Home » The Versatility and Application of Triple Shaft Mixers in Coatings
The Versatility and Application of Triple Shaft Mixers in Coatings
Triple Shaft Mixer
A triple shaft mixer is a powerful equipment designed to combine and disperse different types of materials effectively. It comprises three independently driven agitators – two low-speed anchor agitators and a high-speed disperser. The anchor agitators provide bulk mixing and transport materials within the blending vessel, while the high-speed disperser rapidly breaks down lumps and promotes efficient particle distribution.
Advantages of Triple Shaft mixer
- Long life with a sturdy mixing bowl made by a fully automatic welding robot
Can manufacture all kinds of concrete - High uniformity even with a short mixing time
Parts with excellent durability and wear resistance - Easy maintenance with replaceable bolt lining for large maintenance doors
Automatic lubrication system - Compact design and universal compatibility with existing concrete plants
Application: Paint, Adhesive, Battery, Pharmaceutical industry, Cosmetic
Coatings are essential in numerous industries, ranging from automotive and aerospace to construction and furniture. These coatings provide protection, enhance aesthetics, and improve performance. The production of high-quality coatings relies heavily on the efficient mixing of raw materials to achieve consistent formulations.
Components and Working Principles
The triple shaft mixer typically consists of a mixing vessel, anchor agitators, a disperser blade, a motor, and various control systems. The vessel holds the raw materials and provides the necessary environment for mixing. The anchor agitators promote bulk mixing, while the high-speed disperser blade ensures the thorough deagglomeration and homogenization of the mixture.
Versatility of Triple Shaft Mixers
1. Suitable for a Wide Range of Coating Formulations:
Triple shaft mixers are versatile and can handle various types of coating formulations, including water-based, solvent-based, and high solids coatings. This versatility allows manufacturers to produce different types of coatings while ensuring consistent quality.
2. Effective Mixing of Viscous and Thixotropic Materials:
Coatings often consist of high-viscosity or thixotropic materials, making them challenging to mix efficiently. Triple shaft mixers excel in handling these materials, ensuring uniform dispersion, and eliminating unwanted lumps or agglomerates.
3. Efficient Incorporation of Powders and Pigments:
Powders and pigments play a crucial role in many coating formulations, requiring thorough dispersion to achieve the desired color and consistency. Triple shaft mixers possess high shear capabilities, facilitating efficient incorporation and uniform distribution of powders and pigments.
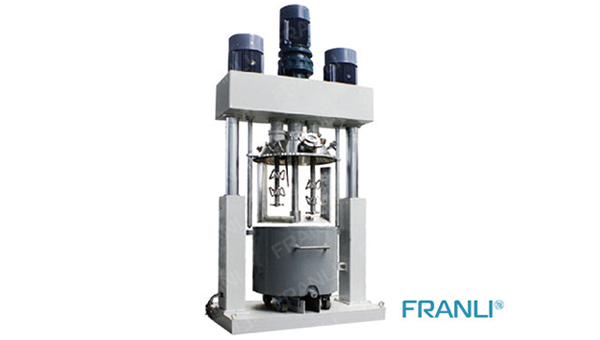
Benefits of Triple Shaft Mixers in Coating Applications
1. Improved Batch-to-Batch Consistency:
The precise control and intensive mixing capabilities of triple shaft mixers ensure consistent mixing across different batches. This attribute is significant in maintaining quality control and meeting stringent specifications in the coating production process.
2. Reduced Processing Time:
Triple shaft mixers significantly decrease processing time due to their high-speed disperser blades and efficient mixing mechanisms. This speeds up production cycles, allowing manufacturers to increase output without sacrificing quality.
3. Enhanced Product Quality:
The advanced mixing action of triple shaft mixers promotes thorough dispersion and deagglomeration of raw materials, resulting in coatings with enhanced properties, such as improved flow characteristics, color uniformity, and reduced defects.
4. Increased Operational Safety:
Triple shaft mixers often come equipped with safety features and controls, ensuring operator protection during the mixing process. By minimizing potential hazards and accidents, these machines increase overall operational safety.
Triple shaft mixers have revolutionized the coating industry by providing efficient and versatile solutions for mixing raw materials. Their ability to handle a wide range of coating formulations, efficient dispersion of powders and pigments, and the consistent production of high-quality batches make them invaluable in the coatings manufacturing process. As the demand for high-performance coatings continues to grow, triple shaft mixers will remain an essential tool for manufacturers looking to meet the evolving needs of the industry.
The triple shaft mixer is a device available at Franli with various functions such as diffusion, emulsion, and blending. The company produces multi-shaft mixers with more than 20 years of experience. These multi-shaft mixers are ideal for mixing systems with high viscosity or high dispersion. A combination of several mixing methods can be used to complete the mixing and dispersing process faster and more completely.
Welcome to send inquiry to us and let’s make a win win business together !
Guidelines For Multi Shaft Mixer
FRANLI customized different kinds of multi-shaft mixers for more than 300+ customers. This kind of machine works in the coating industry, medicine industry, cosmetic industry, and other high technology chemical industries.
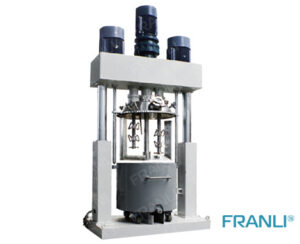
The Application of Triple Shaft Mixers in Adhesives
Triple-shaft mixers, also known as multi-shaft mixers, are innovative blending machines designed to efficiently mix and disperse various components in adhesives.
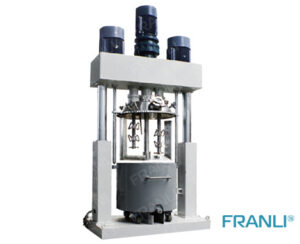
Triple Shaft Mixer: Ideal Equipment for Ink Production
Triple shaft mixers are capable of handling a wide range of ink formulations, including solvent-based, water-based, UV-curable, and hybrid inks.
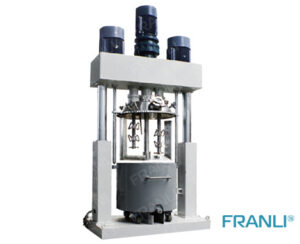
The Versatility and Application of Triple Shaft Mixers in Coatings
Triple shaft mixers have revolutionized the coating industry by providing efficient and versatile solutions for mixing raw materials.
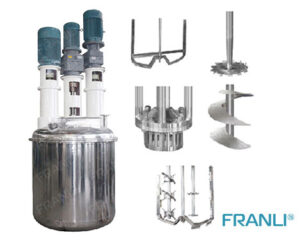
What is a Multi-Shaft Mixer?
A multi-shaft mixer is a type of industrial mixer that has more than one mixing shaft. These mixers are designed to mix multiple ingredients simultaneously, allowing for more efficient and effective mixing.
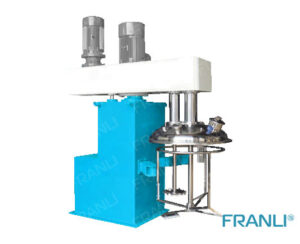
Dual Shaft Mixer – Dispersion & Stirring
The dual shaft mixer is the best mixer to dissolve the specific ingredients with appropriate shear capacity. This activity is performed by the high-speed shafts situated in the mixer and provides you with the perfect uniformity of the product. It also contains an Anchor agitator and a High-Speed Disperser that offer you the best quality and consistency.
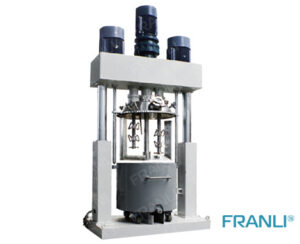
Triple Shaft Mixer | anchor type, butterfly type & frame type
The FRANLI triple shaft mixer extends the working area by adding a rotating stator mixer with a large displacement or a second quick distributor. High shear stator and rotary mixer can emulsify and homogenize products that require higher shear forces to reduce particles into smaller sizes.