Home » The Role and Application of Filling Machines in Ink Filling
The Role and Application of Filling Machines in Ink Filling
Filling Machine
Filling machines have revolutionized the ink filling process, providing efficiency, accuracy, and versatility to ink manufacturers and filling operations. From automated systems for high-volume production to manual machines for small-scale operations, these machines greatly improve productivity while maintaining consistent and high-quality ink filling. Considering the safety features incorporated into filling machines, they have become an indispensable tool in the ink filling industry, ensuring both operator safety and product integrity. As technology continues to evolve, filling machines will undoubtedly play an even more significant role in ink filling processes, meeting the increasing demands of the industry.
Details of Filling Machine
- Single filling can be 100g-250kg
- The operation method is simple and easy to operate.
- High durability and wide range of applications
Application: Paint, Adhesive, Battery, Pharmaceutical industry, Cosmetic
Ink filling plays a crucial role in various industries, from printing and packaging to manufacturing. The process of filling ink containers requires precision, efficiency, and safety to ensure optimal performance and consistent quality. With the advancement in technology, filling machines have become a vital tool in the ink-filling process. In this article, we will explore the application of filling machines in the ink filling industry, highlighting their benefits, working principles, and the different types available.
Benefits of Filling Machines
1. Efficiency and Productivity:
Filling machines significantly improve the efficiency and productivity of ink-filling operations. These machines are designed to fill a large number of containers within a short period, reducing manual labor and speeding up the process. With automated functionality, filling machines can complete tasks quickly, consistently, and accurately.
2. Accuracy and Precision:
The correct filling of ink containers is crucial to ensure consistent quality and avoid spillage or wastage. Filling machines employ advanced technology to dispense the desired amount of ink with precision, ensuring accurate fills irrespective of container size, shape, or viscosity. This eliminates human errors and guarantees uniformity in the ink-filling process.
3. Versatility:
Filling machines offer versatility in terms of their ability to handle different container types such as bottles, cartridges, pouches, or bags. They can accommodate various ink formulations, ranging from water-based to solvent-based, thus allowing ink manufacturers to use the same machine for different products and packaging.
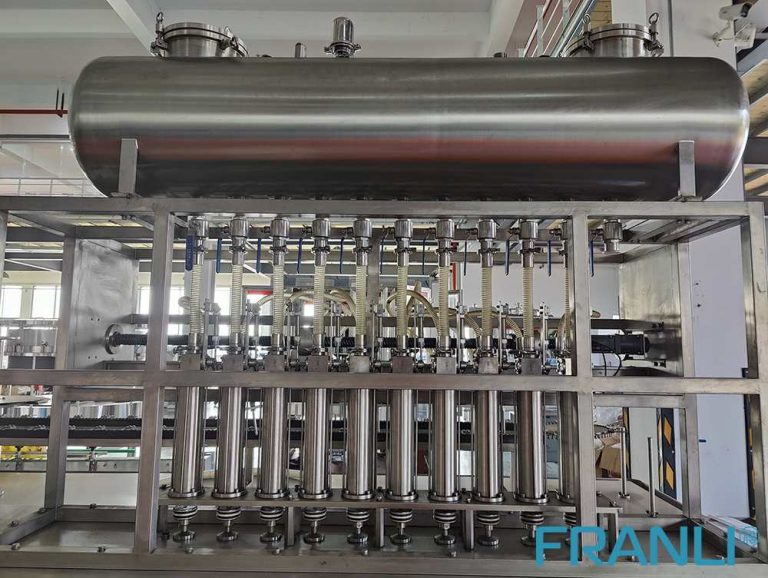
Working Principles of Filling Machines
Filling machines are built on principles that allow for efficient and reliable ink filling. The common working principles include:
1. Positive Displacement:
Positive displacement filling machines use pistons or rotary valves to accurately measure and dispense a fixed quantity of ink into containers. The piston or valve movement creates a vacuum or positive pressure that draws and dispenses ink, ensuring precise filling.
2. Gravity Filling:
Gravity filling machines utilize the force of gravity to fill containers by directing ink into them. This principle works well for low-to-medium viscosity inks. Containers are positioned below the fill nozzles, and ink flows from an overhead tank or reservoir, filling the containers until the desired level is reached.
3. Vacuum Filling:
Vacuum filling machines create a vacuum inside the containers, which causes the ink to be drawn into them. The ink is stored in a sealed chamber, and the vacuum is released, allowing the ink to fill the container. Vacuum filling is ideal for high-viscosity inks or containers with narrow openings that may not allow easy flow of ink by gravity alone.
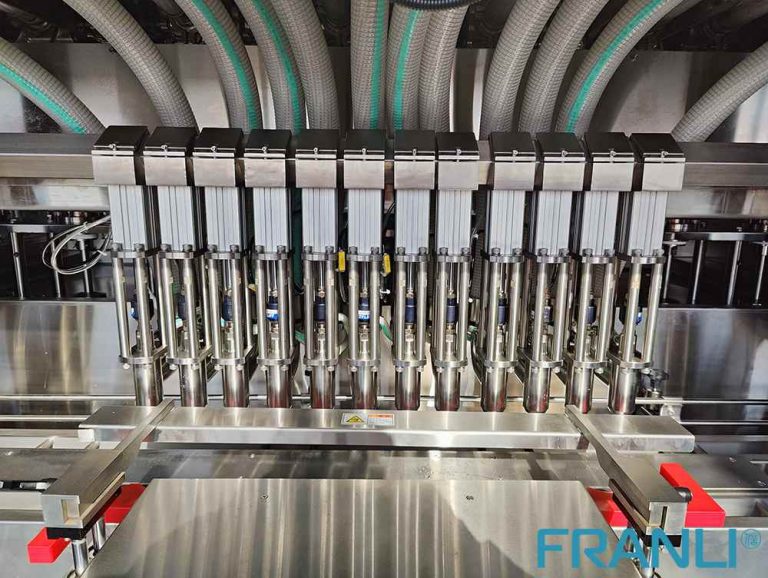
Types of Filling Machines
1. Automatic Filling Machines:
Automatic filling machines are highly efficient and suitable for high-volume ink filling operations. These machines typically have multiple fill heads and can simultaneously fill multiple containers. They can be programmed to fill a specific quantity of ink into each container, ensuring consistency and accuracy.
2. Semi-Automatic Filling Machines:
Semi-automatic filling machines require limited human intervention, offering flexibility for smaller-scale ink filling operations. These machines often have a single fill head and require an operator to initiate the filling process. Though not as fast as automatic machines, they still significantly improve productivity.
3. Manual Filling Machines:
Manual filling machines are suitable for small-scale ink filling or laboratory environments. These machines require complete human control, with operators manually dispensing ink into containers. While the fill process may be slower and less efficient than automated systems, manual filling machines offer cost-effectiveness and simplicity.
Safety Considerations
Ink filling involves handling potentially hazardous materials. Filling machines incorporate safety features to protect operators, minimize spills, and maintain industry standards. Some safety considerations include:
1. Leak and Overflow Protection:
Filling machines are designed with tight seals and anti-drip mechanisms to prevent leaks or overflows during the filling process. This ensures the protection of operators and maintains the cleanliness of the workspace.
2. Fume Extraction:
Given that some inks may emit fumes or volatile organic compounds (VOCs), filling machines can be equipped with fume extraction systems. These systems help to remove any hazardous fumes from the work environment, keeping it safe for operators.
Welcome to send inquiry to us and let’s make a win win business together !
Guidelines For Filling Machine
FRANLI is manufactured as a professional filling machine equipment, our filling machine can be filled from a minimum of 100g to a maximum of 250kg, and the filling dose can be adjusted by itself.
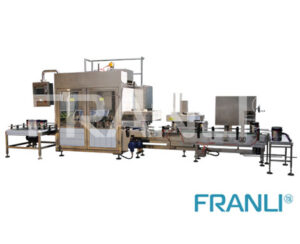
Paint Filling Machines: Enhancing Efficiency and Precision
Paint filling machines are vital equipment in the paint and coatings industry, designed to accurately fill various types of paint into containers of different sizes and shapes.
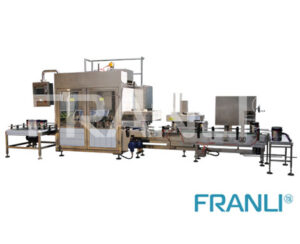
Paint Filling Machine | Liquid Filling Machine
Paint filling machines are automated industrial equipment used for filling paint, coatings, adhesives, and other liquid products into containers.
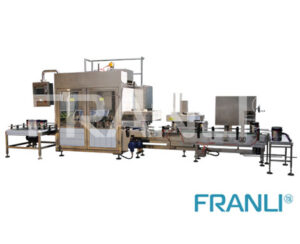
Paint Filling Machine: Efficient and Accurate Filling of Paint
A paint filling machine is a specialized piece of equipment used to fill paint cans with liquid paint. It consists of a conveyor system, a filling station, and a control panel.
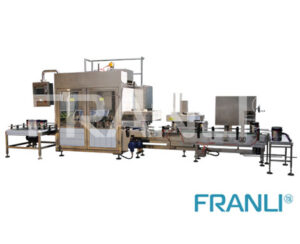
Paint Filling Machine:Accurate Filling of Viscous Liquids
Paint filling machines are specialized equipment used in the paint and coatings industry to accurately measure and fill paint into various containers.
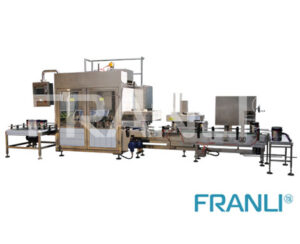
Filling Machines in Lubricating Oil Filling: Streamlining Efficiency & Precision
Filling machines have revolutionized this process by automating the entire operation. These machines are designed to precisely control the amount of oil-filled, ensuring accuracy and reducing wastage.
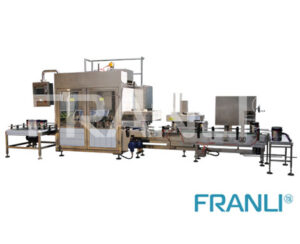
Glue Filling Machine: High Precision & High Efficiency
Filling machines used in the glue field are designed to deliver precise amounts of adhesive into containers, including bottles, cans, tubes, and cartridges.