Home » Paint Filling Machine | Liquid Filling Machine
Paint Filling Machine | Liquid Filling Machine
Filling Machine
Paint filling machines are automated industrial equipment used for filling paint, coatings, adhesives, and other liquid products into containers. They are commonly used in industries such as paint and coatings manufacturing, chemical production, and consumer goods packaging.
Details of Filling Machine
- Single filling can be 100g-250kg
- The operation method is simple and easy to operate.
- High durability and wide range of applications
Application: Paint, Adhesive, Battery, Pharmaceutical industry, Cosmetic
A paint filling machine, also known as a liquid filling machine, is an automated system designed to fill precise quantities of liquid products into containers in a fast, efficient, and consistent manner. The key components of a paint filling machine include a filling station, container handling system, control panel, and integrated liquid supply system.
During operation, empty containers are fed into the machine via the container handling system. The filling station then picks up the containers one by one and fills them with the desired amount of liquid product using filling nozzles or valves. Common filling methods include volumetric, gravimetric, and piston displacement filling. Filled containers are then released onto a discharge conveyor. Modern machines can fill hundreds of containers per minute.
Working Principle of Paint Filling
Paint filling machines work on the principle of automated, high-speed filling of liquid products into containers. The main working steps involve:
– Container Handling: Empty containers are fed into the machine via a conveyor system. Common container types include cans, buckets, drums, and IBCs.
– Container Positioning: Precise positioning devices align each container under the filling station.
– Liquid Supply: Paint is pumped from bulk storage tanks to the filling station via pipes and hoses.
– Filling Process: Nozzles/valves dispense the accurate fill volume into each container based on the selected filling method.
– Quality Control: In-process weighing/volume checks ensure correct fill quantities within tolerances.
– Capping/Sealing: Some machines apply lids, caps, or seals to the filled containers.
– Product Discharge: Filled containers exit onto a discharge conveyor for packaging/palletizing.
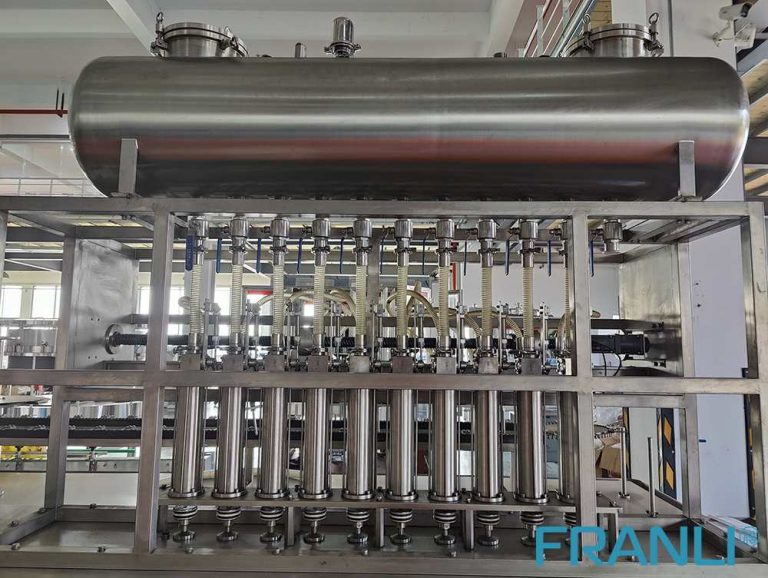
Types of Paint Filling Machines
There are different types of paint filling machines based on their configuration and filling methods:
– Volumetric Fillers: Fill using pre-set fill cycles controlled by flow meters/timers.
– Gravimetric Fillers: Weigh each container on a scale to dispense the exact fill weight.
– Piston Fillers: Use reciprocating pistons to displace a fixed volume into containers.
– Rotary Drum Fillers: Fill containers mounted on an indexed rotary filling turret.
– Inline Fillers: Continuous filling machines for high-speed production lines.
– Robotic Arm Fillers: Articulated robotic arms precisely fill irregular containers.
– Dual-Filling Stations: Increased throughput with parallel filling stations.
– Capping/Sealing Machines: Integrated machines that fill and cap/seal containers.
Applications of Paint Filling Machines
Paint filling machines are used across various industries to automate liquid filling operations:
– Paints and Coatings Manufacturing
– Adhesives Production
– Chemical Manufacturing
– Pharmaceuticals
– Cosmetics and Personal Care Products
– Food and Beverage Processing
– Automotive Fluids
– Household and Industrial Cleaning Products
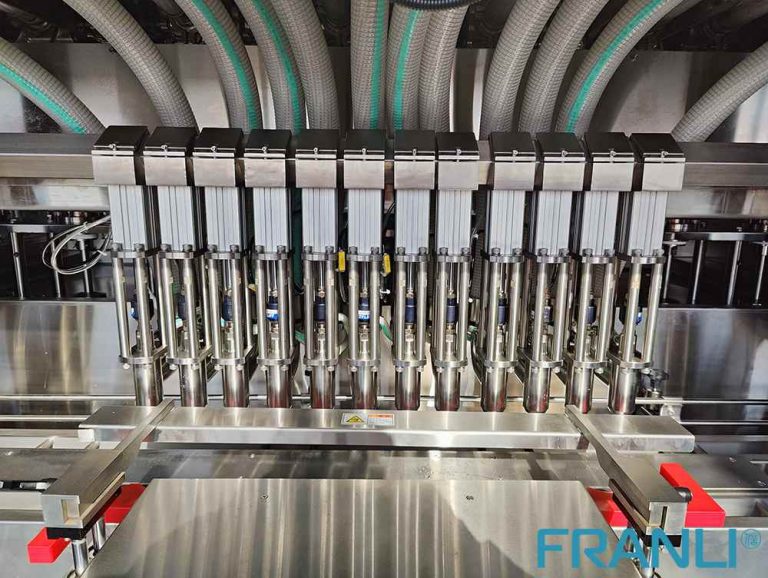
Benefits of Paint Filling Machines
Automated paint filling machines provide numerous advantages over manual filling processes:
– High Speed and Efficiency: Fill hundreds of containers per minute.
– Precise and Accurate Filling: Control fill volumes within tight tolerances.
– Consistency: Ensure uniform fills with consistent product quality.
– Labor Savings: Reduce labor costs by automating repetitive filling tasks.
– Space Savings: Compact designs occupy less floor area than manual lines.
– Integrated Quality Control: In-process weighing/volume checks maintain quality.
– Closed System: Contains spills and prevents exposure during filling.
– Customizable: Can be configured for different container sizes and fill volumes.
– Modular Design: Easy to expand production capacity by adding modules.
– Clean-In-Place: Hygienic designs simplify cleaning and changeovers.
– Traceability: Integrated coding/labeling provides batch traceability.
Key Components of Paint Filling Machines
Major components of automated paint filling machines include:
– Filling Station: Houses filling valves/nozzles and container positioning devices.
– Liquid Supply System: Pumps, pipes, valves for transferring paint to the filler.
– Container Handling System: Conveyors for feeding/discharging containers.
– Control Panel: PLC/HMI for operating parameters, recipe management, etc.
– Weighing/Volumetric Sensors: Ensures accurate fill quantities are dispensed.
– Capping/Sealing Unit: Applies lids, caps, or seals to filled containers.
– Safety Guards and Interlocks: Protects operators and ensures safe operation.
– Support Frame: Robust frame/structure to mount all machine components.
Operating Principles of Paint Filling
Key factors to consider during paint filling machine operation include:
– Filling Method: Volumetric, gravimetric or piston filling based on product needs.
– Container Handling Speed: Depends on required production throughput rates.
– Fill Accuracy: Tolerances of ±0.5-2% of target fill weight/volume.
– Filling Speed: Typically 5-30 seconds to fill a single container.
– Liquid Supply: Pumps must supply paint at filling flow rates and pressures.
– Capping/Sealing: Type of closure and speed of capping/sealing operation.
– Quality Control: In-process weighing ensures fill quantity and weight specifications.
– Cleaning: CIP systems clean machines between changeovers/product batches.
– Safety: Interlocks prevent operation during maintenance or faults for safety.
– Documentation: Printing batch codes, labels, and production records.
Welcome to send inquiry to us and let’s make a win win business together !
Guidelines For Filling Machine
FRANLI is manufactured as a professional filling machine equipment, our filling machine can be filled from a minimum of 100g to a maximum of 250kg, and the filling dose can be adjusted by itself.
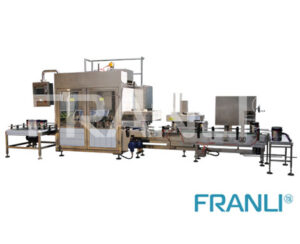
Paint Filling Machines: Enhancing Efficiency and Precision
Paint filling machines are vital equipment in the paint and coatings industry, designed to accurately fill various types of paint into containers of different sizes and shapes.
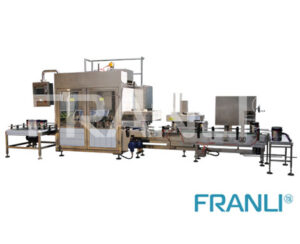
Paint Filling Machine | Liquid Filling Machine
Paint filling machines are automated industrial equipment used for filling paint, coatings, adhesives, and other liquid products into containers.
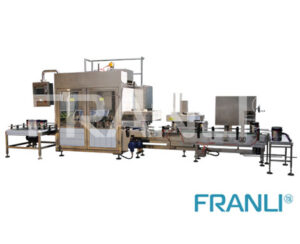
Paint Filling Machine: Efficient and Accurate Filling of Paint
A paint filling machine is a specialized piece of equipment used to fill paint cans with liquid paint. It consists of a conveyor system, a filling station, and a control panel.
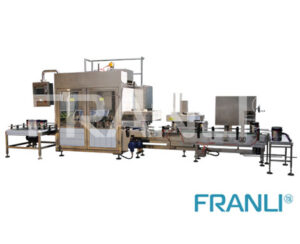
Paint Filling Machine:Accurate Filling of Viscous Liquids
Paint filling machines are specialized equipment used in the paint and coatings industry to accurately measure and fill paint into various containers.
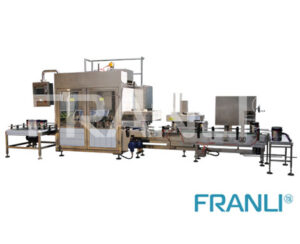
Filling Machines in Lubricating Oil Filling: Streamlining Efficiency & Precision
Filling machines have revolutionized this process by automating the entire operation. These machines are designed to precisely control the amount of oil-filled, ensuring accuracy and reducing wastage.
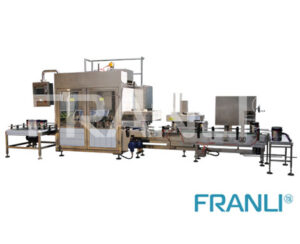
Glue Filling Machine: High Precision & High Efficiency
Filling machines used in the glue field are designed to deliver precise amounts of adhesive into containers, including bottles, cans, tubes, and cartridges.