Home » Manufacturer of Dyno Mills
Manufacturer of Dyno Mills
Dyno Mill
Dyno Mills are often commonly employed in the production of inks. The construction of the dyno mill varies according to the amount of ink being produced. Gravure ink should usually adhere to the following guidelines: Pin or disc dyno mills are often used in manufacturing. Ink for rotary impression printers: Typically, the vertical rod is used.
Details of Dyno mill
- The frame of the Dyno mill
- Grinding system of Dyno mill
- Double mechanical seal of Dyno mill
- The transmission system of the Dyno mill
- Grinding cylinder of Dyno mill
Application: Paint, Adhesive, Battery, Pharmaceutical industry, Cosmetic
Dyno Mills are classified in a variety of ways. The swirling shaft may be classified into three types based on its construction and form: disc type, rod type, and rod disc type Lateral grinding cylinders can be classified based on their arrangement. The cylinder can be classified into 4 different forms, small, medium, big, and super large based on its volume. It may be classified into steady and dynamic separating dyno mills based on the substance separation process. The consistent theme between the two is that they both employ impact, squeezing, and resistance between grinding mediums to crush the materials. As a result, they may both be categorized as media mills.
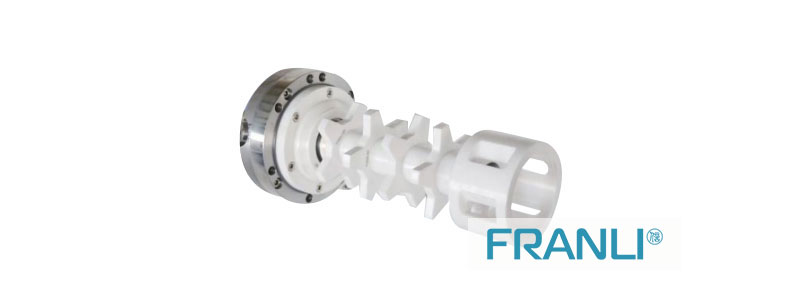
How Does The Dyno Mill Work?
The common element between these two is they both employ impact, squeezing, and friction between the grinding medium to crush the material. As a result, both can be categorized as media mills.
Whenever the product and the grinding media are divided in a dyno mill, then it is employed. A stationary circle and a flowing ring make up the majority of the separating system. The stable ring is primarily positioned on the mechanical seal’s having a dedicated, while the movable component is on the side that comes into contact with contamination. The stationary ring and the flowing ring are composed mostly of solid filament steel. The distance around them is changed based on the purity of your product, such as with the cleanliness necessary.
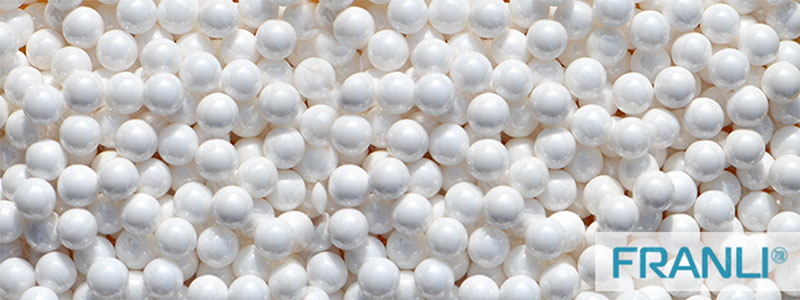
In most cases, the grinding meson is three times the separating gap. As a result, the size of both the grinding medium is determined by pure zirconia beads. The favorable impact of material fineness grinding is mostly represented in the comparatively quick and high yield in a short period and fineness. The dyno mill is a key piece of equipment used in the ink manufacturing process. It’s a machine that grinds and disperses big particles or agglomerated raw materials into a small powder. When the temperature becomes too high during the grinding operation, the ink quality suffers. As a result, a cooling system is installed on the dyno mill. The ink spins at a fast speed in the grinding cylinder were used throughout the process, as well as the pins, have excellent resistance. After just a period, if the double pin system is excessively thick, the points will simply tilt and clash with each other. There will be no discernible effect if there are very few twofold pins. Furthermore, the internal cooling water circuit in the rotor produces a little visible cooling effect and is likely to fail. As a result, the rotor arrangement of the dyno mill is critical.
Dyno Mill supplier
Based on a home automation system, FRANLI has developed an important dyno mill supplier and exporter, providing a wide range of dyno mills and several other items such as Rotary Mixers, Drum Lifters, and Containers. The company uses fresh and current technologies in the development of these products to accommodate our consumers.
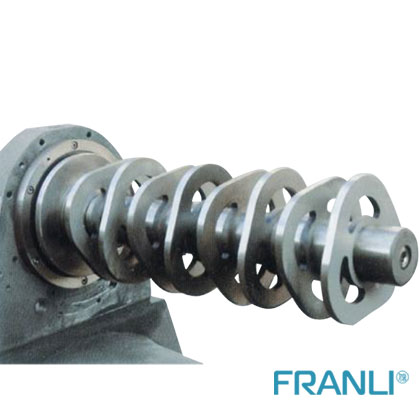
For varying amounts and wet milling down to particle diameter, the Dyno Mill is a great solution. A machine provides exceptional outcomes when it is carefully constructed from elevated materials. Finding one that fits your needs while staying within your dyno mill price might be tough. When compromise is not an option, choose a renowned Dyno Mill Manufacturer in India. Their main objective is to make sure that all of their potential customers are happy. They provide such a diverse variety of modern Dyno Mills to meet a wide variety of needs.
The biomechanical pressures that break up the infrastructure by overriding the importance of teamwork forces are used to grind substances. The condition of the material changes after crushing particle sizes, texture and structure, and durable construction. Having broken down, sorting, sizing, applying, or purifying consistently are referred to as milling. For example, rock crusher or milling to create consistent cement content for constructions, or the separation of rock, soil, or additional materials for an integrated or infrastructure construction. Accumulated milling procedures can also be used to eliminate or segregate contaminants or dampness from material or soil before shipment or architectural filling, as well as to generate “dry fills.” A mill is a mechanical device that grinds, cuts, or crushes solid particles into smaller pieces. The Dyno Mill working principles can easily handle complicated grinding operations.
In engineering, grinding can be used for the following purposes:
● an increase in a solid’s surface area
● Creating a solid with a certain grain size
● resource pulverization
Dyno Mill working Principle
The dyno mill working principle is a closed-loop agitated beads mill with a radial grinder container for dispersion and finer wet crushed. The dyno mill can handle a wide range of products, from light pumpable to those highly sticky. Specially built initiator rings typically mounted on a pole convey the liveliness required for dispersion and wet granulating to the sphere crushed blobs. Some outsourcing construction feeds the materials into the mill. Dyno Mill suppliers and machinery used in the comes in contact with the goods and become worn out are replaced and come in a range of materials. Because of the modular architecture, mills that have been in operation may be transformed fast.
Fields of Application
FRANLI has chosen the most suitable, user-friendly, and safe structure. Whether supplying a few systems to a whole line to a spinning venture, we’ve done it all. In yet another nation, we have technology customer service representatives. We aim to motivate the businesses we represent by proving that it is achievable to provide pleasure, optimism, and sunlight to all of your consumers, employees, vendors, and system integrators at the very same moment. By expressing the same spiritual goal, we are assembling a squad. Machine development and design.
Welcome to send inquiry to us and let’s make a win win business together !
Guidelines For Bead Mill
Bead Mill(sand mill) helps many factories to improve production. Grinding for low viscosity, well-flowing material. Self-cycling cooling system. Don’t need the cooling pump. Franli produces Disc Bead Mill, Pin Bead mill, Turbine Nano Bead mill, etc. Optional material of inner chamber and disc: hardness Alloy, Zirconia, PU.
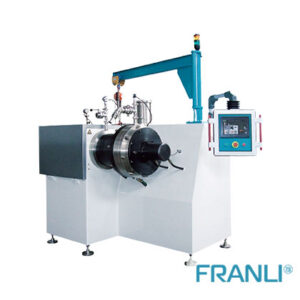
DYNO MILL – A DYNAMIC WAY TO GRIND EASIER
Dyno mill is nothing but an agitator bead mill. It is widely used in the production of paints, coatings, agrochemistry, and pharmaceutical products.
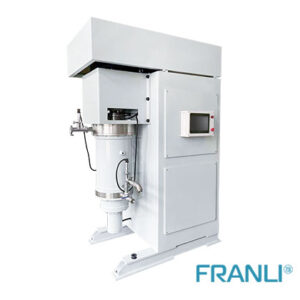
Role of Pearl Mill in the Nano Industry
Pearl Mill can handle both high and low viscosity materials. One is for Nano grinding materials, while the other is for high viscosity materials like offset ink. The operation of the Pearl Mill is straightforward, and all maintenance; may be handled quickly and efficiently. Adding grinding media from the feeding hole is simple.
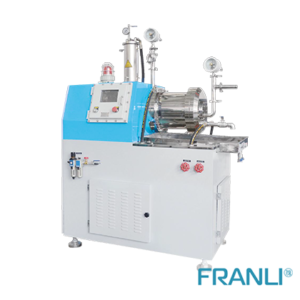
Guide to Bead Mills
The Bead mill is one of the main grindings and dispersing equipment in paint production. Bead mills for coatings are mainly divided into four categories: vertical, horizontal, basket, and special-shaped bead mills.
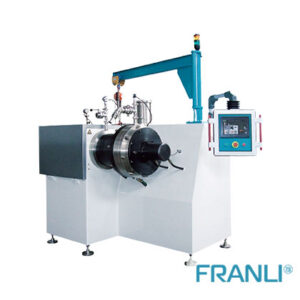
Dyno Mill|Coating & Inks
Dyno mill is a type of bead mill machine which is used in the coating industry specifically, in the manufacturing of inks products.
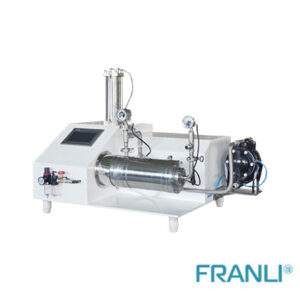
The structure and type of laboratory bead mill
The laboratory bead mill in the chemical experimental equipment, also known as the lab sand mill, is a kind of grinding equipment compared with the bead mill for industrial production.
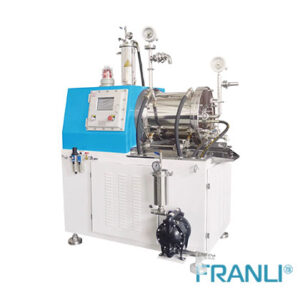
High Viscosity Material Grinding – Bar Pin Bead Mill
The bar pin bead mill is a machine suitable for ultra-fine dispersion and nano-scale grinding of water-based and solvent-based materials. The bar pin bead mill is one of the most widely used production types of equipment. With its very stable performance and sophisticated technology, it has been recognized by a wide range of users. The key thing to know is the characteristics of the bar pin bead mill, which is also the key to people’s favor of it.