Home » What Makes An Ointment Mill A True Expert?
What Makes An Ointment Mill A True Expert?
The world’s first high-pressure roller grinding machine ointment mill uses the application layer crushing mechanism. It can be used in nonferrous mining, oxidation; the pellet was broken, grinding and used in cement with a rolling machine. Because of its high efficiency, Mobile jaw crusher energy savings, significant investment, easy maintenance, province, and the benefits of working environment, it is widely recognized as an advanced crushing and grinding machine.
High-Pressure Roller Mill structure
The features of the high-pressure roll grinding machine
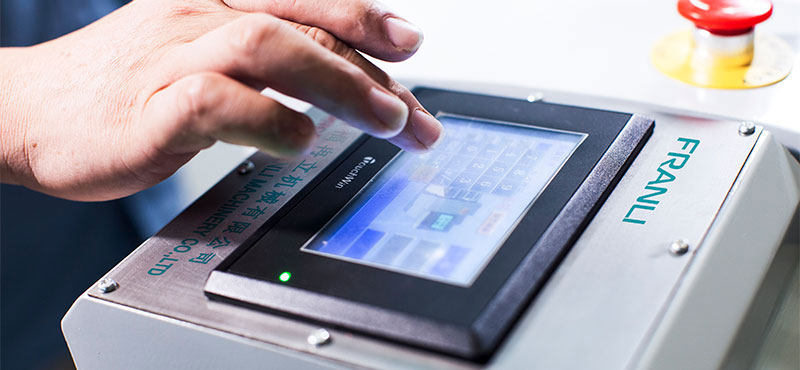
Increase follow-up work product quality and recovery
Covers a smaller area, the investment province
The nano-range of the particle sizes will also be drying the feed material that is enabled through the jet milling process.
For the materials that are sensitive to heat, this is the technique that might not be suitable, but the bed jet mills that are fluidized can be used in terms of getting the nanoparticles in a greater range of minerals as well the pigments here.
Factoring the right method for your material
In response to the government’s call to protect the environment, the coal industry developed high-efficiency and energy-saving rolling crushers. It was becoming more common for industries to focus on energy conservation and environmental protection. Most crusher manufacturers face this challenge. Future trends will be low consumption and environmentally friendly roll crusher equipment. Hanging has developed a range of roll crusher machines with low carbon energy savings, green and environment friendly to satisfy consumers’ needs. This roll crusher is used extensively in silicate, coal, cement, and other industrial areas. You can divide the roll crusher into a plain roller or tooth surface roller. The former is used for crushing medium-hard materials, while the latter is used for brittle and soft materials.
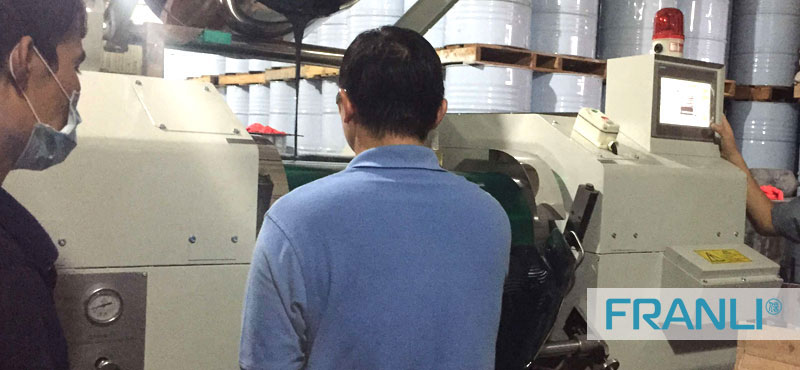
Uses and Advantages of an Ointment Mill
The Vertical ointment mill operates by having the reducer on the top of each main unit rotate with the central axis connected to the couplings. And then, the grinding roll cradle will spin and roll around the inner surface. From the side top of the machine, the materials will be fed into the feeding hopper and divided into two sections. After that, the materials will spread around the central axis. Then they will evenly enter the space between the grinding ring and the roller with the help of the circle tunnel. The materials will then be ground and crushed using the roller and then discharged via the outlet.
For coarse grinding materials, after the board, place the single container into the second warehouse. The warehouse is lined with flatlining and steel balls inside. To complete the grinding operation, the powder is discharged from the discharge grate plate. The structural ointment mill characteristics of the ball mill are determined from the feeding, discharging, Rotary Department, Transmission Division (reducer small transmission gear motors, electrical controller), and other major parts. Hollow shaft with steel casting. They are lining Replaceable. The body is inlaid with cylinder liner wear.
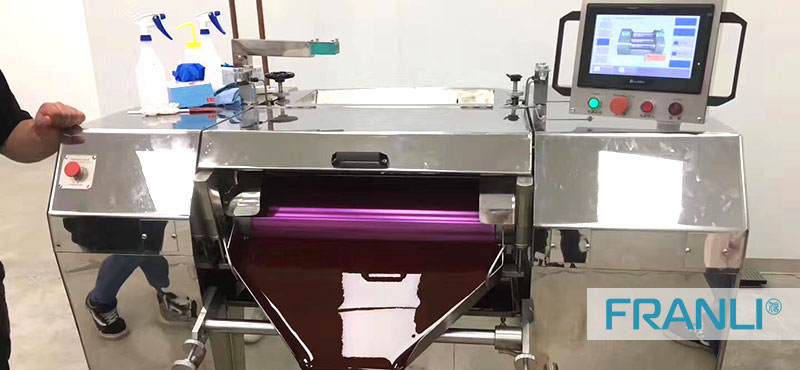
You can choose from many different models depending on your material and input feed size. Select ointment mill models may include stainless-steel knives for grinding corrosive material, jar chutes for examining the finished product and easy storage of samples, and stainless-steel sieves which prevent samples from entering a chute without first passing through a screen. To prevent contamination of the grinding bowls, it is important to use compatible materials for the balls and bowls.
Many reputable companies like Franli are well versed in the dynamics of the Ointment mill. Several patents have been filed by these companies, including the first laboratory-planetary mill with cantilevered bowls. While many lab mills are well-known, you should always select a supplier with care. While there are many highly reputable companies out there, it is worth researching first.
Copyright Notice :
This article only represents the author’s point of view.
This article is published under the authorization of the author.
Source: Franli
This article address : What Makes An Ointment Mill A True Expert?
Related Products
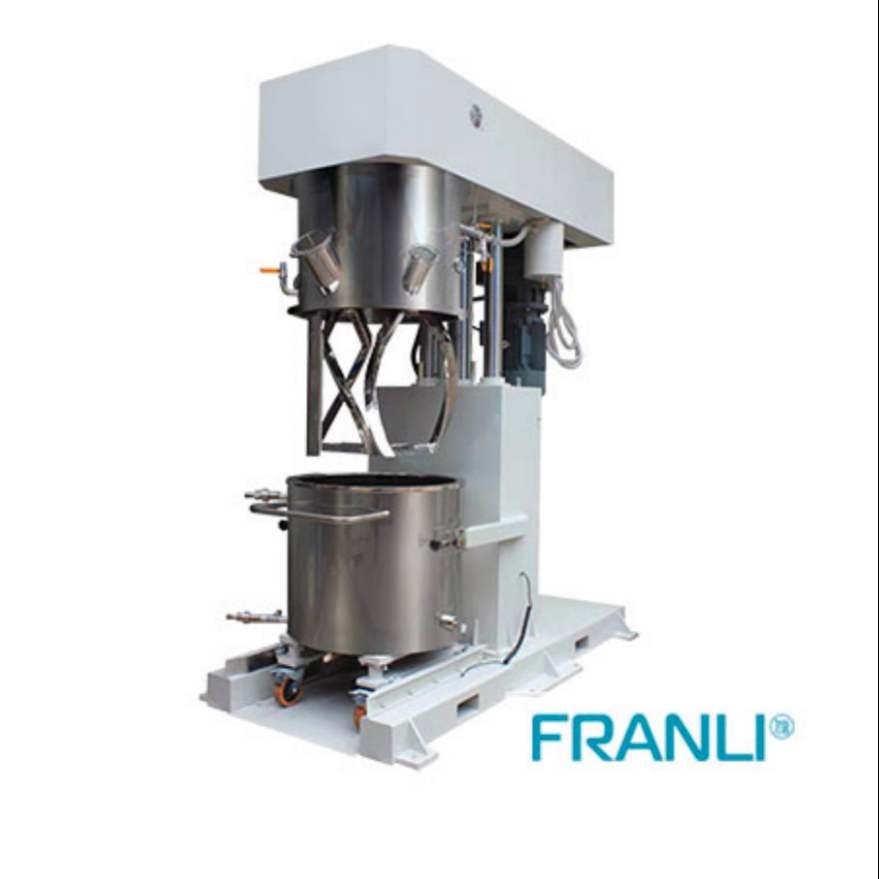
Vacuum Double Planetary Mixer
A Vacuum double planetary mixer is an essential part of any industry to mixing particular material. A double planetary mixer contains two blades that help mix by revolving on their axis in the vessel.
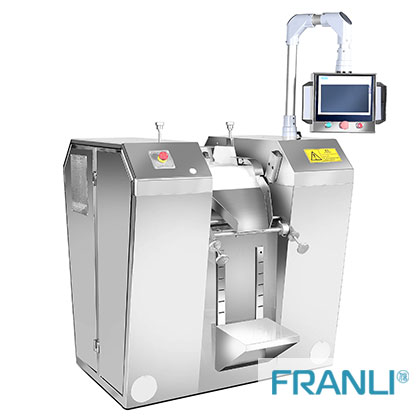
Hydraulic Three Roll Mill
FRANLI Hydraulic three roll mill has a unique Hydraulic system, which controls pressure roller, discharging blade, two sides holders, etc, which system can improve production capacity compared with normal same size three roll mill.
News
Laboratory Reactor: Guide to Stirring System
The laboratory reactor is composed of a pot body, a pot cover, an agitator, a jacket, a support and transmission device, a shaft seal device, etc.
Grinding Media for Bead Mill | Zirconia Beads & Zirconium Silicate Beads
Bead mills mainly use grinding balls as media, and use impact, extrusion, and friction to achieve the final grinding effect, which mainly depends on the size and hardness of the grinding beads, the filling rate of the grinding beads, and the collision frequency adjustment between the grinding beads and the particles.
Overview of Laboratory Reactor
Laboratory reactors, also known as lab reactors, are essential tools in scientific research, product development, and process optimization. These reactors provide a controlled environment for conducting chemical reactions, mixing, dispersing, and homogenizing processes.
Bead mills | Manufacturing technology in various industries
Bead mills, also known as sand mills or grinding mills, are versatile machines widely used across various industries for the wet grinding and dispersion of solid particles in liquid media.
Ribbon Blender Mixer Equipment
A ribbon blender mixer, also known as a ribbon mixer or horizontal ribbon blender, is a powerful industrial machine designed for thorough and efficient blending of various materials.
What is A Stainless Steel Reactor?
Stainless steel reactors are essential equipment in various industries, including chemical, pharmaceutical, biotechnology, and food processing.