Home » Operations Of High Speed Disperser
Operations Of High Speed Disperser
The kind of mixer that is used for the manufacturing process of plastics, chemicals, coatings, paints, composites, and other related products is known to be the high speed disperser. The function included here is in incorporating, dissolving, uniformly distributing, and wetting off the powders into liquid and relatively breaking down the particles agglomerates for the production of finer dispersions.
Mode of operation
There is a dispersing blade and a driven vertical shaft within the conventional high speed dispersers. For creating a pattern of radial flow within the stationary mix vessel, the blade rotates and is known to impart higher shear forces. A vortex is created by the blade that continuously draws the components of the products to the sharp edges of the blade. Thereby to reduce the size of the particle, dispersing and dissolving them within the liquid for yielding a homogeneous product, the surface of the blade tears apart mechanically within the high speed dispersion mixer.
Selecting the right dispersing unit
Note the viscosity
You need to ensure that it is able to mix the viscosity for the range of products you are supplying. The materials here are shear to thinning and flow well under the given force as well as the mixing conditions.
Size of the batch
Be sure to match along with the specifications of the high speed disperser for determining the batch size optimally.
Design of the vessel
A better flow is promoted with the help of the round dished bottom of the vessel that can help in minimizing the possibility for dead spots with that of the materials that are unmixed. The commonly used ones are the flat or sloped bottom. A vessel having the same diameter and height is the one that is preferred here. 3 times the diameter of the blade should be consistent with the diameter of the vessel here. Above the blade, the full batch level, the one that is desired, should be at rest.
Maintaining your disperser
There are sure to take note of a few basic steps for preventative maintenance to help the disperser run smoothly and also increase its longevity. These dispersers can operate for years without facing any trouble when it is maintained in a proper manner.
Check out the wear and tear in the blade and replace it timely
Through the higher shear action of the blade here, the high speed disperser produces homogenous liquid as an end product. There are teeth within the blades of the disperser that has an abrupt edges profile that can wear over time naturally. The rate of the damage depends on the content batches, and it varies. The damage of the blade is accelerated through the silica sand and related abrasive solids. The results of the process are sure to suffer when the edges of the blade smoothen out and become rounded. A thorough frequent inspection of the blade is a must and should be replaced within the time for a seamless output.
Maintenance of the motor
For reaching the needed speed of the blade tip associated with the process of dispersion, these dispersers are operated at a higher speed. This is the reason why the maintenance of motor is significantly important. Most of the motors, especially the electric ones, are free of maintenance. However, electric motors are subjected to failures prematurely. For the applications, each of the new ones, especially the ones with higher viscosities or higher contents of solids, will be monitoring the temperature of the motor during the processing. Prior to burning the windings, the electric motors have overload circuits that are sure to trip, but the motors constantly running near the temperature limitations will have shorter durability.
Look out for the bearings and vibrations of the shaft
To the important speeds is where the equipment with shafts the rotational ones are subjected to. These speeds are the ones at which a frequency natural enough of the machine exists with the amplification of the shaft vibrations.
Experiencing this critical speed along with ramping up the shaft’s speed to meet the operating speed that is desired one is something that is quite common. The damages over the bearing system as well as the shaft can be the outcome of it running on a long-term at the speed that is critical. The speed should be increased rapidly with the help of a range where the increased rate of vibration is specified to prevent this. The high speed disperser should never run dry or without the blade being submerged as it is sure to increase the vibration degrees dramatically and cause potential bending of the shaft with significant damages to the bearings.
Always maintained a scheduled cleaning routine
The general buildup of the debris, along with the remnants of the ingredients in and around the disperser unit, can cause a lot of trouble over time. Always makes sure to create a routine to clean out the shaft, bearing housing as well as the blade of the disperser. Also, clean the ingredients accumulated at the exteriors of the unit that includes the pneumatic and electronic controls as well as the peripheral equipment.
Franli is a company that is trusted by scientists as well as lab managers worldwide for its high pressure dispersers. They offer units that are both reliable and are of higher quality that can help with your dispersion work. They are sure to offer you some master products that can help you with your mixing, grinding as well as emulsifying processes.
Copyright Notice :
This article only represents the author’s point of view.
This article is published under the authorization of the author.
Source: Franli
This article address : Operations Of High Speed Disperser
Related Products
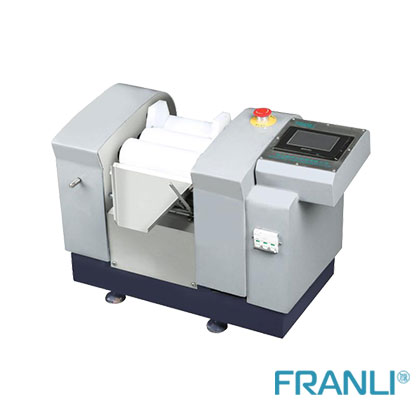
Triple roller mill
Three-roller mills are also called triple roller mills. In daily work, they can be divided into Lab triple roller mills and production triple roller mills. They are mainly used in ink, paint, paint and other industries.
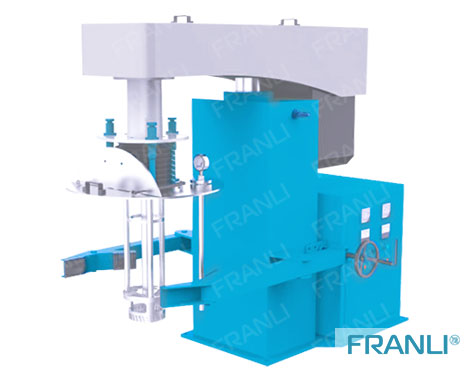
High Shear Mixer
High Shear Mixer is to disperse one or more phases into another continuous phase through efficient, fast, uniform and other processes, and under normal circumstances each phase is insoluble.
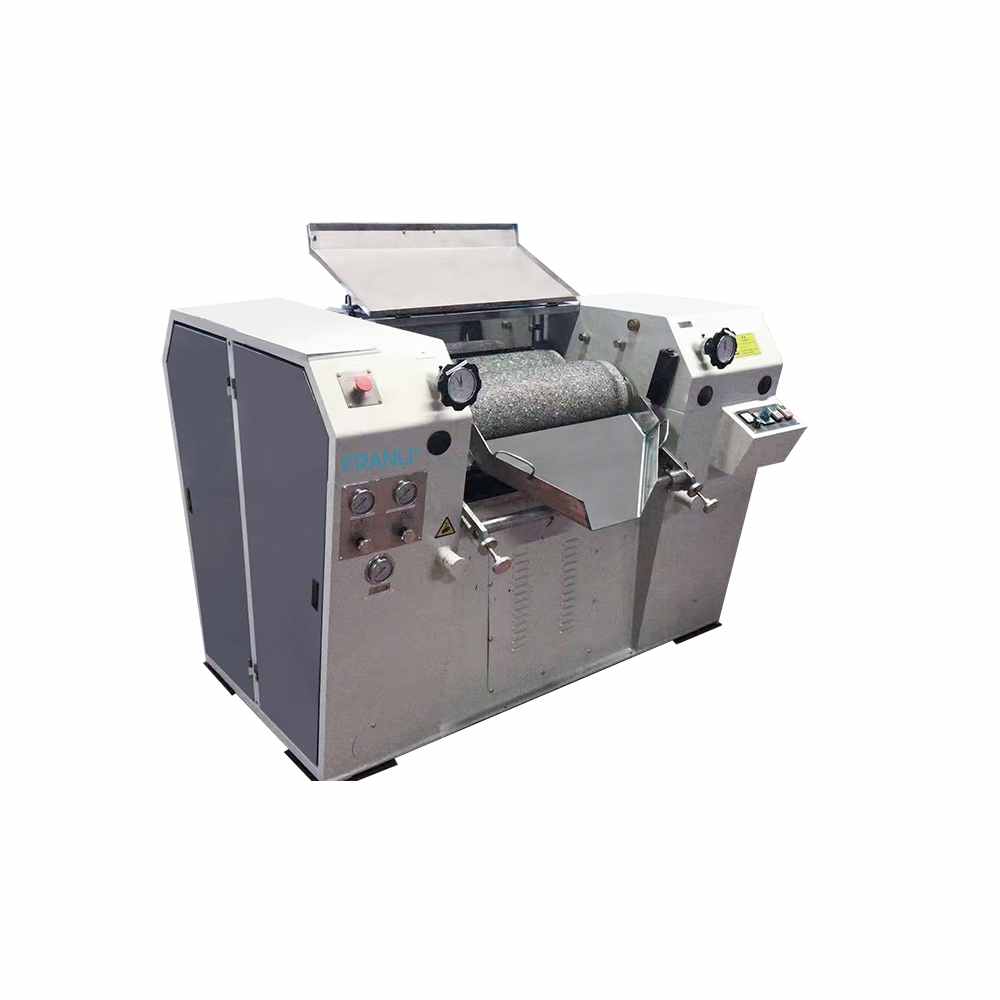
Granite Three Roll Mill
The granite three roll mill is suitable for the grinding of various art pigments, water-based colorants, pasty raw materials, chocolate, vanishing cream, cosmetic pigments, lipsticks, and other materials. It has its unique grinding effect.
News
Laboratory Reactor: Guide to Stirring System
The laboratory reactor is composed of a pot body, a pot cover, an agitator, a jacket, a support and transmission device, a shaft seal device, etc.
Grinding Media for Bead Mill | Zirconia Beads & Zirconium Silicate Beads
Bead mills mainly use grinding balls as media, and use impact, extrusion, and friction to achieve the final grinding effect, which mainly depends on the size and hardness of the grinding beads, the filling rate of the grinding beads, and the collision frequency adjustment between the grinding beads and the particles.
Overview of Laboratory Reactor
Laboratory reactors, also known as lab reactors, are essential tools in scientific research, product development, and process optimization. These reactors provide a controlled environment for conducting chemical reactions, mixing, dispersing, and homogenizing processes.
Bead mills | Manufacturing technology in various industries
Bead mills, also known as sand mills or grinding mills, are versatile machines widely used across various industries for the wet grinding and dispersion of solid particles in liquid media.
Ribbon Blender Mixer Equipment
A ribbon blender mixer, also known as a ribbon mixer or horizontal ribbon blender, is a powerful industrial machine designed for thorough and efficient blending of various materials.
What is A Stainless Steel Reactor?
Stainless steel reactors are essential equipment in various industries, including chemical, pharmaceutical, biotechnology, and food processing.