is used for enlarging the pre-drilled holes within the workpiece with the removal of the materials from the inner walls of the holes, for instance, here.
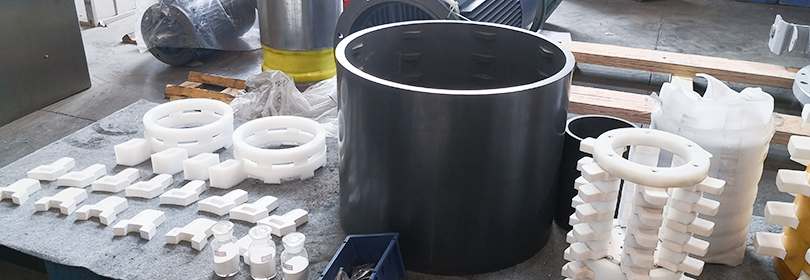
What Is Milling?
In Conclusion
Copyright Notice :
This article only represents the author’s point of view.
This article is published under the authorization of the author.
Source: Franli
This article address : Pearl mill|Reduce material waste
Related Products
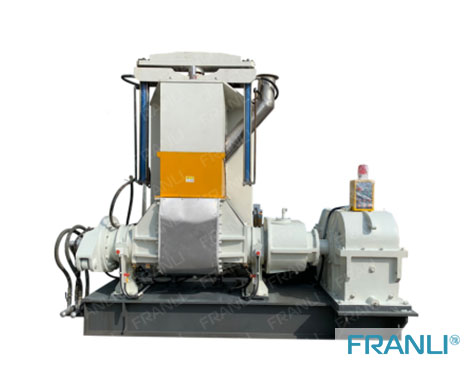
Dispersion Kneader
The dispersion kneader is suitable for the mastication of rubber and plastics, and the mixing of various rubber materials and plastics.
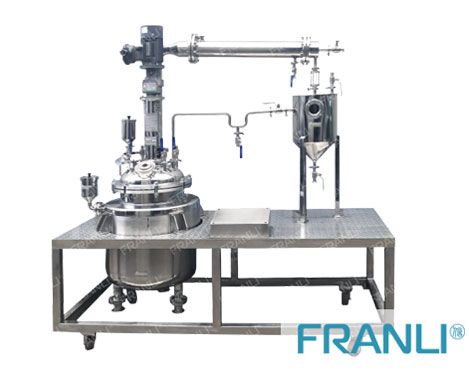
Chemical Reactor
The usual understanding of the chemical reactor is a container with physical or chemical reactions. Through the structural design and parameter configuration of the container, the heating, evaporation, cooling
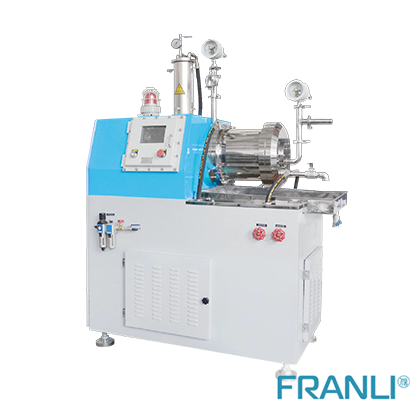
Bead mill for paint
The application fields of liquid coatings are very wide, so a bead mill for grinding high-quality and high-fineness coatings is required.
News
Laboratory Reactor: Guide to Stirring System
The laboratory reactor is composed of a pot body, a pot cover, an agitator, a jacket, a support and transmission device, a shaft seal device, etc.
Grinding Media for Bead Mill | Zirconia Beads & Zirconium Silicate Beads
Bead mills mainly use grinding balls as media, and use impact, extrusion, and friction to achieve the final grinding effect, which mainly depends on the size and hardness of the grinding beads, the filling rate of the grinding beads, and the collision frequency adjustment between the grinding beads and the particles.
Overview of Laboratory Reactor
Laboratory reactors, also known as lab reactors, are essential tools in scientific research, product development, and process optimization. These reactors provide a controlled environment for conducting chemical reactions, mixing, dispersing, and homogenizing processes.
Bead mills | Manufacturing technology in various industries
Bead mills, also known as sand mills or grinding mills, are versatile machines widely used across various industries for the wet grinding and dispersion of solid particles in liquid media.
Ribbon Blender Mixer Equipment
A ribbon blender mixer, also known as a ribbon mixer or horizontal ribbon blender, is a powerful industrial machine designed for thorough and efficient blending of various materials.
What is A Stainless Steel Reactor?
Stainless steel reactors are essential equipment in various industries, including chemical, pharmaceutical, biotechnology, and food processing.